Today, when discussions turn to industrial wireless networking, one often hears a curious mix of successful application stories combined with promises of much to come in the future. The field is new enough to generate a whole series of unfamiliar buzzwords that can leave managers and engineers scratching their heads in bewilderment when trying to decide which direction to go in their plant automation designs.Wireless technology is not totally new to the factory. Remote supervisory control and data acquisition (SCADA) sites have used specialized radio telemetry for many years. Also, the growth of the network popularly called WiFi (from wireless fidelity) for personal computer (PC) networking based on the 802.11 standard of the Institute of Electrical and Electronics Engineers (IEEE) has bled over into industrial applications.Now, however, a recent series of new sensor network products—especially for process plants—is showing promise for helping engineers achieve better plant performance. To be sure, continued bickering among technology suppliers regarding which technology is best
suited to industrial performance clouds this promise. But there are signs that the situation is beginning to sort itself out, and now may be the ideal time for manufacturing professionals to take the deep dive into the promise of wireless.Wireless pump controlThe Coca-Cola Co. purchased a plant in southern Missouri to bottle its Dasani brand of drinking water. The facility would draw water from the nearby Roubidoux Formation—the source of some of the purest water in North America. What Coca-Cola officials didn’t know, however, was that the plant was not equipped to pump the roughly 1,000 gallons of water per minute needed to meet demand. At best, the plant would be able to pump only half that amount.Now, though, the plant is pumping more than 1,500 gallons of water per minute, thanks to a new control and data acquisition system provided by Opto 22, of Temecula, Calif. “We used Opto 22 hardware and software to build this system primarily for the sake of simplicity,” says Barrett Davis, owner of The Automate Company LLC, the Pacific, Mo., control systems integrator that designed and installed the system for Coca-Cola. “We typically build the panels for our control systems from scratch, and the Opto 22 hardware and software makes it easy to do that.”The system includes a pump on each of the three wells, each controlled by a variable frequency drive (VFD). The three drives must work in coordinated fashion to ensure that the storage tank does not overflow. “Any of the well pumps can be designated as the lead,” Davis explains. “That pump will have a set point for moving water at a certain level of pressure, say 60 psi (pounds per square inch). Once that point is set, the pump will work to provide that level of pressure to the plant at all times. The VFD works to speed the pump up or slow it down, as necessary, to keep the pressure at that level.”An Ethernet network for the system connects an OptoTerminal—the primary operator interface—and Snap Ultimate input/output (I/O) controller and I/O systems, many of which are connected to the network wirelessly. The system continually monitors pumping activity. It detects when a VFD is operating at maximum speed and can no longer make the lead pump push enough water to keep up the required level of pressure. When that happens, an additional pump is called into action. This new “lag” pump begins moving water at a preset minimum speed.“Having an Ethernet-based system and running it over a wireless network means that all of the communication takes place very quickly and efficiently,” Davis says. “When the Snap Ultimate unit sends out a request for information, the response arrives within three milliseconds, as opposed to five to 10 seconds with traditional radio telemetry equipment.” This fast response time means that the plant is always operating at maximum efficiency and never pumping too much or too little water.Possible applicationsWhile there are already SCADA and some control applications such as this one using wireless technologies, many possible applications are awaiting the outcome of standardization efforts. There are two organizations working on standards—the Hart Communications Foundation and the SP100 committee of the Instrumentation, Systems and Automation Society (ISA). Davis Mathews, regional business unit manager for interface at Phoenix Contact, a Harrisburg, Pa.-based automation supplier, reflects the opinions of many when he notes that the SP100 committee seems to be divided on technology into two groups driven by vendors Emerson Process Management and Honeywell Process Solutions, respectively.“One thing I noticed was SP100 trying to emulate the IEEE 802.11 wireless local area network,” says Mathews. “That will be popular.
We sell about $5 million per year now of 802.11 products with a proprietary-based product. But customers are looking for a standards-based product so that they can use more devices. Meanwhile, the Hart group decided to move quickly and develop its own wireless standard. It is agreeing on the IEEE 802.15.4 mesh standard for radios. In this area, technology innovation comes from suppliers, but needs to come from users. So, Hart put together a demo with products from eight suppliers for the ISA Expo (Oct. 17-19, in Houston) to enable customers to see a direction and provide feedback.”Mathews sees major customer applications starting in the sensing world. The technology is so new in manufacturing that customers are hesitant to move to continuous monitoring or control right now. “The technology’s evolving,” says Mathews. “Customers are already sending data. It’s only a matter of time before they apply wireless to other needs. Look at the evolution of wired Ethernet use.”How big could wireless networking become? Senior Analyst Harry Forbes, of ARC Advisory Group Inc., the Dedham, Mass., analyst firm, writes in a research report titled “Wireless Technology in Process Manufacturing” that the worldwide market for wireless technology for manufacturing is expected to grow at a compound annual growth rate of 26 percent over the next five years—from $325.7 million in 2005 to more than $1 billion in 2010.Sean Keeping, vice president, technology, for ABB Instrumentation, St. Neots, England, also points to the two standards under development from the process industries point of view. “Hart has been discussed for some time and is reasonably well developed. We have some prototypes for testing by the industry. It’s not something that is device vendor-proprietary, it’s an industry standard. SP100 is slightly less developed than Hart, but many key players are looking at this. These two emerging standards are likely to succeed. I think the industry does not want a device specific or vendor specific solution.”Keeping believes customers will develop confidence in the technology as the suppliers prove that the newer products are both reliable and secure. Adds Gareth Johnseon, fieldbus communications specialist at ABB, “Users are using some proprietary products now, and they are asking for more information. It’s not like when the fieldbuses came in. We’re seeing a lot of inquiries about setting up pilots or field trials.”A matter of visionWhat are the important factors that standards bodies should consider? Hesh Kagan, director, new ventures, for automation supplier Invensys Process Systems, in Foxboro, Mass., says, “The function that comes to mind most is interoperability. But that may not be most important to users. That may be coexistence—that is, will the various radios interfere with each other, be immune to lightning or other radiation and the like? Interoperability will come with a bit-level standard.”Where will wireless technologies find a home in industry? Says Kagan, “Every customer has an application that’s most important to them. I see applications like field data logging from satellites and voice over Internet (VoIP) replacing some currently used radios, perhaps adding a little remote I/O to make remote control easier. I expect to see incremental video over the network for physical plant security. Another application is the mobile operator concept with tablet PCs where an operator can still be in touch with the operation even while stepping away from the main console to check out a problem somewhere else.“Coming down the pike, I see expanded condition monitoring with low-cost sensors. It’s going to be a whole new model of doing maintenance based on those sensors and model-based predictive maintenance. The dollars that can be saved in continuous process are enormous. In the longer term, an interesting thought is to consider what happens when these low-cost condition monitors take hold. They will be very inexpensive compared to today’s process measurement. What if at some point someone takes a look and thinks, ‘That condition monitor may be good enough for process measurement.’ I may have two excellent measurements now. But there’s a lot of math being developed that would say, ‘What if I have 20 to 30 not-so-excellent measurements but I can develop a profile that would give me better information overall?’ This is at least five to seven years out, but think of the potential.”Someone else thinking long term about the philosophy of process control is John Berra, president of Emerson Process Management. He says, “Plant knowledge is the key to improving business performance. No wires means no limits. We can put more sensors in plants at a tenth of the cost with wireless technologies. More eyes and ears in the plant means added intelligence.”Products nowEmerson announced the availability of several wireless sensor products and a gateway at its Users Exchange Conference Oct. 2-4 in Nashville. The technology uses IEEE 802.15.4 mesh radios with technology from Dust Networks. Says Bob Karschnia, vice president of technology for the Rosemount division of Emerson Process, “We did three years of field trials to test out various technologies. We looked at the CDMA (code division multiple access) tree structure, which uses direct sequence spread spectrum technology built on IEEE 802.11 WiFi, but then we switched to mesh networks built on IEEE 802.15.4 with frequency hopping. It coexists with WiFi
in a plant, but doesn’t require a site survey to install nodes. Reliability of a mesh network actually increases with the number of nodes installed.”Dave Kaufman, director of integrated field solutions at Honeywell Process Systems, in Phoenix, says, “As we looked at plant requirements, we saw different classes of applications, including safety, closed loop control, open loop control and monitoring. Customers told us they wanted to do them all, and if they could go wireless, they’d like to do that. So as we looked at architectures, the question we asked ourselves was, ‘How can we do this efficiently and effectively.’ Even if customers may not go directly to control applications right away, we wanted to provide a single infrastructure to handle everything. So, we went after a robust architecture with the performance to meet all requirements.”Robert Jackson, product marketing engineer at Austin, Texas-based test and automation systems vendor National Instruments (NI), sees the current state of wireless as the market “long tail” effect, citing a book by Chris Anderson, titled “The Long Tail: Why the Future of Business is Selling Less of More.” The long tail effect describes a curve with the quantity of each item sold on the y axis and individual products on the x axis. Mass marketers sell a few items of huge quantities each, while other companies—Amazon.com being a good example—sell only a few each of a very large number of products, which in total add up to a large quantity—the long tail of the curve. Jackson reports that NI typically uses 802.11 wireless technology and is partnering with many wireless technology companies, including Accutech, Alcatel, Crossbow, Oceania and Phoenix Contact. “We have drivers within LabView, our programming software, to each of these wireless providers with virtual instruments (software function blocks) defining each driver to make it easy for our integrator partners to develop applications. Right now, typical applications are for monitoring and communication. We aren’t always sure what our partners and integrators will do next, but we’ll have the technical foundation for them to do it.”Adds NI Senior Product Strategist Dave Potter, “Just looking at the companies that we have drivers for shows how fragmented the wireless market is right now. Different technologies fit different applications. The way we look at it, LabView provides a common interface to all of these largely proprietary networks. The benefit of 802.11 is the huge number of developers working with it, especially for security. There is growing momentum for 802.15.4 currently.” Nobuaki Konishi, general manager at Yokogawa, the big Tokyo-based automation supplier, says his company recognizes “field wireless” and WiFi. “Wifi is already established as a technology, but it assumes much power supply. It can be used with PCs (personal computers) and other handheld devices, though. ‘Field wireless’ is what we call technology at the sensor level. This requires devices in the field that require little power supply. Standardization here is still under development. Our intention for this standard is one radio and network management in order to avoid the many protocols of the wired fieldbus solutions.”Jeremy Bryant, automation marketing network specialist at supplier Siemens Energy & Automation, in Alpharetta, Ga., sees many applications for wireless in manufacturing. “Wireless networking gives ease of access to the automation system without the need to plug in. So, if you physically can’t get to a panel easily, you can still get at the information. Another application is remote monitoring and control. Some applications like airplane hanger doors require complicated cable festooning, where wireless makes much more sense.”Eric Marske, product manager for wireless modem provider Electrical Systems Technology-ESTeem, Kennowick, Wash., says, “The biggest thing in designing an application is picking which direction to go. There’s a lot of excitement around wireless right now. This is good. Ten to 15 years ago, wireless was a black box. Now there are purposes for it. Right now, the best-selling systems are in water/wastewater SCADA over long distances. Implementations have come to be based on Ethernet. There’s enough bandwidth now to add video as well.To view an exclusive Web Extra portion of this story, please click here
For more information, search keywords “wireless” and “networking” at www.automationworld.com.
suited to industrial performance clouds this promise. But there are signs that the situation is beginning to sort itself out, and now may be the ideal time for manufacturing professionals to take the deep dive into the promise of wireless.Wireless pump controlThe Coca-Cola Co. purchased a plant in southern Missouri to bottle its Dasani brand of drinking water. The facility would draw water from the nearby Roubidoux Formation—the source of some of the purest water in North America. What Coca-Cola officials didn’t know, however, was that the plant was not equipped to pump the roughly 1,000 gallons of water per minute needed to meet demand. At best, the plant would be able to pump only half that amount.Now, though, the plant is pumping more than 1,500 gallons of water per minute, thanks to a new control and data acquisition system provided by Opto 22, of Temecula, Calif. “We used Opto 22 hardware and software to build this system primarily for the sake of simplicity,” says Barrett Davis, owner of The Automate Company LLC, the Pacific, Mo., control systems integrator that designed and installed the system for Coca-Cola. “We typically build the panels for our control systems from scratch, and the Opto 22 hardware and software makes it easy to do that.”The system includes a pump on each of the three wells, each controlled by a variable frequency drive (VFD). The three drives must work in coordinated fashion to ensure that the storage tank does not overflow. “Any of the well pumps can be designated as the lead,” Davis explains. “That pump will have a set point for moving water at a certain level of pressure, say 60 psi (pounds per square inch). Once that point is set, the pump will work to provide that level of pressure to the plant at all times. The VFD works to speed the pump up or slow it down, as necessary, to keep the pressure at that level.”An Ethernet network for the system connects an OptoTerminal—the primary operator interface—and Snap Ultimate input/output (I/O) controller and I/O systems, many of which are connected to the network wirelessly. The system continually monitors pumping activity. It detects when a VFD is operating at maximum speed and can no longer make the lead pump push enough water to keep up the required level of pressure. When that happens, an additional pump is called into action. This new “lag” pump begins moving water at a preset minimum speed.“Having an Ethernet-based system and running it over a wireless network means that all of the communication takes place very quickly and efficiently,” Davis says. “When the Snap Ultimate unit sends out a request for information, the response arrives within three milliseconds, as opposed to five to 10 seconds with traditional radio telemetry equipment.” This fast response time means that the plant is always operating at maximum efficiency and never pumping too much or too little water.Possible applicationsWhile there are already SCADA and some control applications such as this one using wireless technologies, many possible applications are awaiting the outcome of standardization efforts. There are two organizations working on standards—the Hart Communications Foundation and the SP100 committee of the Instrumentation, Systems and Automation Society (ISA). Davis Mathews, regional business unit manager for interface at Phoenix Contact, a Harrisburg, Pa.-based automation supplier, reflects the opinions of many when he notes that the SP100 committee seems to be divided on technology into two groups driven by vendors Emerson Process Management and Honeywell Process Solutions, respectively.“One thing I noticed was SP100 trying to emulate the IEEE 802.11 wireless local area network,” says Mathews. “That will be popular.
We sell about $5 million per year now of 802.11 products with a proprietary-based product. But customers are looking for a standards-based product so that they can use more devices. Meanwhile, the Hart group decided to move quickly and develop its own wireless standard. It is agreeing on the IEEE 802.15.4 mesh standard for radios. In this area, technology innovation comes from suppliers, but needs to come from users. So, Hart put together a demo with products from eight suppliers for the ISA Expo (Oct. 17-19, in Houston) to enable customers to see a direction and provide feedback.”Mathews sees major customer applications starting in the sensing world. The technology is so new in manufacturing that customers are hesitant to move to continuous monitoring or control right now. “The technology’s evolving,” says Mathews. “Customers are already sending data. It’s only a matter of time before they apply wireless to other needs. Look at the evolution of wired Ethernet use.”How big could wireless networking become? Senior Analyst Harry Forbes, of ARC Advisory Group Inc., the Dedham, Mass., analyst firm, writes in a research report titled “Wireless Technology in Process Manufacturing” that the worldwide market for wireless technology for manufacturing is expected to grow at a compound annual growth rate of 26 percent over the next five years—from $325.7 million in 2005 to more than $1 billion in 2010.Sean Keeping, vice president, technology, for ABB Instrumentation, St. Neots, England, also points to the two standards under development from the process industries point of view. “Hart has been discussed for some time and is reasonably well developed. We have some prototypes for testing by the industry. It’s not something that is device vendor-proprietary, it’s an industry standard. SP100 is slightly less developed than Hart, but many key players are looking at this. These two emerging standards are likely to succeed. I think the industry does not want a device specific or vendor specific solution.”Keeping believes customers will develop confidence in the technology as the suppliers prove that the newer products are both reliable and secure. Adds Gareth Johnseon, fieldbus communications specialist at ABB, “Users are using some proprietary products now, and they are asking for more information. It’s not like when the fieldbuses came in. We’re seeing a lot of inquiries about setting up pilots or field trials.”A matter of visionWhat are the important factors that standards bodies should consider? Hesh Kagan, director, new ventures, for automation supplier Invensys Process Systems, in Foxboro, Mass., says, “The function that comes to mind most is interoperability. But that may not be most important to users. That may be coexistence—that is, will the various radios interfere with each other, be immune to lightning or other radiation and the like? Interoperability will come with a bit-level standard.”Where will wireless technologies find a home in industry? Says Kagan, “Every customer has an application that’s most important to them. I see applications like field data logging from satellites and voice over Internet (VoIP) replacing some currently used radios, perhaps adding a little remote I/O to make remote control easier. I expect to see incremental video over the network for physical plant security. Another application is the mobile operator concept with tablet PCs where an operator can still be in touch with the operation even while stepping away from the main console to check out a problem somewhere else.“Coming down the pike, I see expanded condition monitoring with low-cost sensors. It’s going to be a whole new model of doing maintenance based on those sensors and model-based predictive maintenance. The dollars that can be saved in continuous process are enormous. In the longer term, an interesting thought is to consider what happens when these low-cost condition monitors take hold. They will be very inexpensive compared to today’s process measurement. What if at some point someone takes a look and thinks, ‘That condition monitor may be good enough for process measurement.’ I may have two excellent measurements now. But there’s a lot of math being developed that would say, ‘What if I have 20 to 30 not-so-excellent measurements but I can develop a profile that would give me better information overall?’ This is at least five to seven years out, but think of the potential.”Someone else thinking long term about the philosophy of process control is John Berra, president of Emerson Process Management. He says, “Plant knowledge is the key to improving business performance. No wires means no limits. We can put more sensors in plants at a tenth of the cost with wireless technologies. More eyes and ears in the plant means added intelligence.”Products nowEmerson announced the availability of several wireless sensor products and a gateway at its Users Exchange Conference Oct. 2-4 in Nashville. The technology uses IEEE 802.15.4 mesh radios with technology from Dust Networks. Says Bob Karschnia, vice president of technology for the Rosemount division of Emerson Process, “We did three years of field trials to test out various technologies. We looked at the CDMA (code division multiple access) tree structure, which uses direct sequence spread spectrum technology built on IEEE 802.11 WiFi, but then we switched to mesh networks built on IEEE 802.15.4 with frequency hopping. It coexists with WiFi
in a plant, but doesn’t require a site survey to install nodes. Reliability of a mesh network actually increases with the number of nodes installed.”Dave Kaufman, director of integrated field solutions at Honeywell Process Systems, in Phoenix, says, “As we looked at plant requirements, we saw different classes of applications, including safety, closed loop control, open loop control and monitoring. Customers told us they wanted to do them all, and if they could go wireless, they’d like to do that. So as we looked at architectures, the question we asked ourselves was, ‘How can we do this efficiently and effectively.’ Even if customers may not go directly to control applications right away, we wanted to provide a single infrastructure to handle everything. So, we went after a robust architecture with the performance to meet all requirements.”Robert Jackson, product marketing engineer at Austin, Texas-based test and automation systems vendor National Instruments (NI), sees the current state of wireless as the market “long tail” effect, citing a book by Chris Anderson, titled “The Long Tail: Why the Future of Business is Selling Less of More.” The long tail effect describes a curve with the quantity of each item sold on the y axis and individual products on the x axis. Mass marketers sell a few items of huge quantities each, while other companies—Amazon.com being a good example—sell only a few each of a very large number of products, which in total add up to a large quantity—the long tail of the curve. Jackson reports that NI typically uses 802.11 wireless technology and is partnering with many wireless technology companies, including Accutech, Alcatel, Crossbow, Oceania and Phoenix Contact. “We have drivers within LabView, our programming software, to each of these wireless providers with virtual instruments (software function blocks) defining each driver to make it easy for our integrator partners to develop applications. Right now, typical applications are for monitoring and communication. We aren’t always sure what our partners and integrators will do next, but we’ll have the technical foundation for them to do it.”Adds NI Senior Product Strategist Dave Potter, “Just looking at the companies that we have drivers for shows how fragmented the wireless market is right now. Different technologies fit different applications. The way we look at it, LabView provides a common interface to all of these largely proprietary networks. The benefit of 802.11 is the huge number of developers working with it, especially for security. There is growing momentum for 802.15.4 currently.” Nobuaki Konishi, general manager at Yokogawa, the big Tokyo-based automation supplier, says his company recognizes “field wireless” and WiFi. “Wifi is already established as a technology, but it assumes much power supply. It can be used with PCs (personal computers) and other handheld devices, though. ‘Field wireless’ is what we call technology at the sensor level. This requires devices in the field that require little power supply. Standardization here is still under development. Our intention for this standard is one radio and network management in order to avoid the many protocols of the wired fieldbus solutions.”Jeremy Bryant, automation marketing network specialist at supplier Siemens Energy & Automation, in Alpharetta, Ga., sees many applications for wireless in manufacturing. “Wireless networking gives ease of access to the automation system without the need to plug in. So, if you physically can’t get to a panel easily, you can still get at the information. Another application is remote monitoring and control. Some applications like airplane hanger doors require complicated cable festooning, where wireless makes much more sense.”Eric Marske, product manager for wireless modem provider Electrical Systems Technology-ESTeem, Kennowick, Wash., says, “The biggest thing in designing an application is picking which direction to go. There’s a lot of excitement around wireless right now. This is good. Ten to 15 years ago, wireless was a black box. Now there are purposes for it. Right now, the best-selling systems are in water/wastewater SCADA over long distances. Implementations have come to be based on Ethernet. There’s enough bandwidth now to add video as well.To view an exclusive Web Extra portion of this story, please click here
For more information, search keywords “wireless” and “networking” at www.automationworld.com.
Sponsored Recommendations
Sponsored Recommendations
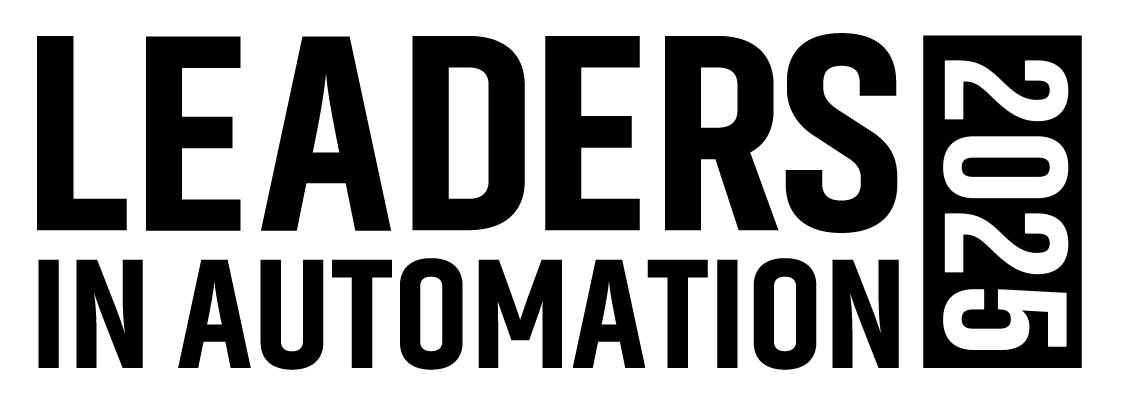
Leaders relevant to this article: