When it comes to the maintenance technicians at your manufacturing company, you’ve really gotta hand it to ’em…literally. If you'd like to see big producvivity gains from your maintenance techs, try handing them each a mobile, handheld computing device to help them better do their jobs. “Mobility,” after all, is one of the fastest growing trends in asset maintenance these days. And for good reason. Improvements in maintenance tech productivity are often reported at 20 percent or better when handheld computers are used, due to reduced paperwork requirements alone. Other mobility benefits include better data accuracy and improved regulatory reporting. Further, many industry sources agree that one of the most important advantages of putting handhelds in the field comes through getting a better handle on your assets—both at the enterprise level and at the maintenance tech level. If technicians can connect to enterprise applications via wireless handheld computing devices, for example, they can download information in the field that is needed for diagnosis and repairs, such as failure codes, schematics, parts inventories or the recent repair history on a piece of equipment. What’s more, if they notice equipment problems or anomalies during their rounds, they can upload pertinent data or enter a work order immediately using their handhelds, instead of writing it down and waiting for someone to enter it into the system.This means that needed repairs get done sooner— preventing possible breakdowns— and that managers have more accurate and timely information for predictive maintenance analysis and scheduling. The result, say industrial mobility proponents, is improved asset uptime and longer asset life. Quick paybacksSeveral industrial end-users interviewed by Automation World are quick to confirm these and other advantages of mobility technology. BP p.l.c., the London-based energy company, for example, is projecting savings of about $1 million per year from equipping operators at BP’s Carson, Calif., refinery with mobile handhelds for use on their daily equipment rounds. The savings will come through improved people productivity and better availability of assets, notes Dave Lafferty, technology consultant for the company’s Chief Technology Office, in Warrenville, Ill. Given those kinds of savings, BP currently plans to deploy the technology at two additional U.S. refineries soon, and will probably also use it at other refining and non-refining operations worldwide, Lafferty says.Likewise, at KeySpan Corp., New York state’s largest electric generator, John Ragone, automation manager, office of electric generation, believes that a new mobility solution his company is piloting for use by its maintenance personnel and others has the potential to produce major savings. Using phone/Pocket PCs (personal computers) communicating through a commercial cellular network, KeySpan technicians are able to access key performance indicators (KPIs) in real-time, whether the techs are up on a stack monitoring emissions, or down at a tank farm taking readings. The application relies on software from Transpara Corp., of Pleasanton, Calif., known as Visual KPI, which draws on data housed in KeySpan’s PI historian, supplied by OSIsoft Inc., San Leandro, Calif. The PI database interfaces to all KeySpan systems across six plants, storing real-time data on temperatures, fluid pressures, equipment vibrations and the like.“You name it, and we have communications with it via our PI database,” says Ragone. “So now, by putting this Transpara Visual KPI product on top of it, we’re able to actually pull out specific data for what we’re working on.” Engineers, managers and technicians will use their Pocket PCs to access preconfigured KPI screens for a real-time look at what’s happening without going to the control room or the office. For quick access, the KPI screens can be stored as Web browser favorites on the handheld devices, and users can drill down into the data as required. The ability to distribute real-time metrics data on demand, when and where needed, will pay off quickly in helping KeySpan technicians and managers to head off operating problems and breakdowns, Ragone says. “When you consider that the loss of a generator can cost hundreds of thousands of dollars a day in replacement costs for power, then it doesn’t take a lot to get a return on investment on something like this,” he observes. Similarly, Lynn Modisette, a Houstonbased senior systems administrator for Air Liquide America, a producer of industrial gasses, says that equipping the company’s field technicians with wireless handhelds is a no-brainer. Air Liquide’s nationwide maintenance field staff has been using handheld devices driven by modems and docking stations since 2002, and the company is now converting to wireless Pocket PCs. “The pricing on these devices is so low now, at about $289 each, that the cost is inconsequential compared to the service that they provide,” Modisette says.Lost paperThe Air Liquide technicians perform maintenance and repairs on company assets such as tanks, vessels and telemetry equipment that reside at customer sites. In the past, when the process was paper driven, technicians would make repairs on equipment, write down what they did, and then mail or fax the information in to the company; the data would then be keyed into the company’s Maximo computerized maintenance management system (CMMS) by a data entry clerk. “It could take days or weeks to get the data, and sometimes we didn’t get the data at all, because the paperwork would get lost,” Modisette recalls. But with the mobility system in place, the technicians are able to transmit the data immediately via their handhelds directly to the Maximo system. This improves data accuracy, and eliminates technician paperwork and data entry labor, while also making the information immediately available to managers for report generation and analysis. Air Liquide’s new wireless handheld devices—6700 models provided by cellular carriers Sprint and Verizon—rely on mobility software supplied by Syclo LLC, based in Hoffman Estates, Ill. The software provides customized screens for the technicians that are geared to Air Liquide work processes. The handhelds also double as phones, and are equipped with cameras, says Modisette. “So if a technician sees something that he can’t repair himself, he can literally take a picture, send it to someone with that expertise, and get help,” she says. Built-in global positioning system (GPS) technology in the handhelds also aids managers in tracking technician locations, and in deciding which technician to assign to emergency work orders, which can be downloaded to the handhelds in the field. Given these and other capabilities, “I would say the [mobility] system pays for itself probably within a month or less,” Modisette estimates. “The ROI (return on investment) case is very compelling with mobile,” agrees Pradeep Nair, senior product marketing manager at MRO Software, Bedford, Mass., an IBM company, and the supplier of Maximo CMMS software. He puts the typical maintenance mobility payback at about six months. MRO last January began offering an integrated mobility module with its current Maximo 6 enterprise system, and also sells a partner-based mobility solution provided by Syclo. Today, fewer than 10 percent of Maximo users—which total more than 10,000—are using the mobility piece, Nair says. But mobility deployments are growing rapidly. “In the past, when we had a customer engagement, mobile was secondary. Customers would try to get the main application installed first, and then a year or two later, they would look at mobile,” Nair observes. “But nowadays, mobile is part of the initial discussions.” Nair says that between 20 percent and 30 percent of first time Maximo buyers are now implementing mobility with their initial installations, and mobility deployments by legacy customers is also on the rise. Off the chartsAt Syclo, Marketing Vice President Mark Curatolo confirms the trend. “Interest in our products, and in using mobile technology in general, is off the charts right now,” he says. Syclo sells its mobility software as a “bolt-on” package that works with a variety of enterprise level systems, including those of enterprise resource planning (ERP) vendors Oracle and SAP, and CMMS vendors Datastream (now part of Infor), Indus (which is being merged with MDSI, a mobile workforce management software provider) and MRO, among others. Syclo software integrates with these backend databases and repurposes the data, based on customer requirements, for viewing on a range of small-screen handheld computing devices. These include the ruggedized devices from Intermec Technologies, Everett, Wash., and Symbol Technologies, Holtsville, N.Y., among others, which are used frequently in industrial applications.One key to wireless mobility in the industrial maintenance space is that the handheld devices used must be able to capture and hang on to data when wireless coverage is lost, says Curatolo. No matter what wireless technology is used—be it commercial cellular, in-plant WiFi based on the Institute of Electrical and Electronics Engineers’ IEEE 802.11 Wireless Fidelity standard, or some other wireless technology—there is no such thing as ubiquitous coverage, Curatolo points out. That’s particularly true in electrically noisy industrial environments, he says. “So you’ve got to be able to work in and out of coverage.”Clipboard-to-computerBP’s Chief Technology Office was thinking along those lines when it developed its mobility application used for operator rounds at BP’s Carson, Calif., refinery, says Lafferty. BP’s so-called “clipboardto- computer” application relies on WiFi connections using what Lafferty calls an “occasionally disconnected” model. The goal of the project, initiated in 2004, was two-fold. BP has an aging operator workforce. Before this group retires, the company wants to capture and transfer their knowledge of best practices to its younger operators. Secondly, as part of BP’s “Highly Reliable Organization” initiative, “we were looking for opportunities to apply operations more consistently across units and refineries,” Lafferty observes.At the Carson refinery and elsewhere, operators have traditionally walked daily rounds, taking readings on equipment and writing down observations on paper attached to clipboards. This data is then entered by clerks into central computer systems. For the clipboard-to-computer initiative, BP is replacing those clipboards with Symbol MC9000 series industrial handheld mobile computers. The intrinsically safe, Windows Mobile-based units are loaded with IntelaTrak mobility software from SAT Corp., of Houston, and can link wirelessly to BP’s PI historian system. The conversion from clipboards begins with extensive interviews of senior operators in each refinery unit, with the goal of capturing a set of best practices for doing rounds and readings in each unit. These practices are then put into a set of business rules covering multiple scenarios, Lafferty explains. This information is then loaded onto the handhelds to be used by the unit operators during their rounds.Step-by-stepThe rules follow a step-by-step approach, specifying the order in which assets, such as pumps and compressors, should be inspected, and providing specific instructions for each task. An operator scans a bar code on each piece of equipment using a scanner built into the handheld computer. This triggers the instruction series for that asset: Is the unit operational? If the answer is yes, the operator might be instructed to take temperature and pressure readings, for example. If the answer is no, the instructions might call for an oil level check, or inspection for oil seepage or leaks, for instance, and might also provide directions for the safest, most effective way to bring a secondary unit online. The next step might then be to issue a maintenance work order for the non-operational asset, which is transmitted, along with data readings and other pertinent information, back to the central server via the wireless connection. That’s where the “occasionally disconnected” model comes in. The refinery environment is filled with metal, motors and overhead pipes that can interfere with wireless coverage. So at the beginning of each round, the operator starts within a control room or other wireless coverage area and loads up everything from the central server needed for that particular round, Lafferty says. Then, if coverage is lost during the round, the operator can continue to work, receiving instructions and storing readings on the handheld. When the operator then walks back into a WiFi hot spot coverage area, the handheld system recognizes the coverage, and automatically connects and resynchs with the central server.Importantly, says Lafferty, data feeding into the PI historian from the handhelds “looks no different than if they were captured by the automation system. What you don’t want to do is create a silo of yet another subsystem that you have to log into to get those [operator round] readings,” he observes. This structure enables the easy use of the data by a variety of BP audiences, including operators, engineers and maintenance personnel.On the maintenance side, the immediate availability of the operator rounds data for analysis provides added lead time. “It helps get you out of a reactionary maintenance program because these guys (operators) spot problems early on and alert the maintenance people,” Lafferty says. The operator rounds data are also more readily available for predictive analysis and trending. “It definitely moves the maintenance world into a more proactive environment, which is part of being a ‘Highly Reliable Organization.’ If all you’re doing is reacting to fire drills, it’s hard to optimize,” Lafferty observes.Following the recent successful completion of a proof-of-concept phase for the clipboard-to-computer initiative, BP has launched a three-year, phased project to implement the program across all 13 units at the Carson refinery, with handheld computing devices going to several hundred operators. BP’s security staff has been involved with the project from the beginning, says Lafferty, and has developed a “layered” approach to security for the wireless application.Additional plans call for a phase-in of similar clipboard-to-computer programs before yearend at BP’s Whiting, Ind., refinery, and later at its Toledo, Ohio, refinery, Lafferty adds. Individual assessments will be required at each site, but he expects that the $1 million per year savings projected for the Carson, Calif., refinery will be roughly transferable to Whiting and Toledo, which are similar-sized operations.Given the success at Carson, Lafferty notes that other BP business units, such as exploration and production, have expressed interest in the handheld technology. Mobility could pay benefits, even in remote locations without wireless coverage, he indicates. In these areas, handheld unit synchronization with a central system could be done using a cradle attached to a conventional PC. “One of the key learnings [from the Carson project] was that you don’t necessarily need wireless to get benefits from mobility,” Lafferty says. In fact, while most agree that the trend in mobility is toward wireless, many users today are still relying on synch cradles. For example, popular handheld tools from Emerson Process Management, such as the 375 Field Communicator, a Hart and Foundation Fieldbus configuration, calibration and diagnostics tool, as well as the CSI 2130 Machinery Health Analyzer, used for vibration collection and analysis, both require a physical hookup for central system synchronization. But as noted by Stuart Harris, vice president of marketing at Emerson, the Austin, Texas-based process automation vendor, “I think wireless most definitely will play a role in our next generation of handheld products.”Likewise at Honeywell Process Solutions, a Phoenix automation solutions vendor, Dave Kaufman, director of business development, notes that his company’s IntelaTrak PKS handheld unit used for field operator rounds is still deployed primarily in a dockable version. Honeywell’s Mobile PKS, a larger, industrially hardened tablet PC intended for wireless operator use, is becoming more popular, he adds. But Kaufman expects a broader migration to wireless handhelds will come with the emergence of more robust and reliable industrial wireless networks.Get educatedJulie Fraser, principal at Industry Directions Inc., a Cummaquid, Mass., market research and consulting firm, sees mobility applications growing “reasonably rapidly” in manufacturing today. But one challenge, she believes, involves a lack of awareness among industrial end-users. “I think there are probably a lot of people using Maximo software who don’t know that MRO has an entire mobility suite that goes with it,” Fraser observes. Likewise, many end-users may not be aware of relatively young companies such as Transpara, and the capabilities that their software can provide, she adds. “So that, to my mind, is the biggest thing that’s going to slow this down, just getting the market educated as to what’s available.”To see the main story this sidebar was taken from - "Saving Big From Wireless Extras" - please visit www.automationworld.com/view-2783*Web Extra: To download or listen to the complete Podcast interview with Industry Directions' Julie Fraser, go to www.automationworld.com/view-2713For more information, search keyword
“handheld” at www.automation.com
“handheld” at www.automation.com
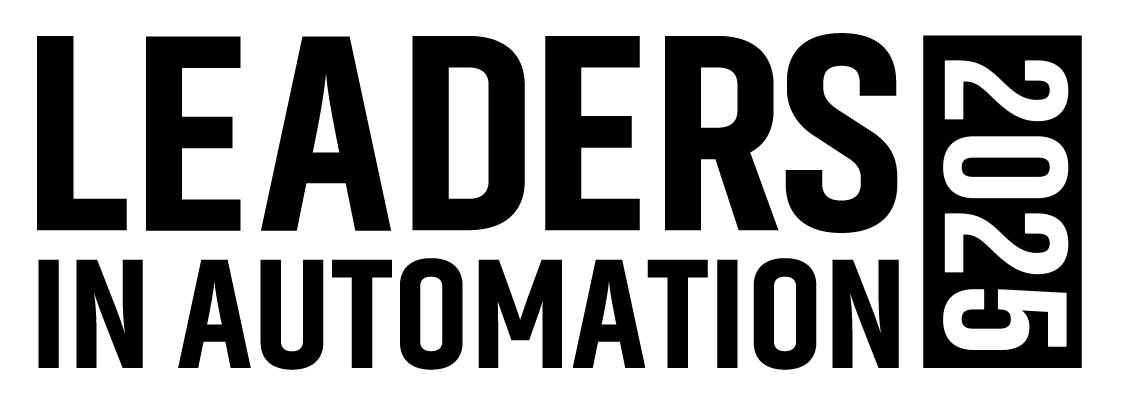
Leaders relevant to this article: