There’s an old adage about pioneers: They’re the ones who take the arrows in their backs. In the best cases, however, the pioneers who successfully dodge the arrows—or even survive a few hits—are the ones who also gain the advantages of being out in front. And when it comes to industrial wireless networking technology, some of today’s pioneering end-users believe that their efforts will pay off for their companies in just such a way.
Leading The Charge
Take the case of David Runkle, production manager at Lost Pines Power Park, an electric power generating complex about 40 miles southeast of Austin, Texas. When Runkle led the charge last year to install a wireless infrastructure at the facility for a new wireless public address system to boost staff efficiency, he faced heavy opposition from his corporate information technology (IT) department. One IT staffer, concerned about security, even hired a third-party hacker to try to break into the system as it was being launched.
Runkle also took flak from some plant personnel when he and a wireless vendor formed a “core team” of employees to test a set of wireless Voice over Internet Protocol (VoIP) paging devices. Their mistake was distributing the devices too soon, before all of the system bugs were worked out. Some workers had already been skeptical of the technology. And when the wireless system would suddenly stop working due to intermittent problems, those suspicions were reinforced.
The cause of the problem was minor, and has since been corrected. But by moving too soon with the tests, the Lost Pines wireless team lost the chance for some “early buy-in” for the project from key plant personnel. In retrospect, says Runkle, “we probably should have waited until we knew what all the issues were.”
Today, however, Runkle is “still standing” after surviving the early problems. The wireless system is up and running, and working well. And the infrastructure put in place for the public address system—installed at cost of about 25 percent less than that of a comparable hard-wired system—includes a “wireless umbrella” over the Lost Pines complex that can cost-effectively accommodate other industrial wireless applications.
What that means is that the Lost Pines Power Park is now well-positioned to use its new wireless infrastructure to cash in on a broad range of other cost-saving industrial wireless applications, Runkle says. “The project was justified on the communications piece alone, and now we’ve got a number of future applications that are already on the drawing board.” These range from remote wireless monitoring of Internet protocol (IP) video cameras, to wireless tank level sensing, leak detection and wireless systems for stress wave analysis-based equipment monitoring.
PPG Industries' Lake Charles, La., plant is using Emerson's Smart Wireless self-organizing mesh network technology at its A Caustic Unit. Shown at left is a Rosemount wireless temperature transmitter, which is being used as a repeater for wireless temperature and level sensing applications. The mesh technology has worked well in tests, and PPG plans to expand use of the technology, says PPG Senior Design Engineer Tim Gerami (right).
IT buy-in
Another pioneer in the industrial wireless space is Tim Gerami, senior design engineer at the Lake Charles, La., plant of PPG Industries Inc. The plant, which comprises more than 20 operating units on about 765 acres, manufactures chlorine, caustic soda and chlorine hydrocarbons.
Unlike Lost Pines’ Runkle, Gerami says he hasn’t suffered any slings and arrows from his company’s corporate IT staff. One key is that Gerami and his fellow Lake Charles engineers got the corporate IT department involved early; they invited IT people from PPG’s Pittsburgh corporate headquarters to join the initial, multi-discipline team formed in 2005 to investigate use of wireless technology at the Louisiana plant. As a result, says Gerami, “it’s a very free and open exchange [between IT and process controls departments] and we all get along very well.” IT involvement at each step of the way also ensures that the wireless team doesn’t run afoul of any corporate IT policies, he adds.
That’s not to say that the Lake Charles wireless team didn’t encounter its share of early problems and setbacks. Some setbacks had nothing to do with wireless technology. Shortly after the PPG team received approval for its first wireless pilot project in late summer 2005, Hurricane Rita roared through, knocking out power and leaving standing water in the Lake Charles plant, which was shut down for 2½ weeks. Then, beginning in late May 2006, the plant suffered a 110-day strike, which had an equally debilitating effect on the team’s ability to install and test wireless technology. That’s life in the real world.
Despite those obstacles, the PPG team was able to successfully complete testing on a variety of wireless technologies and applications at the plant throughout 2006, and is continuing its testing in 2007, says Gerami. And not everything has gone without hitches, or turned out as expected.
Wireless Fiber
In the early going, PPG tested both IEEE 802.16 WiMAX technology (for Worldwide Interoperability for Microwave Access) and IEEE 802.11 Wi-Fi technology (for Wireless Fidelity). Both are wireless standards promulgated by the Institute of Electrical and Electronics Engineers (IEEE). Wi-Fi is the familiar and increasingly ubiquitous technology that allows wireless connection through “hotspots” in homes, offices, airports and retail establishments such as coffee shops. WiMAX is a longer-range, higher-bandwidth wireless technology that can be used for long-distance, backhaul applications, and also can also provide a wireless “umbrella” over a facility. Compared to a typical Wi-Fi range of a few hundred feet, WiMAX supports a coverage range of 30 miles, along with significantly higher data rates.
WiMAX is “sort of like wireless fiber,” observes Steve Lambright, chief executive officer at Apprion, a Moffett Field, Calif.-based vendor that offers a WiMAX-based product family for industrial use. The company’s ION product platform is designed to provide broadband wireless capability on a vendor-agnostic and standards-agnostic basis. Video data from remote security cameras, along with Wi-Fi-based VoIP traffic, for example, as well as data from an IEEE 802.15.4 wireless mesh sensor network, could all be backhauled together on the same WiMAX network, Lambright explains.
Invensys Process Systems, the Foxboro, Mass.-based automation supplier, has partnered with Apprion to provide wireless application services. And because the PPG Lake Charles plant uses distributed control systems (DCS) from Invensys Foxboro, the PPG wireless team at the plant worked with the Invensys/Apprion team—along with various other vendors—for some of its early wireless tests. The PPG plant also uses Rosemount transmitters from Emerson Process Management, the Austin, Texas-based process control vendor, so the PPG team also began work early-on with Emerson as a beta site for some of that vendor’s Smart Wireless mesh networking technology.
WiMAX Intentions
On the WiMAX front, PPG began beta testing in early 2006 on the wireless transmission of video data from an inexpensive IP video camera, says Gerami. “At the time, our intent was to have WiMAX blanketing the whole plant in umbrella fashion, and security cameras that had WiMAX connections would send the video back.” The PPG team was also considering WiMAX for the transport of bar code- or radio frequency identification (RFID)-scanned data that would be used to track forktruck delivery of products and materials to some 150 delivery stations throughout the plant.
Another WiMAX link-up would handle long-haul voice communication between the Lake Charles plant and two salt water brine feedstock facilities that are about eight and 21 miles away. That system would replace the unreliable telephone connections to the brine fields, which are in remote, rural locations.
But a couple of things happened that altered the PPG team’s thinking about WiMAX. One was the failure of WiMAX technology to take off in the market. “We had heard that there would be a wealth of WiMAX appliances coming out, because of the Intel Rosedale chip, which is WiMAX enabled,” says Gerami. “We thought there would be WiMAX laptops coming out, and WiMAX VoIP, WiMAX PDAs (personal digital assistants) and other things.” But so far, despite the introduction of the Rosedale chip by microprocessor supplier Intel Corp., Santa Clara, Calif., “that just hasn’t occurred,” Gerami observes.
As a result, the PPG team began taking a closer look at the capabilities of Wi-Fi, which it was also testing in the Lake Charles plant. The team discovered that it could use an indoor industrial Wi-Fi access point, priced at about $300, and enclose it in a National Electrical Manufacturers Association (NEMA) 4X box for outdoor use at a cost of only about $200 more, says Gerami. “So for less than $1,000, we can get a 54-megabit/second (Mb/s) Wi-Fi access point,” he notes, “whereas it might cost $6,000 to maybe $20,000 for a WiMAX base station.”
A Better Option
Granted, says Gerami, the Wi-Fi technology can’t match the throughput or range of WiMAX. “But once we started studying it, we decided it was better to just blanket the plant in Wi-Fi, by having hundreds of access points, instead of covering the plant with one, two or maybe three WiMAXs,” Gerami explains.
The second thing that happened involving WiMAX was that one contractor used by the PPG team apparently installed the wrong radio for one of the test applications. Instead of deploying a point-to-point WiMAX radio for the brine field communication tests beginning in mid-2006, the contractor installed a point-to-multipoint unit. The result was that the system didn’t work correctly. And PPG now has decided to replace the long-haul WiMAX connection with a dedicated 5.9 Gigahertz non-WiMAX radio from another vendor, Gerami says.
Neither has PPG’s Wi-Fi testing progressed without providing some learning experiences. “In early 2006, we installed several Wi-Fi access points and had some issues with them dropping in and out,” Gerami relates. “We finally figured out what was wrong, with a consultant, and got those pretty stable, with some firmware upgrades.”
The PPG team also learned that even though a Wi-Fi access point may be labeled “industrial,” that doesn’t necessarily make it so. PPG has done much of its wireless testing in its A Caustic unit, one of three caustic soda production units at the Lake Charles plant. This included the installation of nine Wi-Fi access points for testing with VoIP, as well as with wireless handheld computers used for operator rounds, along with tablet personal computers (PCs) for use by technicians in wireless equipment calibration.
Wi-Fi Failures
Despite the “industrial” rating for the early Wi-Fi access points used, the PPG team found that the units couldn’t withstand the rigors of the outdoor A Caustic environment, which includes chlorine, caustic soda and acids. “They’ll say it’s industrial, but it’s just Class 1. It will meet explosion proof ratings, maybe Class 1, Div. 2, but it won’t meet NEMA 4X corrosion resistance ratings, which is what we need,” Gerami says. By about April of this year, some of the Wi-Fi access points were experiencing failures due to gasket erosion and corrosion on portions of the device that were aluminum, instead of stainless steel, he notes.
After researching the issue, Gerami says the PPG team determined that that no vendor at the time was making a true industrial Wi-Fi access point. The PPG team solved that problem by purchasing lower-priced indoor Wi-Fi access points and enclosing them in NEMA 4X enclosures. At least two vendors—Apprion and Cisco Systems—have since introduced Class 1, Div. 2 NEMA 4X Wi-Fi access points, says Gerami. But for now, PPG is moving ahead with tests using indoor access points enclosed in NEMA boxes. The team hopes to make a decision soon on which approach and which vendor's access points to use, and then to move ahead with a plan to blanket the entire plant with Wi-Fi during 2008, Gerami says. Including the plant’s 20 operating units and various non-production areas, that may require about 300 Wi-Fi access points, he estimates.
As part of his advice to other industrial end-users who may want to get started with wireless, Gerami recommends working with as many vendors as possible, and then to “test, test, test and test some more. If any salesman wants to bring you something to try out, go ahead and try it,” he says. “It’s worth it because you learn so much.” And even though PPG has decided to move away from use of WiMAX technology for now, Gerami says the PPG team is still in talks with Apprion and Invensys “to see their latest offerings. They have a really good solution, and we’re still considering them,” he says.
PA Upgrade
Indeed, Lost Pines’ Runkle says that his company’s successful wireless implementation and infrastructure is based upon the Invensys/Apprion technology. The Lost Pines Power Park, which is operated by the Lower Colorado River Authority (LCRA), is made up of two adjacent power producing facilities—the Sim Gideon power plant, which began commercial operation in 1965, and the newer Lost Pines Power Project built in the 2000/2001 timeframe.
When the two operations merged in February 2005, Runkle, who had been production manager at Sim Gideon, took over the job for the combined operation. It quickly became apparent that an upgrade of the combined plants’ communication system would be needed, he says. Sim Gideon’s 42-year-old Public Address (PA) system was rapidly reaching obsolescence. And because the newer plant had no PA system, it was extremely inefficient to try to page and otherwise locate plant mechanics and technicians, who could be working on either of the two sites.
A request for proposals for a hardwired PA system produced “sticker shock,” as Runkle puts it. But through a 12-year-old LCRA alliance with Invensys, Runkle heard about the Invensy/Apprion approach to wireless, and inquired about its possible use to meet Lost Pines’ communication needs. A July 2006 site assessment by Apprion and Invensys showed that “it was very doable,” says Runkle, despite the preponderance of large steel structures at the Lost Pines facilities.
The project proceeded, albeit with various issues and challenges, including those described at the top of this story. But in the end, says Runkle, Lost Pines ended up with a highly effective system that includes a 360-degree WiMAX backhaul system, creating a wireless umbrella over the facility. A total of 51 Wi-Fi access points were installed throughout the plants for local area network access, and the common infrastructure enabled VoIP to support wireless communication using a voice-activated pendant that workers wear around their necks. Wireless speakers were installed throughout the facility, and the system integrates with the private branch exchange (PBX) system and personal cell phones for enhanced connectivity.
The entire infrastructure was put in for a cost of “a little over $400,000,” says Runkle, compared to a $560,000 price tag quoted for a hard-wired PA system, prior to any cost adders. And now, given the vendor- and standards-agnostic nature of the WiMAX backhaul system, says Runkle, “any future wireless applications that we choose to purchase can be easily added to the foundation that’s already in place. So the return on investment will just continue.”
Mesh Tests
Beyond Wi-Fi and WiMAX, one of the most discussed technologies today in the industrial space is wireless mesh sensor networking. Runkle, for one, has been working with Emerson regarding future testing of some of that vendor’s forthcoming products in this arena. And the PPG Lake Charles plant has been working with Emerson as a beta test site for the vendor's emerging Smart Wireless mesh networking family since late 2005, Gerami says.
As with other wireless technologies, PPG has done its wireless mesh testing in its A Caustic unit. “We brought our 900 Megahertz (MHz) Elpro technology there [to A Caustic], our 900 MHz wireless mesh Emerson technology there, our Wi-Fi, and we also had WiMAX there for a little while, just to make sure that coexistence wasn’t an issue,” Gerami explains. “And they seemed to work very well, all together, and are still working very well.”
PPG’s initial Smart Wireless tests involved eight wireless sensors to provide redundant tank level measurements for some existing radar level systems. “With the radar only, we were strapping, or measuring, the tanks by hand every four hours,” Gerami says. “But now, with the radar and the Emerson wireless level sensors in place, we strap it only on Sundays.”
Subsequent Smart Wireless tests involved 10 additional sensors to measure steam pipeline temperatures. “Those pipelines had no temperature measurements on them at all before,” notes Gerami. The mesh technology has worked so well that PPG’s long-term plan now is to install Smart Wireless-based temperature profiling across the entire plant, says Gerami. “I think we’ll have that running by the end of the year, if not before.”
PPG is continuing to work with Emerson for beta testing of additional Smart Wireless product technologies. The list includes wireless vibration monitors, wireless corrosion monitors, instrument health monitors and a wireless device manager for Emerson’s AMS Suite of predictive maintenance applications.
Benefits Galore
So far, PPG’s total cost to purchase, install and test the full range of Wi-Fi, WiMAX and wireless mesh technologies has been in the neighborhood of $400,000, Gerami says. But the savings in conduit and wiring costs from use of the wireless mesh technology alone has already amounted to $216,000 in 2006, he notes, with an additional anticipated savings of $343,000 in 2007 and 2008. That’s not to mention anticipated benefits ranging from improved productivity of workers equipped with wireless tablets and handheld devices, to the elimination of telephone lease lines and the ability to gather data wirelessly that was previously unavailable in the wired world.
Despite some of the problems and challenges encountered, neither Gerami or Runkle have any regrets about being early movers in the wireless space. Both feel the efforts have given their operations an advantage going forward.
“I do feel like we’re really trying to be cutting edge with wireless,” Gerami observes. “I wish we were further along than we are. Rita and the strike really hurt us. But we’re trying to get it together and move forward, because there are a lot of savings here. This is really good stuff, and we’re excited.”
Lost Pines’ Runkle is no less effusive. “We’re going to be ready for whatever comes along in wireless,” he says. “I think we’re ahead of the game. And there’s no doubt in my mind that wireless is going to be the next big thing in the process world,” he declares, “because it works.”
To see the accompanying sidebar to this story - " Wireless Standing Emerging " - please visit http://www.automationworld.com/view-3553
For additional information, search keywords “Wi-Fi,” “WiMAX” and “wireless mesh” at www.automationworld.com.
Companies in this Article
Sponsored Recommendations
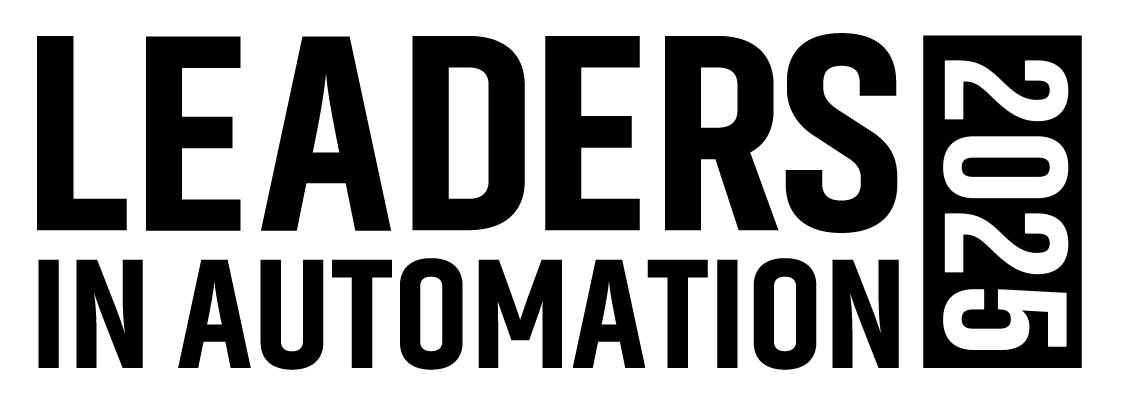
Leaders relevant to this article: