A year ago, Nutramax Laboratories Inc. was struggling to meet the Food and Drug Administration’s Good Manufacturing Practices (GMP) regulations using manual systems to develop raw material forecasts, manage material inventory and execute batch records. Now, the company is benefiting from a Manufacturing Execution System (MES) project that was completed in four months.
“This system gives us real-time vision into all types of information that’s available to all levels, from management to the plant floor,” says Miomir Adzic, manufacturing manager at Nutramax Manufacturing Inc., an Edgewood, Maryland, unit of Nutramax Laboratories. “In the past, we spent a lot of time reconciling raw material inventories and finished goods inventories.”
As a maker of joint supplements and other non-pharmaceuticals, Nutramax Labs doesn’t have to comply with the FDA’s Good Manufacturing Practices policies for pharmaceuticals. But the company uses GMP as a benchmark for manufacturing what are commonly called nutraceuticals, which are food supplements with scientifically supported benefits.
Automating the process provides a number of benefits. One is that managers now have far more insight into the manufacturing and ordering processes than when they had to pore over paper trails. “Our MES provides real-time information that tells us instantly how much raw material we need to execute our forecast,” Adzic says.
That type of insight is something that more and more pharmaceutical companies are trying to get. Drugmakers are catching the wave of using technology to increase productivity, and are increasing their efficiency by using MES and other tools. Technical advances have made it far simpler for companies to tie operations together, gaining the benefits of enterprise-wide communications.
“When data flows seamlessly, companies can make decisions in real time and they don’t need to worry about duplicating data,” says Glenn Restivo, life sciences marketing manager at Rockwell Automation Inc., in Milwaukee.
Among the key drivers behind the slow shift to MES are increasing competition from companies that can quickly re-engineer a new drug and get a competitive product to market in a few months. Growth of generic drugs is also making price more of an issue, spurring drug makers to cut their production costs.
Though pharmaceutical companies are used to working in a regulated environment, they’re increasingly finding themselves in a litigious environment as well. Some are responding by using MES to track products—monitoring production lots through manufacturing and out to the store shelves.
“Traceability goes all the way to the Wal-Marts and CVSes, which are starting to feel the pain of recalls. They’re putting pressure on pharmaceutical companies to use RFID (radio frequency identification) tags, so that when there’s an incident report, the supplier can do an immediate search and say, ‘This is the batch number that needs to be removed,’ ” notes Bharat Nair, high tech industry director for Brooks Software, a division of Brooks Automation Inc., in Chelmsford, Mass.
There’s also a widespread feeling that the era of blockbuster drugs such as Viagra is fading, so companies won’t be able to set up factories that make only one product for months at a time.
“As blockbuster drugs go away, companies need to set up for smaller runs of successful drugs, using existing plants but switching lines instead of running the same product all the time,” says Bart Reitter, life sciences manager for GE Fanuc Automation, in Charlottesville, Va. Instead of reading instructions on paper, operators can tap into an MES system that sends recipes needed for setup to plant floor equipment while also communicating with front office systems that control ordering and inventory management. Automating these changeovers is an easy way to reduce manual operations.
Error avoidance
“When plants are doing hundreds of products, making one of them every three months, the chance of errors rises. MES lets them avoid errors that arise from manual systems,” says Rick Sterrett, chief operating officer at Honeywell POMS, of Phoenix.
This type of automation can significantly improve efficiency. “We’re doing more with statistical process control, triggering alarms when the manufacturing process starts to deviate, so operators can react before the product goes bad,” says Yves Dufort, director, strategic programs, for Wonderware, of Lake Forest, Calif.
Monitoring statistical process control data can reduce the likelihood that unacceptable products can be produced in large batches before problems are spotted. While MES provides more insight into the broad production process, it is only a monitoring system. “MES can’t solve problems, but it gives you early warnings of problems in your facility or in your supply chain,” says Brooks Software’s Nair.
Though observers cite many benefits for companies that adopt MES and other automated technologies, most note that this regulated industry is not quick to change. Altering a process requires a lot of documentation, and companies starting new production operations often stick with techniques they know, rather than take a risk that something new will fail.
“The pharmaceutical industry is conservative. A lot of companies, particularly the major ones, have initiatives to use MES technology, but in terms of deploying it at all their facilities, most have a long way to go,” notes Wonderware’s Dufort.
But things are changing. The industry’s trend to consolidation may cause cautious pharmaceutical suppliers to employ MES technology. It can help simplify control and monitoring of far-flung facilities.
“There have been a lot of acquisitions and mergers, which leads to a lot of disparate systems. Pharmaceutical companies want to look at their operations globally, finding ways to get the right information in a timely manner to make decisions and roll products out,” observes Restivo, of Rockwell.
Technical advances
One thing that makes it easier to deploy MES is the advance of technology. Faster computing speeds and declining hardware prices are key factors that make it easier to deploy broad technical systems.
A number of changes in technologies and their usage make it simpler for MES solutions to control and monitor manufacturing operations. One is the acceptance of Ethernet, which has pushed its way onto the factory floor in many locations, making it far simpler to communicate between front offices and plant floors. That makes it easier for companies to build an enterprise-wide network, often called an intranet.
“Using an intranet lets you bring up the information status of anything in the plant from any site, providing a lot of flexibility that customers haven’t had before,” says Honeywell’s Sterrett.
This also makes upgrades simpler, because software can be replaced on a few servers instead of numerous workstations.
Integrators and software providers who saw difficulty in early MES applications have also responded by developing more software. There are a number of different programs used across the computers that span the regions between the factory floor and the executive offices. “Middleware that’s available now reduces the amount of time it takes to get the MES and ERP (enterprise resource planning) systems talking to each other,” Sterrett says.
Another factor that’s removing the pain of integration is the emergence of standards. The Instrumentation, Systems and Automation Society (ISA), of Research Triangle Park, N.C., has addressed this integration with ISA 95 and ISA 88, which provide a common platform for programmers. “ISA 95 defines and standardizes the transactions between the plant floor, MES and ERP,” Sterrett says.
The Internet has also aided this effort by providing a standard markup language for presenting data. “XML (eXtensible Markup Language) is being used as the communication protocol between sophisticated plant- floor controllers and the MES. That lets you isolate it from what’s going on in the control system,” Sterrett says.
Though standardization brings many benefits, it doesn’t come without issues that cause some vendors to avoid standardization. “Following industry standards makes it easier to integrate systems. Otherwise, you need to write a lot of drivers. But it’s a double-edged sword for suppliers, because it’s easier for customers to switch from one vendor to another,” Restivo says. However, he notes that Rockwell is focusing on a plug-and-play approach that will be a mainstay of product developments over the next few years.
Even with standards, implementing MES encompasses many complex issues. Data must be integrated from disparate areas, some of them from external companies. As manufacturing becomes more precise, it also becomes more demanding.
“MES needs to be an information gatherer from many systems on the campus, including automation, the OEM (original equipment manufacturer) skids carrying raw materials, and the heating, ventilation and air conditioning system,” Restivo says. Manufacturers want to use identification data on the materials received from OEMs, but today the data for these skids must often be re-entered into their systems, raising the possibility of errors in addition to slowing the operation, he notes. Automating this task can bring significant benefits.
Heating and air conditioning can be important in manufacturing because they can have an impact, particularly when companies produce drugs at disparate global locations where temperatures and humidity can vary widely. “If humidity is significantly higher in one plant, it can pose problems, so they need to correlate HVAC data to production lots,” Restivo says.
Faster shipping
Once those products are finished, automated systems can dramatically reduce shipping time. Currently, reviewers must pore over hundreds of pages of documents before they release a shipment. This task often takes a month, delaying time until revenue, while shortening shelf lifetimes and creating headaches for shipment schedulers. Going to electronic systems can streamline this part of the cycle. “Electronic batch recording (EBR) can reduce that idle time from weeks to days,” Reitter says.
That time savings is possible because EBR and MES provide enough confidence in the processes that examiners can look at alarms and other event recordings to see how they impact quality, rather than examining every piece of paper to assure quality.
One aspect of this is to maintain the signoffs commonly used in today’s paper trails. “When operators start a mixer or change the amount of a chemical, they have to enter their password to confirm that they did the job, creating an electronic signature that’s logged into the audit trail,” Reitter says. Going beyond that, many companies are looking at ways to tie MES, ERP and other systems together, automating processes instead of simply digitizing the data, he adds.
Having this information in a searchable digital format will help companies respond when they’re audited or when problems arise. “Manufacturers who put their data into MES can take it forward with full traceability,” says Tom Comstock, vice president of product marketing at Brooks Software.
While integrating MES is today a big issue, observers note that at some point, the technology will become part of the landscape. Programs will merge into enterprise-wide programs. “Users won’t know they’ve just finished a page in MES and gone to a lab information system, the applications will start blending together,” Sterrett says.
For more information, search keyword “MES” at www.automationworld.com.
Sponsored Recommendations
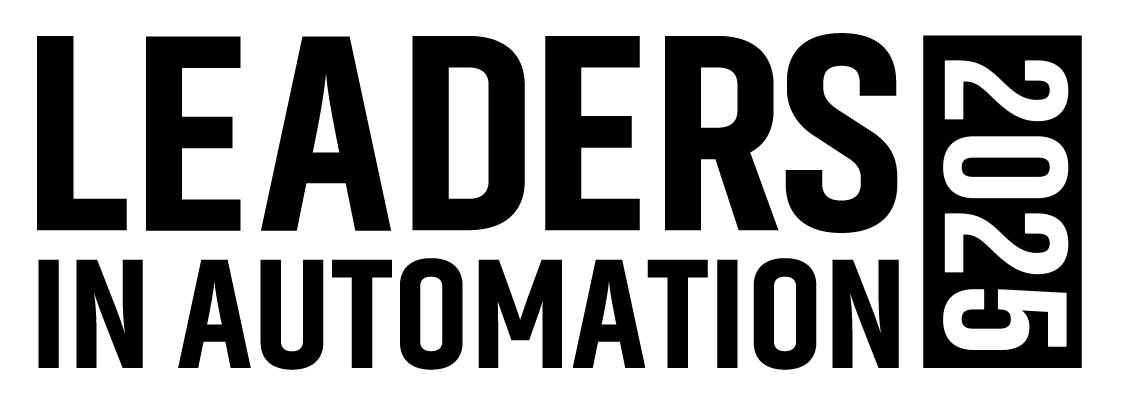
Leaders relevant to this article: