Decisions, decisions…You make them every day on your job. So too do other employees at your manufacturing company, whether they are shop-floor operators, mid-level managers or top-floor executives.
Some decisions, such as whether to eat that day-old, tuna-fish sandwich for lunch, could have a direct impact on your health. But for this story, we are talking about the decisions that you and your co-workers make daily that impact the health and performance of your company. And just as you would probably decide against the tuna fish if you knew that it had gone unrefrigerated for a few hours, so too might your job-related decisions be altered if you had certain key pieces of information about your company’s manufacturing and business operations.
For example, you would probably decide to take immediate action if you knew that a large percentage of parts being produced by a particular machine under certain conditions were coming back defective from the field. Or, if your job includes approval of capital expenditures, you might decide to nix a spending request if you had operating information showing that a certain new piece of equipment would do nothing to solve a problem or alleviate a bottleneck, despite the claims of the manager who was asking for the money.
Getting it right
One inhibitor to faster, better-informed decision making has traditionally been that all of the support data needed is typically stored in multiple, disparate factory and enterprise systems. As a result, getting the right data in the right context to the right people at the right time to provide support for smarter, proactive decision making has been difficult.
But help is on the way. According to industry analysts, there’s an emerging, new class of manufacturing software that is designed to provide visibility to the key information that manufacturing employees at all levels need to make faster, smarter, on-the-job decisions. The technology goes by a variety of names, and vendor products vary in their approach. But they all share certain characteristics.
“One of the main things that these products have in common is a broad set of data connectors to connect to legacy applications in the plant, such as HMI (human-machine interface) systems, data historians, enterprise asset management systems, MES (manufacturing execution systems), laboratory systems or whatever it is in the plant,” says Greg Gorbach, director of collaborative manufacturing research at ARC Advisory Group, in Dedham, Mass.
Data collected from these disparate sources is then typically put through a data management layer or function that provides context to the data. The information is then presented as services—either through methods such as portals, Web browsers, cell phones or other systems that can be used by people—or in a slightly different format for use by other applications, Gorbach explains. “Once you get access to the information through this kind of technology, then it’s a small step to put an application such as decision support, quality or analytics on top.”
Gorbach says this product area, which he describes as “information and integration,” is one of three general categories that make up what ARC classifies as production management systems. The others are “planning and scheduling,” and “operating and execution.” And within the production management systems space, the information and integration category lately “has really taken off and taken on a life of its own,” Gorbach observes.
Pioneer vendors in this category, says Gorbach, include ActivPlant Corp., of London, Ont., Canada; IndX Software, of Aliso Viejo, Calif., which was recently acquired by Siemens; and Lighthammer Software Development Corp., based in Exton, Pa. But there are other vendors that are not far behind, Gorbach adds. “At one of our recent ARC Forums, I lost count of the number of people who came up to me and said that they were building or introducing a new product in this space.”
This is hot
At AMR Research Inc., in Boston, Vice President Bill Swanton agrees that the part of the market that his company calls enterprise manufacturing intelligence (EMI) is heating up. “In terms of the production-oriented applications, it’s one of the fastest growing areas right now,” Swanton says. “One of the reasons is that it’s something that generates value quickly, and it doesn’t disrupt your manufacturing operation,” he adds, “whereas with lots of other things, you have to make changes in your manufacturing to use them.”
Core capabilities of EMI include the ability to aggregate data from multiple disparate sources, including both real-time production data and business-oriented transactional data. EMI solutions can then provide context and analysis, and deliver the information when and where needed. Sometimes that means feeding relevant data to an enterprise resource planning (ERP) system provided by SAP AG, Walldorf, Germany, or by another ERP vendor. Or it may mean sending the data to a visualization system, which can provide easily understood graphical representations that show the interrelationships among various data sets, based upon the needs and the roles of the individuals viewing the information.
“With the Internet today, I can build lots of enterprise-wide applications that can be used completely in parallel, almost seamlessly on peoples’ desktops for decision support,” Swanton explains. “So I could be showing one guy a transactional screen from SAP, a sales-oriented screen from a business warehouse, and a manufacturing capacity and yield screen from a manufacturing intelligence system that’s combining some data from SAP with some data out of the production systems.” Other users would see entirely different screens and information sets based on their roles and responsibilities within the organization.
Like ARC’s Gorbach, Swanton also sees a raft of vendors racing to fill the space for better plant intelligence and decision support tools. Data historian vendors such as OSIsoft Inc., San Leandro, Calif., and Aspen Technology Inc., Cambridge, Mass., have been building out their real-time analysis and visualization capabilities to include higher-level analytics, extended visibility and connectivity to ERP systems, Swanton says.
Traditional automation vendors are also moving into the fray. “GE Fanuc (Charlottesville, Va.) has assembled products from Mountain Systems and Intellution (both recent acquisitions) to come up with a fairly good set of offerings that have a lot of these same attributes,” Swanton points out. And others, including Milwaukee-based Rockwell Automation, and Wonderware, a traditional HMI vendor based in Lake Forest, Calif., and now part of Invensys, also play in the space.
Quick data access
One user who can vouch for the value of the latest Web-enabled analysis and decision-support tools is George Troy, lead engineer, control systems group, at Aughinish Alumina Ltd., an Ireland-based alumina refinery. The company, which produces 1.5 million metric tons of alumina annually, relies on a PI System data historian, supplied by OSIsoft, to record data from the plant’s Honeywell TDC 3000 distributed control system (DCS). In addition to its links to the process control network, PI is also connected to the plant’s business administration networks.
In 2002, Aughinish developed a Web-based plant information system called Business Process Improvement (BPI). The system was designed to provide immediate access for the plant’s 470 employees to real-time and historical process information stored in PI, as well as to other plant data. BPI was driven from the top down, says Troy. “Basically, our managing director didn’t want anyone to have to dig deep for key pieces of information regarding asset performance or engineering data. He wanted people to be able to lay their hands on it within 30 seconds.”
The BPI system makes use of analysis tools and other components of OSIsoft’s Real-time Performance Management (RtPM) platform, as well as other, third-party analysis systems, to deliver decision support via the Internet. Web-based home pages, accessible using standard Web browser software, are customized to employees’ locations and job responsibilities. These pages provide real-time information on production—both plant-wide and in the user’s local area—along with personal tasks, daily logs, key performance indicators (KPIs) and vulnerabilities.
At the plant-floor level, operators use the BPI system to make better informed decisions on a daily basis. “In our plant, dilution, or water ingress, can be a serious problem, and one big cause is faulty glands on pumps,” says Troy. Flowmeters monitor gland water usage at the plant, which is recorded in PI and compared against target usage levels developed by management.
“By looking at the BPI page, an operator can see very quickly from the numbers presented, and also in color-coded bar graph fashion, whether the section is on target or not,” Troy explains. “And the operator can also see the trend of an ingress over time, whether the degeneration is rapid, or whether it is something that’s been happening over a number of shifts.” Based on what is seen, the operator might decide to attempt to tighten the gland, or if the degeneration is gradual, might instead decide to bring up the matter at the next regularly scheduled meeting, Troy says.
Aughinish engineers and managers also use the BPI system in a variety of ways. Process engineers may typically look at a handful of PI data tags when they arrive at work each morning to get a quick snapshot of how their sections of the plant are operating, and to see if any matters need attention, Troy reports.
Data on key plant control loops is also collected automatically on the plant’s Honeywell DCS system and sent electronically to Loop Scout—a remote, control-loop management service operated by Phoenix-based Honeywell Automation & Controls Solutions—which analyzes the data and sends back daily and weekly reports. The reports help engineers and operators quickly spot loops that need attention, says Troy.
Another tool that plant engineers find particularly useful for decision support, Troy notes, is Curvaceous Visual Explorer (CVE), supplied by Curvaceous Software, of Birmingham, England. When used with PI data that has been loaded into Microsoft Excel through OSIsoft’s DataLink, CVE allows Aughinish personnel to illustrate multiple variables and their interrelationships over time on a single screen plot. Parameters such as current, density, flow, temperature or pressure can be compared as a way to spot trends and process drifts.
Aughinish managers also use PI data as an aid to making better capital spending decisions. “When you have a capital program, everyone is lobbying for a pot of money, and some people can shout louder than others, and there’s a certain amount of politicking that goes on,” Troy observes. “It happens in every plant.” So when capital requests are made, management often asks for supporting data drawn from PI.
Say, for example, that an engineer reports that a pipe is undersized and is causing a problem, and that a new, larger pipe is needed. Before approving the expenditure, the capital committee might ask for a histogram showing a year’s worth of flow data for the valve opening for that pipe, based on the projected flow rate needed for future operations, says Troy. “If you see it at 105 percent most of the time, then you may take the guy’s statement as factual,” he notes. But if the numbers show something less, then the engineer might be asked to check other data. “Sometimes, people fix symptoms instead of the problem, and it might be the pump instead of the pipe,” Troy observes. “So if you see that the pump has been drawing less and less amps over time, then it’s probably got an impeller problem.”
Smarter spending
Aughinish has been using PI System data in support of its capital programs for about two years, says Troy. “It has altered the way we make capital spending decisions,” he notes, “and it has also made the people looking for capital far more analytical.”
In general, Troy says that the use of PI—first installed at the plant in 1989—along with the latest analysis and visualization tools, has instilled a new culture throughout the company. “We really don’t want to look at paper-based data any more,” he says. “Everyone demands to see electronic data, with numbers and things on the screen that give us an accurate analysis of what’s happening.”
The ability of today’s systems to assemble and contextualize data from multiple sources and present it in a meaningful way can be an eye-opener for many manufacturers.
“A lot of companies don’t know what they don’t know,” says Dennis Cocco, chief executive officer at ActivPlant Corp., whose ActivPlant enterprise manufacturing intelligence platform is focused for use by discrete manufacturing companies.
While data historians intended for use in the process industries have long been around, a similar historian-type product designed for the discrete manufacturing industries has until recently been missing, Cocco contends. ActivPlant’s Universal Factory Data Model, part of the ActivPlant platform, fills that role, he says, as a repository for data collected from plant floor machines, controls, robots, gages, sensors and the like. When this real-time plant floor data is combined with appropriate data from various enterprise systems and delivered in a meaningful way via Web browsers and other means, users are empowered to see their data and their operations in new and often illuminating ways, Cocco says.
For example, says Cocco, management at a plant that manufactures 50 or 60 different products will likely have aggregate data that shows whether or not the plant is making money overall. But they may not necessarily have the ability to see whether a specific product within that plant is profitable. When job-costing information from enterprise systems is integrated with production data using an EMI system, however, that information can be made visible, Cocco says, and it often provides a strong basis for actionable decisions.
“One of the things that we hear from our customers is that they feel that we’ve made their ERP investments much more valuable, because now they have better decision-making tied right into their ERP systems,” Cocco says.
Another example of improved visibility can often be seen in batch environments, in which production lines need to be retooled following each product run. “If a rush order comes in, and you don’t know exactly where you are on your schedule, you run the risk of asking the line to be retooled or changed over when it’s very close to the end of its cycle, just because you don’t have visibility on that,” Cocco says. If the changeover is done to accommodate the rush order, then the cost of retooling again to finish the previous production run can have a negative impact on profit. Manufacturers can avoid that kind of bad decision making when production scheduling systems can be integrated with real-time factory data, Cocco says.
At five-year-old IndX Software Systems, now part of Siemens Industrial Services and Solutions, Vice President of Marketing George Bauer likewise believes that the improved decision support provided by the latest operations intelligence solutions, such as his company’s XHQ system, will be a boon to manufacturing.
“Today, you’ve got to have an ERP system and you’ve got to have some level of automation, or you can’t be competitive. It’s a cost of doing business,” says Bauer. “But the real edge going forward—the additional edge beyond the cost of doing business—is going to be found in intelligence that gives you a deeper insight into your markets, and into your own production, than your competitors have,” Bauer declares.
Sweet spot
IndX’s XHQ product relies on a component-based data model to represent data and relationships between data in an object oriented fashion. Designed to aggregate, relate and present operational and business data from multiple sources to users in a coherent fashion for real-time performance management and decision support, XHQ is intended for use across a range of industries. But the product has found its sweet spot to date in the oil and gas marketplace, which accounts for about 80 percent of IndX customers, says Bauer. The list includes major multinational players such as ChevronTexaco.
“I think it’s no coincidence that oil and gas has jumped on this first,” says Bauer. “They’ve got a high-priced, but commoditized product, where just a very slight improvement in their production can really dramatically affect the bottom line.” One of the latest trends is a move to extend the technology beyond the single-plant level, to aggregate data from multiple refineries for delivery to managers at the regional and corporate level, Bauer adds.
Vendors say the paybacks on their systems can be rapid, and are typically obtained in a number of ways.
“We’ve seen customers who achieved a return on their investment, literally, in as fast as one month,” says Kevin Roach, vice president of global solutions at GE Fanuc Automation, of his company’s EMI solution set, which includes the iHistorian plant data historian, along with a range of analytical and production management tools, product genealogy and quality tracking systems, and tools for overall equipment effectiveness.
The one-month payback came when a beverage maker was able to dramatically reduce packaging material waste by achieving better visibility of a production line, and then optimizing production routing, Roach says. But across the board, the average time for customers’ return on investment typically falls between nine and 18 months, he says. In general, the added visibility provided enables users to see ways to get more out of their assets, Roach says. “By understanding where the bottlenecks are, they can decide what to go and fix, and what’s going to have the biggest bang for the buck.”
At ActivPlant, Cocco says that return on investment for his company’s customers averages around six months. The sources can range from overtime minimization—through better use of resources—to quality and warranty cost savings, and reduced use of consumables. “We’ve even had customers who have decommissioned entire production lines because when they got better visibility, they found out they didn’t need them in the first place,” Cocco adds.
In the end, the decision support provided by the new breed of factory intelligence applications is likely to pay benefits from top to bottom within manufacturing operations, sources say. “By the nature of these systems, you can provide operating information to a wide variety of audiences who have different roles and responsibilities, and who participate in different business processes,” observes ARC’s Gorbach. “So in my view, it’s not so much the one big decision that’s going to make all the difference, but rather the thousands of little decisions that are made by lots of people every day.”
Sponsored Recommendations
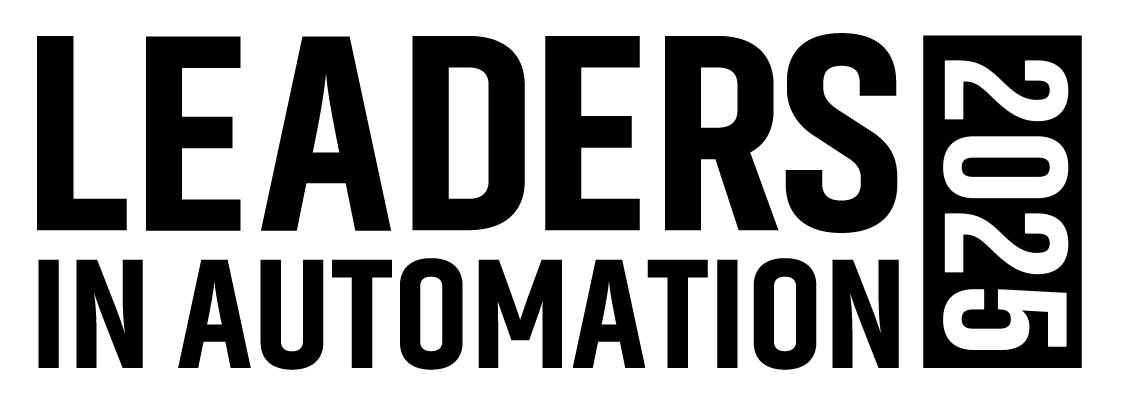
Leaders relevant to this article: