"One reason the Military has trouble operating jointly is that they don’t speak the same language. For example, if you told Navy personnel to “secure a building,” they would turn off the lights and lock the doors. Army personnel would occupy the building so no one could enter. Marines would assault the building, capture it, and defend it with suppressive fire and close combat. The Air Force, on the other hand, would take out a three-year lease with an option to buy."
Source: www.unwind.com
While the above observation may evoke a chuckle, it can be no laughing matter in a manufacturing company when different departments don’t speak the same language—especially when the objective is the integration of enterprise and factory floor systems.
Now, in the world of batch manufacturing, in particular, the long-standing communication gap between information technology (IT) and manufacturing automation departments may finally be starting to close, smoothing the way for faster, more effective and less costly “shop floor-to-top floor” integration. The catalyst? An emerging set of interoperability standards developed by the Instrumentation, Systems and Automation Society (ISA).
The ISA-95 series of standards on “Enterprise-Control System Integration,” commonly called S95, define the models, terminology and interfaces to be used in connecting the manufacturing floor to business-level enterprise resource planning (ERP) systems. Within the past 12 to 18 months, the standard has begun to catch on with manufacturers, vendors report, especially in the chemicals, specialty chemicals, pharmaceutical, and food and beverage sectors. Requirements for ISA-95 compatibility are showing up more frequently in requests for proposals, and a growing number of manufacturers are using the standard on one or more projects.
“A lot of companies bought ERP systems in the ‘90s and tried to integrate them with manufacturing, but it was hard to do and it was expensive,” observes Dave Emerson, systems architect at the Yokogawa U.S. Development Center, in Carrolton, Texas. “S95 provides a much more manageable approach. It’s easier for the automation companies to provide an interface, because they don’t have to delve deep into the ERP systems, and I think it has revitalized a lot of interest at end-user companies, who are saying, ‘Hey, this is possible. This looks like a good way to do it.’ ”
ISA-95 got a big boost in May last year when SAP AG, the Walldorf, Germany-based enterprise software giant, announced support for the standard. Industry sources note that SAP is making rapid progress toward developing S95-compliant interfaces for its products. Further, a number of automation solution vendors—including Aspen Technology, Siemens, Wonderware and Yokogawa, among others—are likewise developing S95 interfaces for communication with SAP and other S95-compliant ERP systems.
These implementations are based typically on Business-to-Manufacturing Markup Language (B2MML), a set of open schema developed by the World Batch Forum (now known simply as WBF) as an S95 implementation. B2MML is based on eXtensible Markup Language (XML).
Can we talk?
ISA-95 is important as a way to define the interfaces that let multiple vendors’ automation and business systems talk and exchange data. But the definitions and activity models that are laid out in the standard also play an important role just in enabling people to talk the same language, say industry sources.
In most companies, IT and shop floor personnel frequently use different terms to describe the same thing, or the same terms to describe different activities, points out Keith Unger, a manufacturing IT consultant based in Sugar Hill, Ga., and chairman of the ISA SP95 committee that is developing ISA-95. The terminology differences can lead to significant debate and time wasted at the beginning of an integration project. “One of the big areas of classic confusion has been what is meant by planning and scheduling, for example, so those areas have been well defined in the standard,” says Unger.
Dennis Brandl, a Cary, N.C.-based consultant who serves as editor for the SP95 committee, agrees that the standard can help get projects rolling more quickly. “If you have a group coming from the engineering disciplines and a group from the IT and financial side, and the two have never had to talk to each other, this really helps them,” says Brandl. “People have been seeing the advantages in this, because they no longer have to say, ‘Okay, everybody on the shop floor has to learn SAP terminology,’ or, ‘Everybody in the IT department has to go find out what manufacturing is like,’ in order to make this work.”
Dan Rozinski concurs. “S95 provides a model for looking at the space to start describing things using common descriptors,” says Rozinski, who is MES project leader (for Manufacturing Execution Systems) at Philadelphia-based specialty chemical producer Rohm and Haas Co., and a voting member of the SP95 committee. “If you’re a business person who’s always thought of manufacturing only in terms of supply chain, you can start to converse with someone who’s a process control engineer who’s only ever thought of plants in terms of production control.”
Parts 1 and 2 of the ISA-95 standard, released in 2000 and 2001 respectively, deal with data models and terminology, object models and attributes. Part 3, published in June this year, covers activity models of manufacturing operations management, while the SP95 committee continues development work on three additional parts.
Interface savings
One manufacturing company that is a strong supporter of ISA-95 standard development is The Procter & Gamble Co. (P&G), the Cincinnati-based consumer products giant. At the 2005 WBF North American Conference last May in Atlantic City, N.J., David Cornell, a P&G global MES executive, described a variety of initiatives that the company has underway aimed at ISA-95-compliant data exchange using B2MML.
Like many companies, P&G has historically relied upon custom interfaces between ERP and MES systems at its various manufacturing facilities. But the advantages of an ISA-95 standard-based interface are numerous, Cornell told the WBF audience.
One is a significantly faster and lower cost of implementation each time new interfaces are required. “Once you’ve got the standard in place, putting the next one in is extremely cost-effective,” Cornell said. Compared to about a year’s time required to put in a custom interface, a B2MML interface requires only about five weeks, he said. Total cost of ownership is also significantly reduced, because just a single standard interface must be maintained, as opposed to numerous custom point-to-point solutions.
An ISA-95-based interface can eliminate being locked into a single vendor, and enables control systems from different vendors to be switched as needed among factory processes without having to redesign the ERP interface each time, Cornell added. B2MML interfaces are also easily deployed to new plants, becoming no more than a standard service request, he said. “You don’t have to go out and appropriate money to build a link between your ERP and manufacturing system. You just put it in there. If it supports the standard, you simply turn it on and add it to the list of sites that your central global support team manages.”
ISA-88 connection
P&G is not only pushing its vendors to provide S95-based MES-to-ERP links, but the company is also working to synchronize its MES systems with its batch-making systems that are based on the earlier ISA-88 batch control systems standard, Cornell said. The company wants all of its different ISA-88-based batch control systems to be able to archive production records to its MES systems, so that the data can be stored in a consistent manner. “Then, once we have it all there, we can focus on the single point of integration between our ERP and MES systems, which is the B2MML file structure,” the P&G executive explained.
Another manufacturer that is linking its ISA-88-aligned batch control system data with the enterprise level is Martens Brewery, based in Bocholt, Belgium. When Martens set out to renovate its brew house shop floor system in late 2003, it had several objectives, including the ability to exchange production data with its Protean ERP system. As one prerequisite for that goal, the company worked with APV, a company owned by London-based Invensys plc, and with
Wonderware, another Invensys company based in Lake Forest, Calif., to install its ISA-88-based batch management system.
The ISA-88 batch system works with the Invensys Archestra architecture. And it not only provides the kind of platform needed to develop an S95 interface to the Protean system, but it also enabled Martens to merge what were previously two separate departments—automation and IT—into what now is a single department, says Paul Bloemen, Martens’ information communication technology manager. “S88 (or ISA-88) is a well-structured standard, with the kind of language that made it easy for automation people and IT people to talk with each other, which was always hard in the past,” Bloemen relates.
Given the positive experience with ISA-88, Bloemen says he “insisted” that the plant floor-to-ERP integration be based on the ISA-95 standard. That project, based on a B2MML interface, was completed in July last year. The implementation went quickly, says Tim Sowell, Wonderware’s vice president of product strategy. “Because Protean had already come out with an S95 interface, and we had an S95 interface, all we had to do was agree on the level of granularity that we would go down to.” The Protean ERP system at the time was owned by Invensys Marcam, a sister company to Wonderware, but it has since been acquired by Chicago-based SSA Global.
The B2MML implementation enables Martens to automatically download production schedules and their required materials and equipment resources, as planned in the Protean system, to the brew house factory system, where the data is inserted into the batch management schedules to start at the planned time, based on optimum equipment availability. As the work is completed, production information such s volumes produced, raw materials consumption and equipment usage is automatically uploaded from the brew house floor to the ERP system.
The system is a vast improvement compared to the previous approach, which depended on manual entry of information, says Bloemen. “The operators in the brew house had to enter the production information and the consumption of raw materials, which took time, of course. And people make mistakes, and they sometimes do it late.” Brewing is a five-step process at Martens that requires nine hours from start to finish. And while operators previously waited until the end of the entire process to enter production results, the S95-based system provides for automatic uploads after each of the five stages.
The result, according to Bloemen, is that inventory data at the ERP level is much more reliable, accurate and up-to-date for the company’s brew house operations. The benefits include improved inventory turns and more efficient reordering, as well as tighter manufacturing capacity utilization. Martens is now making plans for similar renovations including ISA-95-based shop floor-to-ERP integration for the fermentation and filtration portions of its plant, Bloemen says, and is also looking at an upgrade to its filling and packaging line operations that would likewise include S95 links to the Protean system.
Bloemen says he has been well-pleased with his decision to push for an ISA-95-based integration. “We could have gone for a custom, vendor-specific solution, but my experience is that whenever there is a good standard available, use it,” he advises. The use of B2MML interfaces will make subsequent interfaces much easier and faster to implement, and will also facilitate links as needed to other vendor solutions.
Say what?
Bloemen notes too that “just as S88 provided a good communication tool for diverse members of an implementation team, so too did S95. It’s kind of a language, and also a structure that helped in setting up an interface.”
What’s an example of how the definitions provided in ISA-95 helped the Martens team work together more effectively? “It may sound stupid,” Bloemen responds, “but just as an example, the people in IT and in the business area were always talking about ‘schedules.’ But people on the shop floor talk about ‘production orders.’ Even something as simple as that—putting the right definition on one term and getting everybody using that term,” he says, “that was already an advantage.”
For more information, search keywords “ISA-95” and “ISA-88” at www.automationworld.com.
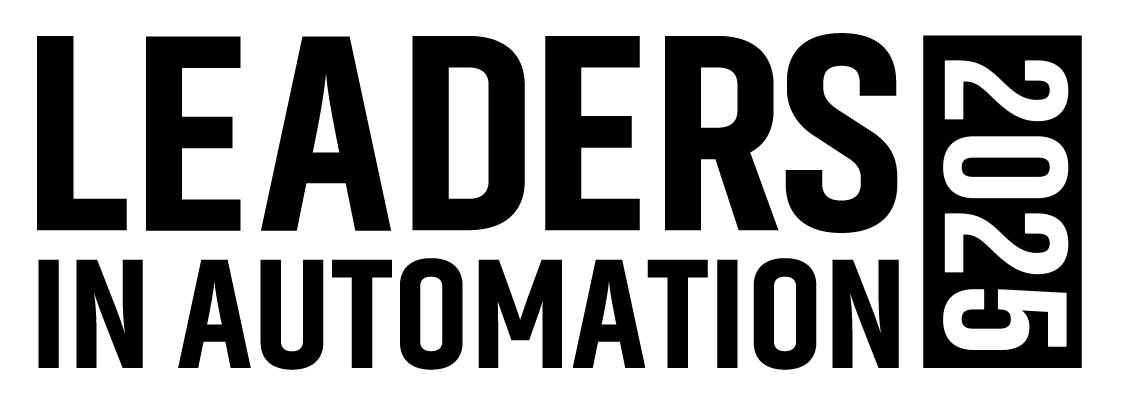
Leaders relevant to this article: