Should I make pulp and paper today, or should I make money? For the operations staff at a paper mill, one might assume that one choice would always equal the other.
But at Abitibi Consolidated Inc., the world’s largest producer of newsprint and value-added paper, the answer to that question is not always a no-brainer—at least for certain mills that have their own hydroelectric power generation capability. Sometimes, if contractual commitments allow, it makes more sense to shut down pulp and paper production and instead produce power that can be pushed onto the electrical grid and sold at high market prices.
Knowing when to do that is the trick. And thanks to a home-grown energy management system that includes capability for real-time monitoring of electric power pricing, Abitibi mill personnel have gained the decision-making tool that they need to better manage their power buying and paper production—even at mills that don’t have electric generation capability.
The catalyst for the system came in 2001, when the Ontario provincial government confirmed plans to deregulate the Ontario electric power market, effective May 1, 2002. Abitibi operates 27 paper mills worldwide, including five in Ontario. That makes the Canadian-based company the largest single user of electrical power in the province. Historically, Abitibi’s five Ontario mills have purchased more than C$100 million ($100 million Canadian) worth of electric power annually.
In 2001, with the prospect of deregulation looming, Abitibi executives knew that electric power in Ontario could soon become subject to wide pricing swings, and that poorly managed power purchasing at the Ontario mills could potentially cost the company hundreds of thousands of dollars. They realized that they needed a system to enable the Ontario mills to track their electric power consumption in real time, along with changing energy market pricing, as an aid to making smarter power-buying decisions.
A search turned up one off-the-shelf energy management system that would work. But the problem, according to Guy Roussel, senior analyst, information technology planning, at Abitibi’s Montreal headquarters, was that the package was priced at about C$3 million, not counting annual support and maintenance costs. “We didn’t have the C$3 million,” Roussel recalls. And at the time, he adds, “We didn’t have a Plan B.”
Yes, we can
But it wasn’t long before Plan B materialized. Working with a team that included personnel from both the mills and corporate headquarters, Roussel began exploring the idea of building an in-house application that could more cost-effectively meet the company’s needs. His conclusion: “We can do it.”
By using systems that Abitibi already had in place and by tapping the programming talent of key staff members, Roussel believed that the company could develop its own energy management system at a fraction of the C$3 million price tag of the packaged system. And the company could do it ahead of the May 2002 deadline, which by then was only six months away.
One key to the plan was Abitibi’s existing PI System data historian systems, which are part of the Realtime Performance Management (RtPM) suite of products provided by OSIsoft Inc., San Leandro, Calif. PI Systems were already in place in 18 Abitibi paper mills, including four of the five Ontario mills, where they were used for production data collection and reporting. They were linked to equipment such as distributed control systems and programmable logic controllers via human-machine interface software. Because they were on the critical path for managing production at each mill, Roussel knew that the PI systems could be tapped to provide the data needed for the energy management project, including electric metering information.
Abitibi added a PI server at the Ontario mill that didn’t have one, and a second at the Montreal headquarters, which would serve as the control center for the entire power management application. Data links and PI-to-PI interfaces were set up between the remote PI servers in each mill and the center in Montreal.
The next step was to link the system to electricity market information and other pertinent data that was available on the Internet. At the time, OSIsoft was developing a HyperText Markup Language (HTML) interface for PI that would enable such links, says Roussel. So Roussel worked directly with the developer of the HTML link at OSIsoft, and “within two months, we had it up and running and tuned,” he relates.
The HTML link provided the ability to connect Abitibi’s PI servers to a new Web site operated by the Independent Electricity Market Operator (IMO), a not-for-profit organization that was formed as part of the restructuring of Ontario’s electric power industry. The IMO site provides real-time spot market electric energy pricing, as well as hourly pricing and next-day pricing forecasts. Roussel also set up links to the Environment Canada Web site to collect real-time weather information that could impact electric power pricing. He also connected to Web sites that provide data on natural gas and crude oil futures markets.
Top level support
By October 2001, when work had begun on the project, the solution was officially known as the ACI Energy Management System (EM-SYS). The project had the full support of Abitibi top management, Roussel notes, and he was able to get the resources needed for the effort, including the temporary assignment of key programmers and specialists from various company locations. One good thing about dealing with immovable deadlines, such as the May 1, 2002, deregulation date, is that it forces people to work together for common goals, Roussel observes.
In the end, the EM-SYS project was completed in less than six months, in time to meet the deadline, and with a total budget of just C$77,000, says Roussel. That’s a far cry from the C$3 million expenditure that the packaged solution would have required, not to mention an estimated C$300,000 to C$450,000 in annual support and maintenance costs, he notes. And given the price increases and market volatility that erupted once deregulation occurred, the home-grown system has already paid for itself multiple times over.
Prior to deregulation, consumers and corporations alike were paying a fixed rate of $43 per megawatt/hour (MWh), says Roussel. But after deregulation, pricing quickly established itself at rates that were not only significantly higher, but also subject to variations and price spikes. From May to December of 2002, for example, the average cost was $52 per MWh. But from January to April 2003, the average went to $75 per MWh, due primarily to cold Canadian weather conditions. Further, due to generator failures somewhere on the power grid or other unusual circumstances, price spikes could be extreme, with spot pricing sometimes even occasionally touching the Ontario legal limit of $2,000 per MWh.
In this environment, the EM-SYS system has proved an invaluable cost saving tool for the Ontario mills, by enabling them to see and react to fluctuating energy market conditions. During the first year of the system’s operation, for example, IMO pricing information accessible through EM-SYS showed at one point a peak price of about $800 per MWh. One Ontario mill reacted and altered its production operations to reduce power consumption, says Roussel. But personnel at another mill looked at the data and doubted that the pricing information was accurate. At the end of the hour, the staff called the IMO to verify the data. It was correct, and that hour cost that mill tens of thousands of dollars, Roussel relates.
For mill personnel, the heart of EM-SYS is the Control Center screen, which allows operators and managers to look at any of the five Ontario mills to make comparisons between their planned demand and their actual load consumption. Staff can also monitor current and projected electric energy prices, aggregate demand for the whole Ontario power grid, prevailing weather conditions and forecasts, and energy futures data.
The EM-SYS system pulls pricing from the IMO Web site on three price variants. The first is the Real Time Energy Market (RTEM), which is basically the spot market for electricity. This pricing is updated every five minutes. In addition, the system monitors the Hourly Ontario Energy Price (HOEP), which is the hourly average of the RTEM pricing. Because market pricing is based on HOEP, it is the most important number for Abitibi, says Roussel. “Using RTEM, we calculate a predicted HOEP every five minutes so operators can have a sense, in advance, of what the true HOEP may be at the end of the hour,” Roussel explains. The third price monitored is an IMO forecast for the next day’s pricing. This comes out around mid-day, and can be helpful to mill managers in planning their next day’s operations.
Weather information drawn from the Environment Canada Web site can also be an important planning tool. “If the forecast is for really cold or really hot weather in Toronto, we know that demand is going to be high, so the price will also be high,” Roussel notes.
One unique EM-SYS component is the load-planning module, Roussel says. “When we were developing the system, I knew in my head what we needed, but this kind of capability just didn’t exist out in the market,” he notes. So with top management approval, Roussel was able to enlist the services of a programmer in one of the Abitibi mills to develop the module, and “within a month, we had that application up and running.”
The load-planning module covers all of the heavy equipment for each mill, such as thermo-mechanical pulp systems, refiners, paper machines and winders. The base load is configured for every piece of equipment according to how many megawatts of power each machine consumes when it is running at full speed. The load plan screen allows users to call up the data and see at what percentage utilization different pieces of equipment are scheduled to run, and for what period of time—down to 15-minute intervals. Managers can then adjust their production schedules for differing strategies to match power pricing and forecasts, by re-configuring the percent utilization and operation schedule for each piece of equipment.
Use it or sell it?
At Abitibi, one interesting twist to the power equation is that three of the five Ontario mills have, to varying degrees, their own hydroelectric generating capacity. These mills can reduce their power purchases by running water through the dam turbines. “Typically, what they do is produce and use their own electricity during the day when electricity prices are higher. During the off-peak periods, such as night time, they keep the water and buy electricity,” Roussel says.
But when the situation warrants, these mills can also choose to shut down parts or all of the mill equipment in favor of making and pushing power to the grid at current market price. “If the market is very high, at $200 per MWh, for example, and management has a shutdown scheduled for the next day, they might decide to take the shutdown right away and sell that power,” Roussel says.
In some cases, even when a shutdown isn’t planned, selling power instead of making pulp and paper may be the most profitable course. This strategy must be weighed against commitments that a mill has to its paper customers, of course. But in some cases, management may have the flexibility to switch paper orders from one mill to another based on electricity cost considerations.
With deregulation, “one of the first things we had to do was change the culture, from making paper to making money, regardless of what commodity you’re selling,” Roussel observes. “And it happens at times that the commodity of the day is electricity.”
Roussel stresses that the EM-SYS is not intended to replace human involvement in the decision-making process. The system doesn’t tell mill managers what to do, but simply equips them with additional information that they can use to make their own decisions. “The accountability remains with the guy between the chair and the keyboard,” as Roussel puts it.
So far, this approach seems to be working. Jean-Guy Trudel, Abitibi vice president, newsprint, credits EM-SYS with enabling savings at the five Ontario mills estimated at C$1 million per year. And Trudel notes that the system can be adapted to the company’s other mills in the short term with just minimum modifications.
EM-SYS does not have all of the bells and whistles that the expensive, off-the-shelf system would have provided, Roussel concedes. But it does have the key functionality that Abitibi needed, at only a fraction of the cost, he observes. “Times are tough in the pulp and paper sector, and when you can’t afford something, you’re willing to take more chances,” he adds. “And that’s the position we were in.”
In this case, the risk-taking paid off.
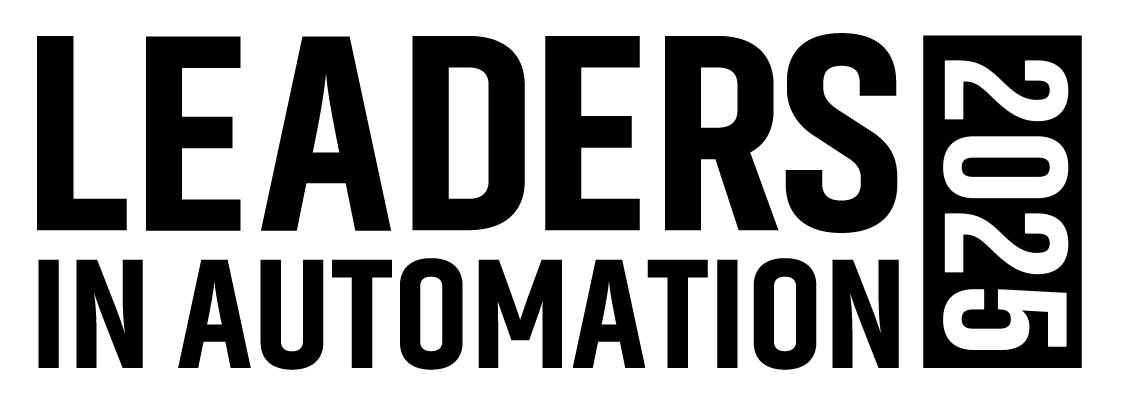
Leaders relevant to this article: