David Watts was between projects when he got the phone call. It came from a contractor that Watts —a Krum, Texas-based systems integrator and consultant—had used in previous automation projects. “This particular individual has lots of contacts, and knew that I was a programmer, and he called and said, ‘Hey, there’s an opportunity for a job in Iraq . Are you interested?’ “At first, I said no,” Watts relates, to the prospect of taking on a job in an overseas war zone. But when Watts later called the contractor back, out of curiosity, to find out the details of the assignment, “it sounded like a pretty good opportunity,” he says, and the idea began to grow on him. FluorAMEC LLC—a company formed between Fluor Corp., Irving , Texas , and London-based AMEC plc to provide services in Iraq —was in need of a programmable logic controller (PLC) programmer for a major water plant project. The PLCs had already been delivered to the Nasiriyah Water Treatment Plant project, in southern Iraq , and the contractor could find no one in the area with significant PLC programming experience.Part of historyWatts discussed the opportunity with his wife and three children. “They were scared for me to go,” he says. But they also agreed that the opportunity to be part of history by helping to build community infrastructure in Iraq would be a positive experience. So Watts decided to take the job.Before packing his bags, Watts reviewed thousands of pages of documents on the project provided by the contractor, and was able to do a small amount of programming work domestically. In mid-October last year, he set out for the job site just north of Nasiriyah City , in southern Iraq . The Nasiriyah Water Treatment plant will replace a much smaller plant in the southern Iraq region, and is designed to supply about 10,000 cubic meters per hour of fresh drinking water to about 3 million Iraqis. The design calls for four Allen-Bradley ControlLogix PLCs, supplied by Milwaukee-based Rockwell Automation Inc. Three of those PLCs are located in pump stations along the Garaaf River , a small branch of the Tigris River . The fourth ControlLogix resides in the control room, functioning as a Supervisory Control and Data Acquisition (SCADA) host for the plant. A fifth PLC, a Modicon Quantum from France-based Schneider Electric, has 20 input/output (I/O) drops, and will be used to control the backwash of 20 individual filter cells. When Watts arrived in October, work had been underway on the plant for some time, so he was surprised to find the project was not further along than it was. “I was really not expecting to go in there and have to do as much as I did from scratch,” he notes. Programming for the four Allen-Bradley PLCs was only about 10 percent complete when he arrived, Watts says, though the Modicon Quantum programming was about 80 percent finished. Machine gun securitySecurity at the Nasiriyah job site was tight. “We had guys with machine guns around us all the time,” Watts says, including a private security detail supplied by a UK company, along with Iraqi troops assigned to protect the workers. “You would hear machine gun fire every day and every night, but nothing was really directed at me or at our camp per se, at least that I’m aware of,” says Watts . Neither did the camp come under direct mortar attack, he says, “though we did have a rocket that was launched over the water plant.” Fortunately, the rocket was a dud, and stuck in the mud near the plant intake, about 200 yards from where he was working, Watts relates.The most hazardous part of the job came when Watts needed to visit the three pump stations, which required a drive of some 65 miles over what Watts calls “a long stretch of dangerous road. When we went outside the camp, we had to wear body armor and traveled in bullet-proof Suburbans.” But again, Watts says he was fortunate, encountering no improvised explosive devices, rocket-propelled grenades or other attacks during the nearly eight weeks that he was in Iraq . Beyond safety issues, Watts says the biggest hurdles he faced on the project involved gathering all the information and documents needed, along with occasional problems due to sporadic electrical power in the region. One information shortfall became apparent when the time came to provide communication between the ControlLogix PLCs and the Quantum. What's this?“We had a ProSoft Technology interface card that was sitting in a rack and had never been configured. We had no cables for it, no manuals, and no one really knew what it was for,” says Watts . “But of course, when I got there, and they told me they needed to get the filter information [from the Quantum PLC] to the SCADA system, I knew that’s what the ProSoft card was for,” he says of the module, provided by ProSoft Technology Inc., based in Bakersfield, Calif.Watts , who had never used a ProSoft interface card, says he downloaded some manuals, made some cables and tried a variety of things, before he was able to get Scott Lee, a ProSoft Technical Support person, on the phone. Lee provided the needed support in a fashion that draws praise from Watts . “He was one of the best tech support guys I’ve probably ever talked to in 25 years of doing this type of work,” says Watts . “He would have stayed on the phone all day with me if I needed him. He had no agenda other than to make sure that I was happy with what I was using, and completely understood it.”Lee recalls the conversation. “You could tell right away that he (Watts ) had his hands full. But he obviously knew how to program and only needed a little nudge in the right direction to get the ProSoft Modbus Interface module up and running,” Lee relates. Indeed, with Lee’s guidance, Watts was able to interface the PLCs relatively quickly, while looking like a hero. “The fact that I got the ProSoft card going in about four hours was absolutely amazing to all the guys in the water plant, because none of them had it working,” say Watts. In fact, it was that newfound knowledge that helped earn Watts a return trip to Iraq earlier this year.Watts finished up the job at the Nasiriyah plant by mid-December last year, going home to Texas for the holidays. But in February, he returned to Iraq for work at another FluorAMEC water plant project site near Erbil, in northern Iraq . That plant has a controls architecture similar to that of the Nasiriyah plant, and workers in Erbil were also unable to get their ProSoft card working. Watts solved the problem, modifying the Erbil plant’s filter program and rewriting a configuration file for the ProSoft card. He also modified the Erbil plant’s SCADA system to accommodate some additional desired features that were not initially specified. “Of course, while I was there, I spoke with the guys in Nasiriyah and offered them some suggestions” for similar upgrades at that plant, says Watts .The Erbil job required only about a two-week stay in Iraq . Back in Texas , Watts says he is in continuing touch with Iraqis at the Nasiriyah plant, which should be online and fully operational by the end of May. And, schedule permitting, Watts says he would be willing to go back for additional project work in Iraq . Calculated riskDoes he feel he would be putting his life at risk by spending additional time in the war-torn country? “Oh sure,” Watts responds. “But I also feel that way when I’m out here driving on Interstate 35. I’m certainly not looking to put myself in harm’s way,” he adds. “But you know, when it’s your time, it’s your time. It’s a calculated risk, I guess.”For more information, search keywords “PLC programming” at www.automationworld.com.
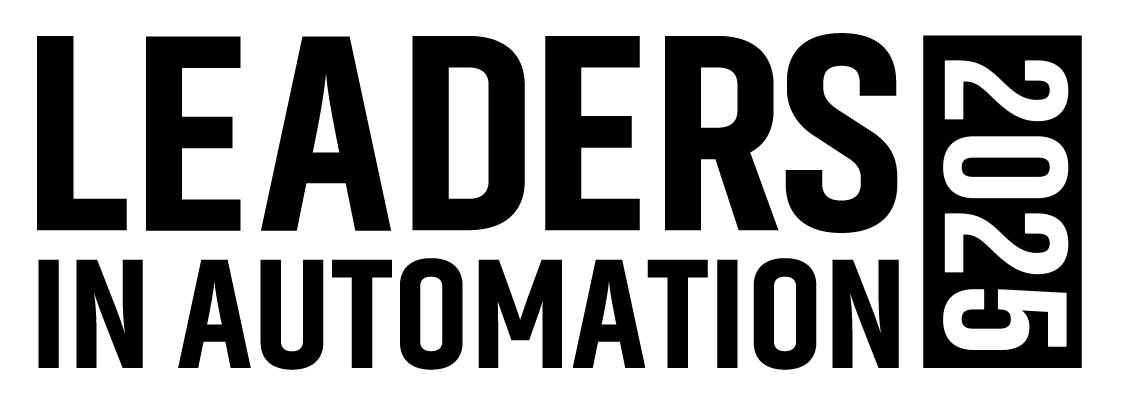
Leaders relevant to this article: