Condition
monitoring can save you a lot of money. Just ask the engineering staff
at Panhandle Energy, a Houston-based pipeline company. New monitoring technology led staffers there to find a previously undiscovered crack in a compressor impeller only two weeks into a trial period that management had negotiated with SmartSignal Corp., of Lisle, Ill., and Invensys Process Systems, of Foxboro, Mass.Had the crack been allowed to propagate, the engineers say that the resulting failure would have been catastrophic. They estimate that the cost would have included both an $800,000 repair bill and lost sales. The savings didn’t stop there, however. “While maintenance was fixing that problem, the models monitoring the other compressors also started catching other things that were going to cause failures in the future,” reports Neil Cooper, general manager of Avantis, the Invensys business unit that offers condition monitoring and management software. Finding the problems early saved the company an estimated $3 million.Although manufacturers have known about the advantages of condition monitoring for decades, many, like Panhandle Energy, seem to be taking a renewed interest in it. According to Cooper, one reason is a sense of urgency generated by the graying of the work force and the coming retirement bubble. “We really must get our arms around how to manage these facilities, because all that knowledge will begin walking out the door over the next five years,” he says.Another reason for the surge in interest is the developments that have been occurring in the technology. Today’s sensors, for example, often contain a measure of intelligence that not only can enrich the data that they report but also often make rudimentary decisions. Software companies such as Avantis have built on this intelligence by devising ways to sift through and make use of the massive amounts of data flowing into already overloaded information systems. The latest generation of condition-monitoring software draws what Cooper calls context from the data. “Simple vibration monitoring, for example, doesn’t really tell you much until you put the measurements in the context of [other parameters like] RPM (revolutions per minute), throughput,
temperature and maintenance life,” he says. “Putting the data into context turns condition monitoring into condition management.”The key for doing this is the modeling software that software companies have developed. Some, for example, make sense of stress-wave, infrared, acoustical, and other data, pre-conditioning the data for the higher-level knowledge management systems that are available today. SmartSignal, for example, applies empirically based modeling software that its engineers have developed for various kinds of equipment. Using what the software developer calls similarity-based modeling, the software not only customizes the models to each of piece of equipment, but also applies sophisticated pattern-recognition algorithms to monitor how its operating variables change in dynamic conditions.“As anyone in operations can tell you, each piece of equipment has its own personality,” says John Kerastas, a spokesman for the company. “One unit might run a little hot, but another might run a little cold, even though the two are the same model and make.” One explanation is that different people probably build them on different days. Another is that differences in installation, maintenance and operation also cause slight differences in performance.Early warningBy weighing the relations in a much larger set of data than is typical, the models offer what Kerastas calls a more holistic and “personal” look at each piece of equipment. “It provides early warnings for small deviations from what is normal for that particular unit,” he says. Even though the operating parameter in question might fall within the normal operation range, the model will flag deviations that are abnormal given other readings. Kerastas claims that this holistic approach saved Detroit Edison about $1 million. At one of the energy company’s plants, the software monitoring the primary air fan warned an analyst that the motor was running at about 90 degrees Celsius. The temperature was 20 degrees below the alarm level, but it was well above what it should have been, given the input from the other sensors. During the next scheduled shutdown for maintenance, the technicians removed and cleaned the motor, which was very dirty. Had the fan motor temperature—high for that time of year—not been detected, the equipment could have failed, causing a forced outage and a half-unit derate of 300 megawatts (MW) for as long as five days. Tailor-made modelsAnother example of modeling software is ROMeo, optimization and modeling software from Invensys’ SimSci-Esscor business that is used by oil refineries and other chemical plants. The built-in models already contain the typical process parameters and their interrelations for typical processes. “Because we are a process automation company, we know that a certain kind of reading from a motor, pump or blower means a worn bearing—or a cracked impeller,” explains Cooper. Installation is largely a matter of tailoring the existing generic rules to the processes in a particular plant. Because these rules are in software, rather than on paper, users can tailor them to fit the peculiarities of a plant, refine the model over time, and use it to monitor the process. “When you map it against real-time data, it can give you warning points,” says Cooper. “If production consistently stays off a target value, it gives you an indicator that either your design was wrong or you should look for a developing problem.” To create the context that Cooper talks about, Avantis also offers Invensys CM (Condition Monitoring), rule-based software that coordinates activity based upon process parameters and diagnostic data. The software collects information from various sources—unintelligent, intelligent, and historical—and combines the readings according to the pre-programmed rules to coordinate operations, maintenance and engineering.Six hours to failure“If a developing condition is in an early stage, then maybe you will simply track it,” explains Cooper. “If the trend is progressing faster than expected, then you might need to adjust your planned outage or maintenance schedule. If the trend is severe, you might need to dispatch a maintenance technician and inform the operator.” The software can even tell management that the trend is toward a failure in six hours and link the event to corporate financials to determine its economic impact. Sophisticated mathematical models are not confined to the process industry. They also are important productivity enhancers for machinery in discrete parts manufacturing. In fact, many builders of machinery for high-volume manufacturing will embed condition monitoring in their machines’ distributed control systems. “Today’s digital intelligent drives have enough CPU (central processing unit) power and resources to run mechanical mathematical models and compare them with the real mechanics,” says Karl Rapp, automation and machine tool branch manager, Electric Drives and Controls Division, at vendor Bosch Rexroth Corp. in Hoffman Estates, Ill.These models can not only monitor the motor’s torque and force as functions of current, but also compare the commanded and actual velocities and positions of the axes. Excessive deviations from the expected values can be indications of excessive wear, play in the power train of a slide or other problems. Consequently, machine builders can program their controllers to alert maintenance, stop the machine or take some other protective action before the mechanics deteriorate to the point where they fail and force lengthy unscheduled downtime for repairs.Bosch Rexroth’s strategy is to emulate automatic human reflexes by exploiting the computing power available in today’s drives and the information already residing in them. Certain reflexes—such as breathing and the sudden, involuntary jerking of one’s hand away from a hot burner on a stove—bypass the central processing unit in the brain and rely instead on the nervous system for a speedier response. “It is exactly the same in automation,” says Matthias Wahler, a drive system development engineer at Bosch. “The detection of a fatal error in the drive must lead to the proper reaction right there.”Although electric drives have exercised this ability internally for a while now, Bosch has extended this protective function to the axis mechanics through a feature that the company calls the Productivity Agent. Wahler describes the feature as “reflexes” added to protect the mechanics of the axis.Do-it-yourself modelingOther modeling software for condition monitoring is emerging from research laboratories. One is Watchdog Agent, an intelligent maintenance system developed over the last five years by the Center for Intelligent Maintenance Systems (CIMS), a National Science Foundation industry-university research cooperative headquartered at the University of Cincinnati. The software helps users to create custom, embedded, predictive-maintenance software for their equipment and processes. “Rather than developing a generic monitoring package, we developed a toolbox that industrial users can deploy quickly in days, rather than months and years,” says Jay Lee, Ph.D., the Center’s director. This toolbox contains more than 18 algorithms that tailor the embedded monitoring functions to the application at hand. The tools generate the features necessary for monitoring and predicting the condition of specific components or units, such as bearings, valves, spindles, motors and compressors.To guide users through the process, the researchers designed a QFD (quality function deployment) re-configuration interface that helps users to select the pertinent criteria for their applications. “It’s kind of like an Excel-based matrix indicating the parameters that you need to configure,” says Lee. “You check the appropriate boxes, and the software automatically suggests which tool you should use.” Now that researchers have developed the software tools for both the National Instruments hardware platform and that based on PC104, an embedded computer standard, the research has entered its final phase, the commercialization phase. Automaker Toyota Motor Manufacturing North America Inc., based in Erlanger, Ky., is already using Watchdog Agent at its Georgetown, Ky. facility, as well as CIMS’ approach for monitoring surge compression ratios, to avoid bearing failures on compressors. Lee reports that more projects are also underway at Harley-Davidson Motor Co., of Milwaukee, General Motors Corp., of Detroit, Samsung in Korea, Komatsu in Japan, and GE-Aviation, of Evendale, Ohio. These companies perceive their investments in condition monitoring and predictive maintenance as the natural next step after lean manufacturing. “They are already lean, so the next step is to improve the health of the equipment to prevent breakdowns,” explains Lee. “So zero breakdowns is the new thinking.” Supporting this strategy through condition monitoring is the healthy way to squeeze more profit from lean plants. To see the accompanying sidebar to this story - "Wireless Expands Applications for Condition Monitoring, please visit www.automationworld.com/view-2784
For more information, search keywords “condition monitoring” at www.automationworld.com.
temperature and maintenance life,” he says. “Putting the data into context turns condition monitoring into condition management.”The key for doing this is the modeling software that software companies have developed. Some, for example, make sense of stress-wave, infrared, acoustical, and other data, pre-conditioning the data for the higher-level knowledge management systems that are available today. SmartSignal, for example, applies empirically based modeling software that its engineers have developed for various kinds of equipment. Using what the software developer calls similarity-based modeling, the software not only customizes the models to each of piece of equipment, but also applies sophisticated pattern-recognition algorithms to monitor how its operating variables change in dynamic conditions.“As anyone in operations can tell you, each piece of equipment has its own personality,” says John Kerastas, a spokesman for the company. “One unit might run a little hot, but another might run a little cold, even though the two are the same model and make.” One explanation is that different people probably build them on different days. Another is that differences in installation, maintenance and operation also cause slight differences in performance.Early warningBy weighing the relations in a much larger set of data than is typical, the models offer what Kerastas calls a more holistic and “personal” look at each piece of equipment. “It provides early warnings for small deviations from what is normal for that particular unit,” he says. Even though the operating parameter in question might fall within the normal operation range, the model will flag deviations that are abnormal given other readings. Kerastas claims that this holistic approach saved Detroit Edison about $1 million. At one of the energy company’s plants, the software monitoring the primary air fan warned an analyst that the motor was running at about 90 degrees Celsius. The temperature was 20 degrees below the alarm level, but it was well above what it should have been, given the input from the other sensors. During the next scheduled shutdown for maintenance, the technicians removed and cleaned the motor, which was very dirty. Had the fan motor temperature—high for that time of year—not been detected, the equipment could have failed, causing a forced outage and a half-unit derate of 300 megawatts (MW) for as long as five days. Tailor-made modelsAnother example of modeling software is ROMeo, optimization and modeling software from Invensys’ SimSci-Esscor business that is used by oil refineries and other chemical plants. The built-in models already contain the typical process parameters and their interrelations for typical processes. “Because we are a process automation company, we know that a certain kind of reading from a motor, pump or blower means a worn bearing—or a cracked impeller,” explains Cooper. Installation is largely a matter of tailoring the existing generic rules to the processes in a particular plant. Because these rules are in software, rather than on paper, users can tailor them to fit the peculiarities of a plant, refine the model over time, and use it to monitor the process. “When you map it against real-time data, it can give you warning points,” says Cooper. “If production consistently stays off a target value, it gives you an indicator that either your design was wrong or you should look for a developing problem.” To create the context that Cooper talks about, Avantis also offers Invensys CM (Condition Monitoring), rule-based software that coordinates activity based upon process parameters and diagnostic data. The software collects information from various sources—unintelligent, intelligent, and historical—and combines the readings according to the pre-programmed rules to coordinate operations, maintenance and engineering.Six hours to failure“If a developing condition is in an early stage, then maybe you will simply track it,” explains Cooper. “If the trend is progressing faster than expected, then you might need to adjust your planned outage or maintenance schedule. If the trend is severe, you might need to dispatch a maintenance technician and inform the operator.” The software can even tell management that the trend is toward a failure in six hours and link the event to corporate financials to determine its economic impact. Sophisticated mathematical models are not confined to the process industry. They also are important productivity enhancers for machinery in discrete parts manufacturing. In fact, many builders of machinery for high-volume manufacturing will embed condition monitoring in their machines’ distributed control systems. “Today’s digital intelligent drives have enough CPU (central processing unit) power and resources to run mechanical mathematical models and compare them with the real mechanics,” says Karl Rapp, automation and machine tool branch manager, Electric Drives and Controls Division, at vendor Bosch Rexroth Corp. in Hoffman Estates, Ill.These models can not only monitor the motor’s torque and force as functions of current, but also compare the commanded and actual velocities and positions of the axes. Excessive deviations from the expected values can be indications of excessive wear, play in the power train of a slide or other problems. Consequently, machine builders can program their controllers to alert maintenance, stop the machine or take some other protective action before the mechanics deteriorate to the point where they fail and force lengthy unscheduled downtime for repairs.Bosch Rexroth’s strategy is to emulate automatic human reflexes by exploiting the computing power available in today’s drives and the information already residing in them. Certain reflexes—such as breathing and the sudden, involuntary jerking of one’s hand away from a hot burner on a stove—bypass the central processing unit in the brain and rely instead on the nervous system for a speedier response. “It is exactly the same in automation,” says Matthias Wahler, a drive system development engineer at Bosch. “The detection of a fatal error in the drive must lead to the proper reaction right there.”Although electric drives have exercised this ability internally for a while now, Bosch has extended this protective function to the axis mechanics through a feature that the company calls the Productivity Agent. Wahler describes the feature as “reflexes” added to protect the mechanics of the axis.Do-it-yourself modelingOther modeling software for condition monitoring is emerging from research laboratories. One is Watchdog Agent, an intelligent maintenance system developed over the last five years by the Center for Intelligent Maintenance Systems (CIMS), a National Science Foundation industry-university research cooperative headquartered at the University of Cincinnati. The software helps users to create custom, embedded, predictive-maintenance software for their equipment and processes. “Rather than developing a generic monitoring package, we developed a toolbox that industrial users can deploy quickly in days, rather than months and years,” says Jay Lee, Ph.D., the Center’s director. This toolbox contains more than 18 algorithms that tailor the embedded monitoring functions to the application at hand. The tools generate the features necessary for monitoring and predicting the condition of specific components or units, such as bearings, valves, spindles, motors and compressors.To guide users through the process, the researchers designed a QFD (quality function deployment) re-configuration interface that helps users to select the pertinent criteria for their applications. “It’s kind of like an Excel-based matrix indicating the parameters that you need to configure,” says Lee. “You check the appropriate boxes, and the software automatically suggests which tool you should use.” Now that researchers have developed the software tools for both the National Instruments hardware platform and that based on PC104, an embedded computer standard, the research has entered its final phase, the commercialization phase. Automaker Toyota Motor Manufacturing North America Inc., based in Erlanger, Ky., is already using Watchdog Agent at its Georgetown, Ky. facility, as well as CIMS’ approach for monitoring surge compression ratios, to avoid bearing failures on compressors. Lee reports that more projects are also underway at Harley-Davidson Motor Co., of Milwaukee, General Motors Corp., of Detroit, Samsung in Korea, Komatsu in Japan, and GE-Aviation, of Evendale, Ohio. These companies perceive their investments in condition monitoring and predictive maintenance as the natural next step after lean manufacturing. “They are already lean, so the next step is to improve the health of the equipment to prevent breakdowns,” explains Lee. “So zero breakdowns is the new thinking.” Supporting this strategy through condition monitoring is the healthy way to squeeze more profit from lean plants. To see the accompanying sidebar to this story - "Wireless Expands Applications for Condition Monitoring, please visit www.automationworld.com/view-2784
For more information, search keywords “condition monitoring” at www.automationworld.com.
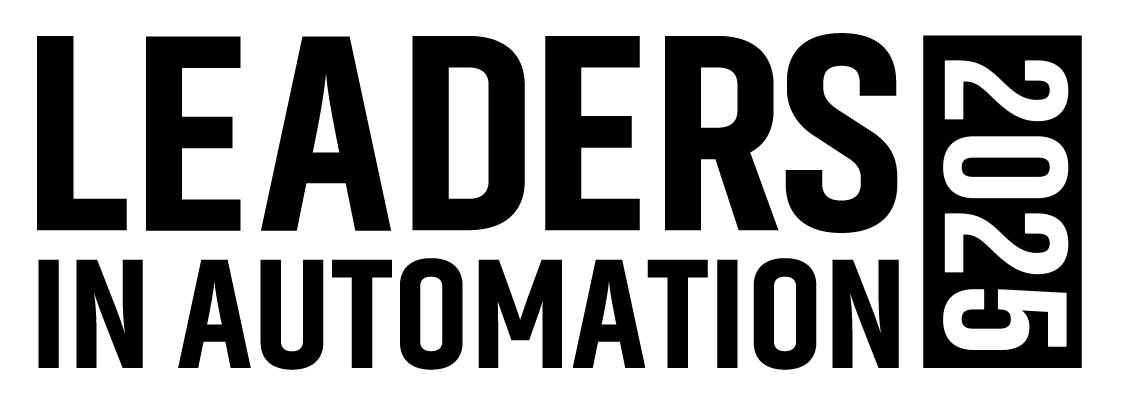
Leaders relevant to this article: