“My application is the automation of a batch reaction and packaging system,” writes an engineer whose company does not permit identification. Using a recent release of distributed control and asset management software, the writer notes that the positive point about the new software is the ability to develop and simulate the application code on a personal computer (PC).
This engineer also finds several “challenges” stemming from the use of modern application software. “The software is relatively new and very ‘open,’ in that code configuration is not what it was like ten years ago, which involved entering data into a system workstation via standard configuration entry screens. One must be well versed in Microsoft Windows operating systems to work with this software, plus training on the new system software is rather extensive. Further, company standards must be developed for effective and consistent implementation. The software has a number of idiosyncrasies (called ‘features’ by the manufacturer) that are only discovered with use. Various objects within the code are linked to each other, and if the links are broken, the code won’t work and the system may crash. Finally, multiple servers are required to support the production system and they can be very temperamental.”
Just about everyone uses a computer these days, especially in manufacturing. And just about everyone uses various software applications to accomplish their tasks on those computers. There are two crucial times when decisions must be made about software use. One is when a supplier releases a “version upgrade,” that is, a revision with enough new features to warrant moving the version number to the next whole number. The other is when one’s current supplier is acquired by another company. The decision to be made is whether the pain of the upgrade is worth the new functions to be gained.
Readers speak
In a Web-based survey, Automation World asked readers to rate their experiences with both version upgrades and with their suppliers’ acquisitions. In total, we received 72 detailed responses. Many readers commented about specific situations and several others were interviewed later. Suppliers were asked how they handled upgrade programs and about their software design strategy for upgrades. While readers did not hesitate to voice unhappiness with their experiences, suppliers were confident that their designs negated any chance of upgrade pain. The survey is not statistically valid, but it does point out that suppliers still have a way to go to satisfy their customers.
Specifically, Automation World readers are less than enthusiastic about the cost and support received for version upgrades, and are downright unhappy when another company acquires their software. They are generally positive, however, regarding version upgrades.
In the software industry, it has become standard practice for new versions of the same application to be numbered in a whole number and decimal format. A new whole number, for example, moving from version 4.5 to 5.0, suggests a major upgrade. Adding to the decimal, say from 5.0 to 5.1, suggests minor upgrades and bug fixes. Major upgrades, as almost all computer users have experienced, often offer cool new features at the cost of some installation and usage headaches. Automation World readers responded with average scores of around 3 on a scale of 1 to 5 (1 being low or unsatisfied, 5 being very pleased) when asked about their experiences with version upgrades in automation software. Concern about the cost of upgrades was more noticeable than concern about installation or support.
On the other hand, when readers saw their software supplier acquired by another company, their experiences were decidedly unsatisfactory. In four out of five categories, a majority indicated either a very unsatisfactory or unsatisfactory experience. These categories included (in order beginning with most unsatisfactory) support for legacy product, cost, easy move and forced upgrade. In the last category, overall support, almost half voiced displeasure (48 percent) with the average creeping closer to 3 (2.69) but still not good.
Happiness is Linux
Josh Lane, SCADA engineer (for Supervisory Control and Data Acquisition) with Auburn, Calif., systems integrator Aqua Sierra Controls, was thrilled with the software he has been using. He was the only person who responded to the survey noting the use of the open-source Linux operating system. Open-source software is free to the user and can be freely adapted to whatever application the user is working on. The expectation of the open-source community is that any improvements the programmer makes to the software will be sent back to the community for incorporation in later releases. As might be expected, Lane is happy with the price of the software he obtains from Data Flow Systems (DFS), of Melbourne, Fla. The company’s HyperSCADAServer product is bundled with a server running the open source Apache application and a variety of input/output (I/O) connections.
“The system comes with a low price, plus all upgrades are free as long as the server supports them,” notes Lane. “DFS also provides free training and technical support. The software provides for connection not only to the DFS controller, but also controllers from Rockwell Automation and Siemens, among others. If there’s anything we need beyond what comes in the package, DFS will implement. We had a basic trender but needed to overlay 12 trends with snap-to grids for a project, and DFS had it two months later. It’s like a $30,000 HMI/SCADA package (for Human-Machine Interface/SCADA) for a fraction of the cost.”
Of course, it is targeted at specific industries such as water and wastewater.
Controls engineer Dave Coulter reports problems both with software upgrades and with internal company organization. In his company, the information technology (IT)department “owns” the HMI/SCADA software, even though the engineering department must make it work. There is a historical reason for this, as the application was implemented as part of a statistical process control program. However, many of the company’s PCs are old enough that they will not run the latest revisions of the application software. Like many companies today, management is reluctant to spend money for new computer equipment. In addition, Coulter notes, the IT department is busy, so projects in other departments must take a back seat.
Coulter’s experience brings out one problem manufacturing professionals have with software upgrades, and Lane alludes to it as well—the difficulties encountered when the latest software revision won’t run on the installed computer base. Maintaining all software to the same revision level is a parallel problem. Robert Antwine, a controls engineer with a Tier 1/Tier 2 automotive supplier, notes that the situation can be a real problem when a contractor writes some code in its version which may be more current than the version Antwine is using. That new code may not even run.
Antwine goes on to state what he sees as the biggest problem for engineers in his industry—cost. “My greatest complaint is how much the supplier charges us to maintain all the software to the current revision level. Our supplier is now charging by how many devices you are supporting. You also have to maintain the contract. If you don’t maintain the contract, then you can’t get upgrades.”
As far as overall support goes, Antwine voices a common theme from the survey—users too often have a problem finding the correct tech support person in a timely manner. Problems are solved, but only after shuttling around for a while. Antwine seconds one of the thoughts of the first engineer quoted in this article, “Overall, the software seems to work pretty well, but when they come up with new revisions, there always seem to be some hidden bugs that have to be discovered and worked out.”
3M engineer William Cotter figures his vendor uses Microsoft Visual Basic for Applications (VBA) for scripting since every time his group must upgrade a Windows patch, or even a patch from the supplier, the application must be re-installed. “So now we often have to reinstall the application about three times a year. This takes about three hours with all the backups and such. With hundreds of units, this adds up to lots of hours for our staff.”
Suppliers respond
It’s not that suppliers aren’t trying, though. Mitch Vaughn, chief technology officer for production management for UGS Tecnomatix, in Richardson, Texas, says that the company has historically supported many hardware platforms, so it was forced to build its base on technology that was supported in many ways—for example “plain, old ASCII.” ASCII is a data format recognized by just about every hardware and operating system in use. The company supported eleven platforms in the mid-1990s, including Microsoft Windows, Unix, HP-UX, SCO Unix and VMS. The company moved from ASCII backups to ODBC, an open database standard.
Jay Coughlin, manager, HMI Products for Norcross, Ga.-based Siemens Energy & Automation says, “When there is an update to an active product, or when a product has reached the end of its lifecycle, Siemens ensures that that there is a path to move the customer from point A to point B with minimal effort. As a user and purchaser of software, we expect this same commitment from our software vendors. For customers who need to keep pace with innovations, Siemens offers a software update service that automatically sends out updates as they occur. Customers who do not need that level of support may obtain upgrades as needed.”
Bernie Anger, vice president of Software Technology for GE Fanuc Automation, Foxboro, Mass., says, “GE Fanuc has a philosophy—both for our hardware and software offerings—to ‘leave no customer behind.’ We continue to offer and support software originally developed by our acquisitions, Total Control Products, Mountain Systems, Intellution, CimWorks, and DataViews. We provide software conversion tools to assist with migration to newer hardware and software, including from third-party systems. For any new software version, we go through a Six Sigma-related process of research prior to development, and extensive field testing with current customers prior to broad release. We have a services team that assists customers and is monitored within GE Fanuc through a rigorous Six Sigma scorecard that charts service effectiveness and customer satisfaction, and offers a means for continuous improvement.”
Ralph Kappelhoff, Rockwell Software general manager at Rockwell Automation Inc., Milwaukee, states, “The primary problem we see is that customers often underestimate the risks and overestimate the benefits associated with major upgrades and migrations. Oftentimes, customers will upgrade simply because IT is mandating the change, not because it will improve manufacturing operations. The most successful customers evaluate the risks to their environments and then identify the business value of the upgrade to ensure the risk is balanced appropriately by the rewards.”
Scott Mack, vice president of operations for software supplier Citect Americas, Alpharetta, Ga., states, “Upgradeability has always been a priority with Citect. Even today, Citect users can upgrade from our DOS version to the latest (Windows-based) version 6.0 with no or little engineering work. Citect tries its best to keep older functionality while adding new features. Unfortunately, new and improved features do sometimes cause older features to be discontinued.”
For more information, search keyword “software” at www.automationworld.com.
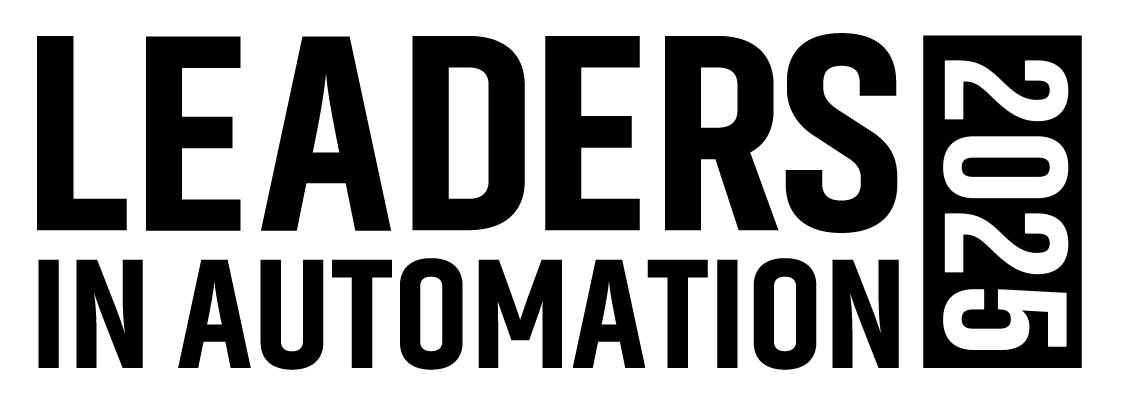
Leaders relevant to this article: