The digital revolution is moving deeper into production facilities, extending right down to the multitudes of sensors that monitor temperature, pressure and many other conditions. These analog sensors are adding more functionality, digitizing data and often doing some preliminary processing before sending information to controllers.
Process sensors are helping plant managers in their ongoing effort to increase output and improve quality by providing continuous monitoring of critical parameters. Digitized data can be transferred with greater speeds and higher accuracy than analog information, providing operators with more input for both operating parameters and diagnostic monitoring.
Productivity gains are often a result. When sensors do a bit of the processing, controllers can respond quickly if parameters start drifting out of range. This can help machines run closer to peak speeds while improving quality and reducing waste production.
“When reactions happen fast, process sensors can provide real-time data. You can even do statistical process monitoring in Fieldbus devices,” says Evren Eryurek, director of PlantWeb Technology at Emerson Process Management, in Eden Prairie, Minn.
The groundwork for this transition to intelligent networked process sensors was set several years ago when Hart devices emerged. The Hart protocol—which originally stood for Highway Addressable Remote Transmitter and was developed by Rosemount, now part of Emerson Process Management—is now managed by the Hart Communication Foundation in Austin, Texas. Hart-enabled devices provide data transmission with both a
4-20 mA component and a digital component, and can be used in any application, regardless of the parameter values that limit discrete devices to specific tasks. Introduction of Hart coincided with a focus on managing assets for maximum benefit.
“Intelligent sensors changed the paradigm of asset management, helping operators in their push to get as much up-time as they can,” says Tanmoy Basu, networking engineer at Siemens Process Automation, of Spring Hill, Pa.
Now the sensors are being used in conjunction with fieldbuses and faster backbones to provide real-time information to operators, maintenance personnel and even front-office workers. The trend toward enterprise-wide networks that operate seamlessly relies on process sensors that provide information to keep factories running at peak levels.
In pharmaceutical production, for example, minor variations can easily ruin batches, Eryurek notes. If data is provided in real time, these variations can be corrected before problems arise. With modern process sensors, chemists can monitor parameters with high precision to avoid ruining production runs.
Fieldbuses such as Profibus and Foundation Fieldbus are gaining acceptance by providing real-time information in entirely digital communication architectures. The Profibus protocols, which are managed by Profibus International, provide specifications for discrete device networking (Profibus DP), process networking (Profibus PA) and Ethernet TCP-IP (Profinet), among others. Foundation Fieldbus, which is managed by the Fieldbus Foundation, focuses on process applications, with protocols for robust and safe process communications and high-speed Ethernet connections. “We’re seeing increased activity in Foundation Fieldbus,” Eryurek says.
Catching The Bus
Today, there’s a focus on making this real-time information more useful to operators. The more data managers have, the more efficiently they can run their operations. “Providing real-time information that can be integrated into asset management is not something designed in as an afterthought. It has to be built as part of the digital control system’s software,” Basu says.
While fieldbuses provide maximum benefit in new systems, the combination of process sensors and fieldbuses can bring significant benefits to legacy operations. These fieldbus architectures make it simple to add capabilities to existing plants.
For example, Emerson’s 3420 interface module makes it possible to communicate with up to 64 devices. These devices can be viewed using an intranet connection. Process sensors communicating over Foundation Fieldbus have far more speed than using 4-20 mA links, Eryurek adds.
These changes have dramatically altered the way that plant managers view systems. Previously, systems ended with the physical boundaries for each piece of equipment. But the boundaries are blurred with networks and process sensors.
“As you build systems, it no longer ends at a 4-20 unit’s I/O (input/output) termination, because the boundaries of a system have shifted. With the adoption of intelligent sensors, the system includes the farthest field device,” Basu says.
Getting away from 4-20 mA wiring also eliminates many of the vagaries that come with the many conversions of analog signals as they travel through paths with many digital modules. Basu likens those analog transmissions to “smoke signals” that are difficult to control precisely. “Once you capture data in an intelligent sensor, it remains digital for life, so the impact of ambient conditions is minimized,” Basu says.
The push for productivity is prompting an increased focus on linking factory floor equipment to the front office. That meshes with a need for more bandwidth in the factory. The result is a push to the most popular network around.
“Open Ethernet has had by far the greatest demand over the last six to 12 months. Everybody wants more data from the factory, and they’ve put in backbones with CAT-5 (Ethernet) cable or fiber optics,” says Scott Saunders, strategic marketing director at Moore Industries International Inc., of North Hills, Calif.
Using Ethernet makes it possible to add more intelligent sensors and share the data they provide with more machines that might need that data for related tasks. Using Ethernet cabling makes it far easier to add new digital control systems than is possible with conventional 4-20 mA wiring systems used with Hart devices and other older technologies.
“Networks allow larger packets to be shipped, so you can add virtually unlimited features without adding unlimited wiring,” says Helge Hornis, intelligent systems manager at Pepperl+Fuchs, of Twinsburg, Ohio.
While there’s a big push toward Ethernet, observers note that many process sensors and other products still connect to networks with the two wires of 4-20 mA schemes.
“Today there aren’t a lot of measurement transmitters, valve positioners and the like available on Ethernet. While Ethernet will become a mainstream field bus for process plants, we still need to find a way to power field devices over the pair of wires that the process industry loves,” Basu says.
Ethernet is starting to make an impact in high-performance sensors, which may open the door for a shift by more mainstream sensors. For example, vision sensors are coming down in cost, so some operators are now using them to provide real-time feedback in applications that run at extremely high speeds. In these simple operations, the cameras are doing little more than sending alarms when the process is sliding outside of specifications.
“In a bottling line, a vision sensor can see if a label is being positioned too high or low and get it back into spec. That’s much different than saying whether quality is bad and something should be rejected,” says Mark Sippel, principal product marketing manager for In-Sight Vision Sensors, at Cognex Corp., of Natick, Mass.
Getting Smarter
As the concept of adding intelligence to sensors has grown, so has the amount of intelligence housed in process sensors. Like all of today’s electronic systems, these sensor modules are reaping the benefits of the semiconductor industry’s abidance of Moore’s Law (named after Intel Corp. co-founder Gordon Moore), which states that semiconductor density doubles every 18 months.
That’s translating to substantially better performance for companies that replace standalone sensors. By combining a 40 MHz, 8-bit processor with a temperature sensor and other components, Moore Industries offers better performance than many discrete products.
“We put a 20-bit analog-to-digital converter in our Ethernet I/O module, and it has better resolution than most transmitters,” Saunders says. That provides temperature resolution of 0.003 degrees Fahrenheit, precise enough for demanding industries.
The evolution of microprocessors is just one aspect of increased performance. Digital signal processors (DSPs) are running faster and have improved development tools, making it simpler for designers to employ them in applications that need faster math processing than general purpose microprocessors can provide.
“Many smart devices are starting to move to DSPs, which are able to extract more data from sensors,” Eryurek says. He notes that in a voltmeter, the DSP chip has the mathematical capabilities to perform frequency analysis. DSPs also make it possible to run more diagnostics. “With new process sensors, you can do normal controls and also run the same diagnostic algorithms you would run on the control system,” Eryurek adds.
Though capabilities are increasing, product developers are focusing on simplified setup. Much of the processing is fairly invisible to operators and integrators. Often, they simply respond to a few queries, entering familiar data points used for conventional sensors. “Programming is easy. It’s mainly setting high and low ranges for alarm point. Now you can do that from a central station that can sit miles away,” Basu says.
Too Much
Though there are many benefits, a potential quandary arising with the use of intelligent sensors is an overload of data. The information explosion that’s been a problem in some offices may be coming to the factory floor.
One way to avoid operator overload is to make it simpler for users to access the data they want. Graphical user interfaces are used in many systems, reducing the number of steps and instructions that they have to recall when they want to see how the equipment is running. Others opt for Web-like instructions.
Another way to avert this problem is to give measurement data to operators on the floor while sending diagnostic data to remote controllers. “Operators do not need to be further burdened by additional diagnostic alarms, and likewise, the measurement or process alarms are kept away from the maintenance folks,” Basu says.
While this diagnostic information might be annoying to operators and plant managers during day-to-day operations, the ability to monitor equipment closely is critical for maintaining optimal performance and reducing downtime. One major benefit of diagnostic information is that it can reduce the need for extensive manual examination.
For example, valves on large equipment can get coated over time, reducing performance as deposits build up. Traditionally, these conditions were spotted only when a valve clogged or during scheduled maintenance examinations. But pulling expensive valves apart during maintenance is time consuming, and can cause problems if repairs aren’t done correctly.
Having sufficient diagnostic data can make maintenance more effective. “If you’ve got 150 to 200 control valves in a plant, you can focus on valves that need repair during your scheduled maintenance shutdowns and avoid unnecessary work,” Basu says.
Determining where and how to send data from process sensors depends in part on how much data they generate. There are often hundreds of these devices in a facility, so the total amount of data they provide can be significant.
For more information, search key word “smart sensors” at www.automationworld.com.
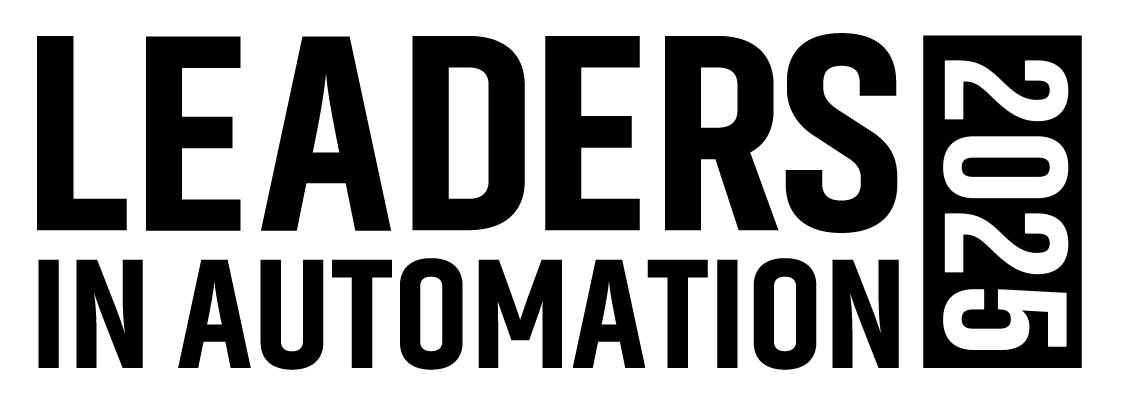
Leaders relevant to this article: