“Performance management is a myth.” Invensys/Foxboro Vice President and General Manager of Performance Management Peter Martin knows how to get your attention. By this statement, he means to shake up management and force the realization that improving manufacturing performance requires more than just buying a product. It requires using new technologies and tools while undertaking a culture change within operations to empower people in their quest to make plants more competitive and profitable.“Performance management implementations are for the most part ineffective,” says Martin from his Foxboro, Mass., office, “and the issue is mindset. Managers believe they should manage, and that operators and engineers are to be told what to do. But minute-to-minute, managers of the plant’s processes are the operators. We need to convert operators and maintenance people into performance managers. We’ve got to get over management egos. They don’t want to empower people. Why, take a look at the design of control systems. It’s an operation by exception philosophy. You only notify the operator if the process is going wrong. We train the operators to believe that if things are going well (without any alarms), then they should just read the sports section of the newspaper.”Provide the toolsMartin likens this to sending a batter to the plate in a baseball game without a bat. We have to give operators the tools to do the job, and then believe that they can do the job. The most important of those tools is information. Switching sports but carrying through with the theme, Martin likens operating a plant to coaching a team sport such as soccer. First, the team knows that the goal of the game is to win. There’s a scoreboard where everyone gets instant feedback as to their status relative to the goal. The coach develops a strategy and recruits players, then trains the players, providing the skills and information they will need to succeed. At game time, it is the responsibility of the coach to put the correct mix of players on the field to play the game. The game is won or lost, though, through the creativity, teamwork and efforts of the players. Manufacturing managers need to learn from this model and do similar things. That is, they must recruit and train personnel, put the correct people in the proper positions and provide the information they need to be successful.Despite shortfalls of the past, there are growing signs that things are changing for the better in manufacturing plants around the world, however, as leaders do try to make the modifications in technology and organization that will lead to optimum performance. Sometimes, the efforts seem a little low key, but the payoffs have been large so far—and the potential payoffs down the road as more technology develops are huge.Sometimes, you have to take basic steps to eventually reach performance excellence. One example can be seen at a medium-sized Western U.S. chemical plant that asked not to be named. The process operations supervisor at this plant describes a control system containing about 8,000 input/output (I/O) points in four operation areas. His problem was too many alarms. His four operators dealt with up to 8,000 alarms per day per operation area. The alarms came so quickly that they scrolled on the display such that the operators couldn’t even see them, let alone react. The supervisor initially started to work on the problem by assigning someone to analyze the alarms and look for root causes, with an eye toward eliminating the spurious alarms and solving the underlying problems that triggered the important ones. He discovered quickly, however, that one person working full time couldn’t make a dent in the problem, and that the budget was stretched with the extra hours.Alarm analysisWorking with Yokogawa, a process systems supplier with U.S. headquarters in Houston, the supervisor found a technology solution for his alarm problem. Yokogawa’s Advanced Alarm Administrator Suite brought order to the confusion. The software has alarm analysis tools with statistics on tags that generate the most problems. An operator can look at a display, quickly identify the problem and devise a solution. The software also has an alarm suppression function that detects if a sensor is chattering in and out of alarm, sending multiple messages, and filters the alarms displayed.“Our goal was to get the alarm total down to 288 alarms per operator per day,” says the supervisor, “and in the first 90 days, we saw an 88 percent reduction in alarms. We actually turned off the system to assure ourselves that it was really working. Our operators stay on top of things now, instead of just reacting. Now, they are actually operating the plant. Plus, the plant is operating with more stability than in the past.”Meanwhile in Saudi Arabia, Thawab Salem Al-Otaibi, an administrator at vertically integrated petroleum giant Saudi
Aramco, confirms many of the elements of performance management pointed out by others. “Since Day One with the company, I’ve been trying to combine information for users in the plant so that they can make better decisions,” states Salem. “Operators need information to open or close the correct valves. Managers need information in order to decide which units to use. But information points were not connected, making information flow impossible. So we started to investigate ways to gather all the data we needed in order to provide useful and timely information to our users.” Salem says the company eventually settled on Enterprise Monitor Solution, from IndX, a Siemens company based in Aliso Viejo, Calif., as a way to solve its problem. “For our selection process, we knew Siemens as a big company that works with Aramco. We visited an existing customer and did video conferencing with other refineries. It was easy to install, and since it’s a Web application, training is minimal.”The IndX application looks into the wealth of tag- and historical-based data existing in a company, and pulls it out, putting it into the context that managers and operators need to do their jobs better. Says Salem, “With the additional information we have, we can make more decisions better. For instance, by looking at the refinery as a whole, we can reassign craftsmen to different areas to tackle backlogs that may not have been reached the old way.” Using this additional information does mean a culture change, and some managers resist it, Salem concedes. But he notes that people who have been using the system are enthusiastic and promote the system and its benefits to their colleagues.Model maintenanceAll of the systems discussed thus far involve real-time information provided to operators and managers that allow them to make the crucial adjustments or find the critical problems to improve process stability and performance. But sometimes the information does not need to be updated that quickly, and the maintenance function works in a more future-oriented preventative way. Such is a program from Swiss-based automation vendor ABB called PM30. The service enables technicians to work with
quality, reliability and maintenance personnel at client sites to collect asset data, analyze this data in a model and send reports and schedules to the clients, allowing them to perform optimum preventative maintenance. Feedback from the clients on work done, downtime and reasons for that downtime goes back into the model for consideration in future schedules.Pat Macary is quality assurance manager at the Apollo Beach, Fla., wallboard manufacturing plant of National Gypsum. “Our goal was to reduce downtime through improved preventative maintenance on our equipment assets. It is not easy to track things that don’t happen, but the results that we have so far with the project have been encouraging,” reports Macary. “The ABB technician walked the plant with us to identify key components that need preventative maintenance—things like bearings that need to be greased and the like. They compiled a list and put it in their system. Now, each week we receive about 200 to 250 ‘green sheets’ that list all the equipment that requires preventative maintenance. We distribute those among the appropriate operations or maintenance personnel for them to perform during the week. We keep track of breakdowns and repairs with costs associated with them and feed that back into the system, along with reports of work done.”Macary receives reports from the system that consolidates the work done and cost information for tracking purposes. Because this is work that is future-oriented and not just fixing something that’s broken, it requires a discipline. Macary notes, “You get as many benefits from the system as the effort you put into it.” Even this system requires a culture change. Maintenance managers sometimes are offended by the idea, thinking they are being told that they are not doing their jobs. They have to be shown that this is just another tool for them to use to keep the plant performing at its best.There is another batch-type preventative maintenance system used to provide asset condition information aimed at timely equipment repairs. Kevin Harper, principal reliability engineer at the AtlanticLNG liquefied natural gas plant in Trinidad, says the AMS performance management monitoring service from Emerson Process Management, Austin, Texas, helps him plan maintenance of the factory’s assets during planned downtimes. The AMS service is a Web-based condition monitoring system in which data is collected on specified assets from the distributed control system, and then sent to Emerson in two-week batches. Emerson analyzes the data and prepares reports that are loaded on a secure server viewable on the Web to those with role-based permissions.Check critical assetsHarper says he started with four critical assets—two refrigeration compressors and two main generators. “The system helps identify which assets need intrusive maintenance during planned shutdowns. The reliability department analyzes information from the condition monitoring system and recommends equipment repairs,” Harper explains. “We look for abnormalities, trends and symptoms of degrading performance.” The AMS system was implemented in early 2005, so the plant has gone through only one scheduled downtime with the system in place, Harper says. But he notes that the Emerson technology did identify a compressor that needed more repair than first thought. While the incremental gain in production was not substantial, the result was positive, Harper observes. “And now that we have a feel for the system, we’re confident enough that we’re adding about 40 assets per year to the system.”Even companies that specialize in developing model predictive control are developing performance management solutions. Dave Cooper, chief technology officer of Austin-based Pavilion Technologies says that his company is developing solutions to help achieve not just performance management, but is also providing solutions that improve value for customers by applying models of processes or predictive information. For example, the Canpac division of Fonterra, the largest dairy products company in New Zealand, wants to understand inefficiencies and wastage in its packaging plants, as a way to improve plant performance. Using Pavilion technology, Canpac is relying on metrics including operating equipment effectiveness (OEE), uptimes, changeover times, production efficiencies and waste, as a way to perform root cause analysis. The ultimate goal is to develop a model that can be used to adjust operations to achieve operating goals. There has been a 5 percent improvement to date.Matt Giordano, business consultant at automation vendor Rockwell Automation Inc., in Milwaukee, agrees that OEE and production efficiency are key metrics for understanding and improving manufacturing performance. “There are a number of solutions coming out right now to help companies improve performance,” says Giordano. “We have found that customers want a solution that looks like a Microsoft Office solution. They are already familiar with Office—typically when you go in a plant to consult with the engineers, they hand you a bunch of printouts from Excel spreadsheets.” As a result, says Giordano,Rockwell is moving to Microsoft Reporting Services. This solution is Web based and allows users to jump immediately to the production line that is underperforming and drill down to the problem area. Six Sigma or Continuous Improvement team members can pull data for use in projects quickly and with confidence in its accuracy, Giordano points out. “This cuts time for those projects, allowing the teams to tackle more projects in a given time period and therefore dramatically increase savings.”Visibilty neededChris Boothroyd, senior product manager at Honeywell Process Solutions, in Phoenix, notes two aspects to performance management tools—visibility of key performance indicators (KPIs), and general access to information in real time from a single access point. “People need to spend time deciding, not looking for data,” Boothroyd observes. “For example, say a corporate vice president looking at his enterprise resource planning (ERP) system sees a problem at a plant. He sends an e-mail message to the plant manager questioning why the process is off target. But the plant manager may not see the same KPI or have access to the same set of information. And often, the ERP data is too old for the plant manager to take corrective action. The plant manager needs the ability to drill down from the corporate KPI and decompose the data in order to get into the details of the process driving the problem.” Boothroyd points out that manufacturing personnel also have a need to understand the impact of their actions on the relevant KPIs. “Companies are just starting to implement that,” he says. “That’s why we provide tools for our customers to get information that’s out there in the plant, analyze for root cause and feedback into relevant KPIs.” A key element of performance management software tools is not just gathering bunches of data, but in providing analysis and correlation functions. Kevin Tock, vice president of production performance management at Invensys/Wonderware, a Lake Forest, Calif., automation supplier, says, “Performance management software benefits manufacturers through better visibility into reasons for downtime or the ability to relate quality issues to other events in the plant. When you compile data into a SQL database you can run data correlations and find causes of problems that you would never suspect otherwise.”Tock sees a lot of interest from companies that have completed their ERP implementations and now wish to connect the plant system to the enterprise system in order to finally realize the promise of ERP. But when it comes to meeting with customers to present solutions, there is often an internal problem within the customer company. “The reality is that information technology (IT) people at the business systems level of the company and the manufacturing people seldom know each other,” notes Tock. “When they start to discuss tying things together, they end up discovering a disconnect between what information is available at the factory level and what is needed by the corporate system.”A final example shows the benefits possible when a manufacturing team—including IT—uses a good information system to dramatically improve performance.The Gallo Glass plant in Modesto, Calif., manufactures more than 100 different combinations of bottle shapes, sizes and colors. “The primary goal of the glass plant is to maintain a steady, reliable and high quality supply of bottles for the E. & J. Gallo Winery,” explains George White, information systems manager at Gallo Glass Co. “What we make at the glass plant today gets used tomorrow in bottling and labeling.”The plant’s automated Shop Floor Information System (SFIS) is iFIX software from GE Fanuc Automation, a Charlottesville, Va-based unit of GE Infrastructure. This information system collects and presents data from all steps in bottle making. The system serves multiple users at Gallo Glass—from operators on the lines to maintenance managers to senior managers who need quick, graphical reports via the Web. Informed decisions“Our automation started with sensing and inspection devices, and from there, we needed a way to collect production data to allow us to make more informed decisions,” White says. “It was critical to implement one interface package and have everyone in the plant operating from the same page and sharing information.”Observing the value of getting operators into the performance team, Bruce Williams, senior production manager at Gallo Glass, says, “SFIS has brought all of my production managers together onto the playing field.”Troy Wells, director of maintenance and engineering, notes, “The Gallo SFIS system has transformed us from a ‘make and inspect’ mentality to a ‘make, measure, and improve’ mentality. This change continually drives us back to the manufacturing process for root cause analysis and correction. SFIS drives us to ‘make it right the first time,’ and this system never ceases to amaze me with its ability to constantly receive and update information that is vital to the production process.”Benefits accrued to the plant by using a rich information source include $5 million in annual savings through improved quality, production increases of 5 percent, a 25 percent reduction in defects, reduction in plant downtime by 25 percent, an 80 percent decrease in furnace emissions and an observed reduction in training time.
Aramco, confirms many of the elements of performance management pointed out by others. “Since Day One with the company, I’ve been trying to combine information for users in the plant so that they can make better decisions,” states Salem. “Operators need information to open or close the correct valves. Managers need information in order to decide which units to use. But information points were not connected, making information flow impossible. So we started to investigate ways to gather all the data we needed in order to provide useful and timely information to our users.” Salem says the company eventually settled on Enterprise Monitor Solution, from IndX, a Siemens company based in Aliso Viejo, Calif., as a way to solve its problem. “For our selection process, we knew Siemens as a big company that works with Aramco. We visited an existing customer and did video conferencing with other refineries. It was easy to install, and since it’s a Web application, training is minimal.”The IndX application looks into the wealth of tag- and historical-based data existing in a company, and pulls it out, putting it into the context that managers and operators need to do their jobs better. Says Salem, “With the additional information we have, we can make more decisions better. For instance, by looking at the refinery as a whole, we can reassign craftsmen to different areas to tackle backlogs that may not have been reached the old way.” Using this additional information does mean a culture change, and some managers resist it, Salem concedes. But he notes that people who have been using the system are enthusiastic and promote the system and its benefits to their colleagues.Model maintenanceAll of the systems discussed thus far involve real-time information provided to operators and managers that allow them to make the crucial adjustments or find the critical problems to improve process stability and performance. But sometimes the information does not need to be updated that quickly, and the maintenance function works in a more future-oriented preventative way. Such is a program from Swiss-based automation vendor ABB called PM30. The service enables technicians to work with
quality, reliability and maintenance personnel at client sites to collect asset data, analyze this data in a model and send reports and schedules to the clients, allowing them to perform optimum preventative maintenance. Feedback from the clients on work done, downtime and reasons for that downtime goes back into the model for consideration in future schedules.Pat Macary is quality assurance manager at the Apollo Beach, Fla., wallboard manufacturing plant of National Gypsum. “Our goal was to reduce downtime through improved preventative maintenance on our equipment assets. It is not easy to track things that don’t happen, but the results that we have so far with the project have been encouraging,” reports Macary. “The ABB technician walked the plant with us to identify key components that need preventative maintenance—things like bearings that need to be greased and the like. They compiled a list and put it in their system. Now, each week we receive about 200 to 250 ‘green sheets’ that list all the equipment that requires preventative maintenance. We distribute those among the appropriate operations or maintenance personnel for them to perform during the week. We keep track of breakdowns and repairs with costs associated with them and feed that back into the system, along with reports of work done.”Macary receives reports from the system that consolidates the work done and cost information for tracking purposes. Because this is work that is future-oriented and not just fixing something that’s broken, it requires a discipline. Macary notes, “You get as many benefits from the system as the effort you put into it.” Even this system requires a culture change. Maintenance managers sometimes are offended by the idea, thinking they are being told that they are not doing their jobs. They have to be shown that this is just another tool for them to use to keep the plant performing at its best.There is another batch-type preventative maintenance system used to provide asset condition information aimed at timely equipment repairs. Kevin Harper, principal reliability engineer at the AtlanticLNG liquefied natural gas plant in Trinidad, says the AMS performance management monitoring service from Emerson Process Management, Austin, Texas, helps him plan maintenance of the factory’s assets during planned downtimes. The AMS service is a Web-based condition monitoring system in which data is collected on specified assets from the distributed control system, and then sent to Emerson in two-week batches. Emerson analyzes the data and prepares reports that are loaded on a secure server viewable on the Web to those with role-based permissions.Check critical assetsHarper says he started with four critical assets—two refrigeration compressors and two main generators. “The system helps identify which assets need intrusive maintenance during planned shutdowns. The reliability department analyzes information from the condition monitoring system and recommends equipment repairs,” Harper explains. “We look for abnormalities, trends and symptoms of degrading performance.” The AMS system was implemented in early 2005, so the plant has gone through only one scheduled downtime with the system in place, Harper says. But he notes that the Emerson technology did identify a compressor that needed more repair than first thought. While the incremental gain in production was not substantial, the result was positive, Harper observes. “And now that we have a feel for the system, we’re confident enough that we’re adding about 40 assets per year to the system.”Even companies that specialize in developing model predictive control are developing performance management solutions. Dave Cooper, chief technology officer of Austin-based Pavilion Technologies says that his company is developing solutions to help achieve not just performance management, but is also providing solutions that improve value for customers by applying models of processes or predictive information. For example, the Canpac division of Fonterra, the largest dairy products company in New Zealand, wants to understand inefficiencies and wastage in its packaging plants, as a way to improve plant performance. Using Pavilion technology, Canpac is relying on metrics including operating equipment effectiveness (OEE), uptimes, changeover times, production efficiencies and waste, as a way to perform root cause analysis. The ultimate goal is to develop a model that can be used to adjust operations to achieve operating goals. There has been a 5 percent improvement to date.Matt Giordano, business consultant at automation vendor Rockwell Automation Inc., in Milwaukee, agrees that OEE and production efficiency are key metrics for understanding and improving manufacturing performance. “There are a number of solutions coming out right now to help companies improve performance,” says Giordano. “We have found that customers want a solution that looks like a Microsoft Office solution. They are already familiar with Office—typically when you go in a plant to consult with the engineers, they hand you a bunch of printouts from Excel spreadsheets.” As a result, says Giordano,Rockwell is moving to Microsoft Reporting Services. This solution is Web based and allows users to jump immediately to the production line that is underperforming and drill down to the problem area. Six Sigma or Continuous Improvement team members can pull data for use in projects quickly and with confidence in its accuracy, Giordano points out. “This cuts time for those projects, allowing the teams to tackle more projects in a given time period and therefore dramatically increase savings.”Visibilty neededChris Boothroyd, senior product manager at Honeywell Process Solutions, in Phoenix, notes two aspects to performance management tools—visibility of key performance indicators (KPIs), and general access to information in real time from a single access point. “People need to spend time deciding, not looking for data,” Boothroyd observes. “For example, say a corporate vice president looking at his enterprise resource planning (ERP) system sees a problem at a plant. He sends an e-mail message to the plant manager questioning why the process is off target. But the plant manager may not see the same KPI or have access to the same set of information. And often, the ERP data is too old for the plant manager to take corrective action. The plant manager needs the ability to drill down from the corporate KPI and decompose the data in order to get into the details of the process driving the problem.” Boothroyd points out that manufacturing personnel also have a need to understand the impact of their actions on the relevant KPIs. “Companies are just starting to implement that,” he says. “That’s why we provide tools for our customers to get information that’s out there in the plant, analyze for root cause and feedback into relevant KPIs.” A key element of performance management software tools is not just gathering bunches of data, but in providing analysis and correlation functions. Kevin Tock, vice president of production performance management at Invensys/Wonderware, a Lake Forest, Calif., automation supplier, says, “Performance management software benefits manufacturers through better visibility into reasons for downtime or the ability to relate quality issues to other events in the plant. When you compile data into a SQL database you can run data correlations and find causes of problems that you would never suspect otherwise.”Tock sees a lot of interest from companies that have completed their ERP implementations and now wish to connect the plant system to the enterprise system in order to finally realize the promise of ERP. But when it comes to meeting with customers to present solutions, there is often an internal problem within the customer company. “The reality is that information technology (IT) people at the business systems level of the company and the manufacturing people seldom know each other,” notes Tock. “When they start to discuss tying things together, they end up discovering a disconnect between what information is available at the factory level and what is needed by the corporate system.”A final example shows the benefits possible when a manufacturing team—including IT—uses a good information system to dramatically improve performance.The Gallo Glass plant in Modesto, Calif., manufactures more than 100 different combinations of bottle shapes, sizes and colors. “The primary goal of the glass plant is to maintain a steady, reliable and high quality supply of bottles for the E. & J. Gallo Winery,” explains George White, information systems manager at Gallo Glass Co. “What we make at the glass plant today gets used tomorrow in bottling and labeling.”The plant’s automated Shop Floor Information System (SFIS) is iFIX software from GE Fanuc Automation, a Charlottesville, Va-based unit of GE Infrastructure. This information system collects and presents data from all steps in bottle making. The system serves multiple users at Gallo Glass—from operators on the lines to maintenance managers to senior managers who need quick, graphical reports via the Web. Informed decisions“Our automation started with sensing and inspection devices, and from there, we needed a way to collect production data to allow us to make more informed decisions,” White says. “It was critical to implement one interface package and have everyone in the plant operating from the same page and sharing information.”Observing the value of getting operators into the performance team, Bruce Williams, senior production manager at Gallo Glass, says, “SFIS has brought all of my production managers together onto the playing field.”Troy Wells, director of maintenance and engineering, notes, “The Gallo SFIS system has transformed us from a ‘make and inspect’ mentality to a ‘make, measure, and improve’ mentality. This change continually drives us back to the manufacturing process for root cause analysis and correction. SFIS drives us to ‘make it right the first time,’ and this system never ceases to amaze me with its ability to constantly receive and update information that is vital to the production process.”Benefits accrued to the plant by using a rich information source include $5 million in annual savings through improved quality, production increases of 5 percent, a 25 percent reduction in defects, reduction in plant downtime by 25 percent, an 80 percent decrease in furnace emissions and an observed reduction in training time.
Sponsored Recommendations
Sponsored Recommendations
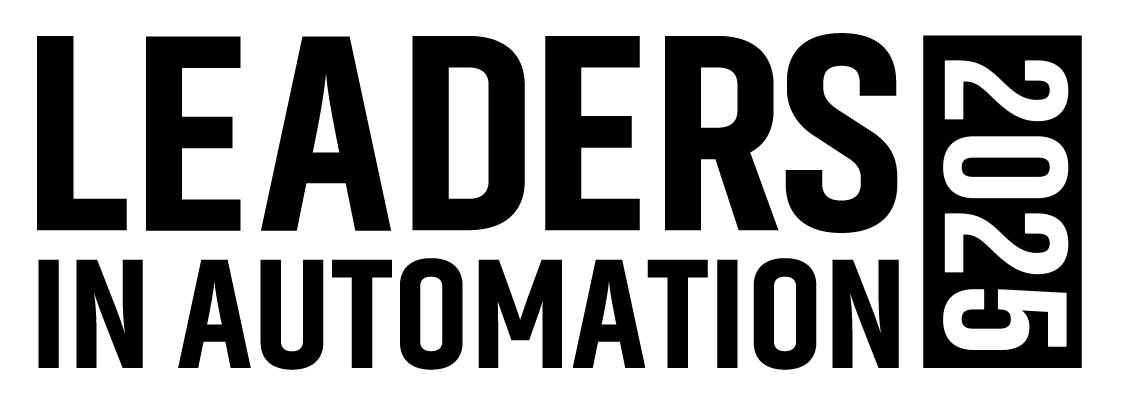
Leaders relevant to this article: