Changing the habits of people in both their personal and professional lives from energy wasters to energy conservers can generate exhortations to both idealism and to finance. Becoming more energy efficient makes sense, both for reducing emissions and for improving a company’s net profit. But changing habits is one of the hardest things for humans to do. Financial incentives often are powerful motivators toward rational behavior.Leaving politics aside and just looking at the science, the February 2007 report of the Intergovernmental Panel on Climate Change Working Group I titled “Climate Change 2007: The Physical Science Basis,” describes progress in understanding of the human and natural drivers of climate change, observed climate change, climate processes and attribution, and estimates of projected future climate change. It builds upon past IPCC assessments and incorporates new findings from the past six years of research.According to the report,“Changes in the atmospheric abundance of greenhouse gases and aerosols, in solar radiation and in land surface properties alter the energy balance of the climate system. These changes are expressed in terms of radiative forcing, which is used to compare how a range of human and natural factors drive warming or cooling influences on global climate. Global atmospheric concentrations of carbon dioxide, methane and nitrous oxide have increased markedly as a result of human activities since 1750 and now far exceed pre-industrial values determined from ice cores spanning many thousands of years. The global increases in carbon dioxide concentration are due primarily to fossil fuel use and land-use change, while those of methane and nitrous oxide are primarily due to agriculture. The understanding of anthropogenic warming and cooling influences on climate has improved since the Third Assessment Report (TAR), leading to very high confidence that the globally averaged net effect of human activities since 1750 has been one of warming.”Of course, what this means for the planet a hundred years out is anyone’s guess, but many people feel that humans should take steps to reduce these gases in the atmosphere. One way to achieve a beneficial social goal is to give people and companies financial incentive to do something. One idea floating around is a “carbon market,” by which companies that can save energy (and therefore carbon emissions) can trade extra credits to those companies that lack current technology for doing so. The overall effect, so it is argued, would be beneficial to both companies and the environment.Dinesh Paliwal, chairman and chief executive officer of automation supplier ABB Inc., Norwalk, Conn., and group executive vice president of the Zurich-based ABB Group Ltd., offers these observations for tying social good to financial interests. “This Business and Climate Change Conference was a bipartisan effort to find common ground on how Congress might create a mandatory market-based greenhouse gas regulatory system to address the potential effects of climate change. For most companies and organizations, the answers to cutting emissions—and cutting energy costs—in this era of rising oil and gas prices are readily available. By applying certain cost-effective power and automation solutions, industry can achieve substantial energy savings today without waiting for the alternative fuels of the future. The benefit of smart energy usage is simple: Put every single kilowatt to work more efficiently and more productively—savings millions of tons of coal and petroleum products that are now being consumed to supply energy that is not truly needed.” A report from Boston analyst firm Industry Directions found that managers at production and engineering companies believe that they must act to offset the impact of high and volatile energy costs on their company’s margins. The company’s second annual study on the impact of energy costs on supply chain strategy, “The Energy Cost Factor: Transforming the Supply Chain to Offset Margin Squeeze,” found that the number of respondents who expect high energy prices to hurt their margins was four times higher in 2006 than in 2005.“This year’s findings are significant because they demonstrate that companies are not simply bearing the brunt of high energy costs in the most obvious areas of the supply chain,” says William Brandel, Principal at Industry Directions. “Further, they now recognize that they cannot pass these higher costs on to customers or demand lower costs from suppliers.”And indeed there are many ways to reduce the cost of running electric motors in manufacturing, from changing the motors themselves to how they are driven and to how they are connected to loads. Another way is to implement overall facility energy control, and even Lean thinking principles can be applied to the problem.John Malinowski, product manager for AC and DC motors at supplier Baldor Electric Co., in Ft. Smith, Ark., says, “Motors in industry consume about 67 percent of a plant’s electricity. Anything that makes them more efficient puts money directly to the bottom line. By 2002, companies who had used best practices were saving up to 50 percent of their electrical cost due to things like right-sizing motors, adding variable frequency drives, using premium efficient motors and improving mechanical linkages.”Managers can get started down the efficiency path by conducting a facility survey, says Malinowski. “The first step is basic. Take a look at your motors, noting each one’s rating, horsepower, speed and estimated hours of use per day. By making this information known, you don’t leave the decision about which motor to replace on failure to a third-shift repair guy,” he observes. “Decisions about which motor to use and whether to rewind or use a Premium Efficient should be made with forethought. In fact, most people evaluate a motor purchase decision on only the purchase price, when in fact, that cost is only 2 percent of the total cost incurred over a motor’s lifetime,” says Malinowski. “So when someone buys the cheapest motor up front thinking he’s saving the company money, often he’s shooting himself in the foot when you consider the total cost to the company.”The second level survey entails taking an ammeter out to each motor and determining if the motor is correctly loaded. “There’s a sweet spot at about 80 percent to 100 percent load,” says Malinowski. “Also consider the type of load. If it is a variable torque load, it may be a prospect for a variable frequency drive. With a centrifugal load, the horsepower of the motor changes by the cube of speed change. If you are using a valve to reduce flow while running the motor at rated speed, you can save significant money by adding a drive and running the motor at lower speeds.”At level three, you really get the engineer hat out. Malinowski states that at this level, you look at the entire system—especially everything attached to the motor. For example, using the correct type of gear box can significantly improve energy efficiency. “Simple things like new V-belts with notches that bend easier can save 3 percent. Or maybe a machine came in with single-phase motors that would be more efficient with three-phase. Or maybe you should change to motors with permanent magnet rotors with higher efficiency ratings. One final piece of advice is to correlate energy savings with reliability. Make sure the motor is correct for the application,” Malinowski concludes.Bruce Benkhart, director of commercial and industrial programs at Applied Proactive Technology, a Springfield, Mass., system integrator, concurs with the assessment that companies should perform a thorough analysis of their motors. He points to the Motor Master spreadsheet provided by the Consortium for Energy Efficiency’s Motor Decisions Matter (MDM) initiative. “While the MDM model is to go in quickly with a Microsoft Excel spreadsheet format and do some analysis, we now just go in and do a complete audit of all EPA-class (for Energy Policy Act) motors,” Benkhart says. “But the most important thing is to effect changes in behavior of all those involved in motor buying and application decisions,” Benkhart continues. “In this respect, all of the government rebates have gone a long way toward achieving this change. The next thing that is important is to codify the new way of buying and using motors. In this way, the changes will outlive the original champion. The next thing to do is to thoroughly train everyone involved.”Some of the applications of motors in manufacturing are not directly related to processes or machines. Jack Creamer, segment manager for pumps at automation vendor Schneider Electric, in Raleigh, N.C., says that implementing variable frequency drives in pumping applications, particularly in buildings, can often justify a payback in less than 18 months. Schneider HVAC Segment Manager, Hua Zhang, adds, “Drives in HVAC (heating, ventilation, air conditioning) applications can save 30 percent.” More important than just adding drives to motor applications, according to Creamer, is that engineers marry the electronics available in drives to overall building controls. “I’ve seen people buy drives, then just operate on set point control, that is, either it’s on or off. Better system engineering involves using the power of speed regulation to optimize all the drives throughout a facility.”Leon Kythas, Schneider product manager for packaged drives, adds a cautionary engineering note to those about to go out and just slap on a bunch of drives to existing motors. “Installing drives in older facilities where motors may have long power leads, or where the motors are designed only for full speed operation, can lead to potential problems such as nuisance tripping or premature motor failure,” he warns. “Engineers need to balance the motor/drive combination and check out the duty cycles, among other factors.”One item that’s easy to overlook in the motor system is the connection of the motor to the load. This is an area ripe for providing energy savings, some experts say. That mysterious black box containing the gear reducers can be a huge energy sieve. Dave Ballard, corporate manager of engineering and marketing at gearmotors and drives vendor SEW-Eurodrive, in Lyman, S.C., acknowledges the potential energy savings with drives, but he also encourages users to look at the entire system. “When the application includes a lot of cycling, starting/stopping or indexing, the energy savings can evaporate due to initial starting current. So look at the entire drive train. Is the entire system stable? Look at the gear boxes. Sometimes you can achieve 25 points of savings with just a newer gear box.”Motors are a major energy user, so it makes sense to very thoroughly analyze all of them. But if the entire facility is ignored, then another chance for big cuts in the energy bill has been lost. Barry Contral, business unit manager for the Access Product Group at automation vendor Siemens Energy & Automation Inc., in Norcross, Ga., says, “Industrials have beat to death other costs, but the power bill is a big unknown. There are costs from the utility, such as a bad power factor charge or peak demand charges, that can be big. Unless you monitor it, you may never know that you should take action to solve those problems—or that perhaps the utility is overcharging you due to faulty measurements on their part,” Contral advises. “With a good power monitoring solution, managers can analyze parts of a plant and determine which processes or parts of the facility are the biggest users. Then they know where to look for the initial big savings.”One last component that can be analyzed for energy savings is hidden in electrical enclosures all over the plant—constant voltage transformers (CVTs). One company that makes a capacitor-based filtering product, SoftSwitching Technologies, in Madison, Wis., has surveyed many companies, and its figures show that the typical CVT is about 50 percent loaded most of the time. Using industry numbers for transformer efficiency at that load, the company predicts almost $2 million per year savings using its product for a “typical” plant that has 2,000 CVTs rated at 6 kVA. For more information, search keywords “motors” and “energy efficiency” at www.automationworld.com
To see the accompanying sidebar to this story - “Cross-belt Energy Savings” - please visit www.automationworld.com/view-3009
To see the accompanying sidebar to this story - “Cross-belt Energy Savings” - please visit www.automationworld.com/view-3009
Sponsored Recommendations
Sponsored Recommendations
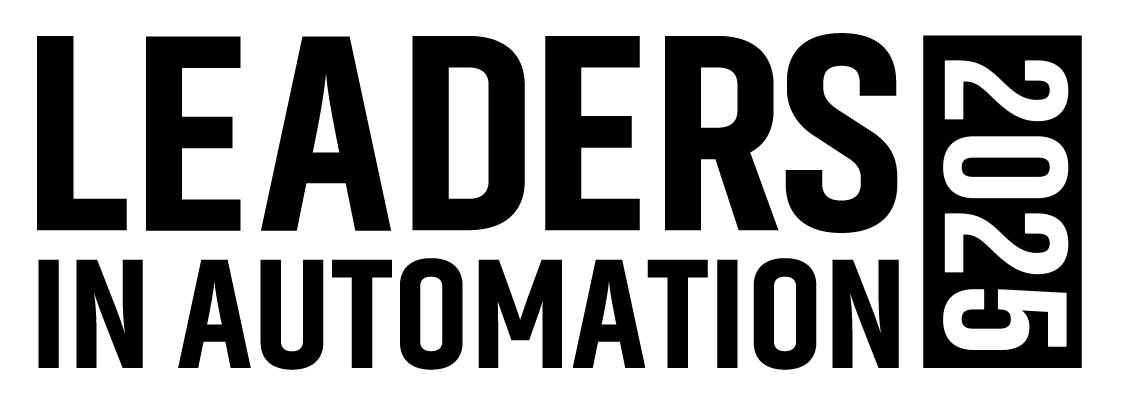
Leaders relevant to this article: