Manufacturing is a tricky business, and the more automated the plant, the trickier things can get. When manufacturers couple automation with the multi-site, geographically distributed nature of their operations, they quickly find that the old way of doing things just doesn’t cut it anymore. Enter Manufacturing Execution Systems (MESs).
In its most basic definition, an MES provides the execution capability to manage workflows and dispatch operations information. For decades, much of this information was handled through manual tasks and paper-based systems, and even today, many companies operate using tags, cards and manually entered data. A more savvy manufacturer may have operators entering electronic data into computers or handhelds, but promulgating that data across production, quality and tracking systems is often an arduous task requiring multiple custom interfaces.
A new generation of MES solutions, based on collaborative practices, is set to change all that by addressing the needs for common platforms, multi-site management and global distribution. From sophisticated electronic equipment to the food we eat and the plates we eat from, MES is positioned to help manufacturers respond to change and manage production throughout a network of assets.
No more red tags
When political luminaries gathered at the White House in Washington, D.C., last month for President George W. Bush’s inauguration ceremonies, there’s a good chance they ate off china plates made by a company that uses MES solutions. Lenox China, a Brown-Forman subsidiary based in Lawrenceville, N.J., and a producer of fine china, crystal and collectibles, has been responsible for all White House presidential china since 1918.
Lenox plants in New Jersey and North Carolina make (an automated process) and decorate (a more manual process) fine china plates. According to Richard Santoriello, senior applications manager, plant floor systems, for Lenox China, the strategic business drivers to move to an MES solution included improving on-time customer delivery, resolving customer back orders, determining accurate customer and product profitability, and responding to market pressure to assume management of customer inventory levels.
These strategic drivers resulted in several tactical drivers. The company needed to reduce and control process cycle times, improve inventory accuracy, increase visibility of work-in-process (WIP) and eliminate spreadsheets and redundant data. Says Santoriello, “In the old way of doing things, we would run around the plant floor putting red ‘priority’ tags on work orders. The problems we had were low inventory visibility and a lot of WIP.”
Lenox formed an MES steering committee and hired an experienced MES integrator to create, approve and deploy a common foundation for MES. Key issues included training, project leadership, information access, and strategies for archiving and integration. Says Santoriello, “You must encourage plant ownership. Plant personnel love these systems and say to me, ‘If you take this away, I would be lost.’ ”
The common platform approach allowed the system to be deployed across multiple plants. The improved visibility has resulted in consistent and uniform yield calculations, a 25 percent increase in WIP accuracy, and a 62 percent decrease in items in WIP.
See it, control it
Manufacturers who wrestle with visibility issues can derive many benefits from MES solutions, especially when applied in complex, multi-tier organizations. Says Jonathon Siudut, executive project manager at IBM Software Group, White Plains, N.Y., “Visibility is a big issue in manufacturing, particularly in the automotive and aerospace industries with their many tiers of suppliers. What used to happen within the four walls of a plant, is now spread among multiple plants in multiple locations” and even among multiple companies.
The new MES solutions have to function across large information technology (IT) networks, but provide a virtual single plant view. Among the challenges is dealing with disparate data, because each component has its own IT system.
IBM provides middleware, modeling and integration tools, such as its WebSphere platform, to architect an MES environment. Says Siudut, “We take a database product and work with our partners and Services group to layer on top of it a business solution.”
Alison Smith, senior research analyst with AMR Research Inc., in Boston, explains how MES business solutions vary from industry to industry, depending on the type of manufacturing. “In high-tech semiconductor manufacturing, there are few or no manual operations, and the MES is tightly integrated with equipment automation,” says Smith. “Medical device manufacturing is more labor intensive, with some manual data entry, such as the use of bar coding, but it requires (the MES functions of) traceability and historical record tracking.”
According to Smith, the pharmaceutical and batch processing industries, such as food and beverage, are also seeing a lot of growth in MES application. “Compliance regulations are driving spending, and pharma executives are starting to construct the architectures that will take them forward in the next ten years. This year, we will see several pharmaceutical companies roll out new architectures, and MES will play a role in these systems.”
Continues Smith, “Another major development is in the area of quality management systems.” The MES captures audit trails and quality data, and integrates that with production systems.
Global food and beverage brand leader, Kraft Foods Inc., headquartered in Northfield, Ill., has launched a major MES initiative, a large part of which focuses on its Manufacturing Quality Future State (MQFS). Walt Staehle, director, shop floor systems, says productivity and quality are intimately intertwined. Kraft selected the Simatic IT solution from Siemens AG, Munich, Germany, because, says Staehle, it provided the links needed between the production and laboratory information systems.
Karsten Newbury, general manager for the Process Automation and Manufacturing Execution Business of Siemens, in Spring House, Pa., believes the increased focus on MES comes because companies are realizing that Enterprise Resource Planning (ERP) systems alone aren’t driving enough benefits—manufacturers need to link ERP to production. “A successful MES implementation starts with a good understanding of the business objectives, then defines the functional requirements, such as reduced reworks or improved quality, then moves to definition of the technology component,” says Newbury. “It’s important to remember that MES is not just about technology. It’s about business processes, and requires senior executive buy-in. Since most manufacturers don’t replace everything at once, MES involves migration, implementation, evolution and strong project management.”
Quality trending
The ability to collect real-time data and track the “as built” status of each component in an assembly is what led KLA-Tencor Corp. to an MES solution. With headquarters in San Jose, Calif., KLA-Tencor is ranked as one of the world’s top 10 suppliers of semiconductor equipment. Formed in 1997 through the merger of KLA Instruments and Tencor Instruments, the $1.5 billion company specializes in process control and yield management solutions for chip manufacturers.
Says John Moore, eQuality program manager at KLA-Tencor, “We provide the enabling equipment to make next-generation chips. The chip technology is so sophisticated—down in the nanometer sizes—that manufacturers can’t even see what they’re making. We deliver light-based, electron beam inspection technologies in multimillion dollar assemblies to very demanding customers.”
While KLA-Tencor manufactures multi-component products in relatively small quantities, it faces the same challenges as its customers, such as Intel, which make extremely high-volume products. Notes Moore, “Like other manufacturers, we have to be first to market with a product that offers the best performance at the best price.”
Moore had experience working with ERP systems, but started looking into MES solutions because he saw a lack of ability to trend quality data from design through production. “Our equipment is low volume, engineered to order and has numerous sub-assemblies, which can require significant changes in production. I knew there had to be a better way to improve quality and track components.”
He selected an MES solution from Datasweep Inc., also based in San Jose, which has been cited by the research firm of Frost & Sullivan as the leader in the pure-play MES market, particularly in the electronics and medical devices industries. Says Moore, “There were two features I wanted in the Datasweep solution. One, a Web-based architecture, and two, the collection of as-built data for every component and sub-assembly in production.”
KLA-Tencor installed a modest Datasweep pilot project across two divisions in 2000, at the peak of the semiconductor industry demand cycle. While the pilot was a success, a full-scale project never really took off, primarily because the company was just too busy shipping product.
With the subsequent downturn in the chip business came the opportunity to expand the MES solution across the company to four geographical sites—one in Israel, one in Massachusetts and two in northern California. Of 5,000 total employees, almost 1,400 now use the MES software in design and manufacturing operations. Moore’s next push is to bring the MES to the company’s service operations.
When KLA-Tencor’s chief executive officer asked for a post-implementation return-on-investment (ROI) analysis, Moore did a month-long survey of 100 users across the system, including planners, supervisors, operators, purchasing personnel and directors. Says Moore, “While it’s a difficult exercise to calculate ‘before’ and ‘after’ trend lines, this really helped solidify gut feelings with hard numbers.”
The data showed that, with the MES solution, the company responded to non-conformance issues twice as quickly as previously, it improved employee productivity an average of 18 percent by reducing meeting times at shift changes, and it decreased manufacturing cycle time by 7 percent, which amounts to four days of production. “By eliminating defects in components before they’re assembled into the final products, we reduce repairs and accelerate new builds,” says Moore.
KLA-Tencor is in the process of migrating from an Oracle ERP system to one provided by SAP AG, of Walldorf, Germany, and one of the project goals is to better align the ERP with the Datasweep MES. However, says Moore, “We don’t want to pay a high IT cost to customize the interfaces. It has taken us a couple of years to build the data bridges between our systems.” With support growing for the S95 integration standard from the Instrumentation, Systems and Automation Society (ISA), Moore believes software vendors such as SAP will build better standard interfaces to the MES.
Scalable and collaborative
Another major trend in MES is the demand for scalable solutions designed for collaborative manufacturing. Recently, the Manufacturing Enterprise Solutions Association (MESA) International, an organization of vendors and users dedicated to promoting MES solutions, released a white paper on the “Next-Generation Collaborative MES Model.” Described in the paper are the collaborative MES, or
c-MES, practices for publishing and distributing customer demands across the manufacturing supply chain.
Charlie Gifford, a senior project leader with GE Fanuc Automation Inc., in Albany, N.Y., described c-MES in a presentation at the 2004 MESA Conference, held near Chicago last September. Gifford says the new model redefines the core MES functions originally outlined by MESA, and now comprises eight major functions that interact with systems and people, inside and outside of the enterprise.
According to Gifford, the next-generation model highlights the following:
Public MES standards and methodologies have matured
The role of MES has expanded to the supply chain
Configurable MES libraries, templates and components have reduced development time and customization
c-MES requires business and IT skills
ROI is greater, due to more functionality at lower costs.
Tim Sowell, vice president of product strategy for Wonderware, an Invensys company based in Lake Forest, Calif., says he is seeing a dramatic increase in requests for proposals (RFPs) from companies looking for worldwide standardization on MES. “Our customers want scalable solutions to manage plants throughout the supply chain.” Sowell notes that, while the numbers of products manufacturers make are staying the same, and even increasing, the total number of worldwide manufacturing facilities is declining. “A machining line originally designed to make two products may now make 12 different products,” says Sowell.
The issues of flexibility, integration and geographical distribution are increasing demand for collaborative MES solutions. Many experts believe that the home-grown MES systems no longer fill the bill. New solutions will leverage scalable, reusable components, common data platforms and integration standards for linking the design, production, business, customer and supplier layers. As well, MES systems will need to address security and firewall issues, demand-driven manufacturing and supplier-managed inventories. Recognition of these needs, coupled with technology developments and acceptance of standards, will promote true collaborative solutions.
For more information, search keywords “MES” and “software” at www.automationworld.com
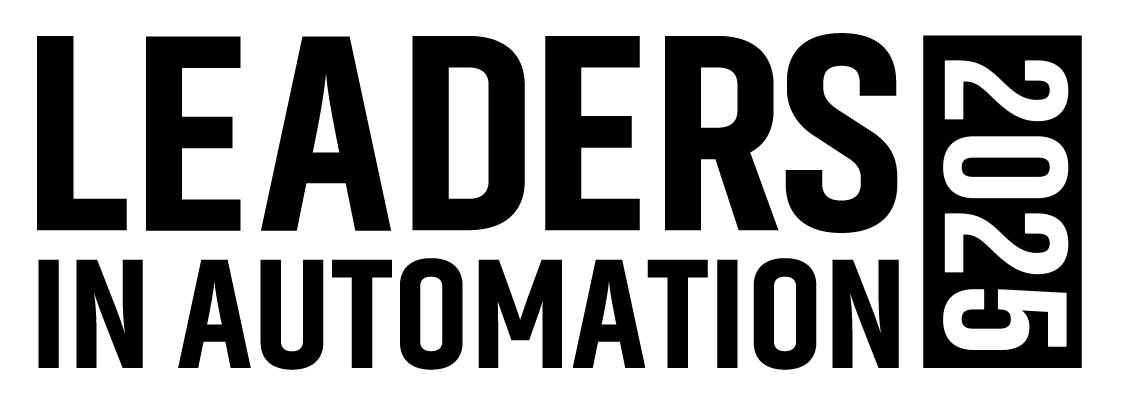
Leaders relevant to this article: