OK, so you’ve automated your factories and leaned out your supply chains. You’ve squeezed out every ounce of inefficiency. You’ve got your machines, your processes and your materials under control, and now the gains are getting harder to come by. With the low-hanging fruit off the vine, maybe it’s time to take a closer look at more efficiently managing your labor force. It’s one area that many manufacturing companies have neglected, says Christa Degnan Manning, a research director at AMR Research Inc., in Boston . “While the concept of strategic human capital management (HCM) has been around for a long time, it’s surprising to me how few companies have really taken a hard look at their workforces and understood and appreciated the impact that personnel have on the success of a company,” Degnan Manning observes. “Unfortunately, I think manufacturers have put so much attention on the supply chain and supply utilization, that they’ve kind of neglected this whole workforce component.”Double digitsBut that is beginning to change. A variety of enterprise software vendors are taking aim at the space. And Degnan Manning says that HCM today is the single, fastest-growing enterprise application, with buying by manufacturers leading the surge. According to AMR, the worldwide market for human capital management software grew by 16 percent in 2006 to $6.3 billion, up from $5.4 billion in 2005. “And we are projecting that it will grow by an 11 percent compound annual growth rate through 2011, when it will be more than a $10 billion market,” adds Degnan Manning. Around 50 percent of the market is driven by manufacturing companies, which are increasingly waking up to the software’s advantages, she says.One company that is starting to cash in on HCM technology is Elliott Co., a Jeanette, Pa., manufacturer of large turbines and compressors that is a subsidiary of Japan-based Ebara Corp. Elliott previously tracked time and attendance of its 250 hourly employees using manual spreadsheets, says John Russo, senior business systems analyst in Elliott’s information technology (IT) department. But when the company installed an Oracle enterprise resource planning system in 2004, it also installed workforce management software supplied by Kronos Inc., of Chelmsford , Mass. With the Kronos system, Elliott employees use any of about 30 personal computer (PC)-based platforms on the company’s factory floor to clock in when they start a job, and to clock out when they finish the job or end their work day. Employees either enter the data on the PC keyboard or scan their bar-coded employee badges along with bar-coded job work numbers, says Russo. The time and attendance module within the Kronos system enables Elliott to track attendance and manage vacation and overtime pay based on union work rules. Russo estimates that the system saves 15 to 30 minutes per day for each of about 15 foremen at the company, who previously had to manually enter the data for each employee. The system has also improved record-keeping accuracy, he adds.Beyond that, however, Russo notes that the activities module within the Kronos system is providing valuable workforce-related intelligence. “We have a lot of metrics that we get out of the system that actually help us manage our work effort,” he says. “Efficiency, productivity and utilization are three common measurements that we watch.”Russo explains that each job within the company has assigned standards that include the amount of time required for completion. The Kronos system enables precise tracking of these hours vs. the hours that Kronos workers actually take to do the job. “If one of our industrial engineers estimated that a job would take, say, 15 hours, and the worker charges 16 hours to that job, then we know we’re an hour over,” Russo says. When combined with an analytics package and some PC graphics dashboards developed by Russo that allow managers to drill down into the data, the Kronos system provides visibility into areas where the workforce is underperforming vs. the standards. When this happens, “since our standards are what our costs are based on, and what we try to sell against, then we know we’ve got some adjustments to make,” says Russo. “Either we have to find ways to get our employees more productive, or we have to raise our standards, and unfortunately, raise costs, which is not acceptable, because it’s pretty much a buyer’s market in our business.”Russo notes that some foremen “really aren’t all that keen” on the system, which can reveal inefficiencies within their areas. “Not everybody likes to be measured,” he says. “But usually, once they know what the measurements are, they’ll try to work on them and improve in those areas.” Notable gainsBy spotlighting areas where workforce efficiency and productivity improvements are needed, the Kronos system has already enabled management to take steps that have contributed to some notable business gains, Russo indicates. One business division that was running at only a 50 percent on-time delivery rate in 2005 has boosted that number to 80 percent to 90 percent currently, while turning a 5 percent loss in 2005 into a 5 percent profit in 2007, says Russo. At Kronos, Vice President of Enterprise Marketing Charlie DeWitt notes that Elliott Co. is one of the vendor’s most forward-thinking customers, and has provided inspiration for some of Kronos’ latest solutions aimed at advancing the state of factory workforce management. The company’s Kronos for Manufacturing line includes a Workforce Analytics module, for instance, that is designed to help companies integrate workforce data with other factory data to develop key performance indicators (KPIs), says DeWitt. “The Workforce Analytics engine will take data out of the MES (manufacturing execution system), take data out of the MRP (manufacturing resource planning) systems and take data out of our own systems and put them all together in a way that department managers can use in real time to eliminate waste and defects,” says DeWitt. Kronos has recently drawn upon a widely used equipment-oriented metric known as overall equipment effectiveness, or OEE, to develop its own KPI pegged around workforce data. OLE, for overall labor effectiveness, says DeWitt, is a KPI developed by Kronos to help manufacturers “look at the labor component on operating efficiency and effectiveness, as opposed to just the equipment effectiveness piece.”The last frontierTaking a similar tack with its workforce management products is Workbrain, a Toronto-based company that was recently acquired by Infor Global Solutions, the Alpharetta, Ga.-based enterprise software vendor. “The workforce is really the last frontier that manufacturers need to tackle in order to optimize, integrate and improve their processes,” says Marc Moschetto, industry marketing manager at Workbrain.Moschetto divides workforce management into three core categories. The first is time and attendance, which is a traditional, yet critical, part of a comprehensive workforce management package, he says. The second is scheduling, which builds upon the information available from having the payroll process 100 percent automated. “As part of the system, you have access to this very robust, very granular pool of data, so you can do a lot more,” says Moschetto. “You understand who is doing what, who has what skill sets, their availability and their current overtime status, so it allows you to schedule more effectively.”Layered on top is the third piece—reporting and analytics—which enables more advanced activities, Moschetto says. Through analytics and reporting, a manufacturer might discover inefficiencies that would otherwise go undetected, he says. For example, if a report shows a significant delta between the time employees clock in at the front gate and the time they clock in to actually begin work on a job, that could provide an area for investigation. Are work orders not ready for employees when they get to their workstations? Are other factors involved? “We have one customer that has actually projected that they’re going to save $700,000 this year just in lost-time savings alone,” Moschetto says.Seven to oneEven without the analytics, converting from a manual time and attendance system to an automated system can produce lost-time savings. “We have about nine plants with manual time cards, and it’s fairly easy to write on your card that you came in at 6 and you left at 6, and that you took a 30-minute lunch. But there’s no validation of that,” says Paul Karlzen, senior program manager, information technology, at Ball Corp., headquartered in Broomfield, Colo. A longer lunch break or a late arrival for work would not necessarily be captured. That is one reason that Karlzen expects that Ball will see “significant lost-time savings” after it finishes converting its North American plants to a centralized time clock-based time and attendance system provided by Infor Workbrain. Ball—a $6 billion global manufacturer of aluminum and plastic beverage and food containers, aerosol packaging, and aerospace products—has acquired a number of different plants over the years. The company now has more than 40 factories in the United States , Canada and Puerto Rico , with some 6,500 hourly employees, says Karlzen. The problem, according to Karlzen, was that after all of the acquisitions, “we had seven different time-keeping systems. To maintain all seven was costing us quite a bit in annual software maintenance costs,” he says, “and it was difficult to support seven systems.” So in 2005, Ball selected a Web-based workforce management system from Workbrain as a single solution for all of its plants. Following a pilot installation at a one plant in 2006, Ball now has seven plants using the system and plans to complete the rollout of the Infor Workbrain system to all of its North American plants by the first quarter of 2009, Karlzen says.With the Infor Workbrain system, workers clock in and clock out for work shifts using proximity cards at time clocks on the plant floor. They can also use the system to record a change during the work day from one job to another that might have a different pay scale. The improved accuracy afforded by the Infor Workbrain system is producing immediate savings, Karlzen says. “In our first plant, we saw a 46 percent reduction in on-demand checks,” he notes, in reference to mid-pay period checks issued to correct errors, such as underpayment for overtime hours. “In one of our other plants, we did not have a single on-demand check for the first three months,” Karlzen adds. “I think it’s because Workbrain is so customizable that we can configure any payroll that we have, so we don’t have the exceptions that we used to have.”Indeed, the easy configurability of the system was a major selling point for Ball, says Karlzen, given that the company has both union and non-union plants in multiple states and locations, all with differing work rules. Ball plant officials in Canada and Puerto Rico were also impressed with the system’s ability to convert almost instantaneously from English to French Canadian or Spanish, he adds. The latter capability will be particularly important in a second phase of the project, when Ball plans to use the system’s self-service “employee transaction manager” module, enabling workers to view vacation and leave balances on the Web-based system, and to put in requests for time off. The self-service capability will translate to reduced administrative costs for Ball, he says.Other savings will come through elimination of an estimated $100,000 per year in software maintenance costs, once the system is fully implemented across all Ball plants, says Karlzen, “because we won’t have to pay seven different vendors any more.” Better decisionsHe also expects that the centralized system will lead to better workforce decision making. “When we have seven different [time and attendance] systems, it’s almost impossible to get company-wide statistics on how many people are on FMLA (Family Medical and Leave Act) leave, how many are out sick, and what our lost time is,” Karlzen points out. “But by having a single system, we’ll be able to get enterprise-wide data on our labor and on what’s happening at our plants. And I think that’s going to be very valuable going forward.”To see the accompanying sidebar to this story - "HCM Defined" - please visit www.automationworld.com/view-3424 For more information, search keyword “workforce” at www.automationworld.com.
Sponsored Recommendations
Sponsored Recommendations
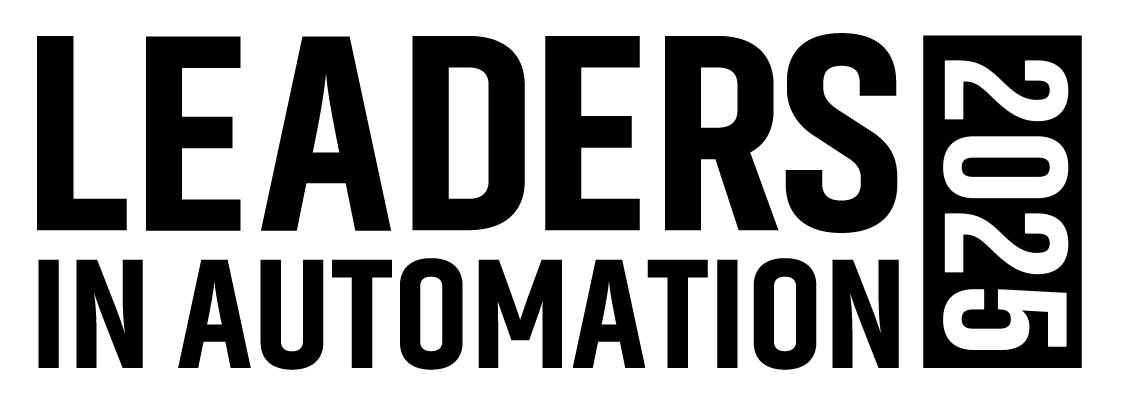
Leaders relevant to this article: