he system calls for an accelerometer mounted to a pump motor that will monitor its health. Information feeds back to an asset management software application that will compile the information, check trends and notify managers when the motor is about to break down. The problem is that the sensor sends a signal in millivolts. Somewhere along the line, the varying electrical signal must be correlated to engineering units (say force of gravity, g) to be understandable to both humans and the software.
This process of correlating the signal to understandable units of measure is known as calibration. The accelerometer must be calibrated at installation and again periodically thereafter, that is, if someone remembers to go back out and perform the recalibration. A technician finds the data sheet, takes electrical measurements and makes the calculations. This must be repeated for all analog sensors in the plant. If a sensor dies, then the data sheet must be located to determine all the specifications of the old sensor so that a new one can be purchased.
If this process could be automated, then manufacturers would not only save money at installation, but also have some assurance that the device would remain in calibration. Suppose that sensors contained an electronic data sheet right inside them that contained all the information that a technician would need to know for proper installation. Further, the sensor would know when it was installed so that it could send a message when it was time to recalibrate. If it was moved, all the information would go with it. When it was time to recalibrate, the technician would not lose time looking for the paper data sheet. Further, the automation system would be able to ping the sensor periodically and ask how much longer until recalibration was necessary. Then decisions could be made about taking the system down for maintenance for business reasons rather than for an emergency.
In fact, that data sheet exists today and is called a transducer electronic data sheet, or TEDS. Proposed standard IEEE P1451 describes TEDS, what the data sheets should contain and how they can be used. Brian Betts, DAQ product manager for National Instruments, the Austin, Texas, data acquisition and automation supplier, explains that finished products that apply the TEDS standard are so new that the company is only just now beta testing their use in systems.
About 50 percent of accelerometers are already TEDS equipped, according to Betts. “We’re just now seeing the hardware and software to read them. A problem is that each vendor provides its own software to read its sensors. National Instruments is taking a leading position in a consortium for ‘plug and play’ TEDS sensors, that is, a standard for the data sheets so that different sensors can be mixed in one system, yet the controller can read them all,” states Betts. Of 22 sensor manufacturers working on the standard, five manufacture accelerometers, says Betts, while others offer load cells, pressure sensors and thermocouples. He explains that the TEDS resides on an erasable programmable read-only memory (EPROM) chip. There is a user-configurable area on the chip where users can write to it every time it’s calibrated.
In operation, the sensor describes itself to the system, including the engineering units it reports, so an accelerometer automatically measures in “g’s.” Because machine condition monitoring is a continuous application, users need to know when the sensor needs to be re-calibrated. The system also enables taking more accurate measurements. Part of the template on the EPROM contains information on typical scaling factors, for example mV/V/g. This becomes a linear number that can be stored in tabular form. The technician can look up and determine the g reading at a particular voltage reading (V). Users can set up a look-up table or polynomial to obtain more accurate readings, enabling better conversion into engineering units.
Not all of the infrastructure is in place for remote monitoring and diagnostics. But the trend is clear. Consider water utilities in the Southwestern United States. Water is a critical resource in short supply. Customers of water utilities want assurance that they are getting the amount of water that they are paying for. Magmeters from ABB, the Swiss/Swedish automation company with U.S. division headquarters in Wickliffe, Ohio, measure the flow and provide the critical billing component. Buried under desert sands, they work continuously. The key billing question relates to accuracy. Are those magmeters still as accurate as when they were installed and calibrated?
Once again, calibration of a field device is critical. ABB has added intelligence and connectivity to the meter, then provided a portable device for technicians to read information about the magmeter. The portable terminal downloads parameters and current information, then saves the charts, trends and other critical information into a database. ABB can provide a certificate of calibration for all the meters that are still within range, or provide information for re-calibrating or repairing those that fail. When sufficient infrastructure is in place, a remote monitoring system will follow.
Change occurs slowly in manufacturing, and there will be many thousands of legacy sensors in use for years. Engineers in those facilities will want to take advantage of real-time manufacturing information and diagnostic aids of smart sensor systems without bearing the pain of complete retrofits. Benson Hougland, Opto 22’s director of technical marketing, says using an intelligent system can turn legacy sensors into smart sensors by driving the level of intelligence and networking to its lowest levels. “For some companies, it’s hard to justify the cost of microprocessor-based sensors,” states Hougland, “but manufacturers can leverage what they have through intelligent input/output (I/O) systems.”
Opto, the Temecula, Calif., automation system and I/O interface manufacturer, provides a variety of methods for users who wish to move data from the factory floor to business systems while leaving current control systems intact. “Don’t think of intelligent I/O systems as just an interface to a controller or signal conditioner, but as a path for data being moved up,” says Hougland. “We’ll do the signal conditioning and electrical interface and also provide a network interface, aggregate sensor data into groups of data and put a level of context to the data to turn them into information. For example, an automation system may just want range data or counts, but the supervisory control and data acquisition (SCADA) system may want real engineering units. Intelligent systems can give sensors that level of intelligence.”
It’s not just the automation and control system that needs sensor data, though. In fact, it probably already has sufficient data for control. It’s the business system that needs up-to-date machine and material status in order to manage the entire supply chain. “If you can provide engineering units to SCADA, then it’s possible to add one other level to the system to give the data real meaning for the business system,” says Hougland. “In many cases information can be fed directly from the sensor to the enterprise resource planning (ERP) system. General Motors personnel have called this ‘guerilla data acquisition,’ where manufacturing information feeds directly to enterprise systems without disrupting the control system.”
Concurrent development of smart sensors and device level networks has led to better process diagnostics. This in turn yields improved machine uptime with a direct impact on the bottom line.
The information provided by the network and its smart devices makes faults easier to pinpoint and correct. Predictive diagnostics offered by the latest generation of DeviceNet sensors can assist in identifying faults before they occur.
Sensors with heart
For example, some Allen-Bradley photoelectric sensors, from Milwaukee-based automation supplier Rockwell Automation, send separate discrete outputs if the sensors fail or experience inadequate application quality. Another A-B photoelectric sensor has a “heartbeat” that is capable of monitoring the sensor, wiring and application characteristics. It issues a continuous pulsed signal, or heartbeat, that will cease transmission in the event of sensor failure, open or shorted wiring, or unstable sensing conditions (high or low margin extremes). It can then send control and diagnostic information on the same wire.
One type of networking that is just beginning to gain some traction in automation is wireless, mesh networking. As the name suggests, a mesh network topology looks more like a mesh than the point-to-point drawing of a typical network. These networks allow individual nodes to communicate directly to multiple nodes. While the solution may be a little expensive to install on a single-sensor system, it is feasible for some multi-sensor applications in locations where the cost of wiring is great.
Peter Stein, vice president of business development for Sensicast, a Needham, Mass., supplier of network components and services, says, “In this relatively new market, building controls and industrial automation are the leading applications for us. We are developing a product for monitoring motor condition. In many cases, the only motors that are continuously monitored are the very large ones, yet if a motor dies an untimely death, the impact on profits can be tremendous. Further, in many cases, pulling wires for additional condition monitoring sensing can be cost prohibitive.”
Stein reports that within industrial automation, the food and beverage industry is currently using wireless mesh networks for temperature and humidity monitoring, and the technology is being used for an automated ventilation system in at least one auto plant.
The evolution of smart sensing for discrete manufacturing includes a new family of discrete sensors from Schneider Electric. This Paris, France, electrical and automation company with U.S. headquarters in Palatine, Ill., leveraged its worldwide sensors expertise to develop a family of configurable sensors under its Square D brand. One model in the family is a photoelectric sensor that is configurable for different sensing modes. This means that one sensor can be installed in any one of diffuse sensing, retroreflective or through-beam modes.
Dave Shutters, controls engineer for Custom Conveyor Inc., of Greensburg, Ind., describes how the sensors help this original equipment manufacturer (OEM) of custom-built conveying systems.
“We design and build custom solutions for material handling,” says Shutters. “I like the intelligence built into the Square D universal photoelectric sensor. We only buy one model for the development of a line. It can be configured for whatever mode of sensing is required for each use. If we discover during a build or trial run that a different mode would work better, then we just reconfigure. If we need to buy larger quantities of sensors after the design and testing is finished, then we can buy a less expensive, dedicated-purpose sensor.”
This type of smart sensor provides a value to the OEM, but what about its customers? Shutters reports, “Even if we supply different dedicated sensors on the final systems, customers can, if they wish, buy just the universal photoelectric sensor for maintenance stock. This means that they only have to stock one type of sensor for maintenance purposes, reducing their inventory investment.”
Something customers are beginning to demand is ready access to manufacturing information that essentially comes directly from various sensors distributed around the plant. Shutters describes the systems Custom Conveyors often uses, “We bring all the sensor data to a programmable logic controller (PLC). A section of memory in the PLC is defined for storing information, such as diagnostics, uptime and other requested manufacturing information. This information is then moved from the PLC to whatever higher level system the customer uses.”
There are a number of other signs of intelligence that can be found in the universe of discrete sensors. Gary Frigyes, product manager for photoelectric sensors at Pepperl+Fuchs Inc., a discrete sensor manufacturer located in Twinsburg, Ohio, describes some of these signs.
“Intelligent, or ‘smart,’ sensors typically feature an embedded microprocessor that broadens their usefulness by offering expanded functionality with features such as remote programmability, self-monitoring (health checking) and the ability to connect multiple sensors on the cable. Coupled with a bus system, intelligent sensors offer a powerful and cost-effective method of automation control.”
Line ‘em up
Aligning sensors for maximum effectiveness is a common problem, not only during installation but also during use. Frigyes notes that manufacturers counter this problem with smart inductive and photoelectric sensors that send data to the controller to indicate when the sensor and target are correctly aligned. This feature can also be used to indicate when a photoelectric sensor lens is dirty.
“Another advantage of intelligent sensors,” says Frigyes, “is remote programmability. This feature of intelligent devices enables users to stock fewer sensors. OEMs might ordinarily keep a supply of normally open and normally closed versions of the same sensor. By using a smart sensor, they need only one version because they can program the output to whatever the application requires.”
Vision systems have progressed from exotic, highly priced sensing devices to devices that are reasonably easy to use and affordable to most manufacturers. Burlington, Mass., vision system manufacturer Coreco Imaging created its “ipd” division to develop and market small, easy-to-use vision “appliances.” Steve Geraghty, ipd director of operations, says, “With the fairly recent integration of machine vision into the Ethernet factory network, it has become a lot easier and a lot more practical for manufacturing to be linked with the rest of the enterprise. This enables real-time reporting of manufacturing statistics, such as number of products run, yield and types of defects found.”
This sounds good in theory, but are manufacturers finding this valuable? Geraghty describes a customer that manufactures packaged goods and has an automated process in which machine vision appliances are used for the purpose of quality control and information feedback. The inspection is to check that the label is present, that the barcode matches the product being run and that the safety seal and plastic cap are present. The inspection is performed at two points along the transport system, as packages leave the labeling station and as they complete their final assembly. Should a package fail either inspection, it is removed from the line. At every step, the inspection information is reported over the factory network to all the applications that require it.
Sponsored Recommendations
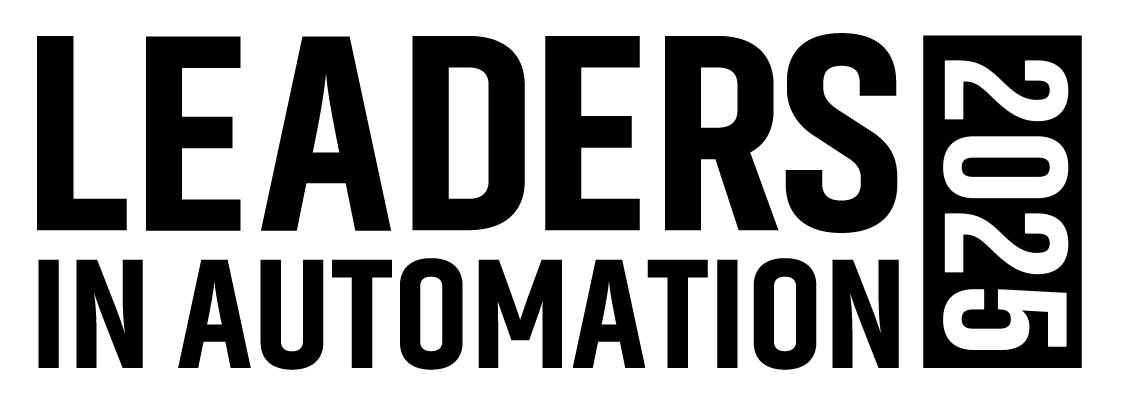
Leaders relevant to this article: