Performance management is about metrics, from read-outs on key performance indicators (KPIs) to statistical charting, to the many fingers on the pulse of units pushed to the loading dock. Does the concept of operational excellence fit into this measured world? At first glance, it would seem not; there is no Operational Excellence Index. People might be justified in thinking that “operational excellence” is just a feel-good tag, useful in a rah-rah session, but not something that your chief financial officer can take to the bank.
Still, the idea is far more than marketing spin. A combination of people, strategies and technologies constitute the “magic formula” for reaching operational excellence. Industry analyst Julie Fraser, a principal at analyst firm Industry Directions Inc., in Cummaquid, Mass., says, “There are a number of broad-based systems that contain metrics you could watch to determine operational excellence. Operational excellence is about excellence of processes and people. Metrics that measure these tend to work best when they are plant wide or line metrics, put in place to make people more aware of their performance against the core things that matter—that is, things that the company cares about.”
Fraser adds that for any company with any degree of sophistication, specific metrics derived from comprehensive software are rapidly becoming the norm. “The world has become too complex for clipboards and isolated data,” she says. “Product lines have exploded, customer requirements become ever more detailed, and supply chain management is only getting more complex. No single person, no single group can keep tabs manually.”
No Excellence In Defects
Some sad realities emerge from Fraser’s study of metrics that matter for the Manufacturing Enterprise Solutions Association International (MESA). The number-one measure of quality remains a count of the number of defects. “For two decades or more, people have been talking about prevention of defects as the most valuable activity for quality control,” Fraser points out. “It’s a little disheartening to see defect counting still a leading indicator, rather than quality-by-design projects, the number of successful preventive actions or the number and length of initiatives for corrective measures.”
Then there is the low rate of adoption for standards. With the proliferation of outsourcing and its attendant supply-chain management demands, says Fraser, there is a concomitant need for well-understood standards that, when possible, are industry-wide. “Instead, we see companies at worst with ill-defined standards and at best, pursuing good but individualistic internal standards,” she says. “They send work out to other companies who in turn follow their own individualistic standards, and that is showing itself to be a formula for disaster. China has no national mandates around lead paint, but there are neutral and well-defined standards on paint for toys that can easily be included in product specifications and easily measured—why are U.S. toy marketers not enforcing them until the government or the newspapers step in?”
The good news is that there is a growing corpus of manufacturers who understand the issues, pursue metrics that buttress their business objectives, and standardize to a high degree. “I recently visited Johnson Controls,” Fraser said. “Automotive suppliers are going under at a frightening rate, but Johnson Controls is doing well. I saw a true lean shop from top to bottom. Everywhere we went, operators were able to tell us what they were doing and why they were doing it.”
Minding Zero Tolerance
California’s Monterey Peninsula mixes urban subdivisions with wilderness reserves, and art colonies with world-class golf courses. The Pebble Beach Community Services District (PBCSD) serves the area for drinking water and wastewater services—and much more, including emergency medical and garbage collection. Since 1970, the PBCSD has maintained approximately 75 miles of sewer lines ranging over the peninsula, handling wastewater flow from roughly 5,000 permanent residents and many thousands of tourists, via eight pumping stations fitted with electric pumps. Wastewater is processed into water at a tertiary level, suitable for irrigation, which is then purveyed for irrigation to two of the five best golf courses. The processed water is held in a new, 12-million-gallon tank.
The collection and distribution of the wastewater in this fragile ecosystem poses challenges. A national marine sanctuary is sited off the peninsula, and California has strict ecological regulations. “We have zero tolerance for spills,” says Michael Niccum, district engineer. “Plus, the State of California has zero tolerance regarding sewage encroachment on the Pacific Ocean, as does the U.S. government regarding the sanctuary. Pump outages can result in spills, so each pumping station has to remain in service no matter what is going on around it.”
Unfortunately, frequent storms interrupt the electrical grid. To counter this, four pumping stations have permanent stand-by power, and the other four have large, portable generators. If a station’s power goes down, switchover to backup power has been automatic since the early 1990s.
“Prior to early systems for automatic switchover, engineers drove to each station during outages to ensure operation. When we went to automatic power backup, we discovered that supervising remote operation could be problematic,” Niccum says. “We put in our own radio-based system, but we found that the terrain prevents simple radio communications. The phone lines often go down with the electrical grid. Both the phones and the power are managed by several separate private entities, so tying the pieces together was highly complex. The result was an iffy system. Without confidence that reporting systems were working, guys would still be driving all night, crisscrossing the peninsula during bad weather.”
Saved By The Network
The recent need for a new pumping station in conjunction with the new high capacity tank prompted PBCSD engineers to rethink their system. Through an integrator, the result was an across-the-board upgrade to Allen-Bradley ControlLogix Programmable Automation Controllers (PACs) and FactoryTalk View human-machine interface (HMI) software from Milwaukee-based supplier Rockwell Automation Inc. The components enabled PBCSD to link its remote locations on the same computer network, using redundant network communications.
“We now can look into any station via the [HMI] interface to see detailed views of each remote operation’s performance,” says Niccum. “All in all, the new system allows us a new confidence level about continuous operation. Upgrading allowed us to expand our service infrastructures significantly without adding new personnel.”
Fewer geopolitical elements apply to more conventional discrete manufacturing facilities, but the complexity of operations that must smoothly mesh to make final product is much greater. This complexity led TRW Automotive to create a dedicated continuous improvement resource at its Mesa, Ariz., facility. The Mesa plant makes airbags and ancillary safety systems.
Its full-time continuous improvement manager, Ted Hansen, manages a group of Six Sigma Black Belts whose responsibility is identifying and furthering improvement and operational excellence initiatives. “After pursuing Lean [Manufacturing] in the early ’90s and Six Sigma in the late ’90s, we finally decided that part-time approaches were not as effective as we wanted,” he says. “Participants naturally felt that day-to-day manufacturing activities took precedence. Real improvement was spotty and the feelings around continuous improvement were deteriorating.”
TRW uses a rotation plan for each dedicated improvement department member. “We pull high potential people from the lines, from engineering, from quality and even from business management functions,” Hansen says, “then immerse them in Lean and Six Sigma training. For the next two years, they drive events and improvements, working toward a dual goal—make a positive difference in the affected manufacturing area and gain familiarity with everything they can, plant-wide.”
Team members manage two or three projects at a time, mentoring and coaching participants from the functionalities at the center of a given project. Eight months prior to completing the rotation, each member begins a proactive transition period, identifying where to re-enter full-time manufacturing. “Some people opt to remain part of the improvement team management,” he says, “but most say they want to get back to ‘real life,’ that is, manufacturing per se. We gain a double benefit from this—we have professionally-run initiatives, and at the end of the rotation, we have an ally on the line, with a broad plant perspective and a solid toolbox of systematic approaches.”
Capture the Data
One technology in particular has proven valuable: throughput analysis software from Activplant Corp., of London, Ontario, Canada. “Throughput Analyzer captures data from every manufacturing line,” Hansen says, “giving us a direct view of how each line is running. If there’s a slowdown, we can see if it’s caused by downtime, delays in cycle time, inadequate product flow or any other root cause.”
Without full product flow analysis, downtime is the easiest fault to spot, but downtime has proven to be irrelevant in a surprising number of cases. “One incident happened early in our installation,” he says. “Engineers were pointing to one cranky machine, but Activplant was pointing at completely different areas, where work-in-progress (WIP) numbers were signaling a problem. We took a flyer on the software analysis and changed some pallet tracking logic and we gained a 5 percent improvement in a few days.”
But by the same token, downtime proved a key indicator for a different problem, one in which three complex lines were making the same product. Downtimes washed back and forth among machines randomly, unpredictably affecting overall throughput. “Our first response was to set up WIP buffer zones that could shunt production to whichever set of lines was doing best,” Hansen relates. “That was a good interim solution, because it gave us a chance to focus more clearly on the causes of the downtime. The better focus then allowed us to fix some fundamental issues. The bottom line is that we have been able to pull WIP back out of the buffers into the lines, and we’re seeing a 20 percent overall improvement in throughput.”
There are other benefits to the fact that the software gathers metrics continuously. Prior to automated data collection, operators had to find time to log downtime, which would flag technicians. In many cases, technicians would fix issues, then forget to close the log. “We had numbers of five-minute fixes that were logged at eight hours,” Hansen says. “We ended up spending inordinate amounts of effort in scrubbing data to determine actual times. Now downtime is automatically logged, and automatically closed out when the machine is making parts again.”
Operational excellence takes on some of its most complex form in Food and Drug Administration (FDA)-regulated industries. Roche Diagnostics has adopted a dedicated resource approach. John Dzelme, CPIM, applications specialist, is a computer systems analyst who uses a Manufacturing Execution System (MES) to drive improvement.
“Operational excellence need not be subjective,” he says. “You can claim operational excellence when you achieve such a high level of success that other peers are willing to tag your work as a best practice or benchmark. Toyota is a standout in this regard—and note that while they’re number one in consistent quality, they state categorically that they need to improve more.”
Given Dzelme’s reference to Toyota, it is not surprising that Roche pursues Lean Manufacturing approaches. “We are firm advocates of continuous improvement,” he says. “We have gained huge returns on investment in the Toyota system along a number of fronts.” In addition to general process improvements, these include medical device manufacturing compliance initiatives, product mix decisions, and controls and process validations—every action, machine, and measure in medical manufacturing has to be standardized in ways acceptable to the FDA.
“We work from the business strategy on down,” Dzelme says. “If you implement solutions that don’t parallel overall business plans, you jeopardize losing direction or funding from stakeholders, or find yourself with a solution that just doesn’t add value to the organization.”
Roche applies rigorous systems analysis, familiar to those who build large software applications. “Our approach is as holistic as possible,” Dzelme explains. “We look at business strategies and directions, regulatory aspects, data collection and management strategies, and end-user adoption. You have to make life easier for the end-user, or you’ll face rejection.”
This systems approach enabled Dzelme to work with its MES provider to create functionality within the system. Roche uses a system from Camstar, Charlotte, N.C., and Roche’s first line of attack after installation was to reduce the cost of compliance. “We had a robust quality management system, because everything out the door has to be 100 percent in compliance with specifications. But it was manual, and the 170-plus pieces of paper that went into batch records were a burden. MES data collection can record steps as they happen, and in fact, enforces specifications, because things must be signed off before products are released to the next stage. Because of this, we’ve dropped to 12 records per batch that take less than half an hour, compared to more than two hours for the previous manual system. Plus, the savings are cumulative. We’ve cut more than four days from the overall batch release time, and we’re now working to eliminate even these 12 records.
“Camstar helped us with our initial implementation about two years ago,” Dzelme says, “Since then, our teams have designed, built and implemented a range of enhancements to the MES to support continuous improvement efforts. Our Roche MES development team is currently working on extremely promising projects for machine integration, packaging, compounding, Kanban queuing and scheduling. The objective for all is yield improvement.”
Creating Visionaries
Dzelme works with changing teams for projects, drawing from what he calls visionaries and sponsors, both drawn from a growing list of candidates that he has amassed. Visionaries are personnel that demonstrate a strong grasp of business strategy and how it relates to manufacturing activity. “More specifically, visionaries help us see where we need to be in five years and are willing to explore avenues for reaching that destination,” Dzelme says.
Sponsors tend to be high-energy players who have a firm grasp on the benefits of improvement initiatives. They are willing to help drive events or to evangelize, creating a steadily growing climate of continuous improvement. “I’m always interested in people who step back and look for answers that are broader than the fix of the moment,” Dzelme relates. “We want people who won’t put up with a failed quality check, who know that if you monitor processes, get into the details, and step in when key indicators first begin to move out of line, quick corrective action is possible.”
One common theme runs through initiatives managed by Dzelme’s teams: They all involve the end-user, whether that is the business manager or an operator on the line. “People dislike being force fed,” he says. “But if you let them plan the menu and do some of the cooking, they’ll build an appetite. Besides, who knows better about an issue than those who live and breathe it day in and day out?”
In all of this, Dzelme says, “you have to accept the fact that some people just don’t get it. The good ones can be moved to operations that have already been standardized, where things are relatively static and mature. Nay-sayers, people who interfere with the ability of others to understand best practices, need to be removed. Visionaries are prime candidates for new efforts or new product lines or processes.”
Dzelme has hammered out three rules for program success. First, when you initially bring technology to bear on a given operational detail, take a long look at the process. If you have many steps, determine whether the activity is actually complex, or whether the steps have proliferated simply because the process is manual. Simply automating the manual steps may bring no benefit.
Second, when selecting technology, dig into vendors’ experience in your industry, and opt for a supplier that can show you relatively short initial projects with appreciable returns—and a product architecture that supports modular installation and development. “You gain sponsorship when you show an immediate benefit,” Dzelme says.
Finally, ensure that the architects of the new systems are providing solutions that align with overall business needs. “It’s better to be open-minded about what good architects are telling you,” Dzelme says. “We pushed ahead with modifications at the beginning, over the recommendations of Camstar—and from this, we’ve learned that we were not the MES experts. A couple of our current projects are focused on undoing what we did then.”
Industry Directions’ Fraser brings an interesting insight to any discussion of operational excellence. “There’s a growing gap between companies who have the discipline to be excellent and companies that cannot or will not measure what counts,” she says. “Our research since the 1990s consistently shows operational leadership from groups that are successful in defining and enforcing principles of operation. The more that brand and quality are important to C-level people, the more you’ll find dedicated resources for strategic direction, improvement initiatives, and measurable information from every hand that’s involved in making the product.”
For more information, search keywords “operational excellence” and “manufacturing execution” at www.automationworld.com.
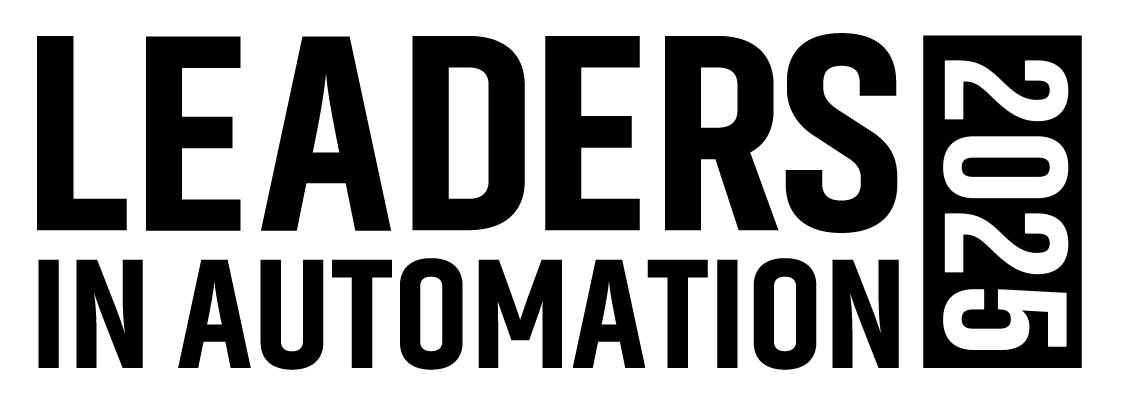
Leaders relevant to this article: