When it comes to controls integration and automation, what progress are the builders and buyers of packaging machinery making these days? Packaging World and OMAC, the Open Modular Architecture Control users group, teamed up on a survey recently to find out. These were among the key findings:Data collection on packaging lines is seldom practicedSome progress is being made in getting packaging lines networkedLess than 25 percent of packaging machinery buyers specify OMAC guidelines on new equipment l Integrating packaging lines with enterprise resource planning (ERP) systems is a subject of
considerable interest among packaged goods manufacturers, even though not many currently have such a connection.In a presentation at the May 24 Packaging Automation Forum in Chicago—sponsored by Packaging World and Automation World
magazines—Dave Bauman, OMAC Technical Director, shared the survey results. Subsequently, Bauman agreed to join Packaging World in a conference call with several packaging machinery builders and buyers (see sidebar list of participants) to gauge their response to the survey. This story is essentially their reaction to key survey results.We begin with Chart 1, which shows how many end users specify OMAC packaging guidelines on the machines they buy. These guidelines, in a nutshell, are aimed at establishing naming conventions and tags for machine states—aborted, running, stopped, jammed, and others—that all programmers in the packaging machinery space can agree upon as standards. Among large companies—annual revenue of more than $1 billion—25.6 percent said they do specify OMAC packaging guidelines in the machines they buy. Among respondents overall, the number was 20.1 percent.“I don’t think enough people know about OMAC packaging guidelines,” says Adco’s Kevin Gilpin.“I was surprised at the numbers,” says R.A. Jones’ Darren Elliott. “I think it becomes an education issue, really. We recently had a machine checkout meeting with an end-user from South Africa, and when we asked if they were familiar with OMAC or any of the advantages it might offer, they hadn’t even heard of it. When we explained it to them, they were on board with the message right away, but it was just one of those things they didn’t know was a resource for them.”“It’s going to take a lot of repetition before the end-users start buying into it,” says Colin Warnes of Adco. “But in time, I think it will become commonplace. One of the biggest advantages OMAC guidelines offer is the ability to communicate upstream and downstream on a packaging line. If my machine is able to participate in that kind of ‘conversation,’ it becomes a significant benefit if the machine is going into a line where the case packer, wrapper, labeler, and conveyor are all from different machinery makers. If all these machines can speak with a common voice, it can help increase efficiency, reduce training time, and reduce time spent on startups.”Bringing this “common voice” to disparate pieces of packaging machinery from multiple machinery vendors would also mean end- users wouldn’t need in-house “specialists” for practically each packaging machine, notes Gilpin. “If the OMAC guidelines are followed, the programming should be fairly similar from machine to machine,” he says. In other words, one “specialist” fits all.“I think the other thing that’s coming up in the next couple of years that will make the adoption of OMAC guidelines even more valuable is something that’s coming from the IT (information technology) world,” says Elliott. “It’s the growing emphasis on being able to pipe information up from the packaging machines on the plant floor to the MES layer so that real-time production data can be tracked and managed. For the most part, OMAC guidelines and standards have been positioned as tools that bring greater connectivity from machine to machine. But the IT folks out there are developing system architectures that will increasingly seek out real-time information from the plant floor that can help packaged goods companies meet demand signals from the marketplace without building up costly and unnecessary inventory.” A greater reliance on standards like those promulgated by OMAC, says Elliott, can only help where this kind of information flow is concerned.Warnes sees another value inherent in OMAC standards and guidelines that could become increasingly important in the near future. He foresees a day when packaged goods companies will grant original equipment manufacturers (OEMs) Ethernet access to plant floor machines. “If they give us an IP address on their Ethernet network, we can access our machine in their plant to see how it’s performing,” says Warnes. “If the data is collected according to tags and naming conventions widely agreed upon in the OMAC guidelines, it will be easier for us to monitor our machine and provide help if, say, a servo motor or drive is giving us irregular feedback. We’ll be able to call the end-user and say, hey, have you guys noticed this irregularity?”Elliott agrees that the OMAC standards could play a key role in facilitating this kind of remote, Web-based troubleshooting. But he emphasizes that for now, at least, such access is practically unheard of.“Very few customers request a remote monitoring feature on equipment they buy from us,” says Elliott. “The reason is
basically two-fold. First, they don’t want to grant access to anybody that can tinker around with their proprietary information. And second, their IT folks are afraid of viruses or hackers or other intruders who might cause trouble if the network is accessible. It’s unfortunate, because it amounts to shutting the door on any feedback that might go to the machinery OEMs on how their machines or lines are performing.”Controls providersSurvey respondents who are OEMs were asked if their end-user customers dictate which controls provider should be used. As Chart 2 shows, 56 percent said less than 25 percent of their customers specify a controls supplier. At the other end of the spectrum, only 8.3 percent said more than 75 percent of their customers specify a controls supplier. R.A. Jones’ Elliott says his recent experience reflects these results, but he observes that it wasn’t always so.“Five years ago, because the end-users were pretty rigid about the controls platforms they prefer, we had 12 different controls suppliers on our machines,” says Elliott. “Now we’re down to two, which results in a number of benefits. One is that we can partner up with our technology suppliers a lot better. We don’t have to be knowledgeable about multiple platforms, which lets us get very, very good at the two platforms we use. It also means getting machines to our customers more quickly because of that partnership we have with our controls technology provider. They’ve become an integral part of how we build our equipment.”Adco’s Warnes agrees. “Having a strong partnership with one or two controls providers puts our engineers in a better position to train our customers in the use of our equipment,” says Warnes. “If a customer requests a controls architecture outside of what we’ve more or less standardized on, not only would there be an upcharge for implementing the change in the first place. We’d also have to send our engineers for a certain amount of training in the new architecture.”What about ERP?The response to a question about ERP is captured in Chart 3.“Predictably enough, more large companies have ERP/packaging line integration,” says OMAC’s Bauman. “But I think there is a growing recognition at all levels that this kind of integration can have some real benefits. The problem is that it’s a tough nut to crack. Figuring out what data needs to be captured and then how to communicate it up and down is not easy.”Frito-Lay is among the companies that are working at packaging line/ERP integration, says Richard Van Dyke, of Frito-Lay.“You need a lot of accurate data to bring about that kind of integration,” says Van Dyke. “What we’re looking at is a complete network system that would start with data collection and then lead seamlessly to ERP. But we have a lot of plants and a lot of lines. Integrating new machines and new lines in an enterprise-wide network is one thing. But what do you do with some of the older lines?”Further complicating the task of integrating ERP with packaging line activity, says Van Dyke, is that packaging, unlike processing, has not been thought of as a system.“In processing, all the controls are integrated,” says Van Dyke. “They’re tied to a common operator interface, and it’s controlled as a system. But as soon as you go into the packaging room, you see right away that it has never really been thought of as a system.”OMAC’s Bauman sees another hurdle in any packaged goods company’s attempts to integrate ERP and packaging.“It requires the involvement of both IT and engineering,” says Bauman. “I continue to be amazed at how high the walls between these two groups can be. They have different priorities that seem to prevent them from seeing eye to eye.”Adco’s Warnes sees the same IT/engineering impasse, but he thinks the realities of modern day manufacturing may bring a change.“Packaged goods companies are looking for anything they can possibly do to improve uptime and efficiency,” says Warnes. “We as machinery manufacturers are becoming more software-oriented, more data-centric, to help them in this quest for improved efficiency. As it becomes increasingly apparent that getting a better handle on data is a key to better efficiency, that’s where IT and engineering are going to begin seeing eye to eye. Because they’ll both see how their combined efforts in communicating data can boost efficiency.”Progress notedChart 4 shows end-users’ response to a question about the extent to which their packaging lines are networked. While large companies showed a greater tendency to be networked, still, about 60 percent of respondents indicated that machines within their packaging lines are not connected control-wise. While OMAC’s Bauman finds this a bit discouraging, he does see a hint of progress.“Compared to a Packaging World survey published in 2002, the percentage of companies that are networked has doubled,” observes Bauman.One question in the survey asked respondents to rank a number of desired capabilities in order of their importance. Both machine builders and buyers tended to agree on the following two capabilities as most important:Ability for maintenance technicians to maintain and diagnose controls systems regardless of system vendor.Ability to access machine diagnostic data.Among the capabilities that didn’t rank very high in importance was this one:
Ability to create applications from a library of reusable software modules. Procter & Gamble’s Mike Lamping predicts that this will become more important in the future.“Creating applications from a library of reusable modules will lead to less downtime and less time spent troubleshooting,” says Lamping. “Because if you have blocks of code that don’t require troubleshooting, people will spend time troubleshooting machine performance instead of troubleshooting code. The code will pinpoint where the machine is in need of troubleshooting.“Also, from a training perspective, you won’t have to train people on rungs, so to speak. You’ll be able to train them on machine functionality, like how the infeed section is supposed to work, for example. You can point them to the function block that controls that infeed so they can see what’s going in and what’s going out, and you won’t have to go inside that code anymore. An unwind is another example. If I want an unwind, I pull the unwind module out of the library and I’m done. No need for writing code.”Two closing thoughts about the survey come from P&G’s Lamping and OMAC’s Bauman.“What leaps out at me is that both builders and buyers of packaging equipment are looking for some kind of common look and feel in the control interface,” says Lamping. “And that’s something that OMAC-driven standards can bring about once they are more widely adopted by OEMs and end-users alike. As for machine builders, they want to focus on innovation, not on controllers or programming languages. They want to be recognized as the most innovative in their field.”“My key takeaway from the survey is that a lot of end-users just aren’t taking advantage of data acquisition and the kind of enterprise integration that it can bring,” says Bauman. “I see that as one big missed opportunity.” {mosimage}
considerable interest among packaged goods manufacturers, even though not many currently have such a connection.In a presentation at the May 24 Packaging Automation Forum in Chicago—sponsored by Packaging World and Automation World
magazines—Dave Bauman, OMAC Technical Director, shared the survey results. Subsequently, Bauman agreed to join Packaging World in a conference call with several packaging machinery builders and buyers (see sidebar list of participants) to gauge their response to the survey. This story is essentially their reaction to key survey results.We begin with Chart 1, which shows how many end users specify OMAC packaging guidelines on the machines they buy. These guidelines, in a nutshell, are aimed at establishing naming conventions and tags for machine states—aborted, running, stopped, jammed, and others—that all programmers in the packaging machinery space can agree upon as standards. Among large companies—annual revenue of more than $1 billion—25.6 percent said they do specify OMAC packaging guidelines in the machines they buy. Among respondents overall, the number was 20.1 percent.“I don’t think enough people know about OMAC packaging guidelines,” says Adco’s Kevin Gilpin.“I was surprised at the numbers,” says R.A. Jones’ Darren Elliott. “I think it becomes an education issue, really. We recently had a machine checkout meeting with an end-user from South Africa, and when we asked if they were familiar with OMAC or any of the advantages it might offer, they hadn’t even heard of it. When we explained it to them, they were on board with the message right away, but it was just one of those things they didn’t know was a resource for them.”“It’s going to take a lot of repetition before the end-users start buying into it,” says Colin Warnes of Adco. “But in time, I think it will become commonplace. One of the biggest advantages OMAC guidelines offer is the ability to communicate upstream and downstream on a packaging line. If my machine is able to participate in that kind of ‘conversation,’ it becomes a significant benefit if the machine is going into a line where the case packer, wrapper, labeler, and conveyor are all from different machinery makers. If all these machines can speak with a common voice, it can help increase efficiency, reduce training time, and reduce time spent on startups.”Bringing this “common voice” to disparate pieces of packaging machinery from multiple machinery vendors would also mean end- users wouldn’t need in-house “specialists” for practically each packaging machine, notes Gilpin. “If the OMAC guidelines are followed, the programming should be fairly similar from machine to machine,” he says. In other words, one “specialist” fits all.“I think the other thing that’s coming up in the next couple of years that will make the adoption of OMAC guidelines even more valuable is something that’s coming from the IT (information technology) world,” says Elliott. “It’s the growing emphasis on being able to pipe information up from the packaging machines on the plant floor to the MES layer so that real-time production data can be tracked and managed. For the most part, OMAC guidelines and standards have been positioned as tools that bring greater connectivity from machine to machine. But the IT folks out there are developing system architectures that will increasingly seek out real-time information from the plant floor that can help packaged goods companies meet demand signals from the marketplace without building up costly and unnecessary inventory.” A greater reliance on standards like those promulgated by OMAC, says Elliott, can only help where this kind of information flow is concerned.Warnes sees another value inherent in OMAC standards and guidelines that could become increasingly important in the near future. He foresees a day when packaged goods companies will grant original equipment manufacturers (OEMs) Ethernet access to plant floor machines. “If they give us an IP address on their Ethernet network, we can access our machine in their plant to see how it’s performing,” says Warnes. “If the data is collected according to tags and naming conventions widely agreed upon in the OMAC guidelines, it will be easier for us to monitor our machine and provide help if, say, a servo motor or drive is giving us irregular feedback. We’ll be able to call the end-user and say, hey, have you guys noticed this irregularity?”Elliott agrees that the OMAC standards could play a key role in facilitating this kind of remote, Web-based troubleshooting. But he emphasizes that for now, at least, such access is practically unheard of.“Very few customers request a remote monitoring feature on equipment they buy from us,” says Elliott. “The reason is
basically two-fold. First, they don’t want to grant access to anybody that can tinker around with their proprietary information. And second, their IT folks are afraid of viruses or hackers or other intruders who might cause trouble if the network is accessible. It’s unfortunate, because it amounts to shutting the door on any feedback that might go to the machinery OEMs on how their machines or lines are performing.”Controls providersSurvey respondents who are OEMs were asked if their end-user customers dictate which controls provider should be used. As Chart 2 shows, 56 percent said less than 25 percent of their customers specify a controls supplier. At the other end of the spectrum, only 8.3 percent said more than 75 percent of their customers specify a controls supplier. R.A. Jones’ Elliott says his recent experience reflects these results, but he observes that it wasn’t always so.“Five years ago, because the end-users were pretty rigid about the controls platforms they prefer, we had 12 different controls suppliers on our machines,” says Elliott. “Now we’re down to two, which results in a number of benefits. One is that we can partner up with our technology suppliers a lot better. We don’t have to be knowledgeable about multiple platforms, which lets us get very, very good at the two platforms we use. It also means getting machines to our customers more quickly because of that partnership we have with our controls technology provider. They’ve become an integral part of how we build our equipment.”Adco’s Warnes agrees. “Having a strong partnership with one or two controls providers puts our engineers in a better position to train our customers in the use of our equipment,” says Warnes. “If a customer requests a controls architecture outside of what we’ve more or less standardized on, not only would there be an upcharge for implementing the change in the first place. We’d also have to send our engineers for a certain amount of training in the new architecture.”What about ERP?The response to a question about ERP is captured in Chart 3.“Predictably enough, more large companies have ERP/packaging line integration,” says OMAC’s Bauman. “But I think there is a growing recognition at all levels that this kind of integration can have some real benefits. The problem is that it’s a tough nut to crack. Figuring out what data needs to be captured and then how to communicate it up and down is not easy.”Frito-Lay is among the companies that are working at packaging line/ERP integration, says Richard Van Dyke, of Frito-Lay.“You need a lot of accurate data to bring about that kind of integration,” says Van Dyke. “What we’re looking at is a complete network system that would start with data collection and then lead seamlessly to ERP. But we have a lot of plants and a lot of lines. Integrating new machines and new lines in an enterprise-wide network is one thing. But what do you do with some of the older lines?”Further complicating the task of integrating ERP with packaging line activity, says Van Dyke, is that packaging, unlike processing, has not been thought of as a system.“In processing, all the controls are integrated,” says Van Dyke. “They’re tied to a common operator interface, and it’s controlled as a system. But as soon as you go into the packaging room, you see right away that it has never really been thought of as a system.”OMAC’s Bauman sees another hurdle in any packaged goods company’s attempts to integrate ERP and packaging.“It requires the involvement of both IT and engineering,” says Bauman. “I continue to be amazed at how high the walls between these two groups can be. They have different priorities that seem to prevent them from seeing eye to eye.”Adco’s Warnes sees the same IT/engineering impasse, but he thinks the realities of modern day manufacturing may bring a change.“Packaged goods companies are looking for anything they can possibly do to improve uptime and efficiency,” says Warnes. “We as machinery manufacturers are becoming more software-oriented, more data-centric, to help them in this quest for improved efficiency. As it becomes increasingly apparent that getting a better handle on data is a key to better efficiency, that’s where IT and engineering are going to begin seeing eye to eye. Because they’ll both see how their combined efforts in communicating data can boost efficiency.”Progress notedChart 4 shows end-users’ response to a question about the extent to which their packaging lines are networked. While large companies showed a greater tendency to be networked, still, about 60 percent of respondents indicated that machines within their packaging lines are not connected control-wise. While OMAC’s Bauman finds this a bit discouraging, he does see a hint of progress.“Compared to a Packaging World survey published in 2002, the percentage of companies that are networked has doubled,” observes Bauman.One question in the survey asked respondents to rank a number of desired capabilities in order of their importance. Both machine builders and buyers tended to agree on the following two capabilities as most important:Ability for maintenance technicians to maintain and diagnose controls systems regardless of system vendor.Ability to access machine diagnostic data.Among the capabilities that didn’t rank very high in importance was this one:
Ability to create applications from a library of reusable software modules. Procter & Gamble’s Mike Lamping predicts that this will become more important in the future.“Creating applications from a library of reusable modules will lead to less downtime and less time spent troubleshooting,” says Lamping. “Because if you have blocks of code that don’t require troubleshooting, people will spend time troubleshooting machine performance instead of troubleshooting code. The code will pinpoint where the machine is in need of troubleshooting.“Also, from a training perspective, you won’t have to train people on rungs, so to speak. You’ll be able to train them on machine functionality, like how the infeed section is supposed to work, for example. You can point them to the function block that controls that infeed so they can see what’s going in and what’s going out, and you won’t have to go inside that code anymore. An unwind is another example. If I want an unwind, I pull the unwind module out of the library and I’m done. No need for writing code.”Two closing thoughts about the survey come from P&G’s Lamping and OMAC’s Bauman.“What leaps out at me is that both builders and buyers of packaging equipment are looking for some kind of common look and feel in the control interface,” says Lamping. “And that’s something that OMAC-driven standards can bring about once they are more widely adopted by OEMs and end-users alike. As for machine builders, they want to focus on innovation, not on controllers or programming languages. They want to be recognized as the most innovative in their field.”“My key takeaway from the survey is that a lot of end-users just aren’t taking advantage of data acquisition and the kind of enterprise integration that it can bring,” says Bauman. “I see that as one big missed opportunity.” {mosimage}
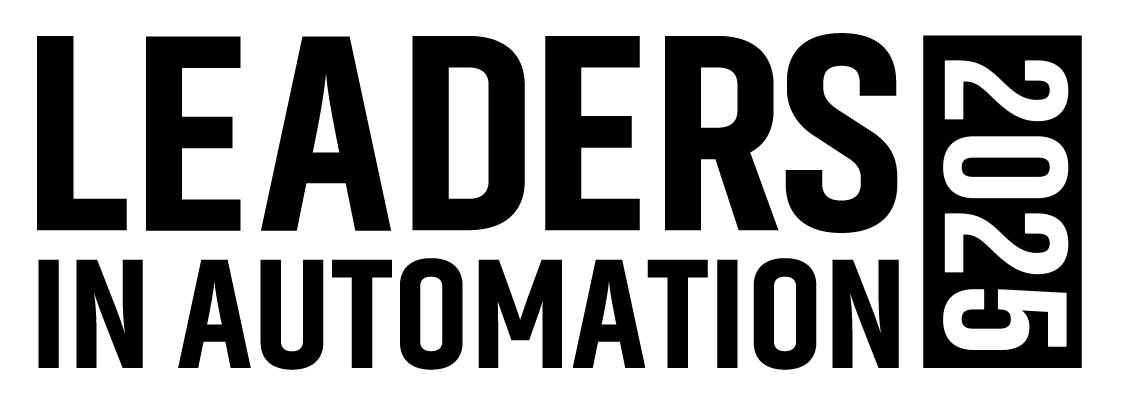
Leaders relevant to this article: