It’s code-named the “Snake”—a robot arm with so many axes of motion that it can bend or twist around objects as needed to perform tasks.
Craig Jennings, president at Motoman Inc., a robot vendor based in West Carrollton, Ohio, declines to provide additional details about the “Snake” robot that his company is developing. “You’ll be seeing the Snake within a year or two,” he promises. But Jennings does note that robots featuring “a dramatic increase in the number of axes per arm” are only one of various developments the company has in the works that will further enhance robot flexibility.
—Here and now—
That’s not to say that industrial robots aren’t already one of the premier automation technologies available for factory applications in which flexibility is key.
Compared to fixed, or hard automation equipment that is designed to perform a single task, robot arms are multifunctional manipulators that can be programmed and reprogrammed to perform a variety of different tasks. That flexibility can greatly decrease the need for costly part fixturing, while significantly reducing the time required for product changeovers. What’s more, robots have shown dramatic improvements in price, reliability and ease-of-use in recent years. And as North American manufacturers look to become quicker, more agile and cost-competitive against foreign producers, there are signs that robotics are finding broader use in U.S. factories.
Consider the operations of Chrysler Group, the Auburn Hills, Mich.-based automaker owned by DaimlerChrysler AG. The Chrysler Group has invested nearly $5 billion in its manufacturing facilities during the past two years, and recently announced plans to spend another half billion dollars on major renovations aimed at improving flexibility at two plants in Sterling Heights, Mich. Upgrades at the Sterling Heights Assembly Plant will include new tooling and about 620 welding and materials handling robots.
“With the advances of robotics and the ability of robots to do more today than they could yesterday, and also with the cost of robots coming down vs. where they were 10 years ago, it gives us a lot of opportunity to do things now that we couldn’t do before,” observes Don Dees, Chrysler Group vice president, small/premium/family vehicle assembly.
In many of its plants today, Chrysler is able to build multiple vehicle types on the same production line—a departure from the one line/one vehicle standard of the past—enabling the automaker to adjust its product mix much more rapidly in response to changing consumer demand. In many cases too, model year changeovers can be accomplished without the traditional multi-week plant shutdowns that characterized automotive operations of the past.
Dees credits this improved flexibility to a number of factors, including a well-trained workforce, vehicle designs based on a Common System Architecture, and a flexible process design that includes widespread application of robotics. “There’s just total flexibility of robots these days. They can seal, they can weld, they can do so many things now—almost as much as your mind will let you think about,” Dees declares.
—Cut it out—
One emerging application area is robotic machining, which relies on a high speed cutting head that is fitted to the end of a robot arm, says Joe Campbell, director of strategic alliances for KUKA Robotics Corp., a robot vendor with U.S. headquarters in Clinton Township, Mich. “It used to be that if you wanted to machine a part—any material—you got a machine tool,” Campbell says.
Robots still can’t handle machining of hard steel. But thanks to advances in the rigidity of robot arms, along with software improvements that have boosted accuracy, robots are increasingly being used for milling of softer materials such as die cast parts, aluminum and plastics, Campbell contends. Advantages include reduced floor space and cost, as well as increased throughput, he says.
“If you’re going to mill a part using a machine tool, you may have to refixture the part multiple times. But with a robot, because of its flexible work envelope and ability to manipulate the tool head, you can probably reduce the amount of set up and fixturing required,” Campbell explains. “And you can actually fixture up multiple parts for the robot to work on in its work envelope.”
The flexibility offered by robots is also promoting a bigger role for these one-armed automatons in the world of consumer products, points out John Dulchinos, vice president and general manager of robotics at Adept Technology Inc., a Livermore, Calif.-based robot vendor.
“This whole push toward mass customization, to be able to tailor products to meet specific customer needs without paying the price of reduced volume, is a big driver for flexibility,” says Dulchinos. One good example involves cellular phones, where robotic assembly provides the flexibility to deal with the variability of sizes, shapes and features that consumers desire, as well as the ability to perform quick product changeovers to the newest “hot” phone models.
Dulchinos notes too that more robots these days are being equipped with machine vision systems, as a way to adapt to changing conditions or variability in the production environment. This is happening in disk drive assembly, for example, where a smaller generation of drives are needed for use in products such as MP3-format music players and digital cameras. “They have these tiny little drives, which of course, is driving a whole new wave of vision-guided robots required to put them together, because they need the flexibility,” Dulchinos observes.
—Keep it CIMPLE—
Steve Thomas, a senior project engineer at Delphi Electronics & Safety, an automotive electronics manufacturer based in Kokomo, Ind., can attest to the value of integrated vision in robotic applications.
About two years ago, Delphi converted to an approach to final assembly based on a standard robotic platform called a CIMPLE cell—for Cost-Improved Multi-Process Lean Equipment cell, Thomas says. Developed with an eye toward lean manufacturing principles, each CIMPLE cell requires only a two-by-three-foot footprint, and incorporates a small SCARA robot (for selective compliance articulated robot arm) that sits atop a standard base, which houses a personal computer (PC)-based controller and associated electrical and pneumatic panels.
Using SCARA robots provided by the Epson Factory Automation Division, in Carson, Calif., the compact CIMPLE cells replace earlier Cartesian robot-based machines at Delphi that required a five-by-six foot work envelope. Each CIMPLE cell can be easily configured to handle a variety of tasks, such as dispensing, screwdriving, test nest loading and unloading, label placement and inspection, Thomas says.
Delphi has so far deployed about 60 CIMPLE cells in three locations— Kokomo, Milwaukee and Reynosa, Mexico —and the number is growing, Thomas says. Around 80 percent of Delphi’s CIMPLE cell robots include integrated Matrox machine vision systems provided by Epson, he estimates.
In many applications, the integrated vision system is used for part location—finding fiducials on a circuit board or holes in a die cast housing, for example—so that the part can be picked up by the robot. In these cases, “what the vision really buys us is the ability to eliminate a number of mechanical components,” says Thomas. This not only reduces cost, but improves process reliability, because, as Thomas puts it, “the part that isn’t there never breaks.”
Among other advantages, Thomas says the platform concept used with the CIMPLE cell pays dividends in reduced training requirements for operators, who encounter the same familiar user interface when they move from cell to cell, even though the application may be different. In addition, the cells provide “deployment flexibility,” he notes, in that cells can be quickly reconfigured as needed to meet differing application requirements.
“We can also put multiple arms together in a single cell,” Thomas adds, which pays cycle time benefits. He cites one application for assembling an engine control product that involves dispensing an adhesive, placing a cover, driving screws and then picking up the assembly and placing it on a belt. With Delphi’s older, five-by-six foot Cartesian machines, that task took 39 seconds. A CIMPLE cell using two SCARA arms does the same job in only 26 seconds, says Thomas, while requiring significantly less floor space.
—Large part handling—
While Delphi relies on vision-guided robots for small parts assembly, the technology can pay dividends for handling large parts as well, as evidenced by one set of applications now in wide use throughout DaimlerChrysler’s North American plants.
The application got its start in early 2001, when DaimlerChrysler’s Brad Dailey was faced with a challenge. As automation electrical/tooling manager at the Chrysler Group Twinsburg Stamping Plant, in Twinsburg, Ohio, Dailey needed a system for handling stamped truck-bed parts for the company’s full-sized Dodge pickup truck production. The task required the unloading of 6.5- and 8-foot long box-side inner panels from large, 1,700-pound racks on which they arrived, and placing the panels on a fixture for welding.
One option was to assign operators to the task, who would use large, ceiling-attached “ergo arms” to pick and maneuver the panels. To meet throughput requirements for the high-volume line, two racks would be used, with two operators moving between racks and the fixture in an alternating sequence, says Dailey. As one operator was fixturing a panel, the other would be grabbing the next part.
But that approach had several drawbacks. Dailey was concerned about the safety of the operators, who would need to remain constantly in sync. A collision could risk operator injury, while also slowing the line’s cycle time. And with a total of eight operators required—four for each of two shifts—labor costs would total around $440,000 per year.
So in May of 2001, less than two months before the truck line was scheduled to launch, Dailey began searching for a way to automate the rack unloading process. He turned to Nachi Robotic Systems Inc., a robot vendor with North American headquarters in Novi, Mich. Nachi, in turn, assembled a team including representatives from machine vision vendor Cognex Corp., Natick, Mass., and Shafi Inc., a Brighton, Mich.-based software solutions provider that specializes in vision-guided robotics.
The team came up with a system that uses a single, Nachi SF 166 robot and eight Cognex In-Sight 1000 vision sensors, or cameras, with robot/vision integration and human-machine interface (HMI) functions provided by Shafi Reliabot software. The system relies on six ceiling mounted cameras above the rack area to verify rack location, that the correct parts are present, and other parameters, before unloading the panels—loaded 18 to a rack. The robot uses a vacuum suction gripper to grab a panel and move it to the fixture. Two additional ceiling-mounted cameras are used to guide the robot, which places each part on the fixture within a 0.25-millimeter placement accuracy.
Despite having just six weeks to develop the system, the team was able to meet the deadline for the truck line production launch, says Shafi President Adil Shafi. “Brad Dailey really put his trust in the team, because this kind of a system had never been done before.”
One of the biggest challenges at the time was ensuring that the vision system could locate and recognize the racks, which were often bent, beat up and rusted due to transport, heavy use and exposure to the elements during outside storage, Shafi notes. “Prior to about 2000, nobody had even considered using vision with racks, because they were so variable and unpredictable,” he says. Advances in vision technology, including improved software algorithms and faster hardware processing speeds, have helped to make the application viable.
Indeed, within six months of launching the truck panel rack unloading system, the Twinsburg plant launched a second system that Dailey commissioned from the same team for the unloading of minivan side quarter inner panels. The automated minivan panel deracking system is more sophisticated than the truck panel system, says Dailey. Among differences, the second system uses three cameras mounted on the robot arm itself, instead of relying on fixed, ceiling-mounted cameras.
That approach enables quicker part location without need for some of the initial verification steps used on the first system, notes Dailey. The three arm-mounted cameras use a triangulation technique to calculate depth of field. And the results, says Dailey, are impressive. “When you get down to the last few panels on the rack, they’ll actually be swinging in the breeze, varying maybe by six inches at the bottom, and that arm still comes in and picks ‘em right out of there,” he observes.
Dailey estimates return-on-investment at six to nine months for each of the two systems at Twinsburg, which together since their installation have unracked about 7 million panels. And Chrysler has since installed numerous additional vision-guided robot “AutoRacking” systems, as Shafi calls them, for handling a variety of part types. “There are six DaimlerChrysler plants that are using this now, with a seventh plant that will be using it soon,” Shafi says.
For more information, search keywords “robots” and “machine vision” at www.automationworld.com.
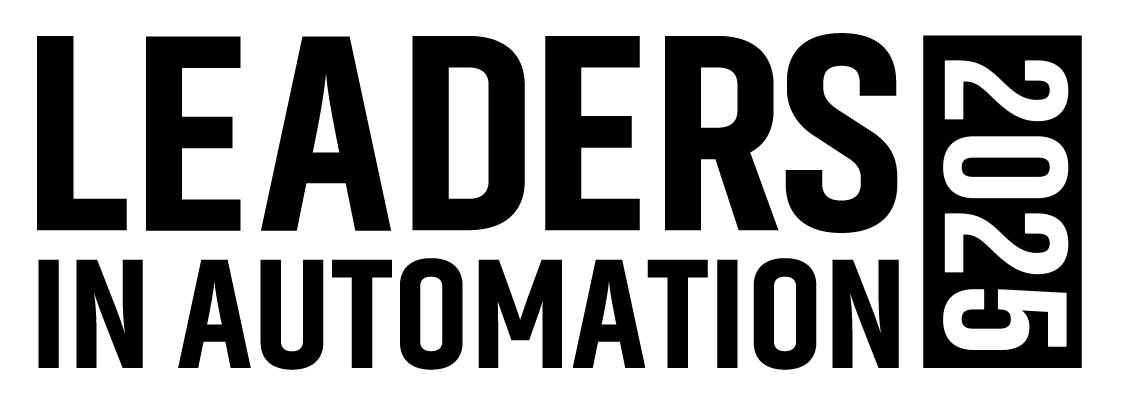
Leaders relevant to this article: