The Terrorist Attack On Sept. 11, 2001, Forced A Radical Change In Security At The Chemical Plant Operated By Honeywell Specialty Materials Along The Mississippi River In Geismar, La. Because An Attack On Any Chemical Plant Has The Potential To Hurt Thousands Of People, These Facilities Make Juicy Targets For Terrorists. Consequently, The U.S. Department Of Homeland Security Has Urged Them To Tighten Their Security To Guard Against Much More Than The Conventional Problems Of Theft And Accidents.
“Before 9/11, security meant keeping valuable tools from walking out of the plant,” says Bill Lessig, Geismar’s plant manager. “Now it has shifted to thinking about threats from external sources—to ensure business continuity, to minimize the impact of an attack, and to make sure the surrounding community is safe.” Today’s industrial security apparatus, therefore, must be aggressive about keeping unauthorized people out, and work with governmental security agencies to mount rapid and effective responses to any incident that might occur.
Adhering to this higher standard for security posed a significant challenge at Geismar. Although the developed portion of the Honeywell facility covers only 240 acres, the facility actually spans 1,900 acres. And one of its five operating units is the world’s largest site for producing hydrofluoric acid, a raw material for refrigerants and other products. The other four units produce a variety of chemicals, such as non-ozone depleting refrigerants and blowing agents.
To take advantage of its location along the heavily traveled, critical Mississippi waterway, the plant also contains a dock that can accommodate ocean-going ships that have capacities as large as 25,000 tons. The resulting traffic puts the plant under the jurisdiction of the Coast Guard. So the security plan must comply with the Coast Guard’s regulations.
Complicating the task is the fact that Honeywell plays host to four other chemical companies on the site. Like Honeywell, these companies bought pieces of some property owned originally by Allied Chemical decades ago. Since then, they have contracted Honeywell as host to provide services, such as water, storage facilities, a medical station, some security services and use of the dock. Consequently, Honeywell must secure its facilities, yet provide the appropriate access to its 275 employees, the 400 employees of the other four companies, and the 80 to 100 contractors that Honeywell has working on-site. All and all, it must control the comings and goings of about 1,000 people a day.
Responding in real time
To prevent the tighter security from encumbering these people from doing their jobs, the plant spent about $3 million on a holistic solution to the problem. It brought in specialists from Honeywell’s security and controls business to develop tighter physical and cyber layers of security, and then integrate them with the building automation and process control systems. The specialists updated video monitoring equipment, improved fencing and lighting, and added sophisticated beyond-the-perimeter surveillance equipment.
At the heart of this integration project is Honeywell’s Experion Process Knowledge System for process control, and its Enterprise Buildings Integrator for security and heating, ventilation and air conditioning systems. Because Honeywell designed both sets of software to run on the same distributed-server architecture, they fit together seamlessly and pass information to each other in real time. Moreover, the standard interfaces that Honeywell uses wherever possible allowed Geismar to use the surveillance cameras that it had already, thereby reducing the number of new ones that it had to buy.
“The computer systems are separate, but the software is totally integrated through the network,” notes Lessig. “From a control room, you can see what’s going on with the security system. Conversely, people in the security command center can see what’s going on in the process.” He points out, however, that the system is flexible enough for management to program the kind and amount of information shared.
Lessig reports that, for him, the biggest benefit from this integration is faster response to an intruder, accident or other incident. He says that the faster response limits the risk from each exposure. If someone were to actuate one of the motion detectors around the plant, for example, only security would have known that in the past. A guard would have to take the time to investigate and decide whether to inform process control. Now that motion detection data are sent directly to the control room, the people there can take any necessary safety precautions more quickly.
Conversely, an alarm sounds in both the security office and the process control room whenever process problems develop. The computer monitor tells the security guard whom to call and what to do. “This has significant value for any chemical plant manager during an incident, such as a spill,” says Lessig. “In the past, somebody had to get on the radio or telephone, call security to inform them of the problem and request action. In the heat of the moment, chances are that’s not going to be the highest priority on your mind.” So putting security in the loop from the start avoids that lag and reduces the huge risk that each passing minute would otherwise present.
The system also will help management to account for its employees should the plant ever have an accident. Standard procedure at chemical plants is for everyone to report to mustering stations so the designated people can take attendance. “In the past, somebody would write people’s names on a clipboard, and eventually we would determine who was at mustering stations and who was not,” says Lessig. “It took time.” The new security system takes attendance automatically. Employees just swipe their identity cards in the readers at each station, and the system generates a report in a few minutes.
Like most other security experts, those at Honeywell believe that a layered approach is the most effective method for thwarting attacks and protecting people and assets. Consequently, they established three basic physical barriers at Geismar. The first, a fence, establishes a perimeter around Honeywell’s operations and isolates them from the outside world and the other four companies on the site. Cameras, motion detectors and microwave sensors monitor the perimeter on land, and radar looks up and down the river to track any movement there.
“The cameras serve two purposes: surveillance and motion detection,” explains Lessig. “If there is some motion at the fence line, the camera picks it up digitally. It will activate an alarm, zoom in on it and provide us with a picture of what’s going on out there.”
The second layer of physical barriers consists of another set of fences and automatic gates surrounding each of the processes and other areas inside Honeywell’s perimeter. Cameras monitor the fences, and workers use their identity cards to gain access to the areas for which they have clearance to enter. The access cards solve the problem of controlling the movement of both the contractors that Honeywell hires and the neighboring companies that buy services from Honeywell. To give its neighbors access to the storeroom, for example, Honeywell security enters the names of the appropriate people from those companies into the security system so they can enter that area with their identity cards.
The identity cards also serve as keys to the control rooms, the hearts of each process in the plant. Only those people with clearance can unlock the control rooms’ doors and pass through the final physical barrier in the layered security scheme at Geismar. Card access also tracks who is where in the facility, not only for security but also for finding people who fail to report to a mustering station during an incident.
Although the control room doors are the third and last of the physical barriers, they are not the last layer of security. Others exist, such as the tracking devices carried by certain people and assets. “For instance, our security people carry a monitoring device, as they make their rounds,” offers Lessig. “We know where they are at all times.” Besides offering a measure of protection for the guards, the tracking devices also can do the same for equipment. They not only deter theft but also can hasten response to accidents when mounted on vehicles.
Cheaper video transmission
Video surveillance has been a crucial element in many layered security plans, including the one at Honeywell. Like any technology, though, it has had limitations that has curbed it use. A number of recent advances in automation, however, are overcoming those limitations and making the technology more practical and effective over a wider range of applications.
One of these advancements is the ability to transmit video over low-bandwidth supervisory control and data acquisition (SCADA) communications networks. This ability changes the economics for monitoring water treatment plants and other facilities that have pumping stations, water tanks and other assets distributed remotely over large geographical areas. The conventional methods for securing these remote assets have chain-link fences and, in some instances, limit switches on hatches and doors are hard-wired to the central plant to report breaches.
In the past, large distances have made video surveillance and other advanced security measures impractical, both economically and physically. The cost of installing new, high-bandwidth cable or fiber network can cost several tens of thousands of dollars per mile, according to Longwatch Inc., a company based in Norwood, Mass., that has developed technology for sending video over existing SCADA control and telemetry networks. Subscribing to multiple cellular contracts to cover a service area was not very appealing either. The ability to use existing low-bandwidth networks eliminates these expenses.
Seeing it all
Technological advances in video automation also can alleviate sensory overload, another limitation on video surveillance. “People may be attempting to monitor hundreds of cameras, door and gate alarms, and radio communications,” says Bill Adams, chief executive officer of G5 Technologies Inc., an information-technology integrator based in Mount Laurel, N.J. Consequently, these sensors are providing more information than a reasonable number of security guards can process.
The backbone of the automation technologies that can solve this problem is a class of video-analysis software that can be programmed to recognize certain behaviors. “The software is continuously staring through the camera, looking for behaviors a human would normally be trained to look for,” says Adams. “Once calibrated, it doesn’t miss detection events.” He points out that this kind of analysis software allows a few security guards to monitor hundreds of cameras effectively.
Another important piece of technology for alleviating sensory overload is geospatial information systems (GISs). Because these systems capture, analyze and display data based on geography, they let security guards see the big picture, placing the data on three-dimensional maps of their facilities. “A GIS presents data from any and all sensor systems in a manner of interest to a particular user so the view is not overcrowded but still comprehensive,” says Adams. The system displays the data in layers so security can see the entire situation, yet retrieve details as necessary. It also can parse the data in Web Services for transmission to remote users carrying personal digital assistants (PDAs) or tablet personal computers (PCs).
Yet another piece of the puzzle is an automated reporting apparatus. “Technology has matured to where rules engines acting like knowledge switches can filter sensor alarms for presentation to users as desired,” explains Adams. He says the rules can be written to notify first responders automatically based on the type of alarm and the kind of communications device held by the responder. When the campus is large, has little to no infrastructure, or both, Adams usually recommends wireless networking to integrate the sensors and extend the existing network.
These technologies are already at work assisting the security forces at airports worldwide. In fact, G5 Technologies recently installed a security system based on them at the Tallahassee Regional Airport in Florida, responding to encouragement from the Transportation Security Administration (TSA) to adopt support technologies that can enhance security without adding new people. In this case, G5 automates security using the SmartCatch intelligent video surveillance system from Vidient Inc., of Sunnyvale, Calif.
The video-analysis program monitors the behavior of everyone in the airport, checking for policy violations. Consider a passenger who might leave a bag unattended or walk the wrong way through an exit. The system alerts security, sending a video clip of the offense and showing the location of the violation. The same would happen if two employees were to walk through a restricted-access door using only one of their identity cards. The automation keeps intruders out and helps security to protect the facility.
For more information, search keyword “security” at www.automationworld.com.
See sidebar to this article: Security Networks, Layer by Layer
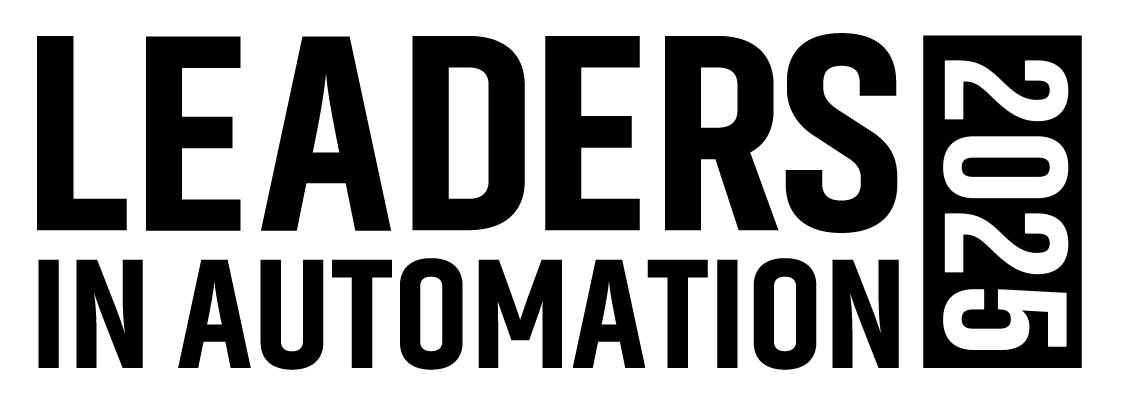
Leaders relevant to this article: