Propal Paper Production had a problem with its plant in Valle del Cauca, Colombia . The only data the plant had on its paper production was stamped on the end of each reel and was never stored electronically. With limited access to data, the company couldn’t make timely and efficient decisions or meet customer requirements accurately. These limitations hurt the company’s ability to compete.Plant managers decided to solve the problem by interfacing the plant’s quality control system, supplied by automation vendor ABB, with a manufacturing execution system (MES) supplied by Honeywell, another automation vendor. This would connect the data from three paper machines at the Valle de Cauca site and also connect with a machine at a remote site. The real-time data would then be available to corporate decisions makers. The data also had to be secure.There were two ways to create the connectivity. One was to use custom, vendor-specific protocols and write proprietary interfaces. Another option was to use OPC, an open connectivity standard. The advantage of OPC is that it is inexpensive and easy to use. It is quick to integrate and it provides a secure environment. Propal chose the MatrikonOPC Transporter to transfer historical data and the MatrikonOPC Tunneller to provide secure connectivity between systems. The off-the-shelf OPC tools eliminated any need to reconfigure existing information technology (IT) infrastructure. “OPC lets anything talk with anything. It lets you use any tool you like by any vendor,” says Steve Pearlstone, technical consultant at Matrikon Inc., of Edmonton , Alberta , Canada .The result, according to Mario Lopez, process control manager at Propal, was low-cost connectivity with no vendor-specific protocols or proprietary interfaces. The plants now have 6,000 data points connected that are updated every 30 seconds. With the wide connectivity, paper production is becoming increasingly efficient.Plants are beginning to adopt OPC and the more recent OPC Unified Architecture (OPC-UA) standard to connect plant-to-plant applications as well as plant-to-enterprise applications. The OPC standard is non-proprietary, inexpensive and it can tie a wide range of applications together. OPC was developed 12 years ago by a handful of companies in the automation industry under the authority of the OPC Foundation, in Scottsdale , Ariz. Three years ago, a group of 35 companies supported the foundation’s development of OPC-UA, an eXtensible Markup Language (XML)-based version. OPC-UA allows communication on the enterprise level and connectivity across the Internet. Foundation members now predict that in 10 years, every device will have OPC built in.There are a number of reasons that companies are seeking greater connectivity across plant and enterprise applications. For one, various systems within the plant itself need to be connected in order to achieve optimum efficiency. “The plant has islands of automation,” says Todd Stauffer, PAS manager, Siemens
Energy & Automation Inc., in Alpharetta, Ga. “To run the business best, the enterprise has to have data from all those islands, and it has to be able to push enterprise information back down to the plant.”The drive to connect internal plant applications and plant-to-enterprise applications comes from the desire to drive costs out of manufacturing. “In order to optimize production, plants want to make the most with the least. Raw materials, energy costs and the cost of the manufacturing process itself go into the cost of the product,” says Stauffer. “If you can connect applications and get a view of the plant’s operation, you can make the difference as to whether the company is profitable. That’s how thin the margins are.”Real-time information can help plants move from bulk production to on-demand, just-in-time manufacturing, which is more in line with customer needs. “With this information, decisions can be made at the higher level of the enterprise,” says Mike Panaleano, product manager for the software group, at vendor Rockwell Automation Inc., inMilwaukee . Visibility into plant operations can help companies make the transition to demand-based manufacturing. “Plants are no longer going to make stock. Now products have to be made-to-order,” says Panaleano. “It’s important that you’re not making cars that are dead on the lot.”Timely decisionsAnother big reason for connecting the plant to the executive suite is to make the company more competitive across a global market. “The modern chief executive officer (CEO) wants to be able to make decisions in a timely fashion, getting the most out of the IT and assets,” says Sean Leonard, director of the Matrikon OPS unit. “The global environment is shrinking and the CEO has to make decisions quicker than 20 years ago. More timely decisions mean you have to have more timely data.”While the reasons for connectivity are varied, the automation industry wanted a vanilla standard for connecting applications. The OPC Foundation was given that mission 12 years ago. A huge benefit of OPC was its ability to connect applications and devices from a variety of vendors. “The critical aspect of having connectivity and allowing multiple vendors to sell products is that end-users are actually able to use best-of-breed solutions,” says Thomas Burke, president of the OPC Foundation. “That’s the fundamental principle behind the OPC technology.”Plant operators are now using OPC to integrate applications within the plant itself or across multiple plants. “Most operators are using OPC primarily at the plant level,” says Matrikon’s Leonard. “They are using OPC for tying into other plants or central headquarters. They’re using it at the operator level across geographies.” That all changed when the OPC Foundation moved beyond OPC to OPC-UA three years ago. With OPC-UA, it becomes easier to connect the plant to the enterprise. With OPC gaining acceptance over the past 12 years—especially in the past five years—the industry wanted an XML-based version to enhance connectivity and make it available via the Internet. “We’ve moved the OPC standard forward with OPC-UA,” says Russ Agrusa, founder and CEO of Foxborough, Mass.-based vendor Iconics Inc. and an OPC board member. “With OPC-UA, you can communicate from the factory floor to IT, and IT can reach down to the PLC (programmable logic controller) and pull data out. The key is the XML capabilities. That allows you to go over the internet in a frictionless way.”One big advantage of OPC-UA is its ability to easily connect with the enterprise. Because it is based on Internet connectivity, it works well with enterprise applications. “OPC-UA is based on Web services,” says Craig Resnick, an analyst at ARC Advisory Group Inc., in Dedham , Mass. “It takes an enterprise flavor to an interoperability solution. With OPC-UA, you can truly connect SAP to devices on the factory floor,” addsResnick, in reference to enterprise applications provided by Walldorf, Germany-based vendor SAP AG.Another major benefit of OPC-UA is that it works better than standard OPC to connect a wide range of applications within the plant, particularly when plant assets range in age. “OPC-UA is a universal adapter, an overarching umbrella that allows you to connect to older legacy components,” says Alison Smith, senior research analyst at AMR Research Inc., in Boston . “Right now, it’s not deployed all that widely, but XML is going to become the standard way to package information between multiple applications.”Smith notes that OPC-UA will become widely adopted simply because it can connect to such a wide array of applications. “XML is the lowest common denominator,” says Smith. “It doesn’t matter if you’re connecting to the shop floor or to the enterprise. That’s why all manufacturing execution systems use XML. It’s self-describing.”Because it is self-describing, OPC-UA can take data from one application and “explain” to a second application what the first application is doing. “At the end of the day, all OPC-UA is offering is an application-to-application standard,” says Matrikon’s Leonard. “It’s like a piece of paper that says, ‘This is what this application is doing.’ OPC-UA is popular because it describes what the data looks like.”Other toolsThere are also some other XML-based connectivity tools. Remote procedure calls (RPC) and Really Simple Syndication (RSS) are used in plants for a variety of purposes, mostly in the area of alarms. These tools, though, are not nearly as widely adopted as OPC and OPC-UA. RPC and RSS are mostly used for alerts. “The only way I could see RSS having any role in manufacturing would be in messaging and paging on the factory floor,” says ARC’s Resnick.Agrusa from Iconics agrees. “The other XML technologies are for alarms and alerts. If you have a fire, you can get a call on the telephone, on a pager or use an RSS feed,” says Agrusa. “You can use RSS to provide the alert.”Industry experts believe OPC and OPC-UA will become widespread in plants across all industries. “In 10 years, every device will probably have OPC in it,” says Iconics’ Agrusa. “A lot of people are already working to get OPC in their devices. Soon, you’ll be able to communicate with every device.”According to Burke, of the OPC Foundation, the real business value of OPC and OPC-UA is the ability to help manufacturers become more competitive. “Companies need to streamline their operations and maximize their use of assets,” says Burke. “OPC provides the infrastructure to facilitate asset management applications to truly be able to access the information in real-time.”ARC’s Resnick agrees that OPC will soon gain wide adoption because of its business value. “We’re probably early in the curve toward mature use of OPC. There is a definite case to use OPC in more and more portions of the plant,” says Resnick. “Looking down the road, OPC will be as ubiquitous as PLCs on the factory floor. It’s going in that direction and there’s no turning back.” Resnick notes that no change happens unless there is a business case for it. With OPC, the business case is inexpensive connectivity that cuts across vendors, cuts across legacy systems and cuts across the enterprise.To see the accompanying sidebar to this story - “Connecting 4,000 Data Points” - please visit www.automationworld.com/view-3168 For more information, search keywords “OPC” and “connectivity” at www.automationworld.com.
Energy & Automation Inc., in Alpharetta, Ga. “To run the business best, the enterprise has to have data from all those islands, and it has to be able to push enterprise information back down to the plant.”The drive to connect internal plant applications and plant-to-enterprise applications comes from the desire to drive costs out of manufacturing. “In order to optimize production, plants want to make the most with the least. Raw materials, energy costs and the cost of the manufacturing process itself go into the cost of the product,” says Stauffer. “If you can connect applications and get a view of the plant’s operation, you can make the difference as to whether the company is profitable. That’s how thin the margins are.”Real-time information can help plants move from bulk production to on-demand, just-in-time manufacturing, which is more in line with customer needs. “With this information, decisions can be made at the higher level of the enterprise,” says Mike Panaleano, product manager for the software group, at vendor Rockwell Automation Inc., in
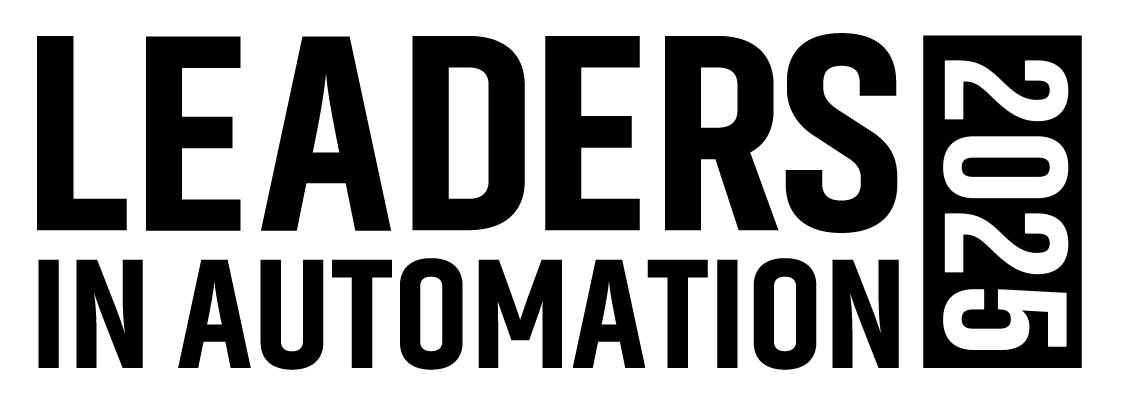
Leaders relevant to this article: