Bringing customers into the factory to talk with employees can be an eye-opening motivational experience. But imagine if your customer was a soldier in the U.S. Army who said that if your product hadn’t worked the first time he used it, then the soldier wouldn’t be standing in your factory that day. Such an experience would likely provide a powerful incentive to employees to live up to your company’s corporate dictum of “Mission Assurance—No Doubt.”
Indeed, bringing in such “customers” helps everyone at Raytheon’s Integrated Air Defense Center (IADC) plant in Andover, Mass., stay focused on the importance of their work. IADC manufactures sensors and control systems for defense and aerospace industries. Perhaps the most well-known of its products is the Patriot missile system.
Lean manufacturing team members discuss how the entire plant came together to implement a manufacturing system to reach the “No Doubt” goal. And if some think that new manufacturing initiatives cannot be successful in a plant with unionized employees, think again. This plant has about 1,500 members of the International Brotherhood of Electrical Workers (IBEW) or International Association of Machinists and Aerospace Workers (IAMAW) unions out of a plant population of more than 4,000.
The implementation team includes Bruce Hunter, director of strategic operations; Peter Kampf, strategic partner, mission integration; Joan Holman, strategic initiatives; Dick Schuler, director of lean implementation; and Paul Heller, customer focused marketing. The plant was awarded the prestigious Northeast States Shingo Prize for excellence in lean implementation in September 2005.
Besides motivating union workers to pull together for a common cause, further benefits realized from lean implementation included reduced cycle times and increased yield due to combining islands of automation into a cellular flow, says Hunter.
According to Kampf, the lean project at Lockheed was initiated at the behest of customers. “It’s essential that IADC products work the first time, every time,” says Kampf. “So we engaged our customers to discover just what they wanted. It became overwhelmingly clear that what they expected from suppliers was lean manufacturing. The Army has a lean enterprise goal. The Navy is talking about ‘lean carriers.’ It is all about getting rid of waste. The forum we held for a couple of days with these customers was a call for action. We needed to adopt lean thinking if for no other reason than reducing waste in our processes. But this was also a tactical approach for us to reach Mission Assurance.”
Once IADC managers realized the importance of lean thinking, they set out to identify the gaps in their processes and to investigate industry best practices. They found a sister Raytheon group in Tucson with a lean-thinking initiative already well under way. The Andover group took the Tuscon group’s tools and altered them to fit the needs of the Massachusetts plant.
Schuler, who heads the lean office in Andover, says they learned early on that having a dedicated office to assure the message gets out, and to provide a constant push, was essential for success. Further, adds Schuler, “In our minds, integrating lean strategies into a facility of 4,000 needs a team approach.”
As part of the best practices investigation, IADC derived a measurement and evaluation model from aerospace manufacturer Boeing, as well as a Lean Aerospace model developed by the Massachusetts Institute of Technology. They asked the Tucson group to evaluate their lean gap analysis and plan. Then they began contacting consultants for help. Other resources included the Boston Manufacturing Partnership and the Lean Enterprise Institute. They also began performing self-assessments.
Training was a crucial element and was done as part of an immediate assessment and planning event held right at the work center. “We wanted to avoid ‘Raytheonizing’ the training process, but instead to use well-proven lean training tools,” says Schuler. “But the real key to success was in energizing the entire workforce. There are daily cell team meetings so that everyone’s ideas are part of the process. We spend a lot of time with consultants, but it’s all about the people. They understand that we support the war effort and the importance of ‘Mission Assurance—No Doubt.’ ”
Obtaining “buy-in”
According to Holman, “The main challenge was obtaining total employee involvement. We needed them to buy into the program. This had to begin with training and education—the what and why of the program. We spent time with management getting them to help communicate why this initiative was important. We reminded everyone who our customers were during the war effort. We had lots of pictures put up and brought in soldiers to speak to employees. And this is total employee involvement.
Summarizes Schuler, “The true benefit was transforming our culture from an activity-based focus to a results-based one. Perhaps the biggest benefit was how we think about problems. We have been able to do more with less space and cost. On one production line, costs were cut by 25 percent to 30 percent as a result of using lean thinking.”
“Lean manufacturing, in a nutshell, is the endless pursuit of eliminating waste. Waste is anything that adds cost, but not value, to a product,” states John Allen, principal at Total Systems Development, a Louisville, Ky., manufacturing engineering consulting company. Some examples of waste include defects, waiting, motion, over-processing, over-production and inventory inefficiency, according to Allen.
Lean thinking has its roots in manufacturing, evolving from the Toyota Production System championed by Toyota engineer Taiichi Ohno. Practitioners have taken the concept far from its automobile production beginnings. Proponents maintain the concept is useful for almost any process.
While there are consultants who maintain that lean manufacturing applies only to manual tasks, John Coolidge, vice president of manufacturing for Aspect Medical Systems, in Newton, Mass., has applied lean thinking to automation.
“Our vision statement is any operation is set up as a pull system linked to customer orders and shipment,” says Coolidge. “We use kanbans between linked processes. (A kanban system is a material control system in which work centers use visible, physical signals to initiate manufacturing and movement of material.) Each process is surrounded by visual factory tools—there’s a place for everything and everything in its place. We are a regulated industry, so the plant has always been extremely clean.”
Pure lean thinking implies a one-piece workflow with no buffered work-in-process inventory. Coolidge maintains that it’s not realistic to get all of the buffer out. Practioners may need about five to ten minutes time to resolve problems that occur.
There is some automation in the Aspect plant. Coolidge defines two types of automation—synchronous and non-synchronous. In synchronous automation, several machines are linked. With non-synchronous automation, people pace the machines. Because operators have control over their own operations, they are happier with their work and are more efficient. People have more control over their jobs, but still have work standards. And they will try to improve when provided with the tools they need, Coolidge asserts. Aspect brings in Kaizan, or continuous improvement practices, using teams to focus on a problem to create a solution for driving further inefficiencies out of the process.
The most common failing in implementing lean thinking in an organization, according to Coolidge, is lack of management support. “Unless lean is pushed by management, it can become a second priority, because people are very busy. Lean takes a lot of work. Management must create a sense of urgency around continuous improvement. Early in my career, I didn’t worry if the process was working. I only worried when it broke. Now, we’re much more proactive, continually searching for ways to improve things.”
Respect for humanity
Steve Thompson is chair of the consortium formed by the Society of Manufacturing Engineers (SME) and the Association for Manufacturing Excellence (AME) for the development and administration of a new Certification in Lean Enterprise program. In his day job, Thompson is lean engineering site manager for the Puget Sound, Wash., Boeing plant. He has been doing lean for ten years.
“Too many people have downplayed that lean thinking is useful throughout an enterprise. They promote it as a manufacturing solution because that’s a more tangible area. Lean is not just a toolbox, strategy or even a set of principles. It’s the whole set of that, plus a culture shift—about developing people. As [lean founder] Ohno’s dictum goes, have respect for humanity. You’d better respect people if you want them to stay the course. They’ll save you some money, but they won’t change their behavior. You really are trying to change the world. This almost takes on a religious feel. You’ve got to be passionate about lean.”
As far as practical advice, Thompson suggests starting with mechanical things and to start at the shipping dock. “That’s the spot where you’ve invested all your money in the product. Then go through the back door into the factory. Look for things that cause waste and cost. Identify things you want to change. Ask what its impact is on throughput. Automation is fine as long as it doesn’t affect cycle time. Sometimes automation isn’t very flexible, so when you design automation in, use a modular approach. Automated transfer lines are too confining. Make it modular and right-sized. For example, we had some very big punch press dies producing small parts. Why? Because small dies would be crushed by the size of the press. Solution, put them in smaller presses and right-size the dies. Now a 20-pound die can be set up by one person easily, rather than trying to wrestle with a 100-pound one.”
One lean tool is known as “5S.” The five organizational tools beginning with the letter “s” are sort, stabilize, shine, standardize and sustain. These form part of the “visual factory” that includes ways to organize a workplace such that things are found easily, and even to reduce dependence on language to find and do things—using pictures instead of words.
Gary Smuda, director of duplication services for the Livonia, Mich., plant for Technicolor, has a lot to say about the visual plant. Imagine a workforce composed of recent immigrants with almost no ability to read, write or speak English. Imagine further these people working in a plant where the product is duplicate video tapes of movies, where it is imperative that the correct label be applied to the cassette. For example, someone who purchased a Disney movie would be shocked, to say the least, if they popped it into the VCR player and saw an adult movie.
Smuda says his boss selected him and another manager to attend the University of Michigan College of Engineering Center for Professional Development’s Lean Certification program.
He credits the five-day “The Lean Experience,” a class by the Lean Learning Center, in Novi, Mich., for providing the education and tools needed to bring lean thinking back to Technicolor. “If you really want to be like Toyota, you need a culture of trust—a management philosophy of coach and teacher, rather than dictator. Ohno’s philosophy is to go to the factory floor to fix problems. Since management and employees could not communicate with each other, either verbally or in writing, we had to rely on pictures. Following Ohno’s principle, we went to the factory and made a fixture to train the employees. Operators learned much more quickly and became so enthused with the system, they starting coming up with more pictures to help improve the process.”
Visual factory
Smuda applied 5S and visual factory in one area and cut problems in half in just the first five months. That sold the rest of management on the process.
Smuda has gone from skeptic to believer in lean. “I’m convinced that it works. I never preached a management philosophy until this, and I never dreamt that I’d be involved in SME activities after work.”
One story that is a work in process rather than a success story is the crusade Gary Gathen, president of G Corp., in Pleasant Ridge, Mich., is on to find a way to cut stamping costs using lean principles. The trouble he has found is that the culture and processes of tool and die shops is quite different from that of automotive plants.
“A customer gave me a copy of ‘The Goal’ by [Eliyahu] Goldratt years ago when I was searching for ways to cut costs in stamping dies. The trouble is that this business is not repetitive like other manufacturing. Then I read about the Shingo Prize, the Toyota Production System, and Ohno and others in the lean area. That has started me working with the SME Lean Tool & Die Machining Group. There are companies beginning to understand that lean is not just another fad like QS-9000 (a quality standard). You do this for business reasons. We are beginning to see some small shops adopting lean, perhaps without even realizing it. Our goal is to make this segment of manufacturing more competitive.”
For more information, search keyword “lean” at www.automationworld.com.
Sponsored Recommendations
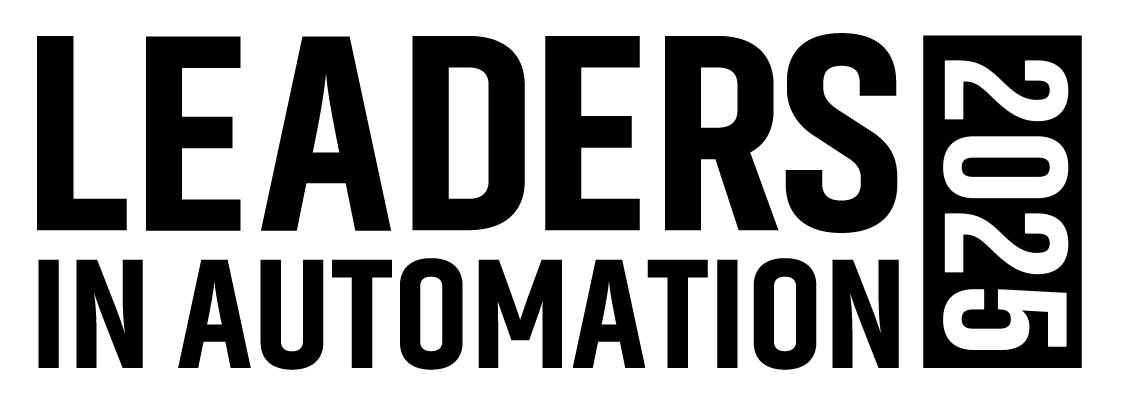
Leaders relevant to this article: