There comes a time in the life of any control system when it must be brought into conformance with the latest technologies. This is true whether it is a process control system or a small programmable logic controller (PLC) on a discrete manufacturing piece of machinery. Many control systems in use today are not equipped to handle the demands of modern digital fieldbus networks, or to process and communicate the vast amounts of real-time manufacturing data required by voracious business information systems. That’s not to mention coordinated motion and logic control, or the development of a library of programming objects.
Management at Nova Chemicals Corp., a Canadian-based manufacturer of chemicals and plastics with executive offices in Moon Township, Pa., near Pittsburgh, decided that if the company was to grow and thrive, it needed to achieve operational excellence across its many manufacturing plants. To form the challenge it placed before its employees, it defined the mission: “We will astutely employ process automation expertise, technology and sustainable infrastructure to achieve Operational Excellence and top quartile manufacturing performance through a program that leverages people, systems and best practices.”
Steve Deschamps, principal practitioner-automation at Nova Chemicals and member of the implementation team, says, “We will achieve manufacturing excellence through automation migration.” The ambitious strategy that Deschamps outlines includes:
optimize cross organizational performance implement short- and long-range plans to fully optimize the prevailing asset base, leverage internal and external knowledge, resources and best practices astutely integrate process and business automation into manufacturing systems and processes.
Deschamps notes that the progress the company has made so far would never have happened without all the relationships that the implementation team formed. As the team members began to focus on the control platform, they realized that the best strategy would be to work with one supplier. After an extensive selection process, they picked Swiss-based ABB, whose U.S. offices are in Norwalk, Conn. Teams of engineers from the two companies conducted a thorough automation lifecycle review, drew up a business case and evaluated the potential lifecycle—including ABB’s product plans—for each automation component. The team then laid out an eight-year evolution plan.
Not only were process engineers and ABB engineers involved, but the team also had active participation from Nova’s information technology (IT) department. Says Deschamps, “We’re really proud of the IT involvement in this project. Plus, I can truly say that collaboration with your supplier works.”
Random migrations? Platt Beltz, technical support specialist at process controls vendor Yokogawa Corp. of America, in Houston, is concerned that customers hearing the term “migration” from a system sales person may conjure visions of a haphazard, poorly designed program to move them from the old platform to a new one. Customers may also be concerned about giving up a system that is working. “The reality is,” says Beltz, “that as systems get older, maintenance costs can increase—especially if they are in a harsh environment. Also, there is a lifecycle phase-out as newer systems are released.”
Beltz enumerates the many advantages of the latest control systems as reasons to consider migrating, or evolving, a working control system. Compared to 10 years ago, for example, when a control station could handle up to 225 instruments, the equivalent control station today can handle 1,200 of the same instruments, plus up to 1 million tags. Plus, users get a more modern set of engineering tools and graphics builders that improve and speed the design process. Add in the benefits of wiring and diagnostics from Foundation Fieldbus, and Beltz makes a compelling case for users to seriously look at migration.
Of course, careful advanced planning and building a compelling business case, as Nova Chemicals’ Deschamps showed, should be done before plunging ahead into a haphazard migration.
Pete Sharpe, principal consultant at process controls vendor Emerson Process Management’s Advanced Application Technologies Group, in Austin, Texas, works with customers as they plan upgrades to their control systems. He agrees that planning is key. “Get your hands on the business justification for your system upgrade,” states Sharpe. “Users should perform a thorough analysis, looking at all the pieces of the system that must be replaced, and cost all the components. There are various levels of complexity that should be addressed. Is the project a complete ‘rip-and-replace,’ or can you maintain your I/O (input/output) modules and racks, and just replace the system boards and software? Or is it a case of ripping out the system and I/O and just leaving the field instruments? In any case, this is a significant activity, so engineers and managers should not shortchange planning.”
Counting the benefits Why would someone want to go to all this work? Sharpe says customers are looking for higher availability of process equipment, and the greater information provided by today’s control systems can help them achieve that goal. With an upgraded control system, they can run consistently closer to specification, gain higher throughput, reduce maintenance costs, improve yields and lower waste.
Dave Cunningham is a project manager for Honeywell Process Solutions, another controls vendor based in Phoenix. Currently working at a major refinery on an 18-month system upgrade project, Cunningham notes that of the seven total projects in process now, four are compliance units. While management wanted to do some work on the units, compliance with U.S. Environmental Protection Agency (EPA) regulations drove the final decisions to start. In a plant with systems from different suppliers in different areas, the initial decision to go with Honeywell to replace a competitive system for the first compliance unit was driven by a desire to match presentation graphics across all areas. In addition, the company wanted an open system to assure a longer lifecycle. The plan is to replace systems on a unit-by-unit basis until the entire refinery has been upgraded.
The real money that results from a control system upgrade is the addition of a broad platform from which to implement advanced process control (APC), according to Cunningham. In the current refinery project involving the four compliance projects, for example, the replacement of a control system and the standardized operator workstations will result in improved uptime and control that might show a 2 percent to 3 percent improvement. But the addition of APC and application of high-level algorithms will increase yield and quality with returns much higher than that.
Keith Hogan, product manager in the Process Control Group at Milwaukee-based controls vendor Rockwell Automation Inc., acknowledges that many people think of his company as a supplier for discrete manufacturing. “So when we come in with the idea of a plant-wide upgrade solution [that includes process control], customers sometimes do a double-take. On the other hand, customers in the food or paper industries have a blend of discrete manufacturing, packaging, motion control, coordinated drive systems and hybrid batch processing. In these cases, it is possible to upgrade to a common control platform and achieve savings in engineering and training,” says Hogan.
Mackay Sugar Cooperative, in Queensland, Australia, is one of the country’s largest sugar cane producing and sugar manufacturing companies. During the annual six months of production from July to December, the mills operate 24 hours per day, seven days a week. In the manufacturing process, sugar cane is shredded and crushed between rollers to extract the sugar juice from the residual fibrous material. The sugar cane juice is then purified and transported through a series of vacuum evaporation pans, where it is concentrated by boiling. During a second stage in high-vacuum boiling pans, the concentrated syrup is seeded with very fine sugar dust in order to crystallize the sugar; this mixture of raw sugar crystals and syrup (molasses) is separated in a final centrifugal process, after which the raw sugar crystals are dried.
According to Peter Mitchell, an electrical engineer at Marian Mill, a Mackay Sugar Cooperative member, the main driver for a recent project to upgrade the Mill’s control system was the need to replace an aged and unserviceable distributed control system (DCS). “It became impossible to buy spare parts,” he says. “The DCS has not been supported since 1992. Since then, we’ve had to beg, borrow and scrounge for whatever parts we could find in Australia.”
More automation The new control platform not only replaced an obsolete system, but it also provided new value. “We were previously limited as to the amount of automatic sequencing we could do with the DCS,” he says. “So we wanted a system that would automatically do all the production sequencing, from start to finish, as well as allow remote monitoring of the process. Since we already had a number of Rockwell Automation SLC-500 programmable logic controllers, we decided to stay with them for the new system.”
According to Mitchell, the upgrade project has been a resounding success. “We’ve been able to reduce the number of pan stage operators from three to two,” Mitchell says, which yields a direct savings of 33 percent. “This is the result of the comprehensive automatic sequencing and the fact that we can remotely monitor the process from either upstairs or downstairs.” The labor savings equates to four operators at 40 hours each per week, for the 24-week crushing season.
It’s not only process plants that carefully study control system architecture upgrades; discrete manufacturers can find many of the same benefits with proper planning. And just as many benefits in process system evolution come from implementing digital fieldbus networks, so too do discrete manufacturers find paybacks in upgrading to digital networks.
“Typically, an auto assembly line will have perhaps 10 or 20 different workstations,” says Greg Deel, project manager at Pyramid Solutions Inc., a Bingham Farms, Mich., system integrator. “Running individual serial lines to each one works well enough, but isn’t very practical.”
Nevertheless, Visteon Corp., a Van Buren Township, Mich., automotive parts supplier, had this exact architecture installed and running in some of its plants. Each workstation—about 17 in all—had a dedicated personal computer (PC) enclosed in a protective cabinet and connected to a Snap Ethernet brain board from Opto 22, a Temecula, Calif., automation supplier. The connection was made through the serial port on the back of the CPU. This architecture worked, but it resulted in excessive wiring and hardware.
To improve this, Pyramid upgraded Visteon’s architecture by using “blade” PCs residing in a single cabinet in the center of the line. The Snap Ethernet systems are now distributed around the line and connected to a network switch, instead of the individual PCs, with each Snap Ethernet unit capable of handling the connections for multiple workstations.
“Switching to Ethernet helped consolidate things considerably,” says Deel. “With everything connected via Ethernet, we were able to put the I/O modules in a more out-of-the-way place and get rid of those bulky cabinets. Each Snap Ethernet unit can handle up to 16 four-channel modules. That’s 64 I/O connections—enough to handle the equipment at five or six workstations.”
Pyramid was able to deploy the Snap Ethernet systems at the Visteon facilities without replacing, modifying or otherwise disturbing the existing installed control systems—a capability that Deel says is extremely important to customers at all levels of an organization, from manufacturing managers on the plant floor all the way up to the Chief Operating Officer.
Fast, flawless changeovers are important for Native American-owned contract beverage processor Yakama Juice LLC, in Selah, Wash., to attract business from major beverage and grocery chain customers.
The company’s ability to do turn-on-a-dime changeovers makes Yakama more competitive in terms of both cost and responsiveness.
Rectangular or round, glass or plastic A Krones brand rotary labeler remanufactured by K2 Engineering Group, Big Bend, Wisc., has removed the bottleneck from Yakama’s quick-change strategy. This labeler was re-engineered with PacDrive SCL integral servo motor/drive technology supplied by Elau Inc., in Schaumburg, Ill. These purpose-built servo modules were developed to make servo automation practical on machines with rotating carousels.
According to Yakama Plant Manager Jack West, the labeler must perform two to three changeovers per day on the line, running round 16 oz., 32 oz. and gallon bottles, plus rectangular quarts. Both glass and plastic bottles use full-wrap, hot-melt glue-applied paper labels.
Yakama is now making format changes in 15 to 20 minutes, which is a savings of 10 to 15 minutes per changeover. Changeovers now consist of selecting the image of the bottle to be labeled on the touchscreen human-machine interface panel, then dialing in the label stations and loading the magazines with the new labels. “You just push on the picture of the bottle you want to run, so language is not an issue,” West notes.
“When K2 said they could do everything on one machine, I was really impressed,” West relates. “Being able to handle glass as well—that was icing on the cake. We could even run the rectangular bottles faster if the volume on the line was higher.”
Sabel Engineering Corp., located in Sonoma, Calif., needed a new control platform for a newly designed robotic top-loading case packer. The new case packer has the flexibility to run a wide variety of cases and products, and sports a fast and reliable no-tool changeover system as a standard feature for simple, repeatable adjustments.
The most critical process of the machine application is the precise staging of the bags for the loading process. This was accomplished by using three conveyors driven by Acopos servo drives from B&R Automation, an Austrian systems provider with U.S. headquarters in Roswell, Ga. The first conveyor, a random feed infeed conveyor, transports the product toward the loading station and guarantees adequate spacing between the individual items. The second conveyor, the product positioning conveyor, indexes the bags forward and forms the products into groups of four, in this particular application. The third conveyor, the loading position conveyor, quickly advances the group of four to the pick station where the robotic arm loads the products into cases or bags. Although the three conveyors perform different tasks throughout this application, they are at all times synchronized with each other.
To accomplish this close coordination, designers used Ethernet Powerlink, a real-time Ethernet based communication protocol, to send positioning information to all of the drives. This architecture eliminates additional encoder wiring between the drives, reducing overall wiring complexity as well as troubleshooting time.
BENEFITS FROM NEW AUTOMATION PLATFORMS Better communication Faster throughput Greater reliability Tight integration with plant devices Supports digital fieldbus networks Increased control capability Improved automation performance Increased plant on-stream time Lower support costs.Sources: Invensys Process Systems and Nova Chemicals Corp.
For more information, search keywords “migration” and “upgrade” at www.automationworld.com.
See sidebar to this article: Best-in-Class Choose Integrated Platforms
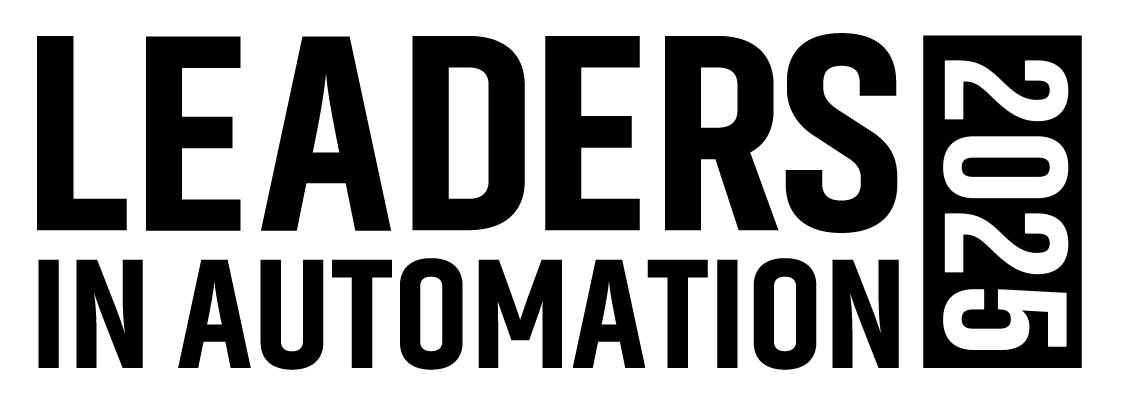
Leaders relevant to this article: