Have you ever paid attention to those high-quality stainless steel washing machines and dryers in commercial laundries? They are also found behind the scenes in hospitals, nursing homes, hotels and motels. Chances are they are manufactured in the Fairfield, Iowa, plant of Dexter Laundry Inc., a unit of Dexter Apache Holdings Inc. Making those huge commercial laundry machines at a profit is not an easy task. As Tony Praza, vice president of information technology and continuous improvement, says,
“Have you seen the price of stainless steel? It’s been skyrocketing.” Add to that the need to enhance product features while meeting competitive price pressures, and initiatives to reduce manufacturing cost rather quickly get pushed into high visibility.Dexter’s roots go back more than 100 years, and for a time, the company was part of Ford Motor Co. It’s now an employee stock ownership program (ESOP) company, a fact to which Praza points with pride. The manufacturing strategy Dexter is using to cut waste and improve profitability is Lean Manufacturing. To drive the Lean initiative and provide the kind of information it needs to do its job, Praza has led an effort to implement a shop-floor reporting system. In fact, Praza has been building shop-floor reporting systems since the 1970s, when he made a switch from engineering to systems. For the Dexter project, he uses software from Alpharetta, Ga.-based Infor Global Solutions.
“We’ve had the Infor XA MES MDCC Suite up and running for over two years now. We use bar codes as the data source, and plan to expand its use where applicable,” says Praza.It doesn’t make sense to bar code everything—for example, when an employee can key in a three- to four-digit employee number. But the combination of keyed-in information and bar-coded information provides a wealth of information to the system, which can then track plant-floor events. When employees log on, they can see their operations, work in process, set-up instructions, quantity to produce and the like. After processing, they can log back on and enter parts produced. Given the types of operations in this sheet metal fabricating facility, automatic data collection from the process just doesn’t seem justified.Part of the benefit Dexter has seen comes from integration with the enterprise resource planning (ERP) system. Praza sees the integration that results from having the manufacturing execution system (MES) and the ERP system from the same supplier as a big benefit. But the real benefit is the ability to capture data. “Some company’s Lean events have nothing to do with information,
but every time we have a Lean event, IT plays a part in making the change. We’ve gained significant profitability, as well as improved safety, because of these activities,” summarizes Praza.Suds to siliconFrom washing machines to microchip manufacturing, the software solution loosely named manufacturing execution systems (MES) provide the information backbone managers are using to cut costs, get products manufactured more quickly and eliminate waste. Imagine the design challenge of inspecting traces etched into microprocessor chips. The 5 feet by 4 feet by 5 feet inspection machines from KLA-Tencor Corp., inMilpitas , Calif. , weigh in at about 3,000 pounds. Even at that size, a granite base is required to maintain machine stability. The traces are so small that it’s even hard to use optical technology anymore.And the machines don’t last a long time, or as John Moore, quality program manager notes, “Moore ’s Law lives (referring to former Intel executive Gordon Moore, who famously predicted that the number of transistors on an integrated circuit would double every 18 months). Every three to four years, manufacturers design smaller chips, so we have to keep up and understand defects on chips with ever-smaller traces. We’re forever challenged to deliver faster, better tools and get them to market more quickly.”Machines undergo improvements over time and John Moore’s team at KLA-Tencor was frustrated by a lack of visibility into product genealogy of each machine “as built.” They looked into the company’s Oracle ERP system, the product data management system and the potential customer relationship management system. But bringing in an MES solution not only gave them track-and-trace capability, but it also can show them other things, such as process procedures to test, and the full configuration of the product through manufacturing. They went with Datasweep—now part of Rockwell Automation Inc., Milwaukee . “It had a lot of back-end database capability, but the user interface was a little lacking. It did have a rich set of tools that we could use to tailor the application to our needs. Later, Rockwell adopted several of our ideas into its product.”Moore ’s team rolled out a small pilot project in the summer of 2000 that went so well that they were asked to roll out for the entire company. By Christmas 2001, they had rolled the application out to five campuses. It took three months to get the application up and running, and to train people on how to use it. It started to show a return within four to five months.“About that time,” says Moore , “the chief executive officer needed to trim the budget and saw a line item for the MES project. It looked like an easy thing to cut. That’s one thing I learned from the project—to get top management buy-in. We just had support up to the vice president level. We asked for time to come up with a sound financial justification, and took a couple of months surveying users to figure out the return generated by the investment. We were actually pleasantly surprised to find out how good the return was. Good enough, in fact, to justify further investments. After taking time to digest a change to SAP from Oracle for the ERP system, we now have six new initiatives in MES.”Benefits of adding MES at KLA-Tencor included a cycled time reduction. Things don’t sit around waiting for decisions during manufacturing. Due to increased visibility of events on the plant floor, operations people are able to see and respond to delays quickly. There was a great reduction in the number of hours per week spent on production management, production control and engineering time spent on studying problems that once had been hard to measure. Now, there is a good baseline to measure the “before” state to evaluate against the “now” state. “This gave us confidence to go on with the project,” adds Moore . “We built a supplier scorecard by pulling information from parts of the MES system along with the customer relationship management and ERP systems. We’re able to assess suppliers quarterly—and this is really important because we have suppliers all over the world, making managing information crucial.”Going paperlessSoftware applications at this “middle level” between the plant floor and enterprise applications can be valuable in process industries as much as in discrete manufacturing. Even, or maybe especially so, in contract manufacturing. Lonza AG, in Visp , Switzerland , a biologics contract manufacturer, is a prime example of how applying an MES solution in a regulated industry can also save time and money.Leander Hertli, head of engineering and maintenance for exclusive synthesis at Lonza, conceived a project with the goal to make the plant paperless. In a regulated industry, there must be a trail of everything that happens in the process. Operators manually recorded and signed everything that they did. During periodic reviews of deviations from standard, it was discovered that about 80 percent of deviations were things such as the operator forgetting to sign the document or to record an event.Hertli researched a number of solutions to the problem and liked the integration he saw with Compliance Suite (MES) by DMI of Bradenton, Florida and Delta V (distributed control system) from Emerson Process Management of Austin, Texas.
The evaluation was completed by the end of 2005, and he decided to go with the system in early 2006. Unfortunately there were some delays in delivery of Compliance Suite and it wasn’t ready until mid-2006. Work need to be completed by the end of the year, and Hertli was able to do it despite the initial delay, along with the help of DMI.“With our manual system, we used to review about 100 pages. Now, with the electronic deviation report, there are two [pages]. We have to explain every deviation, and an investigation often takes two hours each. So all this is saved time for the reviewers,” says Hertli.If Lean is all about reducing waste, Six Sigma is all about reducing variability. Both of these strategies are gaining practitioners at a rapid rate—and both are voracious consumers of accurate, real-time manufacturing data. Master Black Belt in Six Sigma Dave Wilke is manufacturing systems manager at Rexam PLC, inChicago . Rexam is a manufacturer of beverage cans. Wilke got the job of implementing Six Sigma and quickly realized the need for manufacturing data to improve performance. He used a real-time shop floor reporting system from Accumence, a Chicago supplier of performance management solutions. He also tapped into the maintenance database housed in the company’s enterprise application from SAP AG, Walldorf , Germany , and systems from quality.“We had a pretty good feel for the quality of the information and wound up with more than enough data to force improvements,” says Wilke. “Data input into the system was pretty much automated, mostly from the programmable logic controllers, sensors, and in fact, all the infrastructure. We also studied where sensors were needed and what we needed to measure, and solicited input from the process engineers. Setting up the system took a lot of work from operations and IT (information technology) groups. We now can see and utilize data. Since the database is housed on corporate servers, everyone can see and utilize as needed. We have 15 can plants and all use the same type of systems. We can benchmark based on plant configurations and conditions and isolate which one performed. We look at the performance conditions and apply elsewhere.”Drooling over dataIn fact, Wilke says, this is all the data and analyses that a Black Belt drools over. “We work with the biggest issues now,” Wilke adds. But one of the biggest challenges in getting to this point involved disparate systems. Part of the work relies on data in the SAP system and in the quality system from Lighthouse, a supplier from the United Kingdom , in addition to the operations data from Accumence. The biggest problem Wilke’s team found in this situation was in naming conventions. “Standardized names would have helped,” he allows.Implementation teams were sent in to the first plant. They established databases, then pulled in “super users.” They were asked questions along the line of, “If I could have X, what would it be?” They went to live data, debugged, implemented the software and let the trial develop over a few months. People from the other plants came in for a look, and then they rolled out the application broadly. During the trial, for example, maintenance looked and recommended more documentation for unique pieces of equipment and tasks, and for consistent names so that they could look at all the plants; this would enable them to find the best practices in various plants and implement them generally.Wilke summarizes the benefits of the system beginning with, “We are far more aware of our issues than ever. As a result, we can stop the bleeding more quickly if something in the system says ‘Hey, look at this.’ We once thought if we entered data, the job was done. Now we’re moving to data analysis. We like the Accumence system, not just for real-time information, but also for trends and data mining.”Rexam is not the only beverage can manufacturer seeking to optimize production with modern software tools and manufacturing strategies. Amcor, the third largest packaging company in the world, is headquartered in Melbourne , Australia , and has operations in 34 countries. The potential constraint in its production system is the decorator machine, given its rated speed relative to the rest of the line. This machine must be kept running at its rated speed for as many hours as possible. But the manufacturing line is closely coupled, so the decorator’s availability is affected not only by itself, but also by upstream and downstream equipment.In a process not uncommon in manufacturing, data capture was done manually on log sheets, which were eventually transposed into a computer spreadsheet. Because of this, there were many deficiencies in the data. All downtime was in multiples of five minutes, rather than the exact amount. Downtime was recorded only for the decorator equipment—none on any of the other machines that could affect the process. Downtime associated with speed loss was not captured. The ability to look back at historical information was limited. A better understanding of the manufacturing process was required, and better information was the way it was going to happen.The company had been using human-machine interface and supervisory control and data acquisition software from Citect, an Australian software supplier. Citect had an MES application and Amcor personnel checked it out. They conducted a three-day study of how the plant operated, what downtime and spoilage data they were getting and how this data was being captured. They then decided to implement a pilot project using the Citect Ampla MES solution in the company’s Sydney plant. Take a teamA team composed of Amcor’s operations manager, engineering manager and production manager, along with two to three Citect engineers, managed the project. The team decided where to capture downtime information and how to capture it. It decided on the appropriate metrics to display on the plant dashboard. The two- to three-month process included conversations with IT to assure compatibility with other IT systems in the plant.The system was implemented and the information was incorporated into regular morning meetings and weekly planning meetings. The team rapidly discovered it had been too ambitious with categorization. So, the number of categories was reduced. Team members also realized that the real value of the system lies not in the information, but in turning the information into action. Amcor has derived many benefits from this implementation of an MES system. It has developed more appropriate strategies based on true downtime and spoilage information. Hidden downtime has been uncovered, along with hidden spoilage areas. Managers can now compare current with historical data to discern when problems developed. Operating Equipment Effectiveness (OEE) has improved by 8 percent, and spoilage has been reduced by 1.2 percent over the past two years.Grupo Leche Pascual is a Spanish foods manufacturer whose dairy processes were the first in Europe to achieve U.S. Food and Drug Administration certification. That progressive outlook led it in 2005 to upgrade its custom MES to a modern version—this one the SimaticIT from Siemens, the German automation products supplier. One of the drivers for the project was customer service. When a customer called in requesting information about his or her batch, customer service personnel had to search through records, sometimes taking more than a day to find the appropriate information. With an MES system in place, a simple computer search returns the needed information in less than a minute.The overall system implementation allowed batch processes to be rapidly revised, and provided standardized efficiency data for the production and quality departments. By providing a foundation for the company’s continuous improvement processes, the system allowed employees to optimize manufacturing processes. The real-time integration of radio frequency identification information into the system, along with a historian, gave them track-and-trace capability with a complete genealogy.After looking at these different applications, it’s hard to describe MES in a simple sentence because it is a product category that encompasses so many things. Fred Woolfrey, productivity solutions consultant for Yokogawa Corp. of America , in Sugar Land , Texas , agrees. “Lots of problems that are solved kind of fall into MES,” he says. “It’s not a controller or flow control valve, but sometimes an asset management tool relating to maintenance. And for sure, things like laboratory systems, historians, plant scheduling and providing information to the corporation’s ERP system.”Woolfrey points to two examples where this layer of software has yielded big dividends for users. The first involves the problem of alarm management. “In the days of hard-wired control, it was expensive to add an alarm. But with modern distributed control systems and automated supervisory systems, adding an alarm was easy. But this led to alarm flooding. There are so many that operators can’t figure out easily which are the most important,” Woolfrey explains. “One plant had problems it couldn’t catch and had plant upsets (lost production) every four to eight weeks. After adding alarm filtering, that doesn’t happen.” Woolfrey also points to another plant in the pharma industry that used analysis of its plant historian to go back and see why it suddenly had increased yield. It turned out that for some reason, someone expanded the heating time on a batch, he says. The plant literally doubled plant capacity once the new procedures were put in place. “A chemical plant had an intermittent problem on a distillation column for years,” Woolfrey adds. “After analysis of data from the new historian, engineers found the problem and fixed it in days.”There are important conclusions to draw from all these examples of companies improving operations and increasing manufacturing throughput using new software tools. In every case, it took a team of people from many disciplines within the plant. Further, the use of the software tools was not the end in itself, but rather an enabler for people to solve the problems. As Peter Martin, vice president of strategic ventures at Invensys Process Systems, in Foxboro , Mass. , summarizes, “Let technology do the repetitive things and put people where they can make decisions. Artificial intelligence was never able to capture that ability of human decision-making. You have human assets, information assets and equipment assets. A good business process allows managers to use them all.”For more information, search keywords “manufacturing execution system” at www.automationworld.com.
“Have you seen the price of stainless steel? It’s been skyrocketing.” Add to that the need to enhance product features while meeting competitive price pressures, and initiatives to reduce manufacturing cost rather quickly get pushed into high visibility.Dexter’s roots go back more than 100 years, and for a time, the company was part of Ford Motor Co. It’s now an employee stock ownership program (ESOP) company, a fact to which Praza points with pride. The manufacturing strategy Dexter is using to cut waste and improve profitability is Lean Manufacturing. To drive the Lean initiative and provide the kind of information it needs to do its job, Praza has led an effort to implement a shop-floor reporting system. In fact, Praza has been building shop-floor reporting systems since the 1970s, when he made a switch from engineering to systems. For the Dexter project, he uses software from Alpharetta, Ga.-based Infor Global Solutions.
“We’ve had the Infor XA MES MDCC Suite up and running for over two years now. We use bar codes as the data source, and plan to expand its use where applicable,” says Praza.It doesn’t make sense to bar code everything—for example, when an employee can key in a three- to four-digit employee number. But the combination of keyed-in information and bar-coded information provides a wealth of information to the system, which can then track plant-floor events. When employees log on, they can see their operations, work in process, set-up instructions, quantity to produce and the like. After processing, they can log back on and enter parts produced. Given the types of operations in this sheet metal fabricating facility, automatic data collection from the process just doesn’t seem justified.Part of the benefit Dexter has seen comes from integration with the enterprise resource planning (ERP) system. Praza sees the integration that results from having the manufacturing execution system (MES) and the ERP system from the same supplier as a big benefit. But the real benefit is the ability to capture data. “Some company’s Lean events have nothing to do with information,
but every time we have a Lean event, IT plays a part in making the change. We’ve gained significant profitability, as well as improved safety, because of these activities,” summarizes Praza.Suds to siliconFrom washing machines to microchip manufacturing, the software solution loosely named manufacturing execution systems (MES) provide the information backbone managers are using to cut costs, get products manufactured more quickly and eliminate waste. Imagine the design challenge of inspecting traces etched into microprocessor chips. The 5 feet by 4 feet by 5 feet inspection machines from KLA-Tencor Corp., in
The evaluation was completed by the end of 2005, and he decided to go with the system in early 2006. Unfortunately there were some delays in delivery of Compliance Suite and it wasn’t ready until mid-2006. Work need to be completed by the end of the year, and Hertli was able to do it despite the initial delay, along with the help of DMI.“With our manual system, we used to review about 100 pages. Now, with the electronic deviation report, there are two [pages]. We have to explain every deviation, and an investigation often takes two hours each. So all this is saved time for the reviewers,” says Hertli.If Lean is all about reducing waste, Six Sigma is all about reducing variability. Both of these strategies are gaining practitioners at a rapid rate—and both are voracious consumers of accurate, real-time manufacturing data. Master Black Belt in Six Sigma Dave Wilke is manufacturing systems manager at Rexam PLC, in
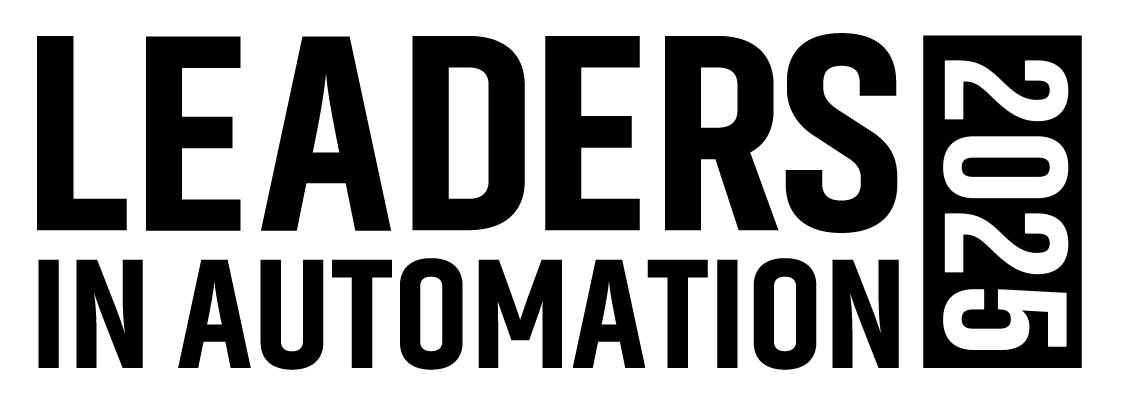
Leaders relevant to this article: