Larry Balcom, process control technology leader at DuPont Performance Coatings, in Front Royal, Va., was facing a problem. When he looked at issues in his manufacturing process that were inhibiting gains in efficiency and profitability, he figured there had to be a better way to manage recipes, improve maintenance responsiveness and train operators. At the most basic level, he needed a way to communicate recipe information and batch status in a simple form that would be understandable by all concerned.
One hurdle was that recipe data was located in many different repositories, ranging from enterprise resource planning (ERP) systems to process description databases, process modeling systems and process control systems. At DuPont Performance Coatings, recipes are used at many levels of the enterprise. Research and development uses them as part of the new product creation process, and for process safety screening and process optimization. Engineering needs recipes for process maintenance and assurance, and also for production transfers. Operations uses them for actual production and for operator training. Recipes also form the basis for product costing in accounting.
The usual way of translating recipes from department to department involved manually writing and re-writing them, and then mailing or hand-delivering them. This process is error prone and time consuming. Balcom searched for a way to automate the system. Looking for standards already existing that could form the foundation of an automated recipe handling system, he turned to a standard of the Web—eXtensible Markup Language (XML). XML is essentially a standard method for structuring data. It uses what are called “schemas,” or rules, to build XML data files.
As Balcom researched the standard, he found that the industry organization World Batch Forum (now known as WBF) had worked on a method of using the state language from ISA-88, a standard promulgated by the Instrumentation, Systems and Automation Society, using the XML format. The result of that effort was BatchML, a standard that provides a common language between systems to allow direct transfer of recipe data.
Using BatchML, Balcom developed ways to represent recipes in his ABB Infi-Batch data manager, part of the Symphony distributed control system from ABB, a Zurich-based company with U.S. headquarters in Norwalk, Conn. His Infi-Batch XML Schemas supported production batch information, control recipe identification, master recipes with single or multiple unit recipes, operations with single, multiple or parallel phases, and unit parameters and comments.
Balcom’s system for translating the ABB Batch Data Manager (BDM) recipe files into XML and back involved some automation in the form of scripts in BDM and XML capability within Microsoft Excel (or any similar application). First, a recipe from the BDM is printed to file. It is then imported into a neutral platform such as Excel via a custom translation utility. Next, the recipe is exported in standardized XML for use in other systems and platforms. To get back into the BDM, the file is exported in the BDM scripting language format.
Anyone, anywhere
Recipes can be displayed in read-only format via standard eXtensible Stylesheet Language Transformations (XSLT) format on a Web browser by anyone, anywhere, given access and authority. Thus, it is not limited to those with engineering workstations. Or, as Balcom concludes, “One technology is used to interface SAP (DuPont Performance Coating’s ERP system) with a PAS (process automation system).”
ISA-88 also recently came to the rescue of a food manufacturer. Canbra Foods is Canada’s largest fully integrated oilseed crushing, refining, processing and packaging company. Its major products include cooking and salad oil, margarine, shortening and a full line of proteins. Engineers at the company’s Lethbridge, Alberta, Canada, facility, decided to integrate the ISA-88 batch standard to control, automate and monitor production in order to drive manufacturing costs down.
While Canbra’s oil preparation process has been largely automated, the milk preparation stage remained mostly a manual operation. The milk-preparation process began with the manual addition of 33-pound bags of salt and 44-pound bags of whey powder into a pre-mixer on an open processing floor. This labor-intensive process created production bottlenecks and spillage, as well as documentation challenges. In addition, the pre-mixer occasionally received inaccurate amounts of ingredients. Worse yet, employees faced potential injury from manually lifting the bags and pouring them into the pre-mixers, and manual activation of the mixer and pumps left the process open to human error. Automation appeared to hold the answer.
“Rockwell Automation supplies all of the manufacturing software in the Lethbridge facility,” says Rick Kurio, control systems coordinator, Canbra Foods. “Therefore, we chose Rockwell Software RSBizWare Batch for batch management in order to employ batch mobility and standardization concepts through ISA-88. This was important, since we were also seeking a common ground for our engineers to program, troubleshoot and maintain the system.”
Says Kurio, “The integrated ISA-88 model provides us with a ‘cut-and-paste’ approach to easily develop and reconfigure recipes. We are currently using eight milk recipes and 10 clean-in-place (CIP) recipes.”
Results of the automation system implementation include an increased efficiency and a safer work environment. “We have been delighted with the results to date,” notes Kurio. “Since automating the process, we have been able to save $45,000 per year, plus additional savings through increased batch accuracy,” he adds. “On top of that, worker safety has improved, since they no longer have to handle 30- to 40-pound bags of material.”
Standards aid biotech
Ronald E. Menéndez, automation engineer with Genentech Inc., a South San Francisco, Calif., biotechnology research company, says, “In response to strong market demand, aggressive competition, and pressure from investors to accelerate the time to market for revenue-producing products, biotech and pharmaceutical companies are viewing manufacturing process automation as a key strategy to achieve operational efficiencies, regulatory compliance, profitability and growth.”
Process automation not only supports the tightly documented “state of control” that is required for U.S. Food and Drug Administration (FDA) compliance; it can also be a valuable strategy for improving productivity, reducing product variance and achieving flexible manufacturing objectives.
But because the biopharmaceutical production process all but defines the finished product, says Menéndez, automation and process design are almost indistinguishable, requiring precision engineering of many factors, including schedule and quality. For biotech and pharmaceutical companies, the regulatory impact makes it even more challenging.
Because of such factors, Menéndez states that early and structured planning is essential to the success of any automation initiative, and that the Good Automated Manufacturing Practices (GAMP) subcommittee of the International Society of Pharmaceutical Engineers (ISPE) provides comprehensive guidelines to help manufacturers automate, and subsequently validate, their processes.
The resulting design consolidated multiple, formerly isolated, equipment-based recipes into a single, overall production recipe following ISA-88. As a result, the company realized dramatic process management and productivity improvements and increased manufacturing in the manufacturing area, reports Menéndez.
The new automated system reduced the overall production schedules and time involved in CIP operations significantly. It also minimized operator interaction with the process, reduced the number of manual tasks and lessened the opportunity for errors. The system significantly reduces potential operator error-based discrepancies—the out-of-procedure production anomalies that require quality assessment and resolution.
One of the original products manufactured at the South San Francisco facility is the human growth hormone, Nutropin. In production for nearly 20 years, Nutropin had been manufactured largely through semi-automated processes, supplemented in part by an older generation process control system. Production took place in a suite of bioreactors, ranging in capacity from ten liters to 1,000 liters.
Semi-automated processes had included CIP, sterilization-in-place (SIP), and bioreactor operations. Media preparation and secondary feed preparation were performed in portable tanks. A pushbutton/switch panel with integrated single-loop controllers provided a modest level of process automation and supervisory control for bioreactor operations.
While effective for batch production, the operation was time- consuming and required extensive involvement by operators. It also did not enable the South San Francisco manufacturing operations to take advantage of new process automation advances and features. To address such concerns, Genentech decided to replace its technology with a state-of-the-art automated production system. And recognizing that GAMP4 was well on its way to becoming the standard approach for planning effective, regulatory compliant production systems, Genentech elected to follow these guidelines.
GAMP4 guidelines recommend a process, which initiates with the creation of Quality and Project Plans, and a User Requirements Specification (URS). These steps are followed by the development of a Functional Specification that will meet user requirements and the Detail Design of the automation system that meets the specification. Following this method facilitates validation because each phase correlates directly with industry accepted procedures for qualifying installation (IQ), operation (OQ) and performance (PQ), as depicted in the GAMP4 “V” model.
A quarter of time
If coordinating these activities with multiple recipes, an operator would, for example, have to coordinate individual recipes for preparing and transferring media, others for sterilization and still others for cleaning. Automating these activities under control of a single recipe, however, provides great efficiencies when compounded throughout the multiple steps remaining in the process flow. Key to the efficiency is synchronized repetition of the process loop. The fact that each vessel ends with a cleaning operation and is ready immediately for a new batch, enables continuous processing and operation, which the plant performs with minimal manual intervention, 24 hours a day. The semi-automated CIP process of the bioreactor had previously taken two operators up to six hours to complete. Now, one operator can start the recipe, turn attention to another task, and return to a clean vessel, three hours later.
Achieving this level of automation required replacing all original equipment. A Foxboro I/A Series server cluster from Invensys provides control, running Foxboro’s ISA-88-based batch management software package that executes recipe procedures, manages equipment and collects batch production data.
While Genentech’s planning has always involved procedures for gathering user requirements, defining functional specifications and then designing the system around them, it was sometimes a varied and isolated process. GAMP4 provided a consistent planning framework, which all members of the multi-departmental, cross-functional planning team respected. This structured, systematic attention to clearly articulated user requirements resulted in reduced capital expenses, more cost-efficient maintenance, improved productivity including reductions in process time and potential batch discrepancies, and streamlined validation effort. It left Genentech well-positioned for successful FDA inspection and audits.
For more information, search keyword “ISA-88” at www.automationworld.com.
Sponsored Recommendations
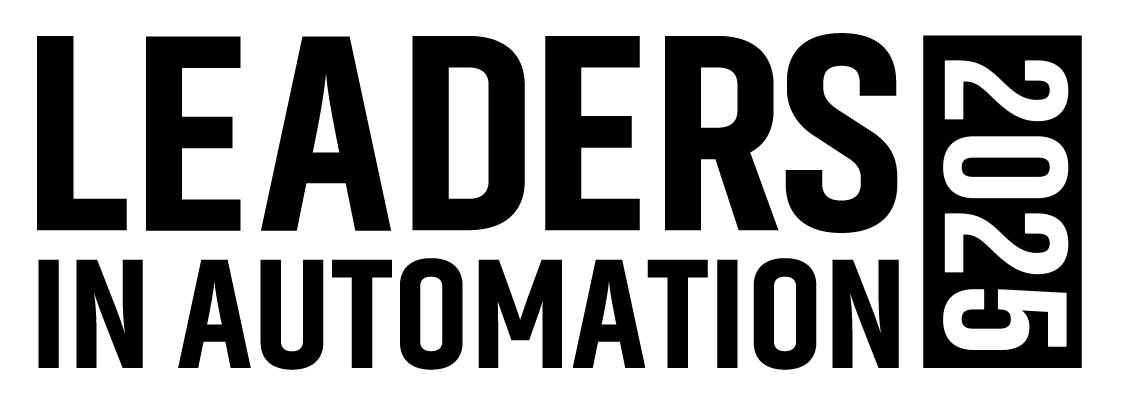
Leaders relevant to this article: