Shorter product life cycles and the need for improved manufacturing flexibility are putting the pressure on automation users in many industry segments these days. And as the U.S. economy improves, there are growing indications that factory end users and systems integrators alike are turning more often to robotics as one way to meet those demands.
Robot unit orders and shipments were both up by 28 percent during the first three quarters last year, following a painful market downturn in 2001 and 2002, says the Robotic Industries Association (RIA), Ann Arbor, Mich. Further, reports from the field point toward broader use of robot systems in industries ranging from food to automotive.
the next wave
“In the automotive industry, the use of robots tends to run in waves, and I think we’re moving into another wave where robots are once again gaining ground on purpose-built, fixed automation,” says Jim Wells, senior staff research engineer, manufacturing systems, at the General Motors Technical Center, in Warren, Mich. Among the enablers, Wells cites the growing availability of high-payload robots that can now handle automotive subassemblies up to 500 kilograms, as well as compact spot welding robots that can work beneath other, larger robots in a cell to hit more welding spots without greatly expanding work envelopes. Both can help in the automaker’s quest to be more agile, flexible and reduce production lead times, he says.
Automotive original equipment manufacturers (OEMs) and suppliers continue to be the largest customers for robotics suppliers, accounting for more than 50 percent of sales. But other industry segments are also increasing their use of robots.
At robot vendor ABB Inc., in Auburn Hills, Mich., Åke Lindqvist sees the largest nonautomotive market growth today in the food and consumer goods industries. “I think consumer demand for larger variety, more frequent changes in product size and in the way that products are packaged is driving demand for more flexible automation, which is where robots come into play for picking, packing and palletizing,” observes Lindqvist, ABB group vice president, robotic products and automation, North America. Lindqvist was recently elected RIA president.
At Kraft Foods, Automation Manager Paul Doll agrees. Continuing reductions in robot system pricing are making robotics more cost-effective for the food and consumer goods industries, says Doll, who is based in Madison, Wis., and also serves on the RIA board. “In some cases, over the last five years, I would say that robot system prices have dropped almost in half,” Doll notes.
Compared to industries such as automotive and semiconductors, in which robots are used more widely, consumer goods industries work on much tighter margins, and have traditionally favored fixed automation over higher cost robotics. “But as the price of these robot systems have come down, and particularly given the flexibility they offer, it’s now beginning to make much more sense to use robots,” Doll says. Some consumer goods firms, as a result, have recently stepped up their use of robots, many equipped with vision guidance, for tasks such as palletizing, he notes.
robot basics
Since their introduction more than 40 years ago, industrial robots have offered advantages in flexibility for automation users. Compared to fixed, or hard automation equipment that is designed to perform a single task, robot arms are multifunctional manipulators that can be programmed and reprogrammed to perform a variety of different tasks. Modern robots typically rely on electric servo control technology, providing high accuracy. When equipped with sensing systems such as vision or force sensing, robots can adapt to changes or variable conditions in the work environment.
Large robot arms of the kind used for welding, painting and heavy material handling typically provide six axes of motion, enabling them to place a tool or object at any orientation in space, anywhere within their working envelopes. Smaller, four-axes models known as SCARA robots (for selective compliance articulated robot arm) are often the choice for lighter, pick-and-place assembly or materials handling applications. Depending on size and style, robot pricing can range from less than $20,000 for tabletop SCARAs to more than $100,000 for large six-axes units.
“The biggest advantage of robots is that they’re reusable,” says Mark Schaffer, technical specialist at Vitec LLC, a Detroit-based manufacturer of plastic vehicle fuel tanks that has used ABB robots for the past several years. “If you bring in a robot for a program that lasts for three years, you can use that same robot over again on another program, because the average robot life span is up to 10 years,” Schaffer says. On the other hand, he adds, one drawback of using the technology is that robot arms “can be pricey.”
Kraft’s Doll concurs that despite system price declines that have made robotics more attractive for many applications, cost can still be a hurdle. “If you’re using a robot to do a pick and place activity, there’s usually a solution out there that involves some kind of air cylinder with fixtures that will always be less expensive,” Doll says. “So you’ve got to look into the future and say, ‘Well, instead of reengineering these fixtures every time we have an application to pick and place something, we can do far less engineering by putting a new tool on an existing robot,’ ” he observes.
need for speed
Some robot users point to the speed with which robots can be deployed or reconfigured, when compared to more complex hard automation equipment. One such user is Andy Carson, director and business group manager for electronics assembly, at RTS Wright Industries LLC, a Nashville, Tenn., system integrator. Around two-thirds of all assembly automation systems built by RTS Wright now incorporate robots—up from just one in three systems five years ago, Carson estimates. He cites the need for speed among the primary reasons for that trend.
“It wasn’t too long ago that we saw projects that had lead times in the 45- to 55-week range. Now it seems like everybody I talk to wants it done in 25 weeks,” he says. Given the reduced time for custom engineering, RTS Wright has increasingly turned to robots, which have become highly reliable and less expensive in recent years, Carson explains. “A robot solution goes a long way to simplify the tooling at any given station, and you can get robots in six to eight weeks, typically, so that takes a lot of pressure off us, schedule-wise,” he says. “In the past few years, robots have become much more of a commodity,” Carson adds. “We look at robots as a great way to get a quick solution for our customers.”
At Factory Automation Systems Inc., an Atlanta-based system integrator, Ron Potter, director of robotics technology, notes that robot-based solutions today are more readily accepted by end users than in the past. Industrial robots had to overcome a bad reputation obtained in the early 1980s when the technology was overhyped by Wall Street analysts and the general press, he says. But since then, steady improvements have won over many manufacturers, Potter concludes.
During the last five to 10 years, robot manufacturers have concentrated on making robot arms as reliable, useful and user-friendly as possible, Potter says. “The average mean time between failure for robots is about 50,000 or 60,000 hours now, so some of the concerns that users had about maintenance and keeping a complex machine running have gone away,” he notes. “A robot is no longer a complex machine. It is really very reliable and it’s been simplified quite a bit.”
GM’s Wells contends that in some applications, a robotic solution can not only be faster to implement, but also more reliable than custom-built, hard automation. “It’s kind of harsh to say that robots are commodities,” he opines. “But they are mass-produced, highly reliable motion devices that have been well-wrung out and validated by their manufacturers,” says Wells. “When you look at the range of offerings, the capability, the dexterity, the work envelope and the control that’s available, robots are hard to beat with any purpose-built, roll-your-own kind of one-off automation.”
Robots are also getting easier to use, points out Terry O’Connell, vice president, sales and marketing, for Genesis Systems Group, a Davenport, Iowa-based integrator that builds robotic welding systems. While most robots still rely on proprietary operating systems, most feature user-friendly front-end systems that provide personal computer-style operation, he says.
“You’re also seeing wireless coming into play with a lot of the robots and the peripheral equipment that goes with them,” O’Connell adds. “You can upload and download your welding programs, edit them and get error reports wirelessly with your Palm PDA (personal digital assistant).”
falling prices
Robot vendors confirm the focus on ease of use and reliability, as well as the trend toward lower robot pricing. “At Adept, you can buy a four-axis tabletop SCARA robot with full capability in the low-$20,000 range today, and that same robot just four years ago was priced in the mid-$30,000 range,” points out Charlie Duncheon, executive vice president at robot vendor Adept Technology Inc., in Livermore, Calif.
The price reduction was achieved primarily by eliminating the need for an external controller, and instead embedding all controls, amplifiers and input/output inside the robot arm itself, says Duncheon. “You simply connect power, plug in a personal computer (PC) to program it, disconnect the PC and go,” he notes. “We knew it was going to be lower cost, but it’s also simpler to use and obviously easier to diagnose. And its got fewer cables and connectors, so we’ve improved the reliability.”
ABB’s Lindqvist declines to cite numbers, but confirms that prices for larger, six-axes robots are also continuing to fall. “The biggest downward spiral we have seen is in the automotive arena, and I would say that competition drives that more than anything, sometimes to levels that I think could even be unhealthy for the industry, long term,” Lindqvist warns.
Kevin Ostby, vice president, general industries, for robot vendor Fanuc Robotics America Inc., in Rochester Hills, Mich., estimates that average robot selling prices have dropped by 25 to 30 percent over the past five years. But Ostby expects the rate of decline to slow in the future. “At some point, the cost per pound of steel is the cost per pound of steel, and you just can’t get it any lower,” he says.
Instead, says Ostby, the most significant cost trend for robot end users is in the emergence of what he calls “enabler products” that allow robots to be more quickly and easily integrated into the manufacturing process—in effect, lowering their system price.
One example is the simulation and off-line programming software packages offered by most robot vendors. Users can typically save weeks in programming and implementation time by simulating a robot application and creating a program prior to taking delivery on the robot arm and associated equipment, says Ostby. Other enabler products include integrated vision and force sensing systems that can make a robot more “intelligent,” as well as application specific software packages that can simplify programming and set-up for particular applications, Ostby adds. Fanuc, for example, offers software packages called ArcTool, PalTool and PaintTool, among others, for use in arc welding, palletizing and painting applications respectively.
Many industry sources agree that use of integrated sensor technologies—particularly vision—is on the rise in robot work cells. Applications that rely on vision guidance to enable a robot to pick randomly oriented parts from a conveyor belt or out of a tray, for example, are becoming more common. And at Vitec, the plastic fuel tank manufacturer, Schaffer says that a robotic application that uses vision to verify the correct application of seals on fuel tank sender unit modules has led to notable quality improvements.
“Most of the robot companies are now on the way to providing an integrated vision system with their robots, if they don’t do so already. This makes it much easier for the end user to apply both technologies together,” says Potter, of Factory Automation Systems. And for users who have experience with a particular machine vision system, some robot vendors are taking steps to make integration easier. “Our robot offering includes an integrated vision system, as well as the ability to communicate with external vision systems via TCP/IP (transmission control protocol/internet protocol) to accommodate user preference for different types of vision systems,” says Thierry Dumont, business unit manager for robotics, at Bosch Rexroth, in Buchanan, Mich.
see it, measure it
At General Motors, Wells notes that one of the latest automotive applications for integrated robot sensing technology involves metrology. Over the past two years, GM has installed several systems that rely on cameras or sensors mounted on the end of robot arms that are used to take measurements for monitoring the fit and build quality of vehicles on production lines. These systems, which include compensation for positional deviations due to environmental factors such as thermal expansion, are used in some cases to replace the fixed sensor arrays traditionally deployed.
Instead of moving a vehicle through a fixed sensor array, “the robot can go to a pose and space, and the sensor can see and instrument a location on a vehicle body,” Wells explains. The key advantage is flexibility. The robot-based system has more capability to comprehend different styles or types of vehicles going down the same process line, and it can also more readily zero in on problem areas, says Wells. “If there’s a specific area of interest, we can direct the system toward that area, which would be very difficult to do with a fixed system.”
Other emerging trends include broader use of heavy-duty robots that can handle payloads larger than the 120 to 160 kilogram weights typical of traditional automotive applications. “Where we do a transfer of large vehicle subassemblies from one conveyance system to another, we might have used a dedicated piece of automation to do that in the past, whereas today we’ll use a high-payload robot,” says Wells. “Sometimes the transfer reorients the part, so when we get subassemblies that are up to 300 or 400 kilograms and higher, the robot gives us a lot of flexibility.”
ABB’s Lindqvist confirms that demand for high-payload robots for transfer applications is on the rise from automotive OEMs. And he points to another, related application by which some automakers are using other robots to perform operations—such as welding—on a subassembly or part while it is being moved. “What you do is coordinate more than one robot through basically the same control system or through cooperating control systems,” Lindqvist notes. As many as three other robots may be able to perform arc welding or spot welding on an assembly while the first robot moves the assembly from one station to the next, he says.
“This is still in its infant stage, but it is definitely coming,” Lindqvist predicts. “Within a year or two, I think, you can expect to see this in full bloom.”
Sponsored Recommendations
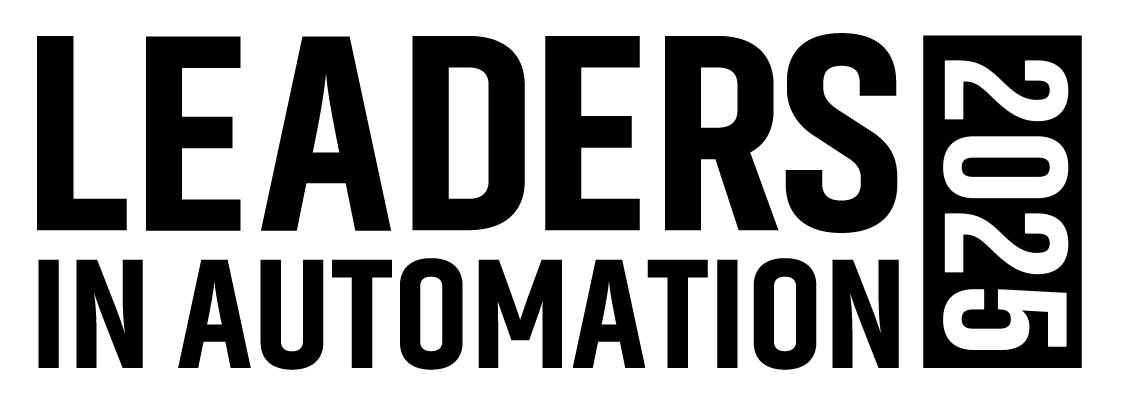
Leaders relevant to this article: