At the Autrans plant in Ingersoll, Ontario, Canada, plant operators were having difficulty creating a product buffer between the plant and its customers. The company manufactures powertrains for General Motors Corp. The automaker needs to know the powertrains will be delivered on time, so Autrans had to create a significant buffer of product to make sure unexpected plant downtime doesn’t interrupt order deliveries.
“We created our buffer manually, but now we’ve started automating it. We use real-time data that allows us to get an accurate look at where we have bottlenecks on the line,” says Jeff MacVicar, process engineering manager at Autrans Corp. “Now we can correct an issue at 9 o’clock in the morning when it comes up and send a flag to the production people.”
In the past, plant managers didn’t learn about a 9 a.m. problem until they received plant reports at the end of the day. The plant intelligence system from I/Gear, a Louisville, Ky., software developer, gives operators reports on bottlenecks and downtime problems as they occur. “That gives us the opportunity to fix it now rather than waiting until the end of the day,” says MacVicar. “Now we can see what’s going on constantly and prevent further production stops.”
Autrans uses I/Gear to get data directly from the programmable logic controllers (PLCs) controlling the line. “The system collects the data from the line and sends all the information from the PLCs to the data collection system,” explains Mark Waters, maintenance and electrical engineering manager at Autrans. “From there, we build our reports. At each station, we have a certain process we have to complete and a certain cycle time to meet. If we go over cycle time, the I/Gear system tells the PLCs what is finished and sends it to the data collection system.”
If everything goes smoothly, there is no alarm, and plant operators know production is going according to schedule. If there is a problem, alarms are sent by e-mail or phone pages to alert operators instantly that production has hit a snag. The result is improved production efficiency and thus, the buffer between Autrans and GM is more secure.
Unlock hidden data
The key to Autrans improvement is the plant operators’ ability to view data that has long existed at plants, though it was previously hidden. Plants have tons of information in their control systems, historians, manufacturing execution systems (MES) and in databases situated in or around enterprise resource planning (ERP) systems. But plants have lacked the ability to turn their rich collection of data into meaningful visibility that can show plant constraints or create basic reports on actual throughput and supply levels. Plants have the data, but they haven’t had a meaningful way to analyze it or communicate it to those who need to know when orders will be completed and when supplies will be depleted. They typically don’t even have enough information to know which of their plants should produce each order.
Plant intelligence tools began to show up just five or six years ago. “In 2000 or 2001, there were a bunch of things happening as manufacturing execution systems folks started trying to figure out if analytics could be useful,” says Alison Smith, senior research analyst in the Manufacturing and Production Operations Group at AMR Research Inc., in Boston. Historian vendors were trying to add dashboard capabilities, she says. System integrators were also finding that their connectivity could be useful for sending data from control systems and MES to other places, such as the company’s ERP system.
The development of information portals, which allow select data from a variety of sources to be aggregated and viewed on a single screen, offered a place for all of these different disciplines to collect and display their data. “The real genesis of plant intelligence came from portal technology,” says Smith. “In manufacturing, you have rich data, but it’s in different silos, it’s fragmented. The goal is to find an application that can gather the data, aggregate it in on the spot, and provide context and visibility into the right metrics.” The companies that specialize in plant intelligence include Activplant, I/Gear and Incuity, though others such as control system vendor ABB, have developed plant intelligence tools.
The goal of plant intelligence is to give plant managers a better view into their own operations. This can be as simple as viewing real-time production numbers or as complicated as tracking and comparing operations at multiple plants. “Managers can look at the whole operation and see what product they’re making at each plant,” says Andrew Ellis, vice president of advanced solutions at Incuity Software Inc., a plant intelligence software company based in Mission Viejo, Calif. “They can see the difference between plants and discover why one plant takes four hours to produce a product while the other takes two.”
Worth the trouble
As plant managers get their hands on data, they are beginning to use the information for analytics beyond just real-time reporting. Managers are using their new visibility to implement best practices, and to compare lines against each other, as well as for looking at disparate plants to determine why one is performing better than another. “You hook up a bunch of data feeds from MES and control systems,” says Julie Fraser, industry analyst at Industry Directions Inc., an analyst firm in Cummaquid, Mass. “The process is tricky, but the end result is something an operator can look at and use to compare the real-time production to theory, or to see problems coming down the line.”
The ability to analyze data lets managers track metrics and determine the optimum production capability of their lines. These metrics gained from superior lines can also be translated into best practices that can be carried from line to line, and plant to plant. “There are a number of reasons plants are using intelligence tools, and one of them is to implement best practices,” says Marc Leroux, manager for collaborative production management at ABB U.S., in Warminster, Pa. “The first thing to look at is what’s happening inside a production line, and once you know what’s happening, you can make improvements.” Those best practices can come by applying the successful elements in the superior line to all lines.
With new data in their hands, plant managers are also using intelligence tools to identify constraints and provide trace-ability. The ability to examine and analyze data can help plant operators identify underlying constraints that cause bottlenecks or downtime. In some cases, managers are able to correct a systematic problem, rather than repeatedly fixing a symptom of the problem. The ability to trace batches helps managers comply with the increasing demands from governmental agencies that are now looking more closely at manufacturing processes in industries such as pharmaceuticals and automotive.
Using plant intelligence, managers can look through a recurring problem and see an underlying systemic problem. “We see many clients fix a downtime problem without fixing the real problem. The fix makes you feel good, but the downtime was not the real constraint,” says Dennis Cocco, founder and chief product strategist, Activplant Corp., a London, Ontario, Canada, company that produces plant intelligence tools. “We identify the constraint. We can tell the client what the top 10 constraints are.”
Plant intelligence is a handy tool when traceability is an issue. “Once you have shop floor data, you get plant intelligence that can provide traceability and analysis,” says Don Korfhage, president of I/Gear. “You can take the traceability and feed it up to the ERP. Then you have a record of all the parts in a car or all the ingredients in a solution. You know what went into each car or each batch.”
Pocketbook protector
Lastly, the data from the control system and MES can help companies avoid some investments in capital equipment. Most of the companies interviewed for this article noted their plant had been anticipating further investments in equipment. But these plans were postponed or canceled altogether when they found they could use data to get more production from existing equipment.
Plant intelligence tools essentially help plants get a view into what is actually happening during production. Anyone with a stake in that production can benefit from the visibility provided to plant managers who are trying to identify constraints to company management, who in turn are trying to reduce production costs while extending the life of capital equipment. The plant intelligence tools do nothing more than consolidate existing plant data into a comprehensible format, but that alone can help managers run a leaner, more efficient plant.
For more information, search keywords “plant intelligence” and “performance management” at www.automationworld.com.
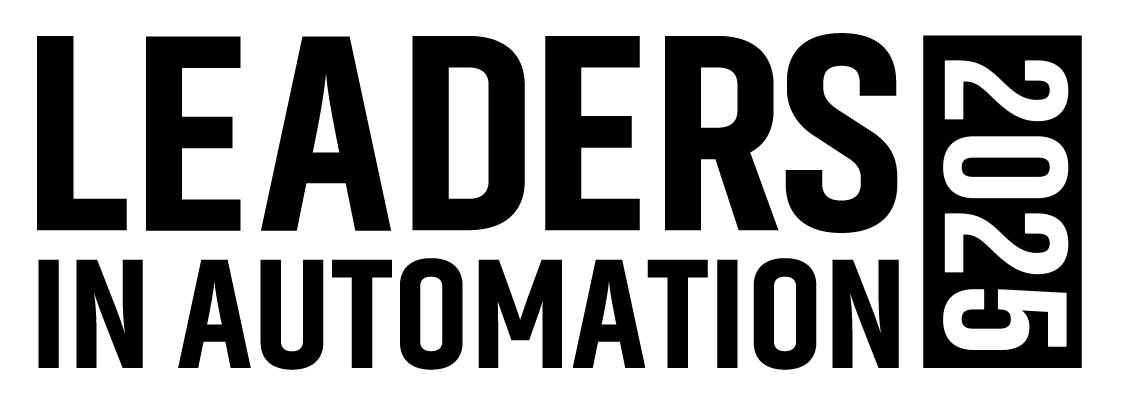
Leaders relevant to this article: