"It is
highly doubtful that an industrial tag satisfying the needs of the
industrial sector will ever be available for 25 cents," declares
Hornis, let alone the nickel price long projected for RFID tags of the
kind developed for use in retail supply chains. Pricing today ranges
typically from $2.50 up to $50 each for industrial RFID tags sold by
Twinsburg, Ohio-based vendor Pepperl+Fuchs Inc., for example, where
Hornis is intelligent systems group manager. And some industrial tags
designed for high-temperature applications sell for up to $300 each. To be sure, the cost of the electronic chips used in RFID tags will continue to decline, Hornis allows. But most of the cost of traditional industrial RFID tags is tied up in the construction and housing materials needed to enable the tags to withstand harsh factory environments, and that cost is unlikely to drop significantly, he contends. How it worksThe “tags” that Hornis describes, also called transponders, are small memory devices equipped with antennas that enable them to receive and respond to queries from RF transmitters/receivers—used in RFID systems for reading and writing information to the tags. Tags can be either active or passive. Active tags contain their own power supplies for transmitting data to a reader. They are typically larger, offer longer read ranges, and are much more expensive than passive tags, which don’t have a battery, but instead convert energy from the incoming RF scan to provide a response to the reader. In the retail supply chain, low-cost, passive tags written with product identification information are attached to pallets, cartons and packages prior to shipment; these tags can then be automatically read and recorded to inventory at the receiving end. In the industrial world, automakers, in particular, have long used RFID tagging to track products and process events on production lines. The technology has lately been making inroads among automotive suppliers, and is also getting greater use in other industry segments, including electronics, aerospace and pharmaceuticals.Intier Seating, an automotive supplier based in Mississauga, Ontario, Canada, credits an RFID system supplied by Escort Memory Systems (EMS), of Scotts Valley, Calif., with enabling it to meet strict Sequenced Part Delivery requirements for seats made for Ford Motor Co. The ability of industrial RFID to reduce identification errors on Intier’s automated lines to nearly zero, as well as its ability to record test and assembly data, has been key, the company says. Michael Darnell, vice president of sales and marketing at Prism Systems Inc., a Mobile, Ala., systems integrator, says that his company has in recent years stepped up its use of RFID. The company recently completed a project for a cigar manufacturer, for example, in which industrial RFID technology from Siemens Energy & Automation Inc., Alpharetta, Ga., plays a vital role for tracking the location and contents of some 3,600 reusable product tubs that circulate throughout the cigar plant. Darnell notes that over the past five to six years, the reliability of industrial RFID systems has improved, and the pricing has come down. “We’ve gained a lot of expertise in using RFID. The products are good, and if RFID is what’s called for, we’re going to use it without hesitation,” he asserts. For industrial applications, RFID offers various advantages over bar codes. The tags require no line-of-sight for reading and writing, eliminating orientation concerns for product moving down production lines. RFID tags can also store upwards of 30 times more data than bar codes, and unlike bar codes, information can be added to a tag as a product moves through various stages in the production process, making RFID technology a good fit for work-in-process (WIP) tracking. “With RFID, you can save time and cost because you don’t need line-of-sight, and you can eliminate labor by not having this manual process of somebody pumping a bar code gun. And you certainly have inventory transparency that you didn’t have before,” says Alex Stuebler, business manager, factory automation sensors, at Siemens Energy & Automation.At ARC Advisory Group Inc., Dedham, Mass., Chantel Polsonetti, vice president of advisory services, reports an upswing in interest among ARC’s industrial clients over the last six to nine months in return-on-investment (ROI)-driven RFID factory applications. ARC sees growing use of RFID by manufacturers for “all types of asset tracking,” including reusable container tracking, fixed or capital asset tracking, and WIP tracking, says Polsonetti. For these kinds of “closed-loop” RFID applications, in which reusable tags are used entirely within a factory or company, many users are finding that ROI falls within their required range of 12 to 18 months, she notes. Enter Wal-MartA great deal of the current rising interest in RFID was stirred up in 2003, when Wal-Mart Stores Inc., the giant Bentonville, Ark.-based retailer, launched its high-profile and much publicized RFID supply chain initiative. This has proven to be a double-edged sword for the vendors of traditional industrial RFID systems. On the one hand, by requiring its suppliers to affix low-cost, passive RFID tags to their Wal-Mart-bound product shipments, the big retailer helped raise awareness levels of RFID and its capabilities. But on the other hand, the barrage of press reports that followed the Wal-Mart pronouncement focused too much on the potential for low tag prices, without adequately explaining the differences among the various RFID technologies, some suppliers believe. And it created some unreasonable expectations. “We run into this every day. People are reading all of those stories about the Wal-Mart style of paper tags, and the assumption is that you can use those tags anywhere. But the fact is that in the large majority, if not all, of what we would deem to be industrial applications, you can’t use those tags. They’re not survivable,” says Mark Sippel, product marketing manager for Balluff Inc., an industrial RFID systems vendor with U.S. headquarters in Florence, Ky. Sippel’s reference is to the low-cost, passive RFID tags that are placed between two layers of paper or plastic to form the
bar code-printable labels that are applied directly to pallets, cartons and packages in Wal-Mart-style supply chain applications. Traditional industrial tags, by contrast, come in a variety of package sizes and styles—from button-sized up to pancake-sized or larger—that are designed to withstand the rigors of the factory, ranging from shock and vibration, to dirt and aggressive fluids, and sometimes, elevated temperatures up to 400 F. In addition, the Wal-Mart-style passive tags require only 12 bytes of memory to carry the product identification data needed. Industrial tags, on the other hand, can be either active or passive, and depending on application needs, may also require a great deal more memory, as much as 32 kilobytes. TradeoffsAnd those are not the only differences. The tags used for Wal-Mart and other retail supply chain applications operate in the ultra-high frequency (UHF) band, at 860 megahertz (MHz) to 960 MHz. These tags are based on the so-called UHF Gen2 standard ratified by Brussels-based nonprofit EPCglobal Inc. in December 2004. Many industrial RFID applications, by contrast, have historically relied upon low frequency (LF) tags operating in the 125 kilohertz (KHz) to 134.2 KHz band, and more recently on high frequency (HF) tags that operate at 13.56 MHz. Each frequency offers tradeoffs in terms of performance, tag size and price. The UHF tags offer faster data transfer rates and longer read ranges than LF and HF tags. Compared to read ranges measured in inches for LF and HF tags, a UHF Gen2 tag can be read at distances up to 25 feet. This means that UHF technology is well-suited for use in supply chain applications; UHF readers are often deployed on warehouse doorway portals, for instance, for reading multiple tags on pallets of packaged goods passing through those portals on forklift trucks.But one tradeoff for UHF tags is that they are more susceptible than LF and HF technology to performance degradation when used around liquids and metal. Given the high metal content in most factories, this means that UHF technology can present challenges in production-line applications. “UHF is not as robust in most environments as HF, so it takes a good deal more care in situating your UHF antennas and tags. And even then, your read rates are diminished,” says Bradley Todd, director of product marketing and technical support at EMS, the Scotts Valley, Calif., industrial RFID vendor. While EMS’s primary product line consists of LF and HF industrial RFID systems, the company last year introduced a UHF system that uses high temperature tags that operate in the 900 MHz range, with an eye toward industrial uses. “There’s a need in industrial applications to have read ranges in excess of a couple of feet sometimes, so we looked into UHF systems and how they could fit inside a factory space,” Todd explains. Todd says that one customer has tried out the high-temperature UHF tags for tracking auto bodies through paint ovens. And the UHF system has turned out to be “a pretty good choice for logistics inside a truck yard,” he adds. But for automated production-line tracking, Todd says, the higher read rates of LF and HF continue to make these systems a better choice. “Industrial automation people would generally not consider 99 percent read rates to be satisfactory. They’re used to having a read failure every 1,000 cycles, or every 100,000 cycles, and those numbers are pretty much unheard of for a UHF system,” Todd relates.At least one other traditional vendor of industrial RFID systems—Siemens—has also introduced systems in the 860 MHz to 960 MHz UHF range. But unlike EMS, which Todd says intends to maintain its focus strictly on the industrial RFID space, Siemens is also targeting the EPC supply chain market. The Siemens RF600 line of RFID products launched in August last year meets requirements of Gen2 and the International Standards Organization ISO 18000-6 standard, says Siemens’ Stuebler. The RF600 line complements Siemens’ 13.56 MHz products, as well as other RFID systems that are aimed at the industrial market. And while more than 90 percent of Siemens RFID sales today go into traditional closed-loop factory applications, Stuebler expects that perhaps half of the company’s total RFID revenues within five years will come from open-loop, EPC supply chain and logistics applications. “We spent a couple of million dollars developing this [RF600 line],” he says, “and we didn’t do this just to test the water.” INDUSTRIAL UHF?Stuebler also believes that the extended read range provided by the UHF family will prove useful in closed-loop industrial tracking applications. Among other things, Siemens plans to introduce metal-mount UHF tags for use in factories, he says. “I think even some of the automotive companies may find benefits out of using UHF within their four walls,” Stuebler observes. “Maybe some of their processes can be improved by just moving the equipment further apart from the actual read stations.” Despite some marketplace confusion over RFID tag pricing and capabilities, most industrial RFID vendors agree that in the end, the effect of the Wal-Mart-driven publicity is positive. “We are getting calls from a lot of people who want to know about RFID technology, and even though what they’ve learned may be inappropriate for the what they want to do, at least we can begin a dialogue,” observes Todd, at EMS. Todd puts the size of the market for traditional closed-loop LF and HF factory RFID applications in North America at $100 million to $150 million annually, and it is growing at 15 percent to 25 percent per year, he says. According to various vendors, LF and HF RFID reader/writers with associated processors equipped for communication over common industrial networks are priced typically between $500 and $3,000 per read/write point. Anywhere from 10 to 100 or more reader/writers may be required for a closed-loop industrial application, while the number of tags needed may range from 10 to several thousand for a large application. Pepperl+Fuchs’ Hornis advises potential first-time users of industrial RFID to consider the big picture. If you’re worried about saving a few dollars on the price of tags for an RFID production-line application, you’re focused on the wrong thing, he says. Because most industrial RFID tags are designed to be reused thousands of times, higher tag costs can be amortized over the life of the system, Hornis points out. So instead of fixating on tag price, says Hornis, factory users should instead focus on picking a tag and an RFID system that is suitable for their applications, while considering factors such as ease of implementation, reliability and total system cost. “Say you’re using 400 tags and you save $2 on each tag. That’s only 800 bucks,” he points out. “But if you pick the wrong system, your loss will be considerably larger.”Powerful Power Train TrackingAt Ford Motor Co.’s power train operations (PTO), radio frequency identification (RFID) plays a vital role in tracking products moving down production lines, says Kerry Paskell, PTO assembly controls supervisor, in Livonia, Mich. “We use it for our engines, head assemblies, transmission assemblies and some of our machining applications to define how a part should be manufactured,” he says.Data stored in pallet-mounted low frequency (LF) RFID tags is read at each station, which triggers appropriate production steps, depending on part type. Data on each step is then written to the tag before it is sent to the next station. “Our primary RFID supplier is Escort Memory Systems, and we have experience working with Siemens RFID and Telemecanique RFID,” Paskell says.The benefits to Ford are many, he says, including improved production flexibility and quality, reduced scrap and labor costs, and lower recall costs due to product traceability. The entire manufacturing history of an engine or transmission is recorded on a tag, and is offloaded into a computer server prior to recirculation of the tag and pallet, Paskell notes. This means that if a problem occurs, Ford can use this data to identify only those products or vehicles that have the problem, avoiding more widespread recalls. For more information, search keywords “RFID” and “track-and-trace” at www.automationworld.com.Web Extra: Click on “Podcasts” under Tools & Resources at www.automationworld.com, to download or listen to an Automation World interview with Michael Liard, RFID practice director, at ABI Research, Oyster Bay, N.Y., on the outlook for industrial RFID.
bar code-printable labels that are applied directly to pallets, cartons and packages in Wal-Mart-style supply chain applications. Traditional industrial tags, by contrast, come in a variety of package sizes and styles—from button-sized up to pancake-sized or larger—that are designed to withstand the rigors of the factory, ranging from shock and vibration, to dirt and aggressive fluids, and sometimes, elevated temperatures up to 400 F. In addition, the Wal-Mart-style passive tags require only 12 bytes of memory to carry the product identification data needed. Industrial tags, on the other hand, can be either active or passive, and depending on application needs, may also require a great deal more memory, as much as 32 kilobytes. TradeoffsAnd those are not the only differences. The tags used for Wal-Mart and other retail supply chain applications operate in the ultra-high frequency (UHF) band, at 860 megahertz (MHz) to 960 MHz. These tags are based on the so-called UHF Gen2 standard ratified by Brussels-based nonprofit EPCglobal Inc. in December 2004. Many industrial RFID applications, by contrast, have historically relied upon low frequency (LF) tags operating in the 125 kilohertz (KHz) to 134.2 KHz band, and more recently on high frequency (HF) tags that operate at 13.56 MHz. Each frequency offers tradeoffs in terms of performance, tag size and price. The UHF tags offer faster data transfer rates and longer read ranges than LF and HF tags. Compared to read ranges measured in inches for LF and HF tags, a UHF Gen2 tag can be read at distances up to 25 feet. This means that UHF technology is well-suited for use in supply chain applications; UHF readers are often deployed on warehouse doorway portals, for instance, for reading multiple tags on pallets of packaged goods passing through those portals on forklift trucks.But one tradeoff for UHF tags is that they are more susceptible than LF and HF technology to performance degradation when used around liquids and metal. Given the high metal content in most factories, this means that UHF technology can present challenges in production-line applications. “UHF is not as robust in most environments as HF, so it takes a good deal more care in situating your UHF antennas and tags. And even then, your read rates are diminished,” says Bradley Todd, director of product marketing and technical support at EMS, the Scotts Valley, Calif., industrial RFID vendor. While EMS’s primary product line consists of LF and HF industrial RFID systems, the company last year introduced a UHF system that uses high temperature tags that operate in the 900 MHz range, with an eye toward industrial uses. “There’s a need in industrial applications to have read ranges in excess of a couple of feet sometimes, so we looked into UHF systems and how they could fit inside a factory space,” Todd explains. Todd says that one customer has tried out the high-temperature UHF tags for tracking auto bodies through paint ovens. And the UHF system has turned out to be “a pretty good choice for logistics inside a truck yard,” he adds. But for automated production-line tracking, Todd says, the higher read rates of LF and HF continue to make these systems a better choice. “Industrial automation people would generally not consider 99 percent read rates to be satisfactory. They’re used to having a read failure every 1,000 cycles, or every 100,000 cycles, and those numbers are pretty much unheard of for a UHF system,” Todd relates.At least one other traditional vendor of industrial RFID systems—Siemens—has also introduced systems in the 860 MHz to 960 MHz UHF range. But unlike EMS, which Todd says intends to maintain its focus strictly on the industrial RFID space, Siemens is also targeting the EPC supply chain market. The Siemens RF600 line of RFID products launched in August last year meets requirements of Gen2 and the International Standards Organization ISO 18000-6 standard, says Siemens’ Stuebler. The RF600 line complements Siemens’ 13.56 MHz products, as well as other RFID systems that are aimed at the industrial market. And while more than 90 percent of Siemens RFID sales today go into traditional closed-loop factory applications, Stuebler expects that perhaps half of the company’s total RFID revenues within five years will come from open-loop, EPC supply chain and logistics applications. “We spent a couple of million dollars developing this [RF600 line],” he says, “and we didn’t do this just to test the water.” INDUSTRIAL UHF?Stuebler also believes that the extended read range provided by the UHF family will prove useful in closed-loop industrial tracking applications. Among other things, Siemens plans to introduce metal-mount UHF tags for use in factories, he says. “I think even some of the automotive companies may find benefits out of using UHF within their four walls,” Stuebler observes. “Maybe some of their processes can be improved by just moving the equipment further apart from the actual read stations.” Despite some marketplace confusion over RFID tag pricing and capabilities, most industrial RFID vendors agree that in the end, the effect of the Wal-Mart-driven publicity is positive. “We are getting calls from a lot of people who want to know about RFID technology, and even though what they’ve learned may be inappropriate for the what they want to do, at least we can begin a dialogue,” observes Todd, at EMS. Todd puts the size of the market for traditional closed-loop LF and HF factory RFID applications in North America at $100 million to $150 million annually, and it is growing at 15 percent to 25 percent per year, he says. According to various vendors, LF and HF RFID reader/writers with associated processors equipped for communication over common industrial networks are priced typically between $500 and $3,000 per read/write point. Anywhere from 10 to 100 or more reader/writers may be required for a closed-loop industrial application, while the number of tags needed may range from 10 to several thousand for a large application. Pepperl+Fuchs’ Hornis advises potential first-time users of industrial RFID to consider the big picture. If you’re worried about saving a few dollars on the price of tags for an RFID production-line application, you’re focused on the wrong thing, he says. Because most industrial RFID tags are designed to be reused thousands of times, higher tag costs can be amortized over the life of the system, Hornis points out. So instead of fixating on tag price, says Hornis, factory users should instead focus on picking a tag and an RFID system that is suitable for their applications, while considering factors such as ease of implementation, reliability and total system cost. “Say you’re using 400 tags and you save $2 on each tag. That’s only 800 bucks,” he points out. “But if you pick the wrong system, your loss will be considerably larger.”Powerful Power Train TrackingAt Ford Motor Co.’s power train operations (PTO), radio frequency identification (RFID) plays a vital role in tracking products moving down production lines, says Kerry Paskell, PTO assembly controls supervisor, in Livonia, Mich. “We use it for our engines, head assemblies, transmission assemblies and some of our machining applications to define how a part should be manufactured,” he says.Data stored in pallet-mounted low frequency (LF) RFID tags is read at each station, which triggers appropriate production steps, depending on part type. Data on each step is then written to the tag before it is sent to the next station. “Our primary RFID supplier is Escort Memory Systems, and we have experience working with Siemens RFID and Telemecanique RFID,” Paskell says.The benefits to Ford are many, he says, including improved production flexibility and quality, reduced scrap and labor costs, and lower recall costs due to product traceability. The entire manufacturing history of an engine or transmission is recorded on a tag, and is offloaded into a computer server prior to recirculation of the tag and pallet, Paskell notes. This means that if a problem occurs, Ford can use this data to identify only those products or vehicles that have the problem, avoiding more widespread recalls. For more information, search keywords “RFID” and “track-and-trace” at www.automationworld.com.Web Extra: Click on “Podcasts” under Tools & Resources at www.automationworld.com, to download or listen to an Automation World interview with Michael Liard, RFID practice director, at ABI Research, Oyster Bay, N.Y., on the outlook for industrial RFID.
Sponsored Recommendations
Sponsored Recommendations
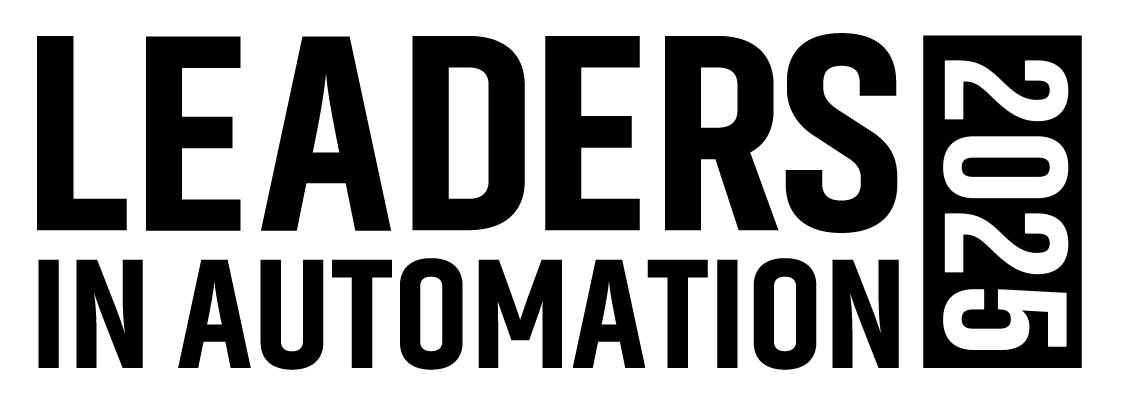
Leaders relevant to this article: