If all goes as envisioned, the first “boot camp” will kick off some time next year. “Our current plan is for this to last for about two weeks. It will be eight working days, and we’ll have folks stay across the weekend as well. We’ll have fairly intense, 12-hour type days, a lot of lab work, a lot of instructional work and then homework each night,” says Nick Sands.No, Sands is not some sort of hard-driving drill sergeant. He’s a process control technology manager who heads up a corporate workforce competency group for automation and process control at DuPont Co., the Wilmington, Del.-based chemicals and materials giant. And Sands believes that the target audience for the boot camp will jump at the chance to attend—even though they’ll be giving up a weekend—due to the wealth of information and networking opportunities being planned for the event. Disappearing talentThe “boot camp” that Sands is talking about is part of DuPont’s response to the looming automation workforce skills gap. Like other manufacturing companies, DuPont is facing a potential wave of retirements by baby boomer engineers and other professionals over the next several years, with too few replacements waiting in the wings. “We estimate that more than 25 percent of our process control talent is going to disappear during the next five years and more than 50 percent will be gone within 10 years,” says Sands. At DuPont, five to seven years are traditionally required for newly hired chemical and electrical engineers to become fully proficient in the company’s process control best practices, Sands notes. The boot camp—intended for new and lesser experienced engineers and other DuPont employees moving into process control—is one idea to help shorten that time period, by providing participants with an early, concentrated dose of DuPont foundational training, including standards, policies and practices. “We want to bring people up to speed to contribute faster, and also make them more aware of what our best practices are, and the tools and resources that are available across the company,” Sands explains.The idea for the “boot camp” training first came up during an internal brainstorming session held late last year at DuPont on ways to address the potential talent shortage, says Sands. The initial process control engineering boot camp could be held as soon as next year’s first quarter, and if successful, may be repeated once or twice annually. “If it works well, then we might also have some other boot camps assembled around maintenance and reliability, or around process engineering,” Sands adds. DuPont is not the only manufacturing company that is developing new approaches to try and head off what many see as an impending workforce crisis. A recent report from ARC Advisory Group Inc., Dedham , Mass. , found that leading process industry manufacturers are taking a variety of steps to deal with the issue. The list of actions ranges from increased development of corporate-wide training standards and increased use of certification and testing, to more formal mentoring programs and the use of online repositories to capture best practices, guidelines, methodologies and standards. Some manufacturers are also stepping up collaboration with local technical schools, as a way to get more people with needed skills. This includes equipment donation and
participation in curriculum development, according to the April 2007 ARC report, titled, “Human Factors Best Practices for Automation—Addressing the Skills Gap.” More process companies are also making use of high fidelity simulators with accurate plant models for training, says the report. And at least one company is even using a mothballed plant unit as a full-scale training simulator.Too Little, Too Late?Despite the efforts underway by leading companies, however, the ARC report points out that many manufacturers are still doing too little to stave off a coming skills shortage. More than 60 percent of manufacturers surveyed by ARC still provide less than 2 percent per year of work time for training and development, for example, and most report that training budgets are either staying the same or shrinking. Maurice J. Wilkins, an ARC vice president and author of the report, warns that too many manufacturers are taking a “head-in-the-sand” approach to the impending skills gap. “By the time they react,” he says, “it may be too late.”Post-boomer gapFew would argue that the potential for a manufacturing talent catastrophe exists. It’s a matter of demographics. At some 76 million strong, the massive baby boom generation—born between 1946 and 1964—is now nearing retirement, with the oldest boomers turning 60 last year. At many manufacturers, boomers make up the bulk of the engineering and operator population, not to mention much of mid-level and upper management. And there simply aren’t enough people in the next age group—the so-called Generation X born in the 1960s and 1970s—to replace them.Making matters worse is that manufacturing lacks appeal for many of today’s youth. Young people are interested in computers, but want careers in Internet and computer gaming related areas, says the ARC report. “There is a huge opportunity for manufacturers to convince these young people that there is a challenging future for them in manufacturing, involving all the computer skills needed for computer games, but in the real world.”In fact, a K-12 education effort designed to elevate the automation profession in the minds of today’s youth is one of multiple projects planned as part of a new workforce development program launched on June 7 by the Instrumentation, Systems and Automation Society (ISA), based inResearch Triangle Park , N.C. (See “ISA Targets Workforce Development,” July 2007, p. 17). ISA Executive Director Patrick Gouhin estimates that industry will have a need for about 15,000 new automation professionals per year in the future—a requirement that he says “far exceeds the supply in the pipeline today. We must take action now,” Gouhin declares, “to make sure that we mitigate the potential damage that would be done by not having the necessary workforce with the necessary skills that will be needed to maintain the pace of advancement that we’ve seen in recent decades.” In agreement is Dorothy Hellberg. “I do believe there is a crisis. I see it in our own organization. If you look at a timeline, we’ve got people who are 50 and above, and we have people who are 25 to about 35. But there is a huge gap in that 35-to-45 age group,” says Hellberg, director of educational services for Emerson Process Management, the Austin, Texas-based process automation vendor. And she sees a similar worker age gap at many of the company’s customers. Hellberg, who is based in Marshalltown , Iowa , at Emerson’s Fisher Controls operation, oversees both internal training of Emerson Process Management employees, as well as external training that the vendor does for its customers. And while she believes that many manufacturers “are going to be caught short” by the exodus of baby boomer talent in the years ahead, Hellberg believes that companies that recognize the problem can take steps to help fill the gap. Keep ’em challengedInternally, for example, Emerson Process Management has in recent years stepped up college internship programs aimed at attracting new graduates as employees, and is providing more training opportunities for those new hires once they have signed on. “One thing we’ve learned is that younger people today are very hungry for learning, and if you don’t keep them stimulated and challenged about what they’re doing, and encourage them to contribute, they are more apt to leave sooner,” says Hellberg. The company also provides cross-training for its more seasoned employees, and encourages lateral moves as a way to provide more personal stimulation for employees while also adding value to the organization. Other efforts include both formal and informal leadership mentoring by senior management “as a way to bring select individuals along a little bit faster in the organization,” Hellberg says.Emerson Process Management began beefing up these and other initiatives starting about five years ago, when the company first began feeling the impact of some early boomer retirements, Hellberg indicates. At that point, she says, “we just kind of had to kick ourselves and say, ‘You know what, if we don’t start doing something, we’re really going to have a problem.’ ” Indeed, for some companies, getting started may be the biggest hurdle. “The skills shortage is somewhat like the global warming issue, in that there may be overwhelming evidence that it’s going to be a problem, but that doesn’t necessarily spur immediate action,” says a manager at one major manufacturing company. “Everyone may know about the demographics, but translating that into an action that has a cost impact today is still a tricky thing.” Training by simulationOne company that is making an investment is Eastman Chemical Co., which is installing a process operator training simulation system at its Longview , Texas , petrochemical plant. The DeltaV OTS Express (for Operator Training Simulation) system supplied by Emerson will be used in a pilot installation initially to simulate utilities processes, including boiler operations, and steam and water distribution for the 6,000-acre plant.“We hope to set up a program through which our operators can demonstrate skills with several process scenarios that are thrown at them. So for our new trainees, it will be a training tool, and for our experienced operators who might not see one of these events but once every three or four years, possibly, it will be a way to keep skills sharp,” says
Carroll Greenwaldt, superintendent, Utilities and CoGen Operations, at the plant. Besides boosting process safety and productivity, Eastman sees the simulator as one potential way to help bring new process operators up to speed more quickly in an era in which many of its more experienced operators are approaching retirement. The company expects to launch its first simulator training this summer. If the technology proves successful for the utilities application, it may also be used for operator training in other, manufacturing units at the plant, Greenwaldt says. Like other manufacturers, the Eastman plant is facing potentially high employee turnover levels due to boomer retirements in the years ahead. “We could be needing to hire dozens of process operators per year over the next several years,” Greenwaldt says. As a result, the plant is taking a number of additional steps aimed at filling the gap. “In some cases, where we anticipate some early retirements, we are pre-hiring, to bring some new employees on board to have them several years down the road on experience levels before some of our more seasoned veterans step away,” Greenwaldt notes. Testing outOther efforts are intended to boost the skill levels of new hires coming in. The Eastman plant worked last year with nearbyKilgore College , in Kilgore , Texas , for example, to develop a two-year process technology operator curriculum, says Greenwaldt. The first class of 20 to 25 students began that program last fall, he notes. They receive summer employment as interns at Eastman, and upon graduation, are considered for full-time employment at the company. It’s an approach that is similar to one that Eastman has taken with other nearby technical schools that are part of the Texas State Technical College system. “When folks come to us having gone through these external programs with the colleges, they are already well along,” says Greenwaldt. As a result, they are often able to “test out” of a number of the modules that the plant would otherwise have required as part of its on-site apprentice training school, he notes. Other efforts to speed up skills development include accelerated cross training. There are four separate job categories within the utilities area at the Eastman plant, for example, and the company has recently been rotating its younger employees through each of the jobs more quickly than in the past, as a way to build broader proficiency levels more quickly. Compared to a three- to four-year rotation cycle in the past, young employees now get trained in all four job areas within about a year. Will these and other efforts be enough to enable the Eastman plant to head off any future skills shortage? “We’re doing what we can,” Greenwaldt responds. “We can see that we’ve got a skills challenge coming, and rather than being caught flat-footed, we’re really striving to get out ahead of the curve.”To see the accompanying sidebar to this story - "Looking For A Few Good Men to Work In Your Factory?" - please visit www.automationworld.com/view-3422For more information, search keywords “skills shortage” and “workforce” at www.automationworld.com
participation in curriculum development, according to the April 2007 ARC report, titled, “Human Factors Best Practices for Automation—Addressing the Skills Gap.” More process companies are also making use of high fidelity simulators with accurate plant models for training, says the report. And at least one company is even using a mothballed plant unit as a full-scale training simulator.Too Little, Too Late?Despite the efforts underway by leading companies, however, the ARC report points out that many manufacturers are still doing too little to stave off a coming skills shortage. More than 60 percent of manufacturers surveyed by ARC still provide less than 2 percent per year of work time for training and development, for example, and most report that training budgets are either staying the same or shrinking. Maurice J. Wilkins, an ARC vice president and author of the report, warns that too many manufacturers are taking a “head-in-the-sand” approach to the impending skills gap. “By the time they react,” he says, “it may be too late.”Post-boomer gapFew would argue that the potential for a manufacturing talent catastrophe exists. It’s a matter of demographics. At some 76 million strong, the massive baby boom generation—born between 1946 and 1964—is now nearing retirement, with the oldest boomers turning 60 last year. At many manufacturers, boomers make up the bulk of the engineering and operator population, not to mention much of mid-level and upper management. And there simply aren’t enough people in the next age group—the so-called Generation X born in the 1960s and 1970s—to replace them.Making matters worse is that manufacturing lacks appeal for many of today’s youth. Young people are interested in computers, but want careers in Internet and computer gaming related areas, says the ARC report. “There is a huge opportunity for manufacturers to convince these young people that there is a challenging future for them in manufacturing, involving all the computer skills needed for computer games, but in the real world.”In fact, a K-12 education effort designed to elevate the automation profession in the minds of today’s youth is one of multiple projects planned as part of a new workforce development program launched on June 7 by the Instrumentation, Systems and Automation Society (ISA), based in
Carroll Greenwaldt, superintendent, Utilities and CoGen Operations, at the plant. Besides boosting process safety and productivity, Eastman sees the simulator as one potential way to help bring new process operators up to speed more quickly in an era in which many of its more experienced operators are approaching retirement. The company expects to launch its first simulator training this summer. If the technology proves successful for the utilities application, it may also be used for operator training in other, manufacturing units at the plant, Greenwaldt says. Like other manufacturers, the Eastman plant is facing potentially high employee turnover levels due to boomer retirements in the years ahead. “We could be needing to hire dozens of process operators per year over the next several years,” Greenwaldt says. As a result, the plant is taking a number of additional steps aimed at filling the gap. “In some cases, where we anticipate some early retirements, we are pre-hiring, to bring some new employees on board to have them several years down the road on experience levels before some of our more seasoned veterans step away,” Greenwaldt notes. Testing outOther efforts are intended to boost the skill levels of new hires coming in. The Eastman plant worked last year with nearby
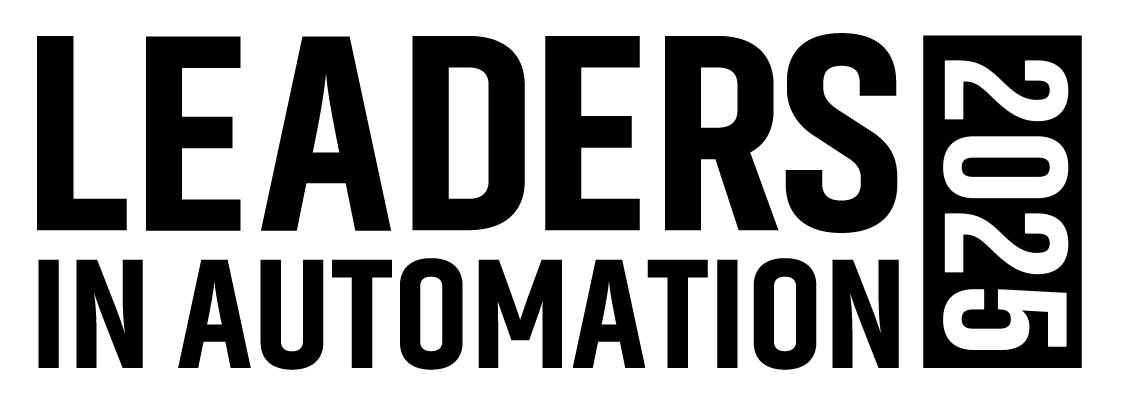
Leaders relevant to this article: