If you have a pound of Tillamook sharp cheddar cheese in the dairy drawer of your refrigerator, the cheese maker can tell you when the batch was made and how long it was aged before shipping off to your local Albertson's. Plant operators can also tell you what ingredients went into the batch. They know when those ingredients arrived at the plant and what suppliers provided them. They can even tell you what cows produced the milk and what pasture they grazed in.
While Mad Cow Disease and the Bioterrorism Act of 2002 may seem to be the likely culprits that forced the cheese maker to adopt the technology to maintain genealogy records for all batches, the plant actually adopted track-and-trace to improve its efficiency. "Our track-and-trace initiative was self motivated, prior to any government regulation. We wanted to get better control and visibility into our inven-tory and real-time processes," says Dan Dodge, business systems manager at Tillamook County Creamer Association, in Tillamook, Ore. "We converted to track-and-trace so we could know the quantity and the location of everything we have."
Eliminate paperTillamook launched its track-and-trace system back in 1998. Prior to that, the plant used a cumbersome and inaccurate manual system. "When we started, our inventory was done through paper transactions," says Dodge. "Since then, our reconciliation time has diminished, and we have visibility into our inventory. We can also see what variances we have and make corrective adjustments."As traceability became more important in food processing over the recent years, Tillamook was already positioned to trace every ingredient that entered the plant. "One ingredient, such as the starter that gives the cheese its flavor, is connected right through the PLC (programmable logic controller)," says Dodge. "If you suspect something, you can call us and we can trace the cheese back to the process it was made in."Tillamook is both a process and discrete plant. After a batch of cheese is made, it is cut into large blocks that become discrete items that need to be aged before they are cut into individual products. "At any given time, we have 50 million pounds of block product waiting to be cut," says Dodge.The plant uses InTrack software from Wonderware, of Lake Forest, Calif. The system handles both the batch and the discrete visibility. "There is a difference between the batch process side and the discrete back end," says Dodge. On the batch side, the system tracks all of the ingredients and the batch process data. On the discrete side, the system tracks inventory location and aging dates, and marries the discrete block with the individual batch data.While Tillamook uses genealogy for efficiency and quality gains, the plant gets the additional benefit of meeting U.S. Food and Drug Administration (FDA) tracking requirements. Other plants implement traceability specifically to meet government regulations. Some plants use track-and-trace to reduce the risk of pricy recalls—if you can pinpoint the questionable ingredient or part, you can limit the volume of the recall. Still other plants use traceability because of requests from major customers.The individual reasons for creating genealogy records vary, depending on what industry the plant serves. The industries that have the deepest commitment to traceability tend to be automotive, pharmaceuticals, and food and beverage. "People make the investment for tracking-and-tracing for different reasons in different industries," says Charley Rastle, beverage industry leader at automation vendor Rockwell Automation Inc., in Milwaukee. "In pharma, the driving force is regulation. In automotive, suppliers do it to meet the requirements of the automakers. In food and beverage, it’s the Bioterrorism Act."Even plants that are forced into adopting traceability want to offset that investment with some economic return. "This is not just to meet regulations," says Rastle. "Plants want the economic benefits." That can come in the form of improved inventory control and greater visibility into the manufacturing process. “If you track-and-trace, you don’t waste raw materials,” says Rastle. “You get inventory updates hourly, and you also get the benefit of on-time delivery. Plus, you can rearrange production more quickly if you know what's on the floor.”Automation catalystFor the pharmaceutical industry, traceability is often the technology that prompts the company into automation. Because of large margins, pharmaceutical companies have had little incentive to invest in automation. The government is pushing hard to change this situation through stiffer regulation and the encouragement it has given the industry to adopt process and analytical technology, or PAT. “The FDA doesn’t say companies have to keep electronic records, but they are recommending it. They call it good manufacturing,” says Carey Clements, product manager for pharmaceutical life sciences at automation supplier Honeywell Process Solutions, in Phoenix. “The problem with paper records is they're not always accurate.”Pharmaceutical companies have been notorious for their lack of automated record keeping. “The pharma supply chain leaks like a sieve. That’s the result of the way the industry has always done business,” says John Blanchard, analyst at ARC Advisory Group Inc., in Dedham, Mass. “The FDA has been attempting to close that supply chain leak and improve it through anti-counterfeiting measures.” Those requirements are becoming increasingly difficult to implement without transitioning to an automated track-and-trace system.In the automotive industry, track-and-trace is pushed down the supply chain by the large automakers who want to reduce the risk of recalls. “Reducing recalls is a compelling reason to start thinking about traceability in automotive,” says Alison Smith, senior research analyst at AMR Research Inc., in Boston. “If 12 cars have a problem, you don’t want to recall 30,000 cars. You want to recall 50.”Early warningThe auto industry also uses traceability as an answer to the federal Transportation, Recall Enhancement, Accountability and Documentation (TREAD) Act, passed in 2000. “The original genealogy traceability in the automotive industry was born of the TREAD Act, which came out of the Firestone and Ford situation,” says Rich Breuning, the discrete end-user solutions manager at GE Fanuc Automation, a Charlottesville, Va., automation supplier. “Part of the TREAD Act is early warning. Plants have to collect key information on airbags or seatbelts to see if there are some conditions that might prompt a recall.”The food and beverage industry has been using genealogy traceability for years as a response to government regulation and because it delivers measurable economic benefits. “The food industry is tremendously mature with traceability. They do it globally to protect their brands,” says AMR’s Smith. “If you’re Kraft, Cheese Whiz shouldn’t taste different in different places. Plus, there are huge efficiencies you can take from the operational excellence that can come from traceability.”Like the automotive industry, recalls are also an issue in the food industry, and genealogy tracking can mitigate the risk and damage of those recalls. “In food and beverage, they want to know what antibiotics an individual animal took,” says John Cavalenes, director of MES solutions at Citect, an automation software vendor in Alpharetta, Ga. “They don’t want to slaughter an entire herd of cows just because of one calf.”Different strokesTraceability is done differently from plant to plant, and industry to industry, but there are some common themes that run though the use of the technology. The manufacturing execution system (MES) is usually at the center of track-and-trace. But not always. “The MES means different things to different people, and it will take a different shape depending on the industry and style of manufacturing,” says AMR’s Smith. “In automotive, they don’t buy MES, they buy traceability."Usually, data comes from the sensors, through the control system and into the MES. "The PLC data talks about the temperature during the manufacturing process," says Maryanne Steidinger, director MES at Siemens Energy & Automation Inc., an Alpharetta, Ga.-based automation supplier. "The MES can access the discrete data and build a record. That record will include identifying a specific person on a specific production shift." The MES can be used to create a template for the manufacturing system to guide all steps in production. "The MES will create a model of the production process, and it will include each step in the process," says Steidinger. "The operator will get instructions on how to attend to each step."To complete the traceability loop, the MES layer integrates with the enterprise resource planning (ERP) system. "The ERP has the master information on materials, suppliers and vendors, while the MES tracks the containers," says Bob Lenich, strategic business director for life sciences at automation vendor Emerson Process Management, in Austin, Texas. "The MES will tell the ERP, 'We've produced 1,000 containers and I'm tracking the containers.'" While different industries have adopted genealogy tools for different reasons, they are all seeking similar benefits from the technology - efficiency and improved quality. A major customer or a government office may spark the adoption, but companies quickly seek a payback for the forced investment. That payback usually comes in the form of improved inventory control, greater visibility into the manufacturing process, a real-time view of order status and better on-time delivery. What’s that Flavor?At Flavor Infusion, a San Clemente, Calif., company that produces flavors as a food ingredient, track-and-trace technology was implemented to satisfy the request of a single major customer. "We're in a regulated industry, but the reason we implemented traceability is because our client does a quality audit, and one of their big things is traceability," says Steve Klehr, Flavor Infusion's director of operations. "We had to set up the track-and-trace in order to do business with this major client."The client requires complete accountability for everything that goes into each batch of flavor that Flavor Infusion ships. "We have to be 100 percent accountable for everything that goes into our batches in case of any recalls," says Klehr. Now we can take any ingredient and we can see every single batch this ingredient went into."The plant uses a control system from Siemens Energy & Automation Inc., based in Alpharetta, Ga. Data moves back and forth from the control system through middleware into accounting software the plant uses to manage work orders and recipes. As the programmable logic controller (PLC) data comes through from the control system, data from each batch is collected in the accounting software. "The accounting software talks to our PLCs and charts the batch data into a single server," says Klehr. "The flexibility of the data allows us to use the sensors to get the best quality out of our process."For more information, search keyword "traceability" at www.automationworld.com.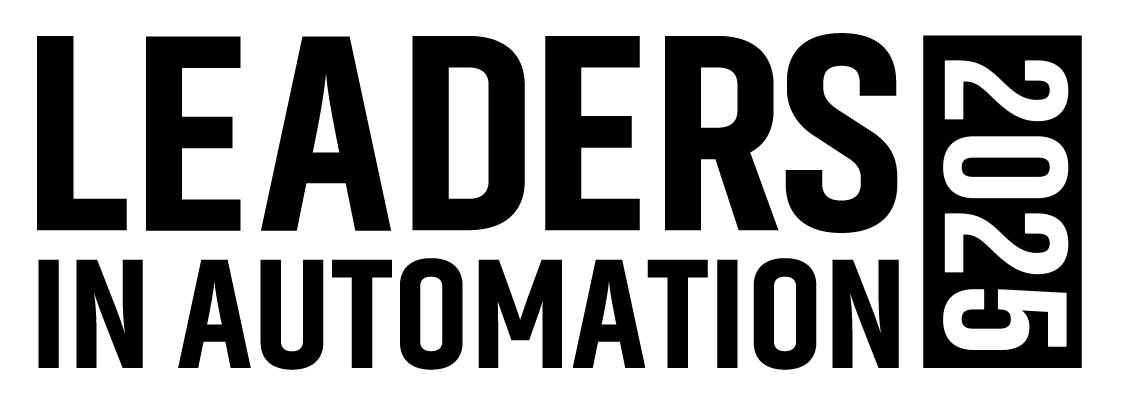
Leaders relevant to this article: