“Lean Manufacturing" has been taken to heart by both process and discrete manufacturing, though as with any manufacturing approach—at least any that is generally regarded as worth pursuing—the outline and details have gotten a little fuzzy through interpretation and individual differences in application.
Lean is an approach that neatly places the familiar needs of manufacturing—throughput, acceptable quality, cost containment and flexibility to meet more or less fickle customer desires—under a single set of corollaries: Do anything that will create value; stop doing anything that creates waste or fails to add value.
For the purist, it is the Toyota Production System (which, ironically, owes much to what people in 1915 were calling the Ford System). If you are among the rapidly dwindling group on the outside looking in, lean consists of a lot of promising tools and a handful of Japanese terms.
Delightfully simple
With all its apparent exoticism—and the millions of words expended on it—the concept of lean is delightfully simple. It is neatly summed up in the first words in the bible of lean, “Lean
Thinking: Banish Waste and Create Wealth in Your Corporation,” by James P. Womack and Daniel T. Jones:
“Muda. It’s the only word of Japanese you really must know....Muda means ‘waste,’... any human activity which absorbs resources that creates no value: mistakes which require rectification, production of items no one wants so that inventories and remaindered goods pile up, processing steps which aren’t
actually needed, movement of employees and transport of goods from one place to another without any purpose, groups of people in a downstream activity standing around waiting because upstream activity is not delivered on time, and goods and services which don’t meet the needs of the customer.”
Simple, yes, but lean is not generally quick to put in place. Two problems seem to beset unsuccessful or abandoned lean initiatives: impatience and rote reliance on the core set of tools promulgated by lean proponents. A fully lean enterprise can be years in the making (and very tough on short-term return on investment), and random or blind use of the tools—even the core tool of value stream mapping—will not automatically result in lean operations.
Forget comfort
Similarly, you cannot curl up in a comfort zone or enjoy long periods of repetitive activity—even though manufacturing likes repetitive activity. Somewhere, Hiroshi Okuda, Toyota chairman and vigorous proponent of lean manufacturing, has said, “Failure to change is a vice.” Continuous improvement—that is, continuous change—is central to lean manufacturing, and continuous change is in some ways a continuous state of agitation.
“But keep in mind, the whole reason for lean is not for the comfort of the manufacturer,” says Timothy A. Davis, Automation Group business systems manager for Parker Hannifin Corp., in Cleveland. “The real objective of lean is to earn value in the eyes of your customers.”
The $8 billion corporation is a keen advocate of lean, at least in the Automation Group, which makes a broad spectrum of electromechanical and pneumatic products, from fit-in-your-hand quick-connect air line components to fill-your-factory gantry robots and everything in between, including ballscrews, actuators and grips, linear motors and positioners. Not only is Parker an evangelist for lean, it has absorbed lean principles comparatively rapidly.
Parker makes a good study for lean. Over the years, it has engineered and manufactured an ever-expanding line of products. Over the long haul, it has delivered consistently well-received components to an extraordinarily broad range of customers, from automotive and aerospace giants, to major manufacturers, to midrange enterprises, to tiny job shops.
“Lean manufacturing is a key component of our three-pronged win strategy,” Davis says. “Our financial performance makes up the second. But the third is the overall driver—premier customer service. We made the transition to lean after 20 years of a type of continuous improvement that we called targets.”
Targets was an objective-driven initiative that singled out areas for improvement. Employees were encouraged to generate solutions. “It was good, and it was action-oriented, but it proceeded project-by-project,” Davis observes. “One positive aspect is that it encouraged improvements through employee empowerment and individual action. But it was a little random. That is, each project had its own rationale, with not a lot of reference to overall objectives.”
Parker decided to take a top-down approach to lean, an oft-repeated prescription for success in the philosophy. Don Washkewicz, chairman and chief executive officer, is himself a strong proponent of lean principles. Parker staff set out to learn as much as it could about the Toyota Production System. “The question was, where to begin?” Davis says. “We opted for a mass education program. From plant manager to line leader to machine operator, we tried to explain why we were looking at the Toyota system, why we were moving away from the targets approach.”
Identify causes
Early work with value stream mapping, which captures on paper what activities and information flows go into a given product, produced highly visible results at Parker. “Value stream mapping allowed us to identify underlying problems, and it helped make those problems solvable,” Davis notes. “It was a major step toward moving change objectives to a high, overall level, so that changes helped not only one work area in a local plant, but potentially everything in our systems worldwide. That approach is much different than applying a series of different solutions without defining the problem.”
Parker has taken its own lean thinking beyond the walls of its factories. “Parker has an overarching strategy to remain close to its customers,” Davis explains. “We’ve taken lean principles into a number of customer situations to find greater efficiency and economy in their systems and not incidentally to find our niche in their value streams.” Both internally and externally, Parker makes resources, training and engineering available to help bring about positive change.
Doubtless, Parker’s 20 or more years of targets, its project-based improvement initiatives, helped speed its adoption of lean principles. Without gainsaying the additional work involved, a lot of the company cultural aspects were already in place, including employee empowerment and problem-solving using multifunctional groups.
“Are we done?” Davis asks. “No. Lean thinking cannot be compared to a project with a completion date. Doing lean, by definition, means you’re still on a journey. There’s always something to improve.”
Not everyone can match Parker’s success. “Many lean programs are under water,” says Greg Bunting, business development manager for Citect North America, Alpharetta, Ga. The company, whose global headquarters are in Sydney, Australia, provides real-time manufacturing data systems and manufacturing execution systems (MES), which in the lean environment, provides numbers that are a useful backbone to value stream mapping, statistical process control (SPC) and a broad range of other manufacturing management needs.
By “under water,” Bunting means a lean initiative that has not yet shown a return on its investment (See “Cumulative Financial Benefit,” at top).
Find objective measures
Citect’s Ampla software system automates the gathering of production data from every programmable logic controller (PLC), control point and machine controller in an operation (and for larger customers, across multiple operations). Ampla then boils the data down into color-coded and charted information. It is especially useful in monitoring a plant’s overall equipment effectiveness (OEE), a metric that combines availability, performance and quality.
By increasing the visibility of production conditions, Ampla has helped a number of users at various stages of lean implementations, some dramatically. “Nobody would argue that actual machine-by-machine data is valuable,” Bunting says, “but the process of gathering it all can be pretty painful. One of our larger customers, Energizer, used to collect information byhaving operators note it down, then send someone around from machine to machine to collect the numbers. One plant’s numbers took 85 hours to gather. Automating the process [with Ampla] takes that down to a minute or two.”
The data itself often spurs improvements. Machine operators naturally tend to discount downtime and overemphasize uptime. Objective OEE numbers can reveal the actual number and types of nonproductive events, enabling targeted problem-solving to improve processes. “Our objective is to get the right level of data to the right people,” Bunting says. “This data can be formatted in a range of depth, from high level summaries on visual dashboards, to line-item lists that permit drill-down to almost any level of data that an engineer might need.”
One ramification of lean that has generated more than a little discussion is the role of automated assembly and processes in lean manufacturing. Dedicated assembly machines are especially difficult to justify in a system that continually changes, because there is no way to predict the extent of machine rebuild that might be required to accommodate later improvements. The obvious answer, flexible automation (anything and everything from work cells built from standard extrusions to robotics), continues to compete with manual labor.
To an extent, this dialog reflects a certain tension between manufacturing operations and business management. Bashar Abdo, product manager, cartesion robotics, at Bosch Rexroth, in Hoffman Estates, Ill., feels that lean will always be under threat from the quick-fix mentality, especially when paired with a narrow view of cost savings.
“Lean benefits from the perspective of the manufacturing or industrial engineer,” he points out. “That person knows set-up, knows the technical side of production flow, knows how to balance labor and machinery for throughput. If the front office is ignorant about how manufacturing works, this position can look like waste. But when you trim that job, you jettison valuable insights that are central to lean.”
Instead, he suggests, the most balanced application of lean principles will allow for an appropriate mix of investment in automation and investment in people.
In the final analysis, any flavor of lean thinking that can balance human resources (and needs), intellectual capital and production equipment will provide a good return—assuming it can be pursued long enough to penetrate into the core of the company. And, given sufficient planning, it can provide a solid infrastructure for future operations. All it takes is a relentless ability to see the real causes behind less-than-optimal throughput.
For more information, search keywords
“lean manufacturing” at www.automationworld.com.
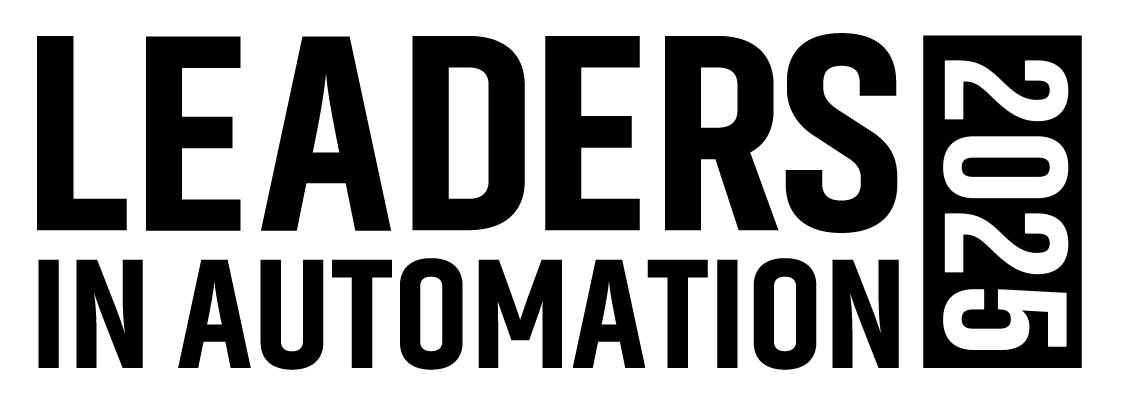
Leaders relevant to this article: