With customers demanding higher product quality than ever before, technologies that facilitate quality control and deliver comprehensive track-and-trace capabilities have become critically important to production and packaging operations—especially in today’s highly automated manufacturing facilities.
At the forefront of this trend are intelligent sensing systems such as machine vision, radio frequency identification (RFID) and bar code systems that record and track key information about the batch or product. There is a veritable ton of data about each widget that comes off the production line that in the past was usually ignored, or even discarded, because systems were manual and no one had an efficient way of turning it into actionable information. That’s no longer the case.
Now these sensors are being wired up to a network—usually with Ethernet—and data about the conditions they monitor are being collected so they can be accessed at any time in the future to facilitate product recalls.
“The information getting tracked will vary by the product, but essentially, it comes out to everything about the product,” says Craig Resnick, research director at a Dedham, Mass.-based research firm ARC Advisory Group Inc. “For example: what’s in it, the ingredients including allergens, all real-time quality and safety information about the product as it was being produced, and all the information about the performance of the production line.”
According to Resnick, this kind of information is critical to a company’s manufacturing and packaging operations, especially in heavily regulated industries such as pharmaceuticals, food and beverage, and automotive.
Larry Luciano, president of Luciano Packaging Technology Inc., agrees, adding that more stringent Food and Drug Admnistration (FDA) requirements—such as the Bioterrorism Act, which demands crisis response within 24 hours—is driving increasing demand from pharmaceutical, and food and beverage industry customers for systems that reliably provide product history.
“There’s a lot of demand for it,” says Luciano. “Everyone I’ve talked to in the industry really needs this [capability].” Luciano Packaging is a small designer of custom packaging lines, based in Somerville, N. J., and does a lot of work with machine vision and bar code systems.
“These technologies put unique identifiers on each package. Then the key production information is stored in a secure database, which is linked to the identifiers so the products can be traced through the various levels of distribution to the consumer,” says Luciano. “Anywhere you need a lot of control, where you are worried about counterfeiting, like in pharmaceuticals and automotive, it’s a need.”
Rfid
RFID technology is based on memory-equipped tags that carry either product data or a pointer to the same data stored in a secure database much like that used in a bar code system. The tags are placed on products or in cartons, and can be read by scanners from a distance that pull the data and use it to verify a host of important elements, including location, contents, product history and whether the part is defective or not.
RFID is being pushed hard by retailers such as Wal-Mart, as well as by the U.S. Department of Defense, for logistical applications. But ARC analyst John Blanchard doesn’t expect it to become market-dominant any time soon. “RFID is going to take a long time to be pervasive,” he says. “There are a tremendous number of infrastructure issues. Most people don’t have the infrastructure to handle this massive amount of data. It will slowly mature on a product-by-product basis.”
When RFID is used in factory automation, tag ruggedness is an absolute requirement, says Helge Hornis, intelligent systems manager, for Twinsberg, Ohio-based Pepperl+Fuchs Inc. “They need to last for years. A fault can have a very high financial cost associated with it. For example, putting the wrong engine in a car increases scrap.” Pepperl+Fuchs supplies sensing systems, including RFID, for factory automation uses and offers more than 10 different tags with varying memory capabilities for different applications.
There is a broad range of RFID applications that are possible in the plant setting, says Hornis, from carrying recipes for process steps to logistics improvement. “It covers the whole spectrum. That won’t change. The technology is there for that.”
One of the key values that RFID delivers is constant monitoring and recording of what happens to a given product as it travels down the line. “At each stage of a multi-step manufacturing process, value is added to the product. But if there is a failure at step five, then you don’t want to add more value to that product. A tag can be associated with a ‘good part/bad part’ signal, and either processed or passed through as something that’s already scrap,” adds Hornis.
Machine Vision
Machine vision has been around for a long time, and is commonly used in many industries for optical character verification of human-readable data such as the date, lot codes and expiration date on drug labels. But new FDA bar code regulations are demanding higher standards, and manufacturers in the pharmaceutical, and food and beverage industries are being driven to adopt more and more sophisticated solutions to meet them.
According to Bryan Boatner, spokesperson for Cognex Corp.’s vision sensors business unit, in Natick, Mass., machine vision systems are essentially “computers that can see.” They analyze images to visually monitor what’s going on at specific points along the line to guide manufacturing. They are typically used to verify label presence and skew, cap presence and position, package integrity and print presence, for example, and for print quality inspection, date and lot code verification, safety seal presence, fill level detection, package color and shape sorting, and to count cycles.
“We see packaging operations applying machine vision in two ways. The first is for inspecting and rejecting bad product at various stations along a single line. The second way involves networking vision sensors across multiple lines for process control and optimization,” says Boatner. “Ethernet provides higher-level computing system access to plant floor data. By linking enterprise-level networks with production control and device networks, Ethernet allows intelligent control devices to share information required for tasks such as automating production line changeovers.”
There are a couple of major trends driving the adoption of machine vision in packaging, says Mark Langridge, packaging market manager for Minneapolis-based Sick Inc. which provides machine vision and bar code systems. The first is an overall increase in factory automation.
The other major trend is worker safety, adds Wayne Meyer, Sick’s product manager for industrial sensors. Sensors are set up in places where someone could be injured by machinery, and are programmed to shut the machine down should their field of view become obstructed by something, such as a human limb.
According to Boatner, machine vision technology is increasingly being used to read bar codes and 2D matrix codes, and networking is a key ingredient in traceability applications.
For example, automotive body parts are stamped out of sheet, but rolled steel is not continuous. It is typically made up of sections welded together. The weld compromises the quality of the steel, and additionally places a lot of pressure on the press, and can even damage a press. Automakers therefore want to avoid stamping a piece that contains a weld. A machine vision application will continuously examine the steel, looking for welds. When it sees one, an output fires, and the weld is cut out and scrapped.
“Everyone started to implement the 2D systems a year or two ago and now we’re starting to see them used in different ways,” says Mike Muldoon, vision department manager for Radix Controls Inc., an Oldcastle, Ontario, Canada-based process improvement company. “We’re starting to see them using the data.”
Another typical application that drives value for the extended line is to set up a camera on a bottling line. The camera captures an image of each bottle as it passes and measures it against a set of acceptable parameters, such as fill levels, cap seal, and label presence and skew. If any of these parameters are found to be out of specification, a signal can be sent to the next step in the line to divert the bad bottle into a scrap bin. Additionally, an image of the scrap bottle can be saved to a database for analysis.
“Engineers can look at images for root cause analysis,” says Boatner. “They don’t have to go down to the reject bin and try to figure out which ones came from which line.”
Bar Code
With a bar code system, everything about a given product is encoded in a device-readable pattern that then acts as a pointer to the full work-up in a secure database.
Procter & Gamble’s Iowa City, Iowa, plant produces hair care products and mouthwash, and uses a mix of large and small bar code printers from Wood Dale, Ill.-based Videojet Technologies Inc. to label both the bottles and the cartons they are shipped in.
“We use the printers for day codes on the bottles. This gives us data right on the bottles for traceability throughout the greater distribution network all the way to the consumer,” says Casey Waechter, process engineer for P&G.
“The code is linked to the exact run—where it was made, and everything that was happening on that day, from what went into it to who was working. Everything comes together in that code.”
In general, the future of product traceability will rely on a blend of technologies, Waechter says. “They will run in parallel. Even as RFID becomes more mainstream, the smaller parts of distribution channels will still need the bar code technology.”
The major drawback to bar code systems is the line of sight requirement. You can’t read a code if you can’t see it. This adds to the challenge posed by smudged or otherwise unreadable codes.
There are literally dozens of different sensing devices at the machine level in both process and discrete manufacturing operations that measure all manner of things about the product and manufacturing process. Industrial sensors reliably sort, count, inspect, measure, recognize and verify the position, size and overall shape of objects.
Some of these sensors provide information back into the process, but the vast majority do not, says Luciano. In most cases, there is simply no need to track the data they are sensing, so instead, they fire off a simple accept/reject signal.
“Intelligent sensors can create the ultimate level of production efficiency for a fully automated manufacturing facility,” says Lyndon Smith, divisional director of quality for automotive parts supplier Freudenberg-NOK, in Plymouth, Mich. “Intelligent sensors make sure you have the right part at the right place at the right time.”
For more information, search keywords “intelligent sensing” at www.automationworld.com.
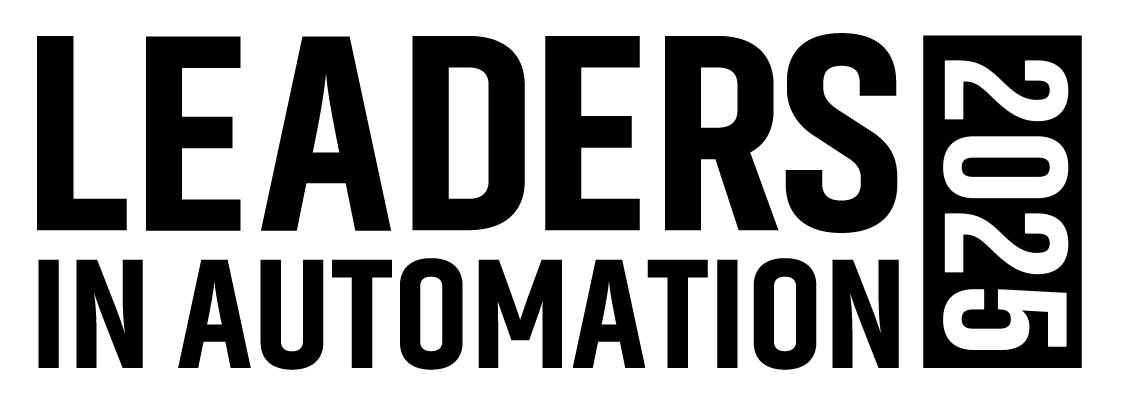
Leaders relevant to this article: