Crisis may be the right word to describe the problems of staffing for today’s automation systems. New technologies demand new skills. Companies are looking for more people with technical degrees, while some studies and anecdotal evidence suggest that students are shunning careers in manufacturing in favor of “sexier” industries that garner more popular press.
Meanwhile, depending on how you view it, teamwork has become either a necessary evil or an essential component of working in a manufacturing company today. The “lone wolf” engineer often worked his or her way up the ladder from electrician or technician to plant manufacturing engineer or process engineer. This engineer was usually empowered to research and source automation products and systems, either alone or with one or two other engineers.
As automation has become more sophisticated over the years, other disciplines within the manufacturing business saw the information sitting untapped in the controller and wanted a piece of the action. Performing a few mathematical functions on the data yields a wealth of statistical process control and statistical quality control feedback. Professionals from those disciplines had to be added to the automation team.
IT joins the team
Tying real-time production information to corporate management systems such as supply chain management became essential for a company to remain competitive. This led to a growth in automation networking and the addition of information technology professionals to the team.
Jack Bolick, president of Phoenix-based Honeywell Process Solutions, provides perspective that combines not only strategic hiring for his own company, but also strategic hiring practices of his customers and the industry at large. Discussing the changes in process control since his days in the plants, Bolick says, “I started in textile finishing plants using an IBM Series 1 computer. Our goal back then was trying to get variability out of the process. We’ve seen technology over the intervening time go from proprietary to open. We are now at a point of technology inflection that will have a major impact on how to staff people in factories.”
According to Bolick, the technology driver of this inflection is the general industry movement to the “Wintel” architecture, that is, computing power in various forms based upon Windows operating systems from Microsoft, in Redmond, Wash., and microprocessors from Intel, the Santa Clara, Calif., semiconductor maker. “The inflection is moving the factory to the ‘net,’ be it the Internet or intranets,” states Bolick. “This opens up the process architecture to where you can see enterprise information, not just locally, but globally. Managers can put capacity where it is needed. We’re starting to link the control room to the enterprise.”
This new capability expands the concept of automation from its traditional fixed factory base to entirely new applications. “For instance, look at what Caterpillar has done with its huge mining dump trucks,” adds Bolick. “It links sensors within the trucks to a satellite link to the Internet. The information moves to a central point where managers can monitor each truck and perform remote diagnostics. They know when to service a truck or take it out of service for more extensive work. Traditional industries such as power generation and refining have a lot of talent in engineers in North America, but the new plants are going up in China and Southeast Asia. This technology links talent to where it is needed.”
Some automation technology providers, recognizing the ubiquity of the Microsoft Visual Studio development environment and the necessity of information integration, are providing tools to simplify programming of control and information systems. These tools incorporate libraries of objects containing pre-defined control tasks, such as starting a motor or configuring a motion control drive. They also enable integration of special algorithms written in C or C++, and operator interfaces or database interfaces in Microsoft Visual Basic, technologies often more familiar to IT professionals than to control engineers.
Independent thinkers
Robb Dussault, automation product manager for Paris-based Schneider Electric, a technology supplier with North American headquarters in Palatine, Ill., believes that there is a limited supply of control engineers, who command comparatively high salaries. He suggests that manufacturers look beyond this group at the wider pool of computer science graduates who are certified in products and technologies from Microsoft.
These professionals, states Dussault, “are less expensive, young thinking, take pride in being independent, are willing to take calculated risks, are fluent with information technology and are eager to advance their careers by using today’s technologies.
“After all,” he continues, “an over-simplified view of an automation program is a piece of software designed to populate databases with time-critical data over a network, based on a set of externally- or internally-generated inputs. Explained in this way, automation programming is understandable to anyone who’s been trained in programming, networking and database management. Turning this understanding into a working control system is as easy as finding commercially compliant automation systems that talk the same language as these technical generalists.”
While it may be true that computer science graduates will command lower salaries than electrical engineers, the problem just may be that there simply won’t be enough engineering graduates to adequately staff automation-hungry manufacturers. Bolick notes, “Look at the curricula in engineering schools and what the students are taking. There is a considerable movement to nano-technology. Students want to go into material science or genetics, the sexy industries. Managers who are looking at where to move capacity or add capacity see the domain expertise they had in engineering talent is retiring, but the new engineers are moving on to the new things.”
As a result, says Bolick, the local plant problem is how to replace that domain expertise and take advantage of the new global realities. “Maybe this is where a company like Honeywell can pick up the slack with the new technologies of using the Web for managing maintenance with new software and new techniques. It may be easier for companies like Honeywell to go to a college and say, ‘I’m a large IT company,’ and entice some engineers to join, then give them domain expertise.”
Certainly Honeywell and its competitors have had service offerings for some time. Bolick believes that, given this confluence of factors, it may well be time for this service business to take off. Challenges remain to be overcome, though, before the theory of engineering support and service of third parties becomes a reality. “We’ll have to build in a lot better cybersecurity,” explains Bolick. “We also have to build mutual trust with the supplier and customer. Certainly, no one is going to turn over an entire refinery to a third party. They will still maintain critical staff running the control room, but with the combination of wireless networking and the Internet, more and more can be done remotely.”
Backing up the assertion of fewer college graduates seeking manufacturing jobs is a recent study sponsored by the National Association of Manufacturers (NAM). “More than 80 percent of the surveyed manufacturers reported a ‘moderate to serious’ shortage of qualified job applicants—even though manufacturing was suffering serious layoffs,” says the report, titled, “The Skills Gap: Manufacturers Confront Persistent Skills Shortages in an Uncertain Economy.” “In sum, what manufacturing is facing is not a lack of employees, but a shortfall of highly qualified employees with specific educational backgrounds and skills,” the NAM researchers conclude.
The chain gang
In addition, the NAM, The Manufacturing Institute and Deloitte & Touche (now Deloitte Touche Tohmatsu) recently conducted two research studies of students, parents and teachers. The studies revealed that manufacturing’s image “was heavily loaded with negative connotations and perceived to be in a state of decline.” Student responses to open-ended questions regarding a career in manufacturing included the phrases, “serving a life sentence,” being “on a chain gang,” or “slave to a line.” Most adult respondents, the report said, “just have no idea of manufacturing’s contribution to the American economy.”
The report writers berated the U.S. educational system for not understanding the positive characteristics and contributions of manufacturing careers. It fails, in their opinion, to counsel students toward technical educations—either four-year degrees or technical school alternatives.
The report concludes with a challenge to those currently in manufacturing to find ways to actively promote the industry to the nation’s youth. “Unless the industry finds a compelling way to communicate a positive image and address education and training issues effectively, manufacturing could experience a shift from merely having a talent shortage to facing a serious labor crisis. This could foreshadow a significant decrease in manufacturing’s competitiveness and accelerate the movement of American productive capacity and well-paid manufacturing jobs overseas. These events could deliver a decisive blow to an already fragile economy and even undermine national security.”
This report is concerned with training for students who will eventually replace retiring baby boomers. A more immediate problem is training for those still working. Staying abreast of technology changes and regulatory requirements while keeping a plant running can be a daunting task. Where is the time for continuing education?
Dick Hill, vice president and general manager, Manufacturing Advisory Services, for ARC Advisory Group, a Dedham, Mass., analyst firm specializing in manufacturing systems, has conducted research on staffing challenges and continues to follow the problem.
“There is a concern that as plants continue to downsize staff, they seem to hit the automation staff pretty hard, maybe going from 20 to five staff people. The people left are barely able to keep their heads above water,” Hill notes. “One of the problems that crops up is that technical staff that is retained is often the older people. They may be trained in the older, say, analog, technologies and now find themselves taking over management of all the digital control that’s been recently installed. So they will need training on the new equipment.”
Hill guided a survey in June 2002 to uncover what managers and engineers think about future staffing needs. “The gist of what we learned is that the problem is still out there,” Hill relates. Survey respondents complained of understaffing and a need to rely on vendors to supply knowledge they no longer have, Hill observes. Engineers in the plants said they typically have no time for creative work but are always “fighting fires.”
The problem with this trend, according to Hill, is that vendors or suppliers can only have about 80 percent of the knowledge necessary to run a plant. “Supplier technical experts may know about certain controls and/or instrumentation,” he notes, “but they may not necessarily know how to manage the particular reactor in a particular plant, for instance, or the particular recipes required for that company’s products.”
Working with suppliers can be a conundrum for manufacturing managers. Certainly, suppliers see a business opportunity in providing technical service and support. They would not be entering this market if customers didn’t want it. But manufacturers need to take a cautious approach to any such partnerships. “If you were able to get a supplier to work on a process problem, what happens when your competitor also has process problems and has partnered with the same supplier?” asks Hill. “Will the supplier’s engineers be able to ignore knowledge about how your company’s control systems act in the process when they’re working on similar processes for your competitor?”
Furthermore, migrating to outsourced engineering and maintenance may require different skills than when internal staff handled those tasks. Hill says, “Perhaps managers kept people who were expert ‘doers’ after the forced round of cuts. These people may have the process knowledge at a detail level, but the new job is now one of managing ‘doers’ who are not even direct employees of the company. This requires an entirely different set of skills, so the company may have the wrong people in place.”
Another set of challenges arises when company management decides to move entire manufacturing operations to contract manufacturers. Hill says managers are now faced with figuring out how to train people to manage these contracts and train the supplier company in company expectations and standards.
Back to the future
In general, says Honeywell’s Bolick, changes in the way that automation staffs are put together seem unlikely for the short term. “Most decisions are made at the facility level by plant management,” he says. “We’re all under pressure from Wall Street for head count per sales ratios. There is a lot of environmental noise like this.”
Whatever actually happens in the next few years, there is no doubt that staffing for automation will be a challenge for manufacturing executives. To help meet that challenge, Bolick has some advice. “When you are staffing a company, look for people who are open to change, dynamic in nature and have passion about what they do,” he says.
See sidebar to this article: Student preparation for manufacturing careers
Sponsored Recommendations
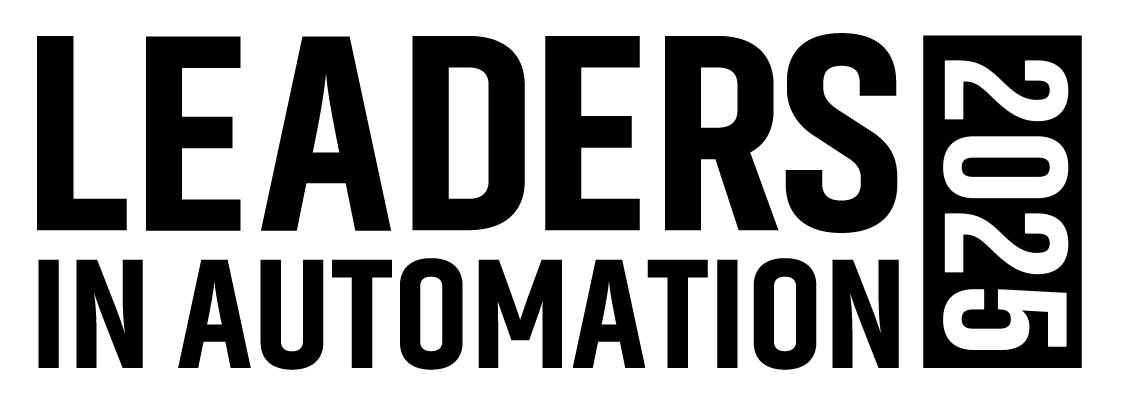
Leaders relevant to this article: