If you make packaging machines, one of your big concerns in recent years is making sure that your machines can talk to the rest of the manufacturing line. You also have to be certain that your machines are flexible enough for fast almost instant changeovers from one type of packaging to another. Your customers—especially the mid-size manufacturers demand equipment that can be changed using a touchscreen and very few manual movements.Adco Manufacturing Inc., a packaging machine producer in Sanger, Calif., has worked to meet its manufacturing customers’ needs for increased integration and flexibility. “What we have done for integration is to align ourselves with the PackML Group,” says Kevin Gilpin, electrical engineering manager at Adco. “We’re using the PackML data structure to connect to the rest of the line.” PackML is the packaging machine language guidelines developed by the Packaging Workgroup that is part of the Open Modular Architecture Control Users Group (OMAC).One big machineAdco has worked with Rockwell Automation Inc., the big Milwaukee-based automation controls
vendor, to develop a common platform between the packaging machinery and the automation system. The integration keeps the entire manufacturing line including the packaging machinery visible from the control platform. “The integration allows the operators to control the entire line,” says Gilpin. “So if the packaging machinery goes down, the whole line goes down. It’s like one big machine.”Not all integration requires the complexity of PackML. In many cases, manufacturers use rudimentary Ethernet connections to send a few specific signals back and forth between the packaging machines and the manufacturing line. “If the customer specifies it, we can hardwire half a dozen devices to send discrete signals using Ethernet,” says Gilpin. He notes that Ethernet has become trendy because of its low cost. “It’s not quite real-time, but it’s very, very close—and it’s cheap, which helps a great deal.”Control technology also comes into play in making packaging machinery more flexible. “A lot of our customers want to get a variety of packaging out of one machine. We’re using Rockwell technology to make it easier for changeovers,” says Gilpin. “Now it can be done modularly. You change a few parts and make a couple of different adjustments on the screen. There are some manual things you do, but there are fewer of them now.”The improved flexibility is a response to customer demand for greater changeover speed. Quick changeover is a competitive factor and a demand that comes from the manufacturers’ customers who want more and more differentiation in packaging. Large retailers, for instance, are now demanding their own individual packaging for many of their consumer goods. In addition to controls integration, robotics is also playing a role in making packaging equipment more flexible. Some robotic-equipped machinery is now so flexible that changeovers can be completed entirely through a touchscreen, with few or no manual changes required.Flexibility key The need for manufacturers to change packaging on-the-run comes frequently through pressure from retail customers. “Wal-Mart will want its package of batteries to look different than Lowe’s or Home Depot’s,” says Carl Traynor, senior general manager, distribution and handling, Motoman Inc., a robot manufacturer in West Carrollton, Ohio. “You used to be able to do one package for all of them. Now you have to do different packages.”Another factor driving the need for flexibility is the sheer number of products produced by manufacturers. “We’re seeing rapid changes in the packaging for food and pharmaceuticals, and we’re seeing a greater number of SKUs (stock keeping units) they need to produce,” says Travis Holley, consultant for packaging at Siemens Energy and Automation Inc., the Alpharetta, Ga.-based automation vendor.
“That means changes to the machines need to be rapid. That leads to the modular design of the machines, and we need to have the controls to support the flexibility.”Some of the flexibility is achieved through use of servo-mechanisms, or servo for short. A servo is typically a motor that includes a velocity and/or position feedback device that can be adjusted. Servo drives can also be programmed to be self-regulating. Servo drives used in conjunction with PackML can help operators make quick changes to packaging machinery to produce different types of packaging.“You can increase the flexibility of machines to produce faster changeovers—and you can reduce the number of spare parts—by using servo motion and the variable structure of PackML,” says Mike Lamping, a technology leader for consumer products giant Procter & Gamble Co., and the chair of OMAC’s PackML Group. “There are over 100 different variables and an extensible array with PackML. That allows machines to talk to each other.” That communication allows the control system to tell the packaging equipment to change in order to shift packaging to match the output of the production line.Some of the new flexibility in packaging machinery comes through developments in embedded control devices and servo drives. “We have a product that has a controller embedded, and we add PLCs (programmable logic controllers) in the variable drive,” explains Jarrett Campbell, packaging segment manager at Schneider Electric, the French-based automation controls supplier with U.S. headquarters in Palatine, Ill. “Where that comes into play with the packaging machine is you have different functions with one drive. The changeover is embedded in the drive, so you don’t have to bring in a different machine. The drive with the distributed I/O (input/output) allows you to plug-and-play.”With the cost of robots coming down—and the cost of manual labor going up—robotic manipulators are becoming more popular as a way to add flexiblity to packaging equipment. “When people think of robotics, they think automotive, with arms welding car parts, but it’s really a controlled movement,” says Chris Wood, industry account manager for food at gearmotors and drives vendor SEW-Eurodrive USA, in Latham, S.C. “The robot might have an arm, but it could be something that moves back and forth. Or it could be an elevator that goes up and moves back down.”Robotics have become cost effective also because the flexibility they bring has value. “I wish I had stock in robots because they’re taking over,” quips Harminder Singh, business development manager for the Global OEM Team at Rockwell Automation. “Robots are the easiest way to get the flexibility. We’re building the PLC to go right through the control to the robotics. It’s a cost-saver, since the price of robotics is coming down, but the most important part is the flexibility. The greatest cost savings comes from the flexibility because you can now dial in the changeover.”Standards also play a significant role in enabling the integration and flexibility that packaging machine customers are calling for. “Integrated motion and logic brings packaging machines into the new era. It’s all one language now, and one programmer can do the whole line with IEC 61131,” observes Al Morin, the food and packaging end-user executive at automation vendor Bosch Rexroth Corp., in Hoffman Estates, Ill. “That allows OEMs (original equipment manufacturers) the capability to implement features in motion without having to do the developing. The open standards are the key.” IEC 61131 is an open standard language for PLCs, promulgated by the International Electrotechnical Commission.Integrate devicesA packaging machine’s individual devices can be integrated, which gives operators the ability to make changeovers with fewer manual tasks. In some cases, no manual changes at all are required. The changeover can be done entirely from the human-machine interface (HMI). “When we talk integrated motion or modularity, we have an integrated servo drive, an intelligent servo,” says John Kowal, global manager at packaging controls vendor Elau Inc., in Schaumburg, Ill. “They’ve replaced conventional loaders and drives and motion controllers with a feedback cable and fieldbus. And we’ve integrated everything into a network that lets each machine have distributed control.”Open standards let manufacturers bring the packaging machinery into the data loop with the rest of the manufacturing line. “The packaging is integrated into the whole manufacturing line,” says Wood, at SEW-Eurodrive. “At one end they’re making it, at the other end they’re packing it. Now it’s like a network on your computer.”Flexibility, robotics, integration. These advances in packaging machines give end-users the ability to keep up with the demand for more variety in products and packaging. Some point to the marketing departments at OEMs as the drivers for flexibility and integration. But the technology developments that allow for these advances are also crucial. Now that these advances have been developed, there are competitive pressures in the OEMs’ marketplace that drive their adoption. For more information, search keywords “packaging machines” at www.automationworld.com To see the accompanying sidebar to this story - “Flexibility Cubed” - please visit www.automationworld.com/view-2922
vendor, to develop a common platform between the packaging machinery and the automation system. The integration keeps the entire manufacturing line including the packaging machinery visible from the control platform. “The integration allows the operators to control the entire line,” says Gilpin. “So if the packaging machinery goes down, the whole line goes down. It’s like one big machine.”Not all integration requires the complexity of PackML. In many cases, manufacturers use rudimentary Ethernet connections to send a few specific signals back and forth between the packaging machines and the manufacturing line. “If the customer specifies it, we can hardwire half a dozen devices to send discrete signals using Ethernet,” says Gilpin. He notes that Ethernet has become trendy because of its low cost. “It’s not quite real-time, but it’s very, very close—and it’s cheap, which helps a great deal.”Control technology also comes into play in making packaging machinery more flexible. “A lot of our customers want to get a variety of packaging out of one machine. We’re using Rockwell technology to make it easier for changeovers,” says Gilpin. “Now it can be done modularly. You change a few parts and make a couple of different adjustments on the screen. There are some manual things you do, but there are fewer of them now.”The improved flexibility is a response to customer demand for greater changeover speed. Quick changeover is a competitive factor and a demand that comes from the manufacturers’ customers who want more and more differentiation in packaging. Large retailers, for instance, are now demanding their own individual packaging for many of their consumer goods. In addition to controls integration, robotics is also playing a role in making packaging equipment more flexible. Some robotic-equipped machinery is now so flexible that changeovers can be completed entirely through a touchscreen, with few or no manual changes required.Flexibility key The need for manufacturers to change packaging on-the-run comes frequently through pressure from retail customers. “Wal-Mart will want its package of batteries to look different than Lowe’s or Home Depot’s,” says Carl Traynor, senior general manager, distribution and handling, Motoman Inc., a robot manufacturer in West Carrollton, Ohio. “You used to be able to do one package for all of them. Now you have to do different packages.”Another factor driving the need for flexibility is the sheer number of products produced by manufacturers. “We’re seeing rapid changes in the packaging for food and pharmaceuticals, and we’re seeing a greater number of SKUs (stock keeping units) they need to produce,” says Travis Holley, consultant for packaging at Siemens Energy and Automation Inc., the Alpharetta, Ga.-based automation vendor.
“That means changes to the machines need to be rapid. That leads to the modular design of the machines, and we need to have the controls to support the flexibility.”Some of the flexibility is achieved through use of servo-mechanisms, or servo for short. A servo is typically a motor that includes a velocity and/or position feedback device that can be adjusted. Servo drives can also be programmed to be self-regulating. Servo drives used in conjunction with PackML can help operators make quick changes to packaging machinery to produce different types of packaging.“You can increase the flexibility of machines to produce faster changeovers—and you can reduce the number of spare parts—by using servo motion and the variable structure of PackML,” says Mike Lamping, a technology leader for consumer products giant Procter & Gamble Co., and the chair of OMAC’s PackML Group. “There are over 100 different variables and an extensible array with PackML. That allows machines to talk to each other.” That communication allows the control system to tell the packaging equipment to change in order to shift packaging to match the output of the production line.Some of the new flexibility in packaging machinery comes through developments in embedded control devices and servo drives. “We have a product that has a controller embedded, and we add PLCs (programmable logic controllers) in the variable drive,” explains Jarrett Campbell, packaging segment manager at Schneider Electric, the French-based automation controls supplier with U.S. headquarters in Palatine, Ill. “Where that comes into play with the packaging machine is you have different functions with one drive. The changeover is embedded in the drive, so you don’t have to bring in a different machine. The drive with the distributed I/O (input/output) allows you to plug-and-play.”With the cost of robots coming down—and the cost of manual labor going up—robotic manipulators are becoming more popular as a way to add flexiblity to packaging equipment. “When people think of robotics, they think automotive, with arms welding car parts, but it’s really a controlled movement,” says Chris Wood, industry account manager for food at gearmotors and drives vendor SEW-Eurodrive USA, in Latham, S.C. “The robot might have an arm, but it could be something that moves back and forth. Or it could be an elevator that goes up and moves back down.”Robotics have become cost effective also because the flexibility they bring has value. “I wish I had stock in robots because they’re taking over,” quips Harminder Singh, business development manager for the Global OEM Team at Rockwell Automation. “Robots are the easiest way to get the flexibility. We’re building the PLC to go right through the control to the robotics. It’s a cost-saver, since the price of robotics is coming down, but the most important part is the flexibility. The greatest cost savings comes from the flexibility because you can now dial in the changeover.”Standards also play a significant role in enabling the integration and flexibility that packaging machine customers are calling for. “Integrated motion and logic brings packaging machines into the new era. It’s all one language now, and one programmer can do the whole line with IEC 61131,” observes Al Morin, the food and packaging end-user executive at automation vendor Bosch Rexroth Corp., in Hoffman Estates, Ill. “That allows OEMs (original equipment manufacturers) the capability to implement features in motion without having to do the developing. The open standards are the key.” IEC 61131 is an open standard language for PLCs, promulgated by the International Electrotechnical Commission.Integrate devicesA packaging machine’s individual devices can be integrated, which gives operators the ability to make changeovers with fewer manual tasks. In some cases, no manual changes at all are required. The changeover can be done entirely from the human-machine interface (HMI). “When we talk integrated motion or modularity, we have an integrated servo drive, an intelligent servo,” says John Kowal, global manager at packaging controls vendor Elau Inc., in Schaumburg, Ill. “They’ve replaced conventional loaders and drives and motion controllers with a feedback cable and fieldbus. And we’ve integrated everything into a network that lets each machine have distributed control.”Open standards let manufacturers bring the packaging machinery into the data loop with the rest of the manufacturing line. “The packaging is integrated into the whole manufacturing line,” says Wood, at SEW-Eurodrive. “At one end they’re making it, at the other end they’re packing it. Now it’s like a network on your computer.”Flexibility, robotics, integration. These advances in packaging machines give end-users the ability to keep up with the demand for more variety in products and packaging. Some point to the marketing departments at OEMs as the drivers for flexibility and integration. But the technology developments that allow for these advances are also crucial. Now that these advances have been developed, there are competitive pressures in the OEMs’ marketplace that drive their adoption. For more information, search keywords “packaging machines” at www.automationworld.com To see the accompanying sidebar to this story - “Flexibility Cubed” - please visit www.automationworld.com/view-2922
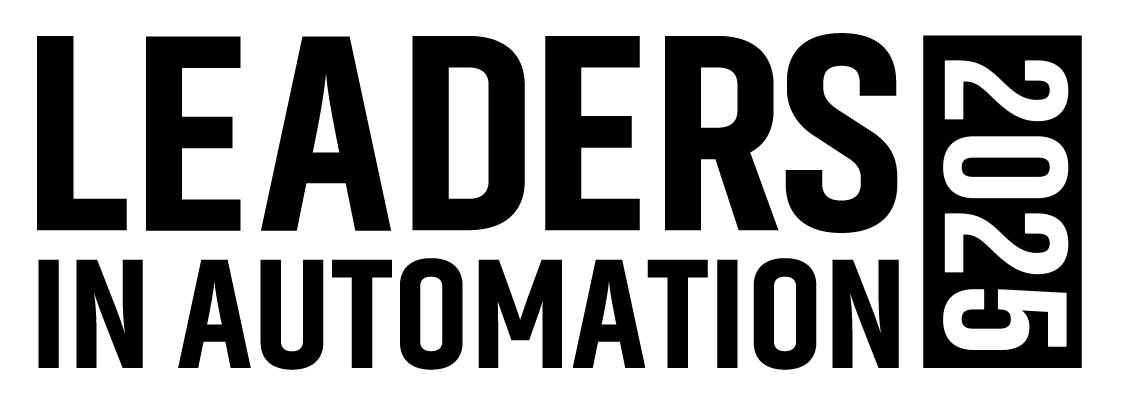
Leaders relevant to this article: