The founder of Advanced Automation Associates realized early on that a key to success for many system integrators was that they always used the same technologies. After a couple of decades integrating equipment that’s undergoing ever more rapid technology advances, he’s even more bullish on the concept of standardization.
“If I were an end user, I’d never allow anything that wasn’t ISA-88 compatible in my facility,” says Bob Zeigenfuse, president of the Exton, Pa.-based system integration company.
Though the Instrumentation, Systems and Automation Society’s (ISA) ISA-88 standard has been around for years, Zeigenfuse notes that “hardly anybody does it.” But that doesn’t stop him from promoting standards. Though the road toward standardized factories has been slow going, he’s among a growing number of automation experts who feel that the tide is beginning to turn. “Now, having a basis in standards is becoming a big benefit for us,” Zeigenfuse says.
Throughout the industry, people are starting to see an increased interest in deploying standards. “As an ISA instructor, I’ve seen a big change over the last 12 months or so. We wrote the first version of the course in 1999, and I did it maybe once. Now the ISA is calling once a month, and I’m presenting to major companies,” says Jay Jeffreys, marketing director for third party programs for Lake Forest, Calif., software supplier Wonderware, a unit of London-base Invensys.
Changing business conditions are helping fuel the push to common specifications. Manufacturing engineers competing in global markets no longer have the time needed to create systems from scratch or spend weeks integrating a new piece of equipment. At the same time, globalization and outsourcing are driving companies with far-flung operations to adopt techniques that let them use compatible processes at facilities around the globe.
Some of the world’s largest corporations are increasingly making standards a central part of their acquisition process. “PackML has worked well for us. Whenever we purchase packaging machinery, we specify it,” says Garth Basson, manufacturing systems manager at SAB Ltd., the South African operation of SABMiller plc. The Packaging Machinery Language standard from the Open Modular Architecture Control Users Group (OMAC) defines machine states so users won’t have incompatibility caused by using different terms for the same task.
As interest increases, the many standards bodies that address various segments of the diverse manufacturing world are focused on making sure that the standards work together. Most standards were developed to simplify connection between pieces of closely related equipment or software programs.
Partnerships formAs these standards gain acceptance, there’s growing interest in fostering linkage with technologies in other areas. Standard bodies are responding by extending their efforts, linking up with other organizations to develop techniques that make it easier to communicate throughout a facility, or even an enterprise. They’re striving to make sure systems built on one set of standards communicate with other standards.
One of the foremost efforts comes from the ISA, which this spring brought together a number of groups that had been communicating informally for a few years. The Manufacturing Interoperability Guideline Working Group brought together the Machinery Information Management Open Systems Alliance (MIMOSA), the Open Applications Group Inc., the OPC Foundation, and the WBF, formerly the World Batch Forum. This collaborative venture follows yet another move that will help bring commonality to standards; last year, the OMAC Users Group merged with ISA.
Committee members feel these unions will help them get standards finished in a more timely fashion by reducing duplication of effort. “This is a very positive thing. The ISA SP95 committee is reaching out to others like MIMOSA, rather than try to address maintenance ourselves,” says Keith Unger, chair is the ISA SP95 committee, which is developing the ISA-95 standard aimed at communication between control-level and enterprise-level systems.
He adds that the SP95 committee was going to define an interface at the supervisory control level. “Now we’ll just take advantage of the work OMAC has done,” says Unger, who’s also the principal manufacturing consultant at integrator Stone Technologies Inc., of St. Louis.
Other groups also see payoffs to the ISA-OMAC merger. ISA-88 is being revised to account for a standard developed by the WBF and OMAC. “Part Five (of ISA-88) will align with Make2Pack,” says Paul Nowicki, chairman of the ISA-88 Update Working Group. That will help companies go from the start of manufacturing to the finish, when products are packaged for shipment. Make2Pack defines common models, language and schemas for packaging automation systems.
Those who develop standards are generally glad to have other groups use them as a stepping-stone for higher-level tasks. “We spent a lot of time figuring out the nitty gritty procedural elements. Once they were defined, people could focus on data exchange protocols,” Nowicki adds.
All the efforts seem to be paying off. Advanced Automation is adding another formal standard to its roster of preferred practices. “We’ve adopted ISA-88. We have a version of it that meshes with our standards,” Zeigenfuse says.
Back on trackThe renewed effort by standards bodies came in response to signs that companies were adopting their own versions of standards, proving the adage that standards are like toothbrushes —everyone needs one, but they all want their own. The push toward standardization looked promising a while back, but then a lot of incompatibilities began appearing. “A few years ago, things started diverging, and it turned into a mess,” says Kemal Turedi, chief executive officer at Cyberlogic, a supplier of communications drivers in Troy, Mich.
Cyberlogic, which built its business around OPC open communication standards, is currently focused on the OPC Unified Architecture, or OPC UA. It is designed to merge many OPC specifications together to regain the benefits of standardization. Adding features that do things like making it simpler to export data is another aspect of the development process.
OPC UA also aims to replace DCOM, or Distributed Common Object Model. This Microsoft-backed communications technology served its purpose for years, but has now become “a roadblock,” Turedi says. Replacing DCOM with Web-based standards makes it easier to communicate with non-Microsoft products such as programmable logic controllers (PLCs), he adds.
Another benefit is that OPC UA makes it simpler to link lower-level machines on the plant floor directly to front office enterprise resource planning (ERP) systems or other higher-level programs. “In essence, you can have companies like (ERP vendor) SAP getting data directly from the production environment instead of relying on other layers to transport it,” Turedi says.
Combined with other specifications, OPC UA gives end-users significant benefits over proprietary techniques. “With OPC, you can handle more data in a more elegant way,” says Randy Kondor, marketing vice president at Matrikon Inc., of Edmonton, Alberta, Canada, a provider of industial information technology solutions. For example, some protocols don’t permit reports by exception, so equipment must be polled often. But with OPC, reports can be sent when data changes, reducing the horsepower needed for polling and reducing the likelihood of errors or data loss, Kondor says.
Those who develop standards and those who implement them are both hoping that the new focus on interoperability will have the same level of success as some past improvements. Standards bodies are in some ways not all that different from corporations—those that respond to feedback often see the most success.
“When OPC was first out, it wasn’t deterministic. Once they changed that, everyone started using it,” Zeigenfuse says.
Hurdles remainStandards will make it easier to interconnect systems and communicate throughout a facility, but the job still isn’t simple. There’s a fair amount that designers have to learn before they can start designing efficient products. Sometimes, they will have to change the way they look at the terms used in their facilities.
Defining terminology is a mainstay of many of the emerging standards. Without common terminology, it’s nearly impossible to link disparate technologies together. But the terms may not be what design engineers and users are used to.
“Understanding the tags can save you an inordinate amount of time. But learning them may take time. Someone in the field for years may call something one name, while the community collectively decided that term means something else,” says Bill Henderson, vertical markets marketing manager at Siemens Energy & Automation Inc., the Norcross, Ga.-based automation vendor.
Although standards bodies are often accused of moving at a glacial pace, observers note that these specifications are periodically revised. Technical staffs at the many companies that use a number of different standards could see changes on some of the specifications several times a year.
That’s particularly true for those developing production equipment and for those who implement these products. “You definitely need to remain aware of new versions so you know what you can do to bring value, saving the customer time and money by implementing standards,” Henderson says.
Although there’s a big push throughout the industry, a change to standards won’t happen overnight. Most companies pick out a segment of a standard such as ISA-95 that pertains to them, filling in those parts before adding more elements. “We’ve implemented one column, and our road map has steps for filling in the other six or seven columns,” Wonderware’s Jeffreys says.
Not all rosesHowever, the move to standards isn’t without drawbacks. Most technology implementers feel the tradeoffs come out in favor of standards, but they say engineers should be aware of those changes.
One of the key issues is that while Web technologies make it much simpler to communicate, they aren’t as compact as some proprietary technologies. “XML is extremely bulky,” Kondor says, in reference to the Extensible Markup Language convention often used in Web communications. However, in an era in which bandwidth and processor speed continue to improve, this is not a key stumbling block, he adds.
Another issue is coexistence with legacy technologies. Few factories receive the luxury of complete makeovers, so engineers must keep them in consideration. Often, legacy specifications provide efficient techniques for solving a subset of the overall problem. “DCOM continues to dominate in computer-to-computer communication,” Kondor says.
Though standards make life much simpler for those charged with connecting equipment on the plant floor, observers note that connecting equipment in the factory will always be more complex than in the front office. “When you’re integrating two pieces of machinery, it will never be as easy as plugging in a USB cable,” Henderson says.
Innovation Vs. ComplianceNo matter how good a standard is, there’s always the chance that different teams will interpret the specification differently. Or they may simply decide to alter it, gaining an edge by ignoring the compatibility that standards aim to provide.
“The real issue isn’t with the standard itself, it’s managing compliance,” says Bob Zeigenfuse, president of Advanced Automation Associates, an Exton, Pa., systems integrator.
Companies are often criticized for making devices that have slightly different interpretations of standards. But that also happens with engineers who are implementing those standards at all levels, from design to integration. “Engineers are innovative and like to make things from scratch. We have developed our own set of tools to help us manage compliance,” Zeigenfuse continues.
Standards bodies are striving to improve things. “We added sections regarding compliance, completeness and conformance,” says Keith Unger, chair is the Instrumentation, Systems and Automation Society’s ISA SP95 committee that is developing the ISA-95 series of standards on “Enterprise-Control System Integration.” However, he notes that compliance is voluntary in the United States. Though some standards organizations have established compliance boards that administer conformance tests, Unger doesn’t see that happening in his field.
The S95 group was interested in setting up some sort of testing, but it didn’t get far. “It didn’t seem to matter enough to end-users that it was something they would pay for. Without a business driver, I don’t see anything happening,” Unger says.
For more information, search keywords “ISA-88,” “ISA-95,” “PackML,” “Make2Pack” and “OPC UA” at .www.automationworld.com
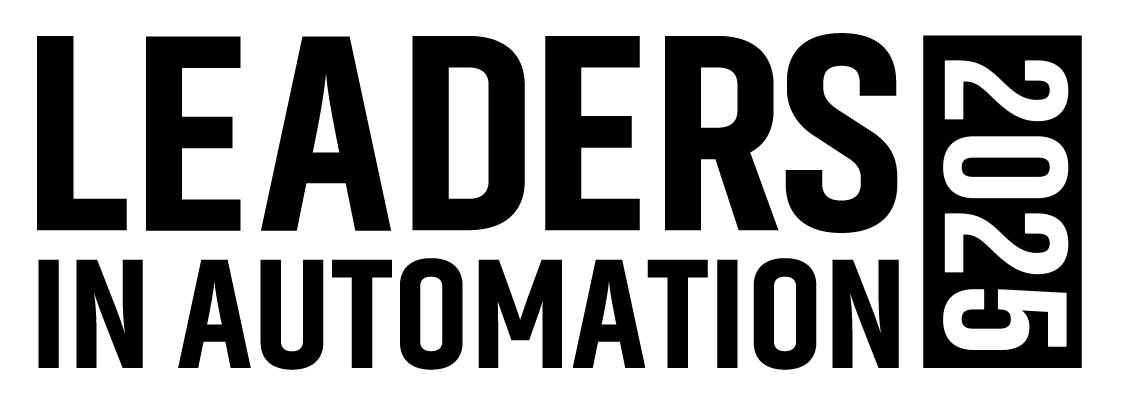
Leaders relevant to this article: