When Wayne Manges talks about industrial wireless networking, he sometimes paraphrases Charles Dickens. In the wireless business today, “it’s the best of times, and it’s the worst of times,” says Manges, who serves as co-chair of the Instrumentation, Systems and Automation Society’s (ISA) SP100 committee, formed early this year to develop an industrial wireless networking standard.
“It’s the best of times, because you’re seeing more and more checkbooks open,” says Manges. He notes that electric power plants, in particular—both nuclear and fossil fuel—are currently among the most enthusiastic adopters of wireless technology. “These guys are buying wireless today, and they’re getting ROIs (returns on investment) of six months,” Manges contends. The Comanche Peak nuclear power plant, near Glen Rose, Texas, is “the largest industrial wireless sensor installation in the world right now,” according to Manges, who is program manager for industrial wireless programs at the U.S. Department of Energy’s Oak Ridge National Laboratory, in Oak Ridge, Tenn.
The flip side of the story, however, is that industrial users in many segments are still holding back from making extensive, in-plant wireless investments. Concerns over reliability, security and the lack of an industrial wireless standard are the most often cited causes. “The bad news is, we’re still seeing failures. There are still horror stories out there where somebody’s microwave oven comes on at lunch time and wipes out the entire [wireless] network. So part of our purpose in developing standards is to overcome some of these obstacles,” Manges observes.
Industrial end users looking to implement wireless networks in their plants today face a dizzying assortment of technology choices, ranging from the Institute of Electrical and Electronics Engineers’ family of IEEE 802.11a/b/g standards, to short-range Bluetooth systems and self-organizing mesh networks based on the ZigBee specification or other IEEE 802.15.4-based approaches. That’s not to mention a collection of proprietary vendor solutions for use on 400 Megahertz (MHz), 900 MHz and 2.4 Gigahertz (GHz) bandwidths.
The SP100 committee is tasked with making sense of it all, based on end-user requirements, and is developing standards, recommended practices, technical reports and related information that will define procedures for implementing wireless systems. The committee expects to release initial documents for industry reaction and use in early 2006, and “we’ll probably have a draft standard in the fall,” says Manges.
Why wireless?
The potential benefits of wireless technology in the factory are compelling. The most obvious advantage is the often dramatic savings that comes with the elimination of wiring installation costs. These can run anywhere from $10 to $40 per foot up to hundreds or even thousands of dollars per foot, say industry sources, depending on the type of installation. Other benefits accrue through the improved mobility achieved both for mobile equipment and for workers, who no longer have to be tethered to communicate or exchange data.
Less obvious are the new kinds of applications that wireless technology can enable. “It’s not trying to take a wired piece of equipment and make it wireless, it’s trying to figure out what you can do that you couldn’t do before, now that you have wireless,” notes Richard A. Sanders, an engineer at ExxonMobil Research and Engineering, in Fairfax, Va. “When you look at it that way, you can find a lot of advantages to wireless and a lot of applications that maybe you never thought of before,” says Sanders, who co-chairs the SP100 committee with Manges.
Gabe Sierra agrees. “One of the key things with wireless is that it requires a new kind of thinking, because you’ve literally changed the game on what you can do and what’s possible,” says Sierra, who is wireless marketing manager for Emerson Process Management, an Austin, Texas-based process automation supplier. Sierra cites wireless temperature monitoring on a steam line as one example of an application not typically done using wired technology. “Because you can cost-effectively install wireless points, you can monitor the steam pipeline over the course of a distance to find pockets of condensation, allowing you to take appropriate corrective action,” he notes.
Emerson currently offers wireless products designed for remote monitoring and long-haul communications, and is working with multiple customers on field trials of various wireless technologies, including so-called “mesh” or “self-organizing” networks for in-plant applications, Sierra says. The company is participating in SP100 activities, and is also working closely with the Hart Wireless Working Group, which is developing a wireless standard that will feature self-organizing networks as a major foundation, according to Sierra. Emerson is probably about 12 months away from introducing a self-organizing network product, he allows.
EPRI jumps inRamesh Shankar, senior technical manager at the Electric Power Research Institute (EPRI), in Charlotte, N.C., agrees that wireless technology can offer significant cost savings and operational advantages. The cost to install wiring in a nuclear or fossil fuel-powered electric plant is “prohibitively high,” he says, ranging from $1,000 to $5,000 per foot, “so wireless seems like a good alternate solution.”
During the past two years, EPRI, a nonprofit center for energy and environmental research, has worked in partnership with various electric utilities in the installation and evaluation of wireless equipment monitoring technology. The goal is improved reliability, availability and maintainability of both power generation and transmission facilities, Shankar says.
One facility where wireless technology is so far proving its worth is the Comanche Peak Steam Electric Power Station, a two-unit nuclear-fueled power plant about 85 miles southwest of Dallas. Operated by Dallas-based TXU Corp., the Comanche Peak Station earlier this year completed Phase 1 of a demonstration project—in partnership with EPRI—involving wireless equipment monitoring.
For the project, the plant installed 55 wireless sensors on generation-critical equipment, including pumps, motors and turbines, in the Comanche Peak Unit 2 building, says Clinton Carter, manager of TXU’s Power Optimization Center, in Dallas. The sensors monitor vibration and other parameters and transmit the data wirelessly to access points in the plant that are linked to a fiber optic backbone. This backbone ties to the plant site’s local area network, enabling plant technicians to access the sensor data for predictive maintenance analysis.
The wireless monitoring system—supplied by Azima Inc., a Woburn, Mass., provider of wireless monitoring and predictive maintenance systems and services—is based on the IEEE 802.11b standard, also known as Wi-Fi, for Wireless Fidelity. As such, it can integrate onto the 802.11b wireless infrastructure installed earlier at the plant to support wireless voice communication and other applications.
This infrastructure includes about 400 wireless access points installed throughout the entire Comanche Peak campus to provide 100 percent coverage, says Carter. “We have several hundred wireless VoIP phones (for voice over Internet protocol) that are deployed at the Station now, and we have piloted [wireless] IP video surveillance monitoring,” he notes. The Wi-Fi system also enables mobile computing throughout the facility. All of these applications, as well as the Unit 2 sensor monitoring system, run on the same 802.11b wireless infrastructure. “The idea with installing 802.11b was that it’s flexible,” Carter explains. “It’s a single platform that lets you do voice, data and video.”
As for the wireless monitoring system, Carter emphasizes that the Comanche Peak facility “does not take any operations- or maintenance-related actions based solely on the information provided by the wireless monitoring of plant equipment. This is strictly a non-intrusive plant information system to provide enhanced information to the plant staff for identifying potentially degrading equipment that can proactively be addressed prior to experiencing equipment or component failure,” he says.
Carter notes that TXU is so far satisfied with the performance of the wireless monitoring system. The Phase 1 demonstration in Comanche Peak Unit 2 wrapped up last February, and EPRI is planning a Phase 2 study next year to look at the long-term performance of the system, according to Shankar. Meanwhile, TXU is making plans to replicate the sensor system installed on Unit 2 in its Unit 1 building, starting early next year. The eventual goal, says Carter, is to eliminate the current system of manual data collection at Comanche Peak in favor of wireless sensor monitoring.
The potential advantages are several. With the current manual approach, the plant’s predictive analysis experts must spend about half of their time collecting data individually from each piece of equipment, leaving them too little time to analyze the data, Carter notes. Further, the staff walks a monthly route. “Once they collect their data, we don’t see that piece of equipment again for another month, so we’re getting these very infrequent snapshots,” he observes.
The wireless system, by contrast, collects and transmits data on each piece of equipment twice daily, producing a 60-fold increase in monitoring frequency, Carter points out. That means that wireless data monitoring could not only produce large, meaningful data sets for analysis much more quickly than the manual approach, but it could also free up more staff time to perform the analysis, because staff would no longer be required to walk the data collection routes.
Before manual data collection can be replaced by wireless monitoring at the plant, however, the staff must complete a thorough engineering evaluation of the wireless system, comparing the quality and reliability of the wireless data to that gathered manually. “We think the wireless data is good, but everything in a nuclear plant has to be analyzed and documented,” Carter explains. That evaluation project is “something we’ll be working on in 2006,” he says, and if the project pans out as expected, the phase-out of manual data collection routes could begin later next year.
In a few instances, the Comanche Peak staff has already made good use of wireless monitoring data. In one case last year, for example, personnel noticed some unusual sounds coming from the main turbine in the plant’s Unit 1 building. “We were sending people out twice per shift to listen to the sound and collect acoustic information to see if it was getting worse,” Carter notes. “And it occurred to us that we could take some of the wireless sensors that we were using on Unit 2 and put them on the Unit 1 turbine to monitor for changing conditions. Because we have 100 percent coverage, getting a network connection wouldn’t be a problem.”
That idea panned out. “We were able to deploy the sensors in a very short period of time,” says Carter, reducing the need for extra manual monitoring of the turbine. The staff used the wireless monitoring data to keep tabs on the turbine until time for its regularly scheduled maintenance outage.
Going forward, Carter says Comanche Peak expects not only to eliminate today’s regular manual data gathering routes, but also plans to take advantage of the ease with which the wireless sensors can be installed. Plant staff plans to have sensors and equipment available on a “crash cart” that can be rolled to potential trouble spots. “Where a problem emerges in the plant and we need to enhance our monitoring for a period of time, we can go out and rapidly instrument that piece of equipment, and put it online with the other pieces of equipment that we monitor,” Carter explains.
A bigger picture
Just as Comanche Peak chose 802.11b as a way to integrate multiple applications on a single wireless infrastructure, so too are other companies looking at similar standards-based strategies. Raj Rajani, product marketing manager, network infrastructure, for automation vendor Siemens Energy & Automation, in Norcross, Ga., notes that “several of our customers have asked us to show them how our wireless products work in the office environment, as well as the factory floor.”
Many customers are “thinking about a much bigger picture” than just a single industrial wireless application, adds Jeff Howe, Siemens business manager, networking products. These customers may be “starting out only doing monitoring,” Howe says. But they want a wireless infrastructure in place that can handle more. “They’re saying, ‘I want to be able to support voice, because down the road, I might have my maintenance guys out there with not only handheld devices, but also VoIP telephones. And I don’t want to have to put in separate wireless networks to handle that,’ ” Howe relates.
In response, says Rajani, Siemens has been expanding its wireless industrial product line beyond proprietary 900 MHz technology to include 802.11 frequency bands. Networks based on 802.11b and 802.11g use the 2.4 GHz band, while 802.11a uses the 5 GHz band.
Nonetheless, proprietary products today still account for a significant chunk of wireless industrial applications. One company that recently began using a proprietary wireless system is ZLB Behring LLC, a plasma-based pharmaceutical manufacturer based in King of Prussia, Pa. The company’s manufacturing site in Kankakee, Ill., was looking for a way to automate the level measurement process for 12 large tanks that store ethyl alcohol used in its production process, says Jeff Dabney, senior process controls engineer.
“We had operators who had to go out and measure how much was in each tank,” Dabney explains. That process required about an hour’s worth of work each day, and was seen as a safety hazard, given the explosive nature of the alcohol, says Dabney. In addition, due to U.S. Environmental Protection Agency restrictions on alcohol emissions, the company wanted to eliminate the need to open the tanks daily for measurements.
To solve the problem, ZLB turned to the XYR 5000—a wireless sensor monitoring system supplied by Phoenix-based Honeywell Process Solutions that relies on proprietary 900 MHz frequency hopping spread spectrum technology.
Thousands saved
By installing an XYR 5000 wireless pressure transmitter on each of the tanks, Dabney figures the company saved $4,000 to $5,000 in wire and cabling costs that would otherwise have been needed to link the tank farm to the ZLB Behring plant about 300 feet away. The cost of the wireless solution was about half that of a wired solution, he estimates.
Compared to the once-a-day manual measurements before, the wireless system transmits tank level data every 30 seconds to a base station in the plant that links through a programmable logic controller to a display where the data can be viewed. “It helps clear out the operators’ time and lets us control our inventory a little better,” says Dabney.
Dabney says the company has so far been pleased with the wireless system, and now plans to deploy the technology for other, process-related applications in its plant. “This is something that could really save us a lot of money and a lot of time going forward,” he concludes.
For more information, search keyword “wireless” at www.automationworld.com.
Sponsored Recommendations
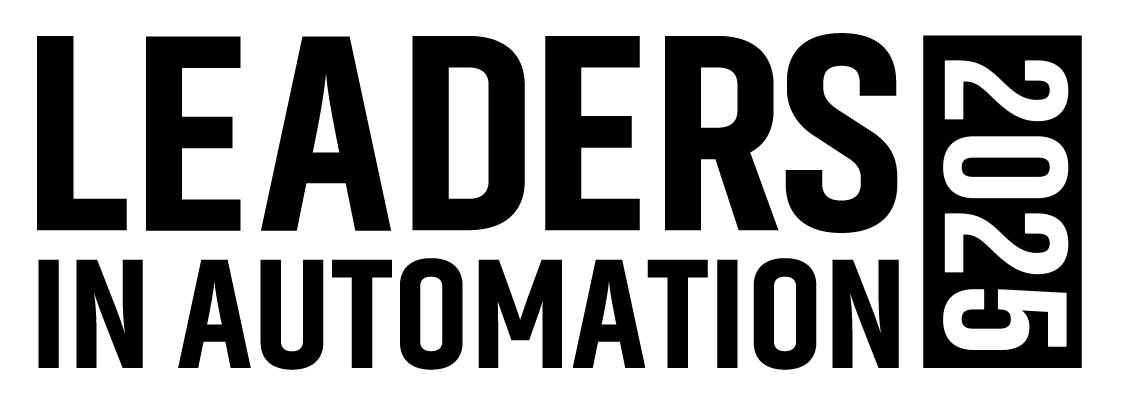
Leaders relevant to this article: