As capital available for investment shrivels, manufacturing managers need to squeeze the last useful drop of economic life from equipment. Profitable return on assets is possible through a savvy, up-to-date maintenance outlook. But traditional reactive and preventive maintenance must be blended with today’s predictive maintenance tools.
Balanced, too, must be competing business considerations of trying to increase capacity, maintain quality and reduce production costs. Success for maintenance practitioners, facing dwindling budgets and smaller staff, will mean finding a fresh perspective on their function and communicating in business terms with the enterprise’s higher levels.
Manufacturing executives need a maintenance tune-up. They must grasp the criticality of adequately funded and implemented maintenance programs—and then act accordingly.
Optimizing asset utilization has its challenges. The enterprise must understand what predictive maintenance is, and how and why it is used. Then the business must identify which assets are best monitored predictively.
Predictive is proactive
Technology-based predictive maintenance provides advance notice of problems, says Mike Laszkiewicz, vice president for asset management programs at Milwaukee-based Rockwell Automation. “Reactive equals ‘Fix me, I’m broke.’ Preventive is using a structure.”
With predictive, “you still have the repair cost, but not the downtime. It will allow you longer run time and higher level of utilization because you don’t have as much preventive maintenance.”
Predictive maintenance deals more with things involved in flow, temperature and level measurements, including vibrating and rotating equipment, says Houghton Leroy, an analyst with ARC Advisory Group, a Dedham, Mass.-based research firm.
Dave Quebbemann, strategic marketing manager for Omron Electronics, in Schaumburg, Ill., describes predictive maintenance as monitoring two or three critical variables in a device that, with a 90 percent confidence level, “will tell you that the device is going to fall out of operation in a very short time.” However, the technique’s predictive capability is most likely not related to the number of operational cycles, he says. “More likely, it will be related to voltage, harmonics, temperature characteristics of the bearings, and the like.”
“The market is looking for products that allow customers to determine where they need to improve or focus their efforts. Those would be maintenance, cost reduction and quality improvement. But all of these are asset management solutions,” says Tom Mueller, business manager for asset optimization products, for ABB, in Wickliffe, Ohio. “Predictive maintenance is one component of an asset management strategy. The others would be performance monitoring, condition monitoring, quality improvement and cost reduction.”
Stuart Harris, vice president of asset optimization, at Austin, Texas-based Emerson Process Management, notes that predictive maintenance involves more than device data. “It’s process-centric data with comprehensive asset-health information in the context of the customer’s business,” he says, ”which enables the best financial decisions.”
Collaboration works
Predictive maintenance provides accurate, reliable and early-warning information on performance. “This eliminates most duplicate and inappropriate work orders and helps organizations deal with preventing short-term and long-term limitations,” says Kim Custeau, Director of Product Marketing for Invensys Avantis, in Burlington, Ontario, Canada.
And now, because customers have reduced maintenance budgets, yet have increasingly complex systems and devices, “they need the ability to figure out where to direct their maintenance activities,” ABB’s Mueller says. “We have many examples of failures that go unnoticed for a long time. But if the system that is supported notified someone who was in a position to act that a problem has occurred, then something could be done sooner.”
Mueller believes that industry shouldn’t underestimate the benefit of optimizing reactive maintenance, “because reactive maintenance situations will still continue to occur.” But, regarding predictive, he says, “What we’re talking about is having a population of assets. Rather than having to apply maintenance resources to that entire population, [it’s] being able to have the assets inform you where you ought to apply your maintenance resources.”
At Phoenix-based Honeywell, Dave Kaufmann, director of its PKS Advantage asset management product, says that the way to the future for asset management and predictive maintenance is through collaborative knowledge shared among enterprise, device manufacturer and solutions provider.
“This should be done for all types of devices, not just valves. Consider whether the asset could give you more information that could be combined into a knowledge system,” Kaufmann advises. Currently, Honeywell’s goal is to put a device’s maintenance “in context to your business. Context equals function plus priority plus financial impact,” he explains.
Emerson’s Harris says that industry needs freedom of choice, “so that manufacturers can integrate assets from any supplier using industry standard communications protocols.” Through collaboration, the enterprise’s “data fog” can be turned into useful knowledge, he says. “You truly need an open architecture, process-centric, software-based approach to get quick hits and assess what’s going on.”
Once maintenance analyses are done, then someone has to take the next steps—and computerized maintenance monitoring systems (CMMSs) are the means, says ARC’s Leroy. “You schedule and implement. You obtain maintenance history. You also obtain inventory and purchase history.”
The enterprise asset management (EAM) system is also a higher-level response mechanism for predictive maintenance, he says. “These are tied to the financials for return-on-asset information. The EAM solutions tend to impact more people in the enterprise.” In which direction is EAM going? “We’re calling it collaborative asset life-cycle management,” Leroy says.
Asset Acknowledgement
While condition monitoring and performance monitoring feed into predictive maintenance, businesses could benefit from acknowledging that automation systems and devices, including wiring, as well as products themselves, are assets to be considered.
“Unfortunately, lots of plants have five generations of automation systems and devices. That means distributed control systems. But some plants could have 10 generations, including pneumatics,” says Will Chin, an ARC Advisory Group analyst. “When you’re so far away from digital communications, to upgrade the plant would involve tremendous capital investment. Right now, who has the money? No one has. That’s what makes a process-centric solution more attractive,” Chin says.
In the process industries, the next frontier for predictive maintenance is in the measuring devices, says Bruce Jensen, manager of systems marketing at Yokogawa, in Stafford, Texas. “We’re working first on our pressure transmitters. One problem they have is on the suction and discharge sides, in the impulse lines. You use signal-processing technology to determine impulse-line plugging,” Jensen says. Then the device can tell that it needs fixing. These and similar applications used for other devices, he says, “will tell the users of their health. We’re calling it asset intelligence. It examines and then reports.”
Chin agrees that a solution may be “self-validating assets, for example, like those developed by Invensys and Oxford University. The asset says, ‘I have a problem, I know what it is, it’s biasing me by some factor.’ And the instrument self-corrects to the extent that it can.”
A challenge, according to Jensen, “is to transform the maintenance shop and its skill sets into being network knowledgeable. You’re also bringing information technology from office automation into field automation. How you deploy field networks and how it gets into computers has to be examined.”
Regarding communications protocols, Chin believes that “what you’ll see in the future is HART, Foundation Fieldbus, Profibus PA, AS-I and DeviceNet.” He says that AS-I is used in a lot of switching overseas. “DeviceNet is more prevalent in the United States.”
To get the information connected to the upper world of the enterprise, Honeywell’s solutions use network-based solutions such as OPC, Ethernet and DeviceNet, Kaufmann says.
Stunning savings
So significant are the cost savings from predictive maintenance, it is difficult to imagine operations without it. “You can save 90 percent on costs on critical assets that have a downtime component,” says ARC’s Leroy.
One savings comes in avoiding unnecessary preventive maintenance, Chin points out. “Some of the statistics that I’ve seen are that 40 to 50 percent of the time [when maintenance is performed], there was nothing wrong with the asset.” Honeywell’s Kaufmann agrees. “You save $5,000 per valve by not pulling them out of service and doing preventive maintenance before it’s needed,” he says.
“If maintenance in predictive fashion equals $X, then preventive costs equals $5X and reactive maintenance equals $15X,” says Harris. But, “if you actually end up with an unplanned shutdown, then you’d be looking at $40X or more for costs.”
In the energy business, lost availability means not just excessive maintenance costs but substantial revenue loss, says John Kerastas, marketing communications director at Lisle, Ill.-based SmartSignal.
“If 95 percent asset availability is acceptable or is the norm, that’s really high for many industries. [But] it masks two costs for downtime.” On average, unplanned downtime costs for a typical process industry “can represent 1 to 3 percent of revenues and 30 to 40 percent of profits annually,” according to Kerastas. For large capital equipment, he says, “the costs may be 1 to 3 percent of asset value per year. I just read a Forrester report that said the maintenance cost of a large turbine is four to five times the original purchase cost.”
Also requiring consideration are maintenance inventories, often overstocked when only reactive and preventive maintenance are used, which can be profitably decreased. “Typically, any dollar you have tied up in maintenance is a dollar you could use elsewhere. And you have a carrying cost that most financial experts will tell you amounts to 25 percent of the [value of the] inventory,” says Rockwell’s Laszkiewicz.
See sidebar to this article: Process-centric solution to deliver 500 percent savings
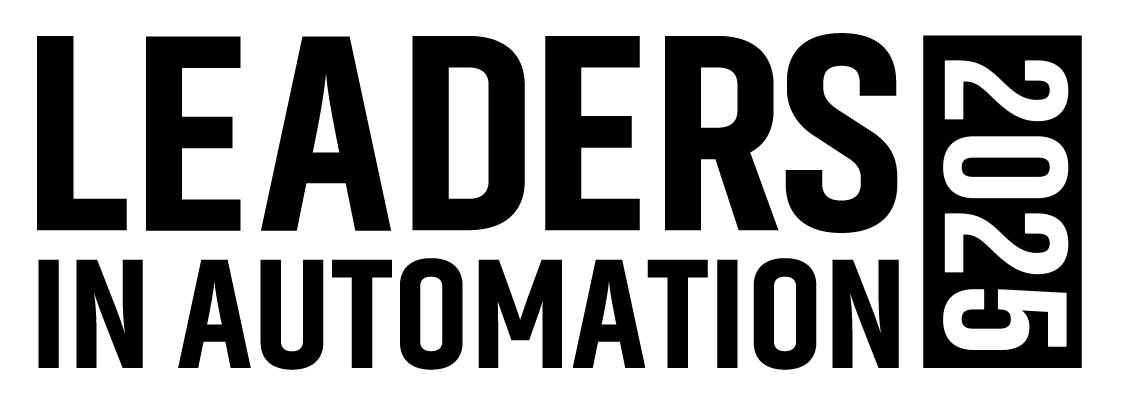
Leaders relevant to this article: