Can information technology (IT) and automation engineering work together? The short answer is yes. The long answer is also yes, but it is long indeed, with many avenues and byways. Yet, in too many companies, this is a friction drive that can generate a great deal of heat.
“A balanced company is likely to have three groups across the IT-engineering divide,” says Julie Fraser, principal and industry analyst at Industry Directions, Cummaquid, Mass. “In those companies, you will find enterprise IT, manufacturing IT and engineering. A lot of companies are highly successful in connecting business and engineering with this kind of basic structure, so you see it being applied more and more often.”
She continues, “But traditionally, and unfortunately for many companies today, the chasm can be deep between corporate IT and controls.”
Fraser, who has been an observer and analyst in computer integrated manufacturing and automation for many years, traces this chasm back to the initial development of microprocessor-aided controls in the late 1960s.
“The people developing control systems made conscious decisions to keep IT out of their hair,” she says. “At that time, real-time deterministic control needed special hardware, languages and operating systems. They knew what IT systems of the day could do, and they knew IT equipment wasn’t going to work for their applications.”
“There had to be computer platform differences in the beginning,” agrees Eric Cosman, engineering solutions architect for The Dow Chemical Co., in Midland, Mich. Dow is one of the companies that have worked long and hard to affect a marriage between IT and engineering. He adds, “It’s becoming more and more important for IT and engineering to work together, because we are now two organizations separated by common technology. We use the same commodity platforms, whether that be operating systems from Microsoft or standard hardware for networking. But, the applications are very different. You have to acknowledge those differences and avoid the temptation to extrapolate your own technology experience into domains other than your own.”
Fraser underscores that IT and engineering have very different objectives and time frames. “Engineering needs real-time data flow,” she says. “The intermediate manufacturing execution system (MES) layer wants data that could be anything from minute-by-minute, to hourly, to weekly. IT needs some things only monthly. The granularity is very different.”
How do the millions, perhaps billions, of ones and zeros rampaging right now through control systems become a handful of bytes on a monthly report? The further you move up the information systems ladder, the more you need data aggregation or data reduction.
“To aggregate or reduce data, you have to figure out what’s needed,” says Fraser. “All the ones and zeros are needed by the machine, but the front office doesn’t care about most of this. At the office level, you need a highly aggregated view: How is
actual production proceeding compared to this plan or schedule I sent down? Every function needs its own level of aggregation about what is happening with the product.”
The tricky part, Fraser says, is figuring out what data is critical to those outside your department. It is difficult enough to know what matters in your own realm, let alone all of the details about what other functions need. She is currently involved conducting a research study, commissioned by the Manufacturing Enter-prise Solutions Association International (MESA), called “Metrics That Matter,” designed to identify key performance indicators (KPIs)—those critical things that must be measured based on corporate strategy.
WHY COLLABORATE?
There are some good reasons why engineering might be interested in collaborative interaction with corporate IT and the executive staff. A primary one is an ability to tap into the skills of the IT department in getting funding for new systems. Less often mentioned, but in the long run perhaps more important, are the opportunities that are enabled by direct engineer-to-executive conversation. Top management knows engineering is important, but few of the players in the carpeted suites can follow more than the first sentence of a genuine technical discussion.
Fraser puts this more eloquently. “If we in controls and automation have someone who can communicate with executives, it’s far less difficult to justify systems and necessary improvements. We need to learn how to put things in terms that they care about. We need to learn how to explain things clearly, and we need to clearly demonstrate how we help make things a success at the company.”
There can be specific advantages to people-to-people IT/engineering communication on the production floor as well. One example is given by Sarah Wiseman, software engineering specialist at systems integrator Eagle Technologies Group, in Bridgman, Mich. “In one installation for a large customer, we came across two identical machines using separate data systems. The machines were building the same part, but couldn’t communicate. After involving corporate IT for the first time—the first such involvement in that part of production—IT said, ‘Let’s look at your network and make it right.’ The result was a much simplified infrastructure, one that avoided a lot of duplicate activities.”
The ultimate benefit of direct connectivity between production and business is more visibility of manufacturing’s ability to respond to business objectives. Everybody wins, assuming the goals are rational: improve good-selling products, streamline processes by which to make them, jettison unprofitable products and cease processes that create waste.
FIVE KEYS
Reaching a state of communication between plant and executive suite is, as Dow’s Cosman puts it, “a journey, not a destination. It’s something you have to work at every day.” The process begins with human communication, not technology layers.
“If you’re in a situation where people immediately begin arguing technology,” Cosman says, “it’s a sign that everyone may have missed the boat. You simply have to go to the soft side, talk about the win-win, about sharing objectives. Neither IT nor engineers jump to that immediately.”
According to experts, successful marriages between IT and engineering typically have five key attributes in common:
• Commitment by top management
• Involvement by all affected departments
• Inclusion of at least one strong participant who has experience on both sides, IT and plant
• Creation and maintenance of a team
• Strong focus on a specific goal, at least at first.
You have to start at the top. “When we first started,” says Cosman, “we called a meeting with the chief information officer, the vice presidents of engineering and representatives from various technology centers. When they were around the table, we said, ‘We want to create a partnership, and we need you as a sponsor. We need you to say you support it, act like you support it, demonstrate your support at all times.’ ”
“Sponsor” is the key word there—by asking for support beyond simple approval of a good idea, sponsorship suggests powerful, measurable activity. Cosman continues, “We asked them to help us figure out the win-win, help us be better together than separately. With their help, we identified a small group of people in leadership and influential positions to act as proponents, to advocate, coach, direct and guide.”
Rich Santoriello, now with MES software provider Camstar Systems Inc., in Campbell, Calif., was earlier in charge of manufacturing IT for Lenox Inc., best known for its fine china. He emphasizes the necessity of active support at the top in any initiative to bring IT and engineering together. “It has to be a high strategic goal from the chief executive officer or from the VP level. You can’t just go into the plant or plants that will be included in an MES and start changing things. The effort must be strategic, from the corporate executive level, and the corporate executives have to articulate that this is a common goal for everyone.”
“Support at the top was a major help to me,” Santoriello adds, referring to his Lenox initiative to install an MES system. “If I found resistance to change, I could simply mention that the vice president of manufacturing wants this system because of these KPIs, and then I would list them. I could say, ‘Your boss and my boss want us to make this happen.’ At the very least, it gave the foot-dragger something to think about.”
INVOLVE EVERYONE
You cannot expect people to be happy unless they buy in to a process. You are also unlikely to answer everyone’s needs unless you really know what they are. Soliciting the involvement—input, discussion, action—of everyone concerned is about the only way to ensure success.
“We also did not just hand the plant people a new system,” says Santoriello of his days at Lenox. “We got everybody in a room, with representation from every plant and every department in every plant. Around the table, these people talked about how the MES should be put together. We did the same thing on the corporate level with IT, production planning, new product development, and the whole range of other people whose lives were going to be affected by our changes.”
Fraser says, “You need to put a team together with people who have experience on both sides—you need people who are not just IT or just the plant, but know how the business and how engineering work.” She points out that most of the most highly effective people in Manufacturing IT, while they have
IT technical background, bring an in-depth understanding of manufacturing information flow. “Relatively speaking, you can learn technology fairly quickly,” she says, “but it takes decades to learn manufacturing.”
Santoriello was able to bring both IT and engineering skills to the Lenox initiative. “Basically, Lenox put me in charge of manufacturing IT because I kept complaining that we in manufacturing should not rely on data that is different across several separate systems,” he says. “But a lot of the success in our MES installation, from an IT perspective, stemmed from the fact that I knew what it was like to work in the plant. I had been the plant analyst, making sure that the computers ran right, that the network was working and that we subscribed to the standards of corporate IT. Up to the point when I was given the manufacturing IT title, I worked at the plant level, and the people I spoke to at the plant level had worked with me and knew I could get things done and had manufacturing’s best interests in mind.”
Cosman has been with Dow for more than 30 years and has worked both in engineering and corporate IT. His from-the-top experience dovetails with the from-the-floor experience of Eagle Technology’s Wiseman.
“One of the first things I do when we start a system installation is to communicate with IT,” Wiseman says. “Before beginning a given installation, I’ll tell IT what has been purchased and tell them I need their help configuring things so they can support them. I’ll ask them if they have a [specification] that I can follow, and if not, would they be willing to work with me to develop a new one. If we’re putting in a product they don’t know, I’ll forward information on training so they’ll be up to speed by the time the new project goes live.”
She has enjoyed gratitude from IT departments because she routinely contacts them. In some cases, the system specification and procurement process had gone on without IT involvement, a source of many a potential pitfall. In other situations, she has uncovered existing corporate machine interface specifications that worked as well as, or better than the one originally on the system plan.
“I stay aware of any disconnect between engineering and IT,” she says. “I started my work life in IT, and I know the importance that IT puts on staying abreast of what’s going on in the company. And I know what it means to have to support non-standard systems because somebody didn’t do their homework.”
Fraser underscores the need for IT participation. “Basically, IT needs to be heavily involved because information from the plant floor can be used by almost any department you can think of,” she says. “ERP (enterprise resource planning), data warehousing, procurement, distribution, regulatory and compliance—and these are becoming more and more important—the list goes on and on. All of these have to see where things are going right or wrong, and IT is good at putting information conduits into place.”
BUILD A TEAM
Fraser points out that competition is so fierce, and so much is being outsourced or offshored, that you have to build a team quickly.
These tactics include open discussion, and a moderator who can control those who would steal the spotlight, encourage input from those who would remain silent, and bring things back to the point when focus is lost. “You really need to have a contracting discussion with the parties sitting down together,” says Cosman. “A key thing is to take the time to really think about and understand what your essential wants are. Insist that the guy across the table do the same. Without understanding the wants involved, there’s no hope of common vision.”
The process is not as simple as it sounds, however; nothing is simple that involves human beings trying to pull together for a goal. “As part of a systems integration group, I see a lot of diversity in how individual members respond to things,” says Wiseman. “I’ve seen IT groups who are highly receptive, and pitch right in to move toward a solution. I’ve seen others where corporate IT says, in effect, they want nothing to do with the system installation, that they don’t want to see it again.”
Cosman details one key consideration: the drawbacks of a team whose members come from organizations with differing levels of empowerment. One group might be task oriented, where people are told what to do. A second group might be individualistic or self-tasked. “When you put those two types of groups together, you will have problems,” he says.
He adds, “It helps that in our company, we have internal training as part of HR (Human Resources). One course focuses on creating strategic partnerships for mutual success, and if you are in engineering, it’s mandatory that you take it. It helps people realize that their success is connected to the success of their partners.”
Identifying a focused, yet meaningful, initial project can be a key enabler for ongoing collaboration among team members. Fraser notes, “You need to make sure you are fighting for something that matters. Create a solid set of requirements based on your business strategy, and create a focused program.”
She gives some examples: In a process industry, you might focus on how close you are to theoretical yields, or whether you are making margins, whether you are meeting market needs with production. In discrete manufacturing, this focus could well be on the pace at which new products make it to delivery. “If there is a longer ramp-up time to quality than you want, a delay of three or four weeks may put you past your window of opportunity,” Fraser points out.
MAKING THE MOVE
Though there are barriers and tough spots, many companies have successfully married corporate IT and automation. It takes some learning, but the most down-on-the-floor manufacturing team can learn enterprise perspectives. The most remote of IT departments can at least begin to get a sense of what transpires in manufacturing.
One key return, albeit soft, is pride. Says Santoriello: “We helped in a revolution that changed how a 100-year-old company makes its products. Everybody should be proud of that.”
And other returns can be pleasantly measurable. “Once the IT staff understands what you’re doing, they can lobby for you,” Fraser notes. “They’re already in the top office, and they have great success funding their systems—now it’s our turn to get some goodies.”
So, yes, business and engineering can work together.
For more information, search keyword “information technology” at www.automationworld.com.
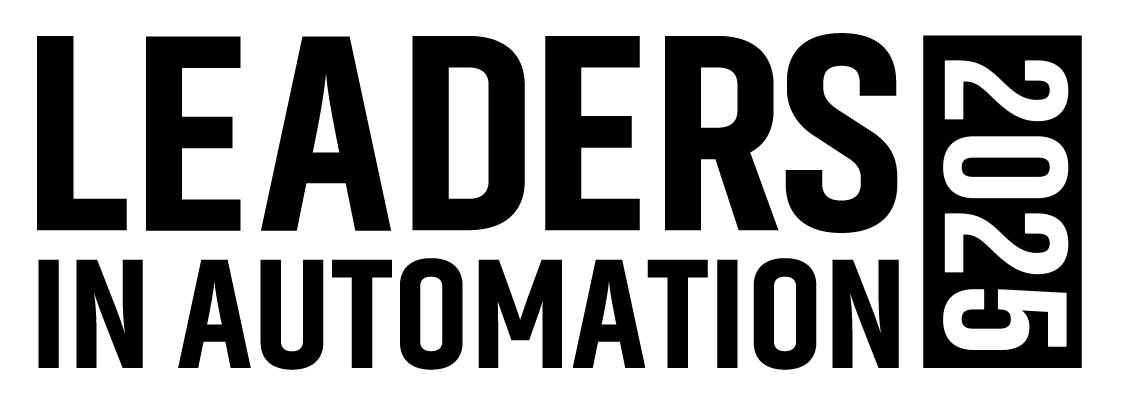
Leaders relevant to this article: