The intelligent positioners are vital to controlling the quality of the PET pellets made at Wellman’s Pearl River plant in Mississippi. They regulate the introduction and, hence, interaction of purified terephthalate acid (PTA) and monoethylene glycol (MEG), the two main reagents, in the reactors. Consistency is critical because final product is a flexible, clear plastic that is fast becoming the preferred packaging material for beverages and other fluids. Not only must the plastic have the specified strength, but it also must look good.
“Controlling the injection of PTA and MEG, from a small trickle to an almost gushing chemical flow, is very difficult, and very, very critical,” says Robert Goetzman, senior controls engineer at Pearl River. “The process must be precise and repeatable to maintain the quality of our plastics, whether for clarity or strength.”
The Foxboro SRD991 Positioners from Invensys Process Systems, of Foxboro, Mass., operate pneumatic valve actuators from control systems and electronic controllers over the Invensys FoxCom field device protocol. If one fails, it sets off an alarm in the control room, which is based on Foxboro’s I/A Series automation. The operators there either shut down the PET line temporarily or bypass the failed valve while technicians replace the positioner, a task that involves unbolting and removing it and installing a new one.
Then the automatic self-calibration kicks in. “It enhances quality control by eliminating or reducing mistakes that might result from a technician incorrectly calibrating the positioner,” says Goetzman. This is critical, because a miscalibrated positioner will inject the wrong amounts of PTA or MEG and ruin an entire batch.
Using its FoxCom communications instrumentation, the positioner performs the necessary diagnostics automatically in two to three minutes and sends the results to the control room. “From my office, I can check the status of all valve positioners and transmitters,” says Goetzman. Because of the positioner’s ability to monitor and calibrate critical parts of the company’s processes, Wellman uses one everywhere it needs to control the opening and closing of a valve continuously—including a new line slated to boost the plant’s output of PET by 50 percent this year.
Intelligence at workThe most important development in field devices has been their growing intelligence—intelligence to sift through the mountains of raw data being generated to find useful information and send it automatically to where it is needed. Building this kind of intelligence into field devices is crucial if users are going to reap benefits from the data available to them these days.
“Information is a good thing, but too much of it is a bad thing,” explains Rick Gorskie, senior product manager at Phoenix-based automation controls vendor Honeywell Process Solutions. “If devices just deluge you with information that you can’t use to run your process better, then the effort is wasted.”
Two developments have made the growing intelligence on field devices practical, according to Richard Casimiro, director of development for measurement and instrumentation at Invensys Process Systems. The first is the enhanced firmware made possible by the continuing advancements in digital electronics. The second is the international open-communications standard promulgated by the Brussels-based Field Device Tool (FDT) Joint Interest Group for managing the configuration and flow of information between field devices and automation control systems.
The FDT standard differs from the OPC open communication standard by focusing primarily on the device’s configuration, thereby making it independent from the communications protocol and the software running the device or the host system. “By expanding communications to field devices, FDT allows for exchanging much more diagnostic-rich information than do device descriptors (DDs) or enhanced DD language,” says Casimiro.
The result is better asset availability and utilization. Not only do the on-board diagnostics perform health checks on the internal workings of the instruments, but they also can report richer information in real time. In the case of valve positioners, such as the ones used by Wellman’s Pearl River plant, “management can plan their maintenance better and be more proactive at keeping their assets healthy,” says Casimiro.
Soon, warehouses equipped with automated storage and retrieval systems will have the same ability with the photoelectric sensors monitoring their equipment. “These facilities are generally very large and do not have much human interaction with the measuring devices for preventive maintenance and cleaning,” notes Wayne Meyer, product manager for industrial sensors at Minneapolis-based vendor Sick Inc. Because optical sensors in these situations are out of sight and out of mind, maintenance at these facilities needs an automatic prompt to alert a technician when the sensors are becoming dirty or misaligned.
Meyer reports that Sick is currently conducting beta tests on a communications network that can remotely set and poll several photoelectric sensors. The company’s engineers are adapting the technology that they are already using for controlling and diagnosing vision cameras and distance-measurement devices.
Making diagnostics pay“There are three ways to take what seems like a small bit of raw information from a transmitter and use it effectively in an asset management program,” says Gorskie, at Honeywell. The first way is to use it right there at the device. A pressure or temperature transmitter, for example, knows that it is supposed to work in a certain way. When it fails to perform as it should, it can transmit a diagnostic code to tell an operator or maintenance technician that something is not quite right, and then ask someone to come and look at it. Using the data at this level is relatively easy because it involves reading diagnostic codes from the transmitter.
The next level of using diagnostics from a smart field device is the asset level. Exploiting information here is a bit more complex and expensive because it requires a measure of integration to feed the data into an asset manager, which can review both real-time data coming from the sensors and the data stored in its archives. By linking all of the sensors and other field devices on a heat exchanger, pump or other asset, the asset manager can monitor the device as a whole and help users to diagnose and repair problems before a failure occurs. “It could cost you five times as much to fix a problem by running to failure than it would if you scheduled an outage to make the repair,” notes Gorskie.
The highest level of using diagnostics, the plant level, can save even more money. However, this level requires even more integration because it collects information from disparate locations around the plant for various uses. For example, the data could feed the fault models that operations management might use to simulate parts of the plant relying on a faulty heat exchanger or pump. These models retrieve data they need from several assets and various databases through the plant communications network, using it either to identify developing problems or to troubleshoot recurring ones. An enterprise resource planning (ERP) or other management system also can use the data to marshal the plant’s resources around a shutdown that might have to occur in a few hours.
Gorskie offers an example of a temperature transmitter monitoring a pump to illustrate how a company might exploit the built-in diagnostics at all three levels. Consider an incident in which the insulation falls off a steam jacket just above the sensor. As the sensor tracks, say, the temperature of the pump’s housing, its built-in diagnostics could report temperature readings that exceed the recommended operating range. Repairs are necessary to prevent the heat from ruining the sensor and other nearby equipment, as well as from being a source of inefficiency.
If the asset management system receiving the report is integrated into a maintenance work order system, then it can send a work order to the maintenance superintendent. “At the same time, the system can send a message to the operator saying that the asset manager has just reported a problem with pump 1,” says Gorskie. “Switch to pump 1A.”
Production can continue with the backup pump until maintenance can investigate and resolve the problem.
Meanwhile, a reliability and safety engineer might notice that the incident is the fourth time in the last month that this pump has gone off line. If the data are being archived somewhere, he will be able to retrieve and analyze the history of not only the temperature readings but also other data being collected and use them to determine the root cause of the problem. “So not only can the intelligence diagnose problems with the transmitter itself, but it also may be used to diagnose other problems,” notes Gorskie.
Smart tool managementThe process industry is not the only sector exploiting the growing intelligence on field devices. Discrete-parts manufacturers, especially those in the automobile industry, are finding them useful too. Look at Linamar Corp., a global automotive supplier based in Guelph, Ontario, Canada. Its Traxle Mfg. division has implanted radio-frequency identification (RFID) tags in the cutting tools for the machining cell capable of producing 750 axle carriers a day for Germany-based automaker DaimlerChrysler Corp.
The cell contains two sets of seven machines, one for the roughing work and the other for the finishing cuts. Each machine contains approximately 20 milling, drilling, tapping, and boring tools in its tool magazine. Each tool contains an RFID chip, or “tag,” supplied by Balluff Inc., of Florence, Ky., that not only identifies it, but also carries information about it. By tacking this information to the tools electronically, the RFID tags automate the flow of information among the 14 machining centers in the cell and the equipment in the tool crib managing the tools.
The flow of information begins with an automatic tool presetter from Zoller Inc., of Ann Arbor, Mich. The unit measures each tool and calculates the offsets necessary for tweaking the machining programs for the slight variations among the tools. It then writes to the tag both the measurements and the number of jobs that the particular tool is expected to last.
When the tools arrive at one of the machines, a technician uses a reader on a tool cart to transfer the data on each RFID tag into a machine’s controller and loads the tools into the machine’s tool magazine. The cell’s controller can then retrieve that information. “So, an operator has the ability to pull up a machine on the cell controller, scroll down the list of the tools in its magazine, and know how many hits a tool has left,” says Don Kraemer, program manager at Traxle.
When the controller calls for a particular tool, a reader on a robotic tool-changing arm loads the offset data into the controller while the arm loads the tool into the spindle. After the tool completes its task, the reader updates the remaining life as the arm returns it to its spot in the magazine. “The system will warn us at a pre-established time, usually about five parts, before the tool is at end of its life,” says Kraemer. “Then after that, the machine will not run that tool.” The tool must return to the crib and be replaced with a fresh one.
Of course, that’s the ideal situation. Sometimes, however, variations in the work material and problems developing on a particular machine cause the tool to wear prematurely. So when the dimensions of the parts produced start drifting toward tolerance limits, the tool responsible is sent to the tool crib for inspection.
Whether the tools return to the crib on schedule or prematurely, the presetter will retrieve tool life from the RFID tag, make new measurements, and dump both sets of information into the tool management system’s database. If the tool is broken or worn beyond acceptable limits, technicians will replace inserts and send the repaired tools back to the presetter for recertification. They also will conduct various analyses on the historical data, asking questions like whether the tools from a particular vendor are not holding up as they should, and whether a particular machine may be eating up tools.
Automating the data collection with the Balluf smart chips and streamlining its analysis with the Zoller software also allows Traxle to conduct experiments. For example, engineers can push inserts beyond the manufacturers’ recommendations and measure whether it pays any dividends. They also can compare the lives of tools from various vendors and try new grades of inserts to see how they stack up against the ones that the company has been using.
These studies have yielded fruit. Kraemer reports that in some cases, Traxle has been able to program the expected tool life settings higher, and squeeze at least 15 percent more life from its tools. “There’s probably 20 percent more uptime,” he says. Without the automation, conducting the studies necessary to reap these benefits would have been cumbersome at best, and would have required hiring more people at a time when labor with the necessary skills is in short supply.
Experts at Balluff and Zoller expect competitive pressure to force the automotive industry to embrace this form of automation more than it has. They are banking on the automakers’ continuing demand for ever-tighter tolerances and greater productivity. To comply, manufacturing engineers are turning to
highly engineered tools made of diamond, cubic boron nitride, and other expensive materials. Because these tools can cost thousands of dollars, the engineers want technology such as RFID to help them to get the greatest return from their investments.
RFID is not the only technology connecting smart field devices to distributed control systems and other computer networks. Mobile phone technology is another way that field devices are communicating, as the governmental agency in Denmark responsible for managing the streetlights discovered. The technology helped the government to monitor and adjust the lights to match actual conditions, and, in the process, reduce the power consumption by 35 percent.
Generating that much savings required more than simply paying careful attention to altering the times that the lights come on as the seasons change. It also needed to account for current weather conditions, the location of the lights and time of day. Not only were the lights supposed to turn on when storms darkened the skies, but the plan also called for dimming the lights at various locations as the traffic becomes less busy. Clearly, a simple timer, photoelectric switch or human intervention was insufficient.
Moreover, the lights and other devices on the network also needed the ability to keep a central control apprised of their status. and to send diagnostic information about themselves. For instance, management wanted reports of any faults immediately so it could generate reports on the status, dead bulbs, and other problems, and dispatch maintenance crews to fix the problems. This meant establishing two-way communications over a network capable of transmitting data in real time.
Building such a network that connects the control points physically by wire would have been too expensive and unwieldy. So, Amplex, the Aarhus, Denmark-based contractor responsible for the integration work, decided to exploit a network that already exists everywhere in the country—the mobile phone system. It installed a network of terminals using the general packet radio service (GPRS), a wireless communications protocol for transmitting as fast as 115 kilobits per second over the global system for mobile communications (GSM) networks used by most European mobile phone companies.
Amplex’s engineers also specified the Siemens MC 35 mobile radio module, which weighs just 16 grams and is only 6 millimeters (mm) thick. At only 54-by-36 mm, it’s smaller than a business card.
Is telemetry suitable for industrial and other commercial applications? It depends. “If you are in a fixed, permanent location that already has telephone lines and internet hookups, then you wouldn’t use cellular,” admits Peter Fowler, general manager at Siemens Wireless Modules. He also says that the technology is inappropriate for any links that cannot endure the short interruptions that cellular phone services experience occasionally.
Despite those limitations, there are many commercial applications that can benefit from telemetry. “These are sites that need monitoring, but either don’t have communications networks or move around,” says Fowler. “Chemical plants, for example, often have a lot of facilities with tanks and pumps in remote locations. Cellular technology can help them to monitor fluid levels in the tanks and the condition of the pumps.” The alternative is to send a driver to check manually—but that wouldn’t be a very smart use of intelligent field devices.
For more information, search keywords “sensing” and “smart sensors” at www.automationworld.com.
Sponsored Recommendations
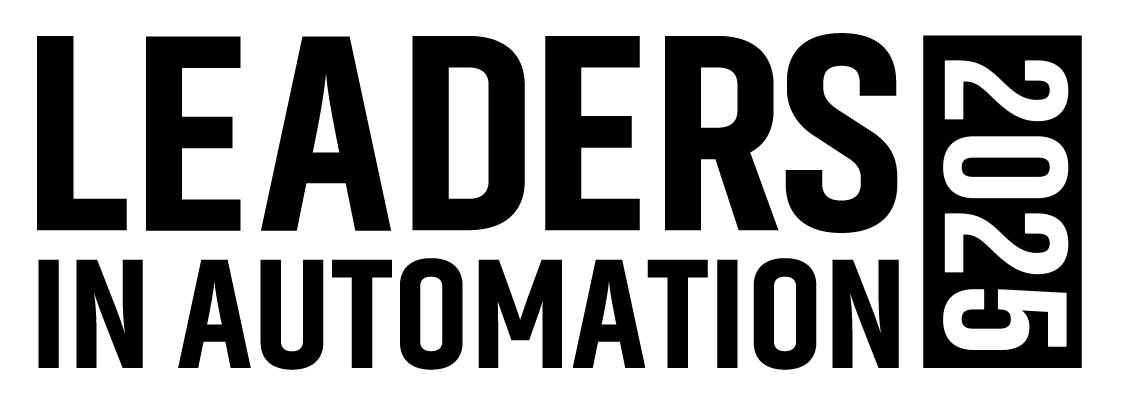
Leaders relevant to this article: