This is a tale of mice and MEMS.
That’s MEMS, as in MicroElectroMechanical Systems, an emerging, integrated microchip technology, and mice—not the kind that you double-click, but the kind that reside in about 16 million laboratory cages around the world, about half of which are located in North America.
At Siemens Building Technologies Inc. (SBT), a Buffalo Grove, Ill., unit of German-based Siemens AG, researcher Osman Ahmed is laying no small plans for those mouse cages. On Jan. 31, Ahmed completed an 18-month, Siemens-funded project in partnership with the University of Florida that proved the feasibility of monitoring mouse cage environments using wireless, MEMS-based technology.
If the mouse cage micromonitoring technology can be successfully commercialized, it could turn into a new business opportunity for Siemens in the health and pharmaceutical research laboratory market. More importantly, if further work pans out, Ahmed’s MEMS-based wireless, micromonitoring platform could be a launching pad for additional new products in other industry segments. The possibilities range from improved environmental monitoring and control of office buildings, schools and factories, to low-cost, industrial equipment monitoring for predictive and on-demand maintenance applications.
“We chose one specific application for this project, in monitoring laboratory mouse cages, but the goal was to see whether we can now find many, many applications that we can do today, as well as in the future, that can be launched on top of this microsystems platform,” explains Ahmed, a senior principal engineer in SBT’s Building Automation Unit.
Ahmed was recently named one of Siemens’ top 12 inventors for 2004.
MEMS, or MicroElectroMechanical Systems, are so-named because they work by using both the mechanical and electrical properties of micrometer-scale devices formed on silicon chips. The technology relies on traditional integrated circuit fabrication techniques combined with compatible “micromachining” methods to form the electrical and mechanical structures. A tiny cantilevered beam etched out of silicon can serve as a vibration or pressure sensor, for example, by propagating physical force as an electrical signal that can be processed by on-chip circuitry.
A wide variety of sensor possibilities exist for MEMS integration. MEMS-based sensors for detecting various gasses, for instance, can be made by depositing a layer of gas-specific sensing material on a silicon base; when the gas contacts the sensing material, it diffuses through the sensing layer, causing a measurable change in electrical characteristics that corresponds to the gas concentration level.
Ahmed became interested in MEMS in 1997. But it wasn’t until this decade that he found an application with sufficient commercial potential for Siemens to move forward with field trial research.
In 2001, Ahmed and his collaborators spotted a potential market opportunity in animal research laboratories, which sometimes maintain hundreds of individual mouse cages. Scientists doing experiments with mice need to be sure that reactions of the animals are the results of certain drugs or treatments, and are not due to environmental fluctuations in their cages.
Field Trials
“The mice must be kept in a very highly controlled environment, but right now, the industry does not have any good monitoring system for these mouse cages,” Ahmed explains. By developing a MEMS-based micromonitoring system that could wirelessly communicate sensor data from each cage back to researchers, Ahmed believed that Siemens could help scientists improve the quality of research, while also boosting productivity and lowering lab operating costs. Field trials on the system began in August 2003.
In developing the mouse cage micro-monitoring system, Ahmed worked with a team of researchers both inside and outside of Siemens. Collaborators included a group of engineers at Siemens Corporate Technology laboratories in Munich, Germany, who focus on MEMS device development for various Siemens divisions. Researchers at the University of Florida, where the field trials were conducted, contributed their expertise and knowledge of animal care facilities.
For the micromonitoring project, the Siemens Corporate Technology engineers created a design that can integrate five separate MEMS sensors, together with associated support circuitry, all on a single silicon chip. The MEMS chips used in the field trials contained elements for sensing carbon dioxide (CO2), ammonia, relative humidity (RH) and temperature, with the fifth sensor space reserved as a “spare,” says Ahmed. For future applications, “this could be a light sensor, or something else, depending on what is needed.”
The MEMS sensor set is well suited to the mouse-cage monitoring application. High levels of ammonia or CO2 in a cage, for example—which the MEMS chip can detect—is an indication that the air is stifling or the straw in the cage needs to be changed. Temperature and RH in cages must likewise be monitored and controlled for optimum experimental results.
Future commercial MEMS chips will integrate wireless communication capabilities on the same chip with the sensors, says Ahmed. But for the field trial, Siemens Corporate engineers provided separate Radio Frequency (RF) transceiver chips that were mounted with the MEMS sensor chips in multi-chip assemblies. These assemblies were placed within mouse cages, and sensor data was transmitted wirelessly to a hub station in the room and also to a laptop personal computer used by researchers.
“The hub actually connects to a Siemens building automation system, and we used our standard Ethernet protocol to get that data from all of the sensors,” says Ahmed. “The building automation system can then serve as a platform to store and archive the data, and to create applications for people who need it.” The wireless connection to the laptop enabled researchers to instantly access real-time sensor data from any of the cages by simply sending a query. The same query could be sent using a wireless personal digital assistant (PDA), says Ahmed, “so someone could just walk into the room with a handheld PDA and say, ‘Give me the values of ammonia for cage number 45.’ ”
Additionally, the field trial system was set up with a cage-locating system based on low-powered radar technology, also provided by Siemens Corporate Technology engineers. Using this system, researchers could quickly learn the X-Y-Z coordinates of any cage in the room, which could save time and boost productivity in real-world animal laboratories.
Product prospects
Ahmed calls the results of the field trials “very promising.” Some issues related to packaging or encapsulation of the MEMS sensor chips to protect them from water during cage wash cycles must still be worked out, he notes. “But we have not found any big technical show stoppers so far.” Current efforts are focused on assessing the data from the trials and determining “where we have to go to make this product available in the market.”
If the business case proves out, a commercialized version of the cage micromonitoring system could be ready by 2007, says Ahmed, and additional products in other industry segments could follow.
Because of the ability to integrate numerous functions—including sensing, processing, power management and wireless communication—all on a single semiconductor device, MEMS technology holds potential for vastly improved building control systems that will, to a large degree, be self-controlling. The ability of MEMS-based chips to process and transmit sensor data wirelessly will greatly reduce installation costs, compared to today’s wired building control systems, says Ahmed. Further, the chips can be very low cost when produced in volume.
Ahmed envisions buildings in the future that will be able to “sense” the comfort level of occupants and instantly adjust settings for temperature, humidity and other environmental parameters automatically. For example, thousands of tiny MEMS sensors could be embedded in a building’s carpet or in the paint on the walls to measure temperature, or the amount of CO2 in the air, and then transmit data to the control system for action. The result would be enhanced worker comfort, as well as improved energy efficiency, perhaps in the neighborhood of 30 percent to 50 percent in some cases, Ahmed says.
Before this can happen, however, improvements in wireless sensor battery technology or in power consumption requirements for the devices will have to be made, Ahmed observes. Such sophisticated wireless building control systems would require frequent sampling by the MEMS devices, on the order of every 10 milliseconds, he says. And this kind of duty cycle is beyond the ability of today’s technology to power the devices for sufficiently long periods. “If we want to make them completely plug-and-play, so they can be used like stickers on the wall, we have to solve the power issue, so that they can last for years before being replaced,” he says. “And right now, the technology is not there.”
That is not to say, however, that highly integrated MEMS devices could not be used in wired applications to provide new capabilities unavailable today with more conventional control technology, or in wireless monitoring applications that require less frequent sampling. For applications in which a sampling interval of say, 15 minutes, is acceptable, today’s battery technology is sufficient to support wireless applications, says Ahmed.
The mouse cage monitoring is one example of such an application, he says. And in human environments, Ahmed foresees applications such as mold monitoring systems in schools. “We have tremendous problems in U.S. schools with mold and moisture, and one of the reasons we can’t do much more today is because of lack of sensing,” Ahmed observes. A wireless network of MEMS-based sensors spread throughout a school that could take periodic samples to detect water leakage, mold growth or allergens in the air could lead to healthier environments for students, he says. In the industrial sector, wireless applications could include industrial equipment monitoring, Ahmed adds.
Additional applications that rely on conventional power wiring may also show promise. “In many cases, you could have very cost-effective wired sensor networks for different applications that go beyond the traditional temperature and humidity controls that we have today,” Ahmed says. Industrial applications might include specialized environmental monitoring and control systems for factory areas in which toxic fumes or vapors are produced, for example. And highly integrated MEMS-based chips might likewise prove cost-effective for use in airports, government buildings and other public spaces for the detection of anthrax, sarin or other terrorist-released substances, says Ahmed.
From an applications standpoint, “we are going to look at the low-hanging fruits from the technical and business point of view for these micromonitoring systems,” says Ahmed. “We are looking into all sorts of applications to see what can be done today, what the market can and cannot accept, and what we can do to remove any barriers in the future.”
For more information, search keyword “MEMS” at www.automationworld. com.
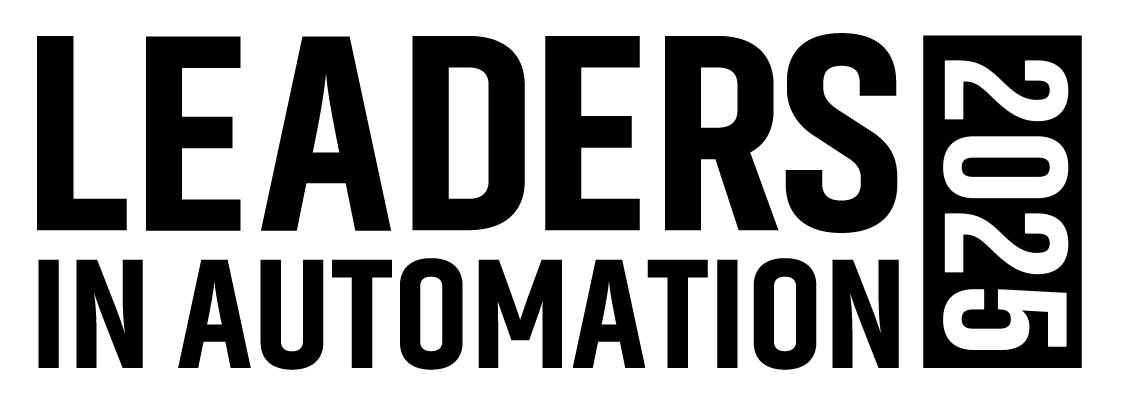
Leaders relevant to this article: