Generally speaking, Lean Manufacturing is pegged to mass production. Toyota itself, proud parent of the Toyota Production System, says it will manufacture more than 9.2 million vehicles in 2007, and that is a pretty hefty mass. Almost anywhere you turn for a company-specific picture of Lean principles in books and articles, you will more than likely find the principles applied to mass-produced goods. Little wonder then that Lean tends to be more or less automatically linked to production that involves hundreds of thousands, millions, even hundreds of millions of units. But a few companies, among them Pearson Packaging Systems, Spokane, Wash., have had good success applying lean manufacturing principles to one-off, custom products. The company’s experience offers a side to Lean that rarely gets mention—the need to pull the camera back, way back, to see underlying, basic structures.Pearson joined the Lean revolution more than three years ago, and the results are impressive. “Final assembly is down to 70 hours from 180,” says Michael A. Senske, president and chief executive officer. “Delivery lead time is down to 35 days from 70. Best of all, since we’re in a price-sensitive segment, we’ve been able to pass substantial cost reductions along to our customers.” Senske says the company’s 80 percent increase in sales over the last year is in part related to those cost reductions.Pearson makes custom packaging equipment, include case erectors, case sealers, tray formers and robotic palletizing systems. While many standard subassemblies and components are used in a variety of machines, no single machine is exactly like any other.The more dramatic improvements ascribed to Lean usually involve rooting out habitual (if wasteful) work patterns. Patterns are seen most easily in large arrays of data. They generally emerge from masses of production information, or at least enough data to determine the impact of certain repetitive work activities on costs. But when almost nothing is habitual, very little is 100 percent repetitive, and production levels are (by mass-production standards) minuscule, how do you proceed?Lean permeation“We are well aware that we’re in a low-volume, high-variability business,” Senske says. “We either build to very specific customer specifications or modify existing designs to handle new types of packaging. We build-to-order or engineer-to-order, as opposed to build-to-forecast, the way a high-volume, low-variability manufacturer would.”Pearson’s impetus toward Lean—or better, its tendency toward Lean thinking—began as fallout of building a highly customer-oriented executive staff over many years. “Our equipment goes to major players in pharmaceutical, food and beverage, consumer durables and key chemical suppliers,” Senske explains. “For many years, we’ve recruited key staff with specific experience in those industry segments.”The main driver for this was to build Pearson’s intellectual capital around specialized industry needs, allowing the company to talk the language of its customers and to understand first-hand the roles and requirements of packaging for each customer’s operations. Lean thinking came with the management who brought this industry knowledge. “Because nearly everyone came from operations that depended on Lean Manufacturing, either to maximize throughput or minimize costs, Lean more or less became an undercurrent here,” Senske says.This undercurrent never really reached the surface until an eager intern brought Lean systems into play a few years ago—and even then, the processes almost failed to move beyond a single experiment. “The intern worked with people on the floor around the assembly of new type of case erector,” Senske says. “Together, they developed assembly processes that literally took hundreds of hours out of assembly. Unfortunately, the new methods fixed one set of things but threatened to break some upstream activities. Manufacturing took a look at that situation and backed away. Later on, we reached back into this experience to develop what has turned out to be a rule with a huge payoff—we don’t stop any Kaizen event focused on an improvement simply because other operations might be affected.” (Kaizen, a Japanese term that translates to “continuous improvement,” is a core methodology of Lean Manufacturing.) Outside influenceAround the same time as the intern’s efforts, Pearson personnel were informally gathering best practices from Buck Knives, just over the border in Post Falls, Idaho. Pearson and Buck came to know each other through local Chamber of Commerce and regional Workforce Development Councils. Buck’s Lean practices—and their benefits—brought yet another level of influence on Pearson. “In the end, everything kept pointing to what we might gain through Lean and what we were losing [by not doing it]. We decided to move forward with a formal program to bring Lean Manufacturing to our operations,” Senske says. Initial preparation for Lean followed a conventional path. Pearson took stock of its current state of business and operational practices, then invested in value-stream mapping as a means of identifying both high-value activities and the more obvious wasteful practices. “The biggest learning from this was that, despite customization and one-off production, our machine design and build processes were similar, project to project,” says Senske.By revealing the patterns of design and assembly at work in the company, this preparatory activity did more than anything else to enable Pearson management to make the connection to Lean. Company teams created standard operating procedures that defined the steps of machine development and manufacture, a process that helped Pearson institute consistent processes through the whole organization. Now relatively mature, Pearson’s Lean initiative has become formalized, both organizationally and procedurally. Pearson created a new department, a Kaizen promotion office. Full-time resources assigned to it gather candidates for improvement projects—Kaizen events—from anyone in the company who spots an area for improvement, then prioritizes them.As a given event begins, the Kaizen office develops a team for the event and acts as a moderator as the event unfolds. Every team includes members from assembly, customer service, marketing and sales, plus any other functional area affected by a given project. “The direct input from sales and marketing, and customer service provides a touchstone for a key attribute of any project,” Senske explains, “which is to ensure that whenever possible, any improvement should have direct applicability to customer needs.”One-week limitKaizen events begin on Monday and close by Friday. The one-week duration focuses maximum energy on improvement projects, deftly keeping them from sinking into death-by-committee. Second, knowing that only a week is available helps the Kaizen office and the teams focus the problem as tightly as possible.For any given event, on Monday, the team gathers and is presented with the challenge. It then reviews Lean principles; a significant portion of the Kaizen promotion office’s responsibilities lies in ensuring company-wide familiarity with the principles, processes and benefits of Lean thinking. On Tuesday, the team reviews the current state, usually with hands-on visits to the functional area involved, and performs value-stream mapping specific to the problem.On Wednesday, the team creates the future stream. The process involves taking the waste out of the target activity, then hashing out how to remove non-value-added steps—and more importantly, how to replace them with value-added activity. Thursday and Friday mornings are devoted to implementing the changes, capped on Friday afternoon with a report to management on what has been accomplished and what measurable changes the company can expect.“If something comes up, or the problem reveals itself as too broad, that usually happens by the end of the second day,” Senske says. “If that happens, we just narrow it down and take on the new, more specific problem.” Even with two Kaizen events per month, the need to start-stop-refocus has happened only two or three times over the last three years, a testament to the company’s skill in defining and pursuing areas for improvement.There are only a few rules. First, projects cannot compromise safety for employees or customers. Second, compliance with all regulatory specifications must be maintained, including both those of the Occupational Safety and Health Administration (OSHA) and local building codes. Third—a rule designed to prevent a second instance of Kaizen stoppage like that of the early, intern-driven project—improvements are pursued even if they might stress or break other processes around them. “Our object is to do something better,” Senske says. “If something breaks as the result of an improvement, we’ll deal with it. The Kaizen event can then stay focused on the original, identified improvement.”Free reinThere are no other constraints. Teams have cut holes in walls and even taken a 30-by-70 foot wall completely down (a non-load-bearing wall, to be sure). They have moved equipment. They have completely reoriented work stations and cells. “The teams are empowered to change anything, if it will help,” Senske says.Once a project has reached its Friday afternoon target time, it goes on a 30-day list. A month later, the project comes under review to ensure that any follow-on needs are met and to evaluate the project’s success. Finding new Kaizen targets has been aided by a program that Pearson maintains with its customers—30 to 50 at any given time—to review Pearson equipment performance and to solicit input on costs, options, functionality, machine footprint and product range. “It took a year or more to get the customer program fully rolling,” Senske says. “At first, customers were understandably skeptical, fearing that we’d take their time and then not listen to them. A few positive projects helped turn that around, and now customers line up to help us. At the end of the day, it has proved invaluable in making sure that customers drive product development.”Pearson has adopted one-piece flow (the concept of moving one workpiece at a time between operations within a workcell) to its operations—an approach that seems especially fitting for a custom product environment. The company ended a practice of making components in batches, then inventorying them until needed. It took capital equipment away from functional centers, instead placing cutting, welding, turning and milling resources along specific lines. This allows operators to make parts for immediate incorporation into assemblies.Capping Pearson’s approach to Lean is an infrastructure of rewards for participation. Supervisors can give any employee an instant cash award in recognition of improvement efforts. An advocate-of-the-month program singles out key contributors, and from those, one advocate of the year receives not only recognition but a substantial bonus. Performance reviews focus on improvement efforts and merit increases go to those who make continuous improvement a priority. Finally, nobody is let go as as the result of a Kaizen event. If a given improvement eliminates a job, that resource is reallocated to other areas—including the Kaizen office.“The real key,” Senske says, “is to realize that you never are done—you never reach a point where you can say, ‘We’ve now implemented Lean.’ You can’t plateau because you think you’ve reached perfection. There’s too much change going on for that to happen.” For more information, search keywords “Lean Manufacturing” at www.automationworld.com.
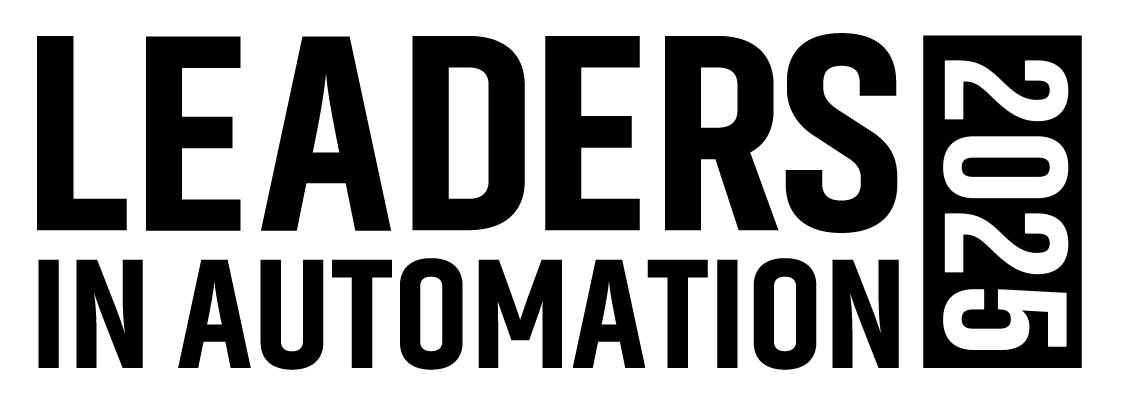
Leaders relevant to this article: