A discussion of the role of standards in packaging can sometimes seem like a cross between alphabet soup and Sudoku, a kind of number placement puzzle, what with IEC 61131, ISA-88, PackML and ISA-95 among those most frequently mentioned. But despite their apparent complexity, the potential impact of these and other standards is both simple and profound. At its most basic level, say industry proponents, the widespread adoption of open packaging industry standards will lead to higher levels of integration, improved responsiveness to customer demand and reduced cost.
According to Mike Wagner, business lead, global OEM team, for Rockwell Automation Inc., Milwaukee, it starts with vocabulary. He likens manufacturing operations to book publishing. Different books will have different tables of contents, indexes, chapter headings and the like. But those involved with book publishing know what an index or a table of contents is, and how they are supposed to be structured. Publishers don’t have to invent these things from scratch.
“Similar format rules apply to manufacturing suppliers, OEMs (original equipment manufacturers) and end users,” says Wagner. “For example, the ISA-88 standard follows the ‘state model,’ a manufacturing standard that uses a defined set of terms and definitions to describe the process being controlled. OEMs are not told what words to choose, but the state model defines the vocabulary so that original equipment manufacturers are speaking the same language and using the terms appropriately. This creates a predictable, reusable model that helps ensure consistency.”
The problem is that ladder logic is a time-consuming and less-than-capable tool for programming these more sophisticated machines.
ISA-88 is the brainchild of the Instrumentation, Systems and Automation Society (ISA). By establishing standard modes for describing basic states of machine operation (thus the term, “state model”), the standard has facilitated automated data transfer between machines, including machines from disparate vendors, in the batch processing sector. More recently, the state model has been enhanced with the development of PackML—Packaging Machinery Language. Created by the Open Modular Architecture Controls Users’ Group, or OMAC (now affiliated with the ISA), PackML adapts the state model to the specifics of packaging machinery, adding new data definitions, or pack tags, to describe the basic states that all packaging machinery undergo. Importantly, its consistent data format also makes integration with manufacturing execution systems (MES) easier.
Add to the state model concept the standard with the geekiest name of all—IEC 61131—and the efficiencies really begin to add up.
As packaging machines became more capable and complex, notes Tom Jensen, senior technology evangelist for Elau Inc., a Shaumburg, Ill.-based packaging controls vendor, “machine programs grew very large to articulate the new found sophistication of machines.” The problem is, ladder logic, which has been used for decades to program programmable logic controllers (PLCs), is a time-consuming and less-than-capable tool for programming these more sophisticated machines. And, because ladder logic programs are sequential, each segment of code is dependent on previous segments, so modifying a program is difficult.
“It was commonly realized that other languages may be helpful in describing these more complex ‘Generation 2’ machines. There were many languages available from the industry, but they all suffered from one of two conditions. The languages commonly offered on the market were either text-based or graphical. Text-based languages in general were capable of describing complex objects with much less code, but were not intuitive. This meant a programmer could actually create machine code that worked well and described how that machine should operate, but nobody without programming education would be able to work on the machine. Secondly, there were graphical languages. They were intuitive but lacked depth.”
LANGUAGE POWER
This is where IEC 61131 comes in. Developed in 1992 in Europe by the PLCopen standards organization, and promulgated by the International Electrotechnical Commission, it has gradually gained acceptance through the years. It defines a suite of programming languages; a ladder language called Ladder Diagram and Function Block Diagram are both graphical languages,while Structured Text and Instruction List are textual languages. The standard also includes a higher-level “organizing principle” for “modular” programming called Sequential Function Chart. Software objects containing subroutines for specific tasks can be written, tested and reused as standardized modules. Importantly, the standard also provides for the nesting of one language inside another.
Jensen provides an example of the power of the standard. “Let’s start with making a piece of modular code for a servo motor,” he says. “Once we model the servo in a Function Block and store it in a library, we can drop it into any other code module where a servo is needed. At this point we need to decide which language would be the best, and the obvious choice would be the 61131-3 language Structured Text, because of the mathematical demands as well as the complicated sequencing needed.
“Any of the standard’s languages will do,” Jensen continues, “but the goal is to reduce code. We will define a number of input and output variables to the Function Block we are writing, and set out. Even though we may have used different languages for the Function Blocks we’ve just made, we can call them into the next layer in whatever language we want. This means the servo object we made in Structured Text can be displayed as Ladder Diagram, creating a graphical representation of the machine that most technicians will be comfortable with.”
By using IEC 61131 languages with the ISA-88/PackML state model, says Jensen, you open the door to “documented engineering time savings of 70 percent to 80 percent by machine builders, better engineering collaboration between OEMs and specifiers, and ongoing reduction in users’ total cost of ownership through reusability, consistency, maintainability, mechanical modularity and execution speed.” In addition, validation savings of 40 percent have been documented in regulated environments, Jensen notes.
The problem is that ladder logic is a time-consuming and less-than-capable tool for programming these more sophisticated machines.
Standards promoting modularity have arisen in response to the growing sophistication of packaging machine design, and in turn are facilitating that sophistication. An example is the new Flexline from Hamba Filtec, a packaging machine builder based in Neunkirchen, Germany. Flexline, introduced last year in Europe, is a plastic bottle, cup, and tub filling and sealing machine. And like other so-called “Gen 3,” or Generation 3, machines, it relies on servo motors to achieve higher throughput and faster changeover than can be achieved by machines driven by a central shaft with mechanical linkages.
“A high end automation solution is essential to control such a flexible machine, one requiring up to 34 servo motors,” notes Uwe Gerasch, development manager for Hamba. “We simply implemented a completely modular control software structure with the help of...programming templates and software libraries.” The control system, which operates up to 1,000 distributed digital input/outputs (I/Os), employs a programmable automation controller (PAC) that integrates motion and logic control in the same IEC 61131-3-conforming program.
Packaging machinery builder Douglas Machine, Alexandria, Minn., has also benefited from software modularity. According to Joe Faust, electrical engineering manager for Douglas Machine, companies can reduce engineering costs and increase consistent quality through the use of libraries of tested, reusable, IEC 61131-conforming software modules that plug into a state model. Faust reports that for Douglas Machine, programming time was reduced at least by 50 percent (from 20 to 25 days down to 10), and program testing was reduced by approximately 80 percent (from 15 to 20 days down to just three to four). The savings potential was clearly derived from better software engineering, as the machine testing component remained unaffected at 15 to 20 days.
The shorter program development time and standardized program structure also helped Douglas Machine increase machine features. Faust notes, however, that there are upfront costs in a move to IEC 61131/state model modularity. The coded best practices, templates and software objects that save so much time must first be created. He says developing software for the company’s first modular machine took 100 days, plus 30 days of software testing, in addition to normal machine testing.
ADVANCING THE MODEL
Douglas Machine is committed to modularity; so committed, in fact, that it is involved, through the OMAC Packaging Workgroup, in the development of PackAL. Building on the PackML state model and IEC 61131 modularity, PackAL is an application library of common software elements used in packaging applications. It consists of twenty-three functions. Thirteen functions are machine functions, such as wind/unwind, dancer control, registration and indexing. Nine are communication functions for horizontal line communications, and one function is for the PackML machine state model.
“Version 1.0 of PackAL was released on March 29 of this year and vendors are beginning to implement it,” says Bill Henderson, marketing manager, vertical markets, for Norcross, Ga.-based automation vendor Siemens Energy & Automation Inc., and an executive board member of the OMAC Packaging Work Group.
“The benefits are considerable for both machine builders and end-users,” says Gerd Hoppe, chief technology officer of automation vendor Beckhoff Automation LLC, based in Verl, Germany, and chair of the technical committee overseeing the development of PackAL. “The organization of machine communication and commonly used functions facilitates seamless machine programming across control platforms and between machines from different vendors. The benefits are considerable for both machine builders and end-users. They are freed from unnecessary programming efforts, and more of their valuable time can become available for process-specific solutions.”
“With standard programming, companies don’t have to retrain their people for various machines, which helps lower their overall business costs.”
It’s not hard to see how these various standards fit together. “Convergence” is the term some in the standards community are using to describe the way that the different standards are beginning to fit together like pieces of a jigsaw puzzle, the intended picture being one of greater openness and reduced cost for OEMs and end-users alike. So far, however, the action has largely focused on improvements at the plant-floor level. That’s beginning to change, though, and the vehicle for that change is ISA-95.
The ISA-95 standard for Enterprise-Control System Integration was released in 2000, with additions published subsequently. It aims to facilitate the flow of data from the plant floor up through the MES space to the business, or enterprise resource planning (ERP), level. It does this in part by providing a lexicon of standard terminology so that the different levels can communicate unambiguously, and in part by providing a series of interfaces so that the different functional levels can, essentially, plug into each other.
GOING DEEP
In response to competitive pressures, management is striving to get data from deeper within the plant floor,” notes John Wenzler, food and packaging key account manager for Bosch Rexroth Corp., Electric Drives and Controls Div., a Hoffman Estates, Ill.-based vendor. “The information they need is available on the plant floor, but the challenge is to make sure they can get it in a timely manner. ISA-95 provides the handshake between ERP and factory floor systems, allowing that to happen.” In addition, Wenzler adds, because ISA-95-based interfaces are open, they keep users from being locked into a single vendor.
Allowing something to happen and actually having it happen are, of course, two different things. That was the case with ISA-95. After being promulgated at the dawn of the millennium, it languished, employed in a relative handful of applications. (Indeed, as one source remarked, you could almost hear engineers muttering, “What, another standard?”).
That began to change in 2004 when the German software giant SAP AG adopted it, and the legion of software companies that work with SAP began to incorporate it into their offerings. Now, to use a decidedly non-technical description, ISA-95 is progressing like a snowball rolling down hill.
Shawn Nelson, a sales engineer with Motion Tech Automation, a packaging machine distributor in Oakdale, Minn., is beginning to see the benefits of standards implementation in many packaging facilities he calls on. He cites the case of the IEC languages. “In our market locally, people are starting to recognize the value in having standard programming languages so that when they use products from different vendors, they don’t always have to reprogram. It’s like choosing a new brand of PC (personal computer) and knowing that [the Microsoft] Windows [operating system] is still going to run on it. And, if they’re more comfortable with programming in ladder logic, that’s still available to them, they’re just not locked into it.”
PEOPLE SIDE
Then there’s the people side of standards. “With standard programming, companies don’t have to retrain their people for various machines, which helps lower their overall business costs,” says Nelson. In today’s business climate, notes Bosch Rexroth’s Wenzler, that is more important than ever. “Because of the downsizing of engineering staff—both at the end-users and the OEMs—it’s critical that new people come up to speed quickly. Standards, and IEC 61131 in particular, help them come up to speed.”
“Still,” cautions Nelson, “in order for standards to really take hold, the vendors have to fully commit to open connectivity. If there is a standard but the hardware doesn’t comply with it, then what good is it?”
For more information, search keywords “IEC 61131,” “ISA-88,” “PackML” and “ISA-95” at www.automationworld.com.
Sponsored Recommendations
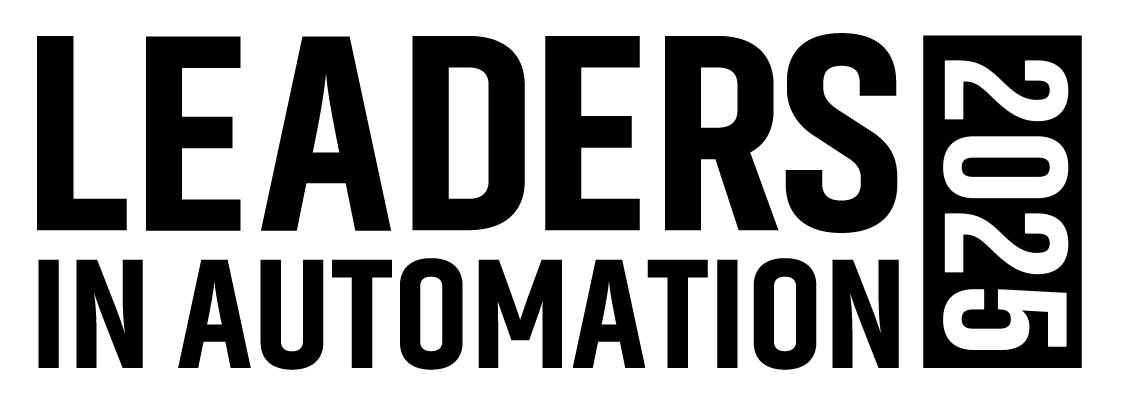
Leaders relevant to this article: