Automation World: What is the Center for IMS?
Lee: The Center for Intelligent Maintenance Systems (IMS) is a National Science Foundation (NSF) Industry/University Cooperative Research Center. Participating universities include the University of Wisconsin-Milwaukee, at which I am a professor and co-director, and the University of Michigan-Ann Arbor, where Prof. Jun Ni is a professor and co-director.
We chose to focus the Center on intelligent maintenance systems in a very broad context. In the narrow view, intelligent maintenance is defined as the prediction and forecast of equipment performance. Using these techniques, maintenance on equipment can be scheduled prior to failure.
Our long view on intelligent maintenance is that we can use any means—including embedded technologies, such as embedded software, and remote technologies—to monitor equipment performance. Then, if degradation starts to occur, there is enough time to trigger service before failure. A machine can self-assess its health and trigger its own service request as needed.
If this model works, then we will have a product in the field that can manage its own service performance and manage its own warranty-based contracts. And, it can alert users on how to keep it running in a high-performance manner. That’s real intelligence!
AW: The center is developing solutions for near-zero-downtime performance. What does this mean?
Lee: When we say “near-zero downtime,” we refer to two areas. The first relates to equipment performance reasons for failure, the second involves operator reasons, such as human error. Near-zero downtime focuses on predictive techniques to minimize failures.
The goal is to predict machine health in the same way that the weather is forecast. We really don’t care about how precise the prediction is, we care about the trend—cold to hot, or clear to rainy. Forecasting gives us priorities and a back-up plan.
Today, machine field services depend on sensor-driven management systems that provide alerts, alarms and indicators. At the moment the alarm is sounded, it’s already too late to prevent the failure. Most factory downtime is caused by these unexpected situations. There is no alert provided that looks at degradation over time. If we can monitor degradation, then we can forecast upcoming situations, and perform maintenance tasks when necessary.
Downtime costs are extremely high. One minute of downtime at an automotive manufacturer can impact production throughputs for up to 45 vehicles. And downtime rates are not the only cost concerns. If equipment starts to degrade, you may start generating parts with unacceptable quality, and not know it for a long period of time.
AW: How is this predictive maintenance approach different from traditional maintenance solutions?
Lee: There are two kinds of traditional maintenance solutions. The first is condition-based maintenance, where machine conditions are constantly monitored and their signatures are evaluated. This is done at the machine level, one machine at a time. The second traditional solution is scheduled maintenance based on equipment supplier recommendations and practices.
Predictive maintenance, on the other hand, focuses on machine performance features. Data come from two sources: sensors mounted on the machine to gather the machine feature information, and information from the entire manufacturing system, including quality data, past history and trending. By correlating data from these sources—current and historical—predictions can be made about future performance.
AW: What role do smart sensors and networks play?
Lee: Many sensors come with a machine, and sometimes users mount additional sensors to retrieve more information about the machine. However, most of the sensors on a machine operate at the data level.
This presents several problems. First of all, you need experts to understand what the data means. In remote applications, or applications in high-security areas, such as medical or defense manufacturers, it’s impossible to send these data out of the facility. And, it is critical that you convert the data into information that’s usable by the system. This is the role of smart sensors—they locally process data, convert it to information, and network the machine-health information, not just the data.
AW: What is the IMS Center working on to help a manufacturer build an information-based approach to maintenance?
Lee:One approach we’re developing is a Watchdog Agent. This is like putting a dog in a machine, and the dog barks depending on how it feels about things or what it “smells.” The Watchdog Agent is a computational tool—embedded in the machine system—which uses prognostics algorithms to convert data into coherent, representable, performance-based information. The approach reduces the need to understand and transmit large amounts of raw data over the network.
A second development is the Device-to-Business (D2B) platform. D2B encompasses the devices on a machine, such as a spindle or a pump. In today’s environment, those devices are connected to a machine controller, which in turn is connected to a programmable logic controller. The PLC monitors the on-off status of the devices, but doesn’t distinguish between a “delayed-on” condition and a “perfect-on” condition. As long as the device is in the “on” mode, there is no additional information conveyed by the PLC.
D2B means that if these devices contain intelligent performance data, they can be directly connected to the business systems, such as the enterprise resource planning systems, and trigger their status to the ERP. Data is deposited into a file, where it is compared to historical trends and sent to relevant personnel—such as supervisors, operators, warranty contractors and machine builders—via e-mails and alerts. This kind of alert system is very interesting because it bypasses the traditional factory monitoring systems, such as PLCs, often with faster connections, using cellular and wireless networks.
AW: What are the benefits of using these methodologies?
Lee: With industry so focused on the bottom line, the cost of downtime has a big impact on profitability. In addition, manufacturers who have outsourced operations to other countries, such as China, need to remotely monitor the quality of products before they are shipped.
The Watchdog Agent and D2B methodologies are game-changing approaches. Not only can they reduce downtime, they also provide the ability to look ahead at the quality of products before they ship, by closely watching machine degradation. Rather than reactive mode maintenance—what we call “fail-and-fix”—companies can move to “predict-and-prevent” maintenance.
AW: How are you working with industry to apply these solutions?
Lee: About 150 people from industry attended the IMS Center’s first workshop in Milwaukee in November 2000. At this workshop, we identified a few areas that we believed were fundamentally critical to achieving our broad vision of intelligent maintenance.
Since that time, we have worked with a number of different companies, both suppliers and users, such as DaimlerChrysler, Ford, GM, Kone Elevators, Mitsubishi Heavy Industry, Rockwell Automation, the United States Postal Service and United Technologies. For example, we’ve worked with Harley-Davidson on a project to extend machine tool life in the factory. GM wants to really understand e-manufacturing and how to synchronize across its supply chain for high productivity and low downtime. Intel can’t afford downtime on its 300 mm wafer fab system. Although these companies all make different products, our prognostic tools can be used across applications.
To participate in the IMS Center’s research and technology development, large companies pay a $35,000 annual membership and small companies pay $10,000 per year. Membership fees are pooled by the Center, so everyone can benefit from the development of common and leveraged engineering tools.
In summary, today’s automation world will focus on sensors and communications. In this world, all products and machines are networked by some means. It’s hard to know what to do with all this data. We need to move the data world to the information world by using computational tools to process data locally.
The automation world of tomorrow is an information world for feature-based monitoring. Information should represent a trend, not just a status. It should offer priorities, not just show “how much.” If we can do that, then automation can be focused on asset-level utilization, not just production rates.
For more information on the Center for Intelligent Maintenance Systems, visit www.imscenter.net, or contact Dr. Jay Lee at [email protected].
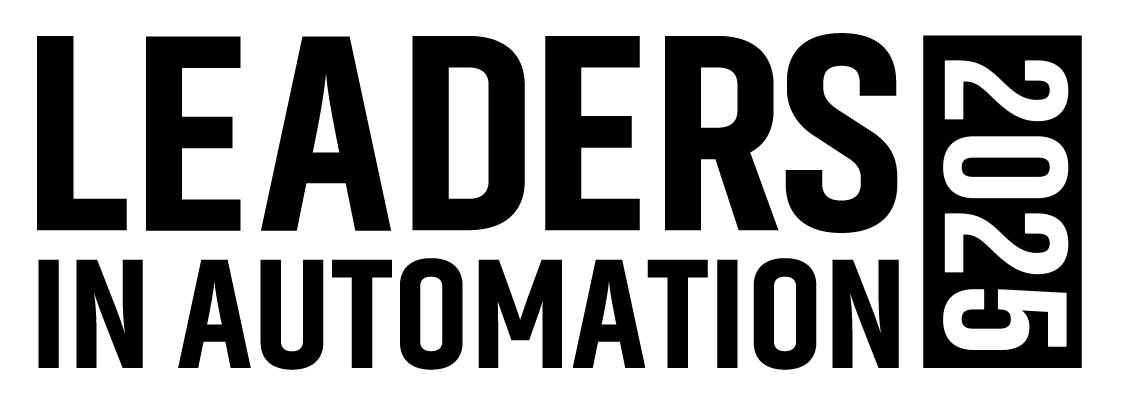
Leaders relevant to this article: