The recent recall of chili sauce and other products by Castleberry's Food Co., in Augusta, GA., shows how information can be the friend of consumers and companies alike. From the first reports of people getting sick to initiating a recall and then widening that recall, information from the factory to the consumer is required. For example, information from the grocery in the form of a Kroger Plus Shopper’s Card account contains a record of purchases, including a possible recalled product. The next time the card is used, the user is alerted to the previous purchase with instructions on how to check the lot number of the product and what to do if it’s on the recall list. When you are dealing with the health and safety of the public, information is your ally in times of trouble, protecting your customers, your brand image and even your bottom line.With some of the disease scares that have hit the meat producing industry, it’s sometimes a good idea to be able to trace a product all the way from the grocery shelf through the meat packer to the farm, and maybe even to a particular herd of cattle. Fortunately, there are tools in general use that will allow companies to accomplish much, if not all, of this goal. Starting with bar codes and radio frequency identification (RFID) on the input side, a complete solution includes database software, analytics and human intervention.Mike Hader is director of Information Technology at Odom’s Tennessee Pride, in Madison, Tenn., and says that not only is detailed information critical, but so is the time required to report. “We’re a meat producer,” says Hader, “and we’re governed by the U.S. Department of Agriculture for some of the track-and-trace requirements. At our Little Rock , Ark. , plant, we bring in live animals and process them. Under the rules, if there’s a product safety issue that comes up, we have to do a lot of tracking. Information on the sourcing and distribution of a lot must be available in a detailed report within two hours. And the time frame keeps growing shorter.”The challenge is getting information into the system. Hader uses an enterprise resource planning (ERP) system from Alpharetta, Ga.-based Infor Global Solutions. The system, which tracks production lots with a “where-used” field, requires a lot of control over inbound ingredients. Says Hader, “We make sandwiches at our Dickson, Tenn. , plant using meat processed by our Little Rock plant. We also purchase bread, egg patties and cheese. All are lot-controlled from their respective manufacturers and tracked in our system. We have to record where each lot came from and which outbound lots they were in. We use bar coding as input into the ERP system. When we bring out the meat, we scan the lot number. It’s recorded as an input and reported as part of the finished goods.” RFID somedaySpeaking about future technology, Hader predicts, “Eventually we’ll embrace RFID for all of this. Theoretically, this technology would remove labor from the process. Another benefit would be reducing errors introduced into the system, either by keying in data or in scanning the bar codes. But these systems are still pretty young. There are issues with read rates and how to assure a successful read. Tag prices still need to drop, too. Then there is the problem of scanning near metal, but even more important are problems induced by high moisture content. On the other hand, remember that it took 30 years for bar codes to make it to the consumer part of the chain.”The real benefit of RFID, notes Hader, is that it would be more finite than a bar code system. “You want to narrow down any recall, so if you can get more granularity with your process and determine that any irregularity is confined, then you can reduce your cost of recall.”The Infor ERP system was installed in 1999 as part of a “Y2K” project, and then upgraded in 2004. It enables creation of production lots used for both incoming material and outgoing product. The system does historical tracking of both work-in-process and finished goods. The quality group “owns” the lot control portion of the system. It is charged with doing microbiology testing at specific stages. A lot will be placed on hold while testing is occurring, and the ERP system won’t allow a further action until the hold is
lifted. Upon shipping finished goods, information gathered includes how many lot numbers are shipped for each particular stock keeping unit (SKU), the quantity, SKU and lot numbers for each item shipped.Products are shipped from Dickson to contracted warehouses before distribution to retail customers. The warehouses are different vendors, but their tracking processes are integrated into Odom’s. These third-party warehouses must report each end-customer shipment every night. They have the same hold status procedures as the plant. Hader says there are about 400 different reports out of this system. The quality, production and order-to-cash subsystems all use the same lot database.Odom’s system also provides timely information for users within the production and supply chains. For a given SKU, an inventory dashboard shows inventory levels, in-transit items and demand for shipments coming up. This latter item can be drilled into using a daily window on demand running 10 days into the future. On the inventory item, there is the ability to drill down into lot details, how many and where everything is located, including in which third-party warehouse. The system can even show which slot number within the warehouse the inventory is sitting. The dashboard is constructed in Dynamic HyperText Markup Language (DHTML) for display in a browser. Hader adds, “Everyone in the plant relies on this system. It is the one version of the truth. This is the bible for everyone.”Odom’s Tennessee Pride purchased a fully functional ERP system with manufacturing execution system (MES) built in. Another option is to build your own MES. Of course, one problem with building your own system is keeping up with technology advances, as well as increasing requirements as the system needs to grow.David Lamb is manufacturing applications manager at meat products producer John Morrell and Co., inCincinnati . He says the company has been on a path of increasing automation since the mid-1990s. The first automated data gathering was from bar-coded case labels. Then the company started to track work-in-process in the pork slaughterhouse. This system would track the slaughter and first cuts of fresh pork. “We started with manual tickets keyed into a back office costing and reporting system,” continues Lamb. “We implemented it into two fresh pork facilities three years ago, then wanted to move to processed meats operations.”The fresh pork tracking application was written in house, but development time for the staff, plus limited internal knowledge of the MES state-of-the-art, created a challenge for the company in expanding and upgrading its system. “We decided that we should go with an MES application in order to take advantage of increased features. I went to a MESA (Manufacturing Enterprise Solutions Association) meeting three years ago and gathered a number of vendors to do a proof of concept. We selected one company, which eventually was purchased by Rockwell Automation.”Material challenges One challenge Lamb noticed while evaluating MES suppliers was that all of them had backgrounds in discrete manufacturing. He was not sure that this would be a good fit for meat processing. His system had to deal with the fact that the raw material was not uniformly consistent. It had to consider varying weights, fat content and many other variables. Another challenge came directly from his experience with the first application. The company had originally hired a system integrator who worked with a particular MES supplier. As Lamb puts it, “A few months down the road, we found that the solution was too expensive. So we took the project in house to get what we wanted for less expense, plus to give us more control over the look and feel and responsiveness of the system. With the second system, we wanted to take advantage of best practices from industry, giving us the ability to grow the system in addition to all the standard MES functionality.”Some of the added functionality Lamb is looking for in the final system—it’s still in the final roll-out phase—is the ability to get all of the data collection functions for every transaction on the floor and into the ship-to-cost application. Eventually, the system can move into line controls and performance monitoring for equipment. Further, Lamb is looking for increased control of what goes into processed meat blends. Finally, the system needs to interface with other packages such as production scheduling and the ERP system.After the first implementation situation, Lamb took a more cautious approach this time. Following supplier evaluations and selection, his team specified the functional requirements of the system. They then went through four months of initial design and development work from December 2005 through March 2006. Sign off on the project was March 2007 with final rollout continuing through July 2007. This project is part of a three- to four-year commitment by John Morrell and Co. for automation systems. Another part of the caution is in the approach to implementation—as in not taking a “ram it down their throats” attitude. “We’ll have to wait for operations to find their needs on their own. We can’t just tell them. But we do have to be in a position to respond when they do recognize a need. We’re literally trying to guess the future. We may not have the exact thing they want, but we have to respond quickly when they request. With an MES package, we don’t have a fixed next step. We can go whatever direction the business needs.”Available for analysisBeyond inventory tracking and narrowing a potential recall situation, there are several other reasons for implementing a tracking application. Bob Lenich, business development manager, pharma, for process controls vendor Emerson Process Management, in Austin , Texas , sees several other ways customers are using track-and-trace technology.“One part of the application is on the operations side for when you lay out an order and execute it,” Lenich says. “With the advent of electronic records, you can have all your batch and materials information available for analysis. Then, engineering has much more control of changes.” Genealogy is important, Lenich allows. “But the most immediate requirement is to assure the right ingredient goes in the batch,” he says. “And not just the right ingredient type, but also checking such quality attributes as expired date or proper refrigeration. A lot of companies either never had the data or had data scattered all over the place. One company I worked with had 250 different spreadsheets or other places for data. So if you just consolidate all this in one place, you’ve achieved a major objective.”Gregg Le Blanc, director of technical strategy at OSIsoft Inc., a San Leandro, Calif.-based supplier of enterprise historian and related software, agrees that using an MES system for tracking can pay benefits for end-users. “Some companies do it because they have to, but those that benefit the most decide that they are going to use these systems as a way to improve the way they do business,” Le Blanc says. “Look at the Wal-Mart RFID initiative. Many companies just took a slap-and-ship approach. Others took it as a way to implement further implementation of the [Food and Drug Administration’s] 21 CFR Part 11 electronic batch record regulations. Now the business benefit is the ability to release products to market faster since the paperwork is easier.”There are still other federal regulations that are best met with an electronic solution. Jamie Bohan, segment marketing manager for developing markets for vendor Honeywell Process Solutions, in Phoenix , points to the U.S. Bioterrorism Act (Public Health Security and Bioterrorism Preparedness and Response Act of 2002) as another reason. “You have to be able to show where an ingredient came from and where the final product was shipped,” says Bohan. “Food safety is a big concern on manufacturers’ minds right now.” In addition, Bohan notes, some companies use the fact that they’ve implemented an electronic track-and-trace solution to alleviate consumer concerns and to differentiate their brands. Some manufacturers also find that implementation of this solution can result in improved business processes by automating previously human tasks, he adds. For example, having humans complete and maintain equipment sanitization logs, inventory tracking records and the like is error prone and time consuming. If these processes are included in the trace-and-track solution, reliability of these forms and information is greatly improved, Bohan says.Bob Gates, global technical manager for consumer products and healthcare for GE Fanuc Automation, a Foxborough, Mass.-based supplier, concurs that there are benefits to a company that go beyond the obvious tracking and genealogy applications. “Tracking product genealogy is a key part,” says Gates. “But more important is tracking through the processes. Answer questions such as, ‘How well are we doing?’ ‘What’s the operating equipment effectiveness (OEE)?’ and the like.” Companies with good business sense improved profits after the laws were passed by moving beyond the law into better quality, improved efficiency and root cause analysis,” Gates says. “OEE is becoming a more important measure than ever.”Data correlationSometimes, the added information allows correlation of data that leads to unimagined benefits. Says Barry Lynch, Proficy product manager at GE Fanuc, “We were working with a dairy company in Europe who wanted to track the genealogy of the milk. The thing that blew them away was when they found out it was a simple matter to track energy consumption while making the batches and then correlate the two. It helps them calculate margin per customer—a number valuable for further business analysis.”An MES implementation is only as good as the data input. There are only a few current methods: manual entry, RFID, vision systems and bar code. Alex Stuebler, manager of factory automation sensors at Siemens Energy & Automation Inc., in Alpharetta , Ga. , and Maryanne Steidinger, senior market development manager, also at Siemens E&A, discuss the role of MES and RFID input. Take the case of an engine manufacturer that needed to implement a tracking system with MES and RFID. Steidiger notes that when companies with an ERP system put out a request for an MES system, it is for track-and-trace as one of the key components. “If you have a repair item, you need to isolate the products affected when you initiate the recall. Track-and-trace is one way you know what went into the car, helping with the recall problem.” The engineering and IT departments need to work together on this issue, she says. Adds Stuebler, “There was an engine manufacturer where the IT department implemented an MES and looked into RFID for data collection. They didn’t talk to the controls department who already had RFID installed all over the plant.”
To see the accompanying sidebar to this story - "Bar Code Label Tips" - please visit www.automationworld.com/view-3496 For more information, search keywords “track-and-trace,” “tracking” and “traceability” at www.automationworld.com.
lifted. Upon shipping finished goods, information gathered includes how many lot numbers are shipped for each particular stock keeping unit (SKU), the quantity, SKU and lot numbers for each item shipped.Products are shipped from Dickson to contracted warehouses before distribution to retail customers. The warehouses are different vendors, but their tracking processes are integrated into Odom’s. These third-party warehouses must report each end-customer shipment every night. They have the same hold status procedures as the plant. Hader says there are about 400 different reports out of this system. The quality, production and order-to-cash subsystems all use the same lot database.Odom’s system also provides timely information for users within the production and supply chains. For a given SKU, an inventory dashboard shows inventory levels, in-transit items and demand for shipments coming up. This latter item can be drilled into using a daily window on demand running 10 days into the future. On the inventory item, there is the ability to drill down into lot details, how many and where everything is located, including in which third-party warehouse. The system can even show which slot number within the warehouse the inventory is sitting. The dashboard is constructed in Dynamic HyperText Markup Language (DHTML) for display in a browser. Hader adds, “Everyone in the plant relies on this system. It is the one version of the truth. This is the bible for everyone.”Odom’s Tennessee Pride purchased a fully functional ERP system with manufacturing execution system (MES) built in. Another option is to build your own MES. Of course, one problem with building your own system is keeping up with technology advances, as well as increasing requirements as the system needs to grow.David Lamb is manufacturing applications manager at meat products producer John Morrell and Co., in
To see the accompanying sidebar to this story - "Bar Code Label Tips" - please visit www.automationworld.com/view-3496 For more information, search keywords “track-and-trace,” “tracking” and “traceability” at www.automationworld.com.
Sponsored Recommendations
Sponsored Recommendations
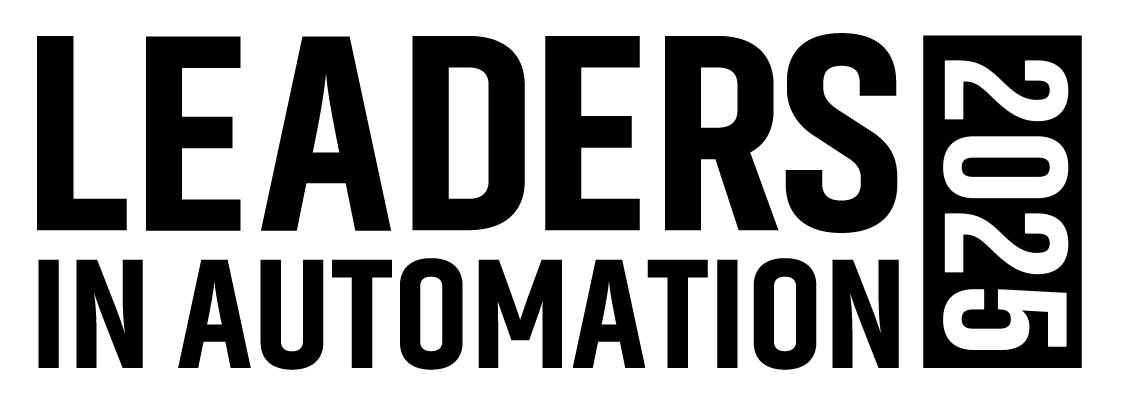
Leaders relevant to this article: