Steve Foster was worried. He and a team of plant maintenance specialists from Rexam Beverage Can Americas (BCA), based in Chicago, had just finished a multi-day training session learning the ins and outs of their new SAP plant maintenance (PM) software module. The team, led by Foster, was charged with implementing the SAP PM system at Rexam BCA.
“We walked out of that class in a bit of a panic,” Foster recalls. “We weren’t sure how we were going to make it work, because the user interface looked a little unfriendly to us.”
The user-friendliness of the system was key, because Rexam’s plan called for the PM module to be used by most of its plant floor machine operators in Rexam’s 17 U.S. plants. The system had to be easy to use, because many of the workers had little familiarity with computers, let alone any of the systems provided by SAP AG—the German-based enterprise software vendor.
Rexam, one of the world’s largest manufacturers of aluminum beverage cans, had been an SAP customer since 1997, deploying various financial and management modules within its SAP R/3 system. In 2000, Rexam BCA made the decision to replace its paper-based plant maintenance system with SAP PM, as a way to improve the efficiency of its plants and further increase product quality and customer satisfaction. Because the PM system would be used heavily by plant-level personnel, the company called for volunteers from its manufacturing plants to help launch the system. Foster, who was a plant engineer in Rexam’s Brunswick, N.J., factory, was one of four manufacturing representatives selected, and was named to head up the PM implementation team.
As at many manufacturers, equipment operators at Rexam BCA plants also perform machine maintenance. The PM implementation plan called for SAP computer terminals to be placed throughout the plants. “We had a vision of one of our operators walking up to a terminal, logging on to SAP, creating a maintenance work order, releasing the work order, printing it, logging off, and walking away to the storeroom to get the parts that they needed, all in 30 seconds or less,” Foster relates. “People outside our company just laughed at us. They said you can’t even log on to SAP in 30 seconds.”
The SAP PM training session attended by Foster and his team provided little encouragement. While the SAP PM interface was sufficiently friendly for use by maintenance management personnel, says Foster, the interface the team saw at the training session was neither simple enough nor fast enough to enable what Foster and the team had in mind. “We had this idea of creating a maintenance system that looked like an ATM (automated teller machine),” says Foster. “No one’s ever been trained on how to run an ATM, yet everyone can use one. Why should it be any more difficult to create a work order in SAP?”
Foster and his team found what they needed in a then little-known software product called GuiXT, developed by Synactive LLC, Burlingame, Calif. “There was one page in the SAP PM training module that showed this screen shot of a GuiXT transaction that had some nice-looking push-buttons,” says Foster. “So we started looking into it.”
Though it hadn’t been covered in the SAP PM training sessions, the Rexam team discovered that GuiXT is a scripting system embedded within SAP R/3 that can be used to streamline and simplify SAP user interfaces. “To do some of the higher-end GuiXT work, we had to buy a license from Synactive,” says Foster. “And we kind of took a leap of faith, because at the time, no one had really used it to any great extent,” he adds.
But the effort paid off. With the help of a Synactive consultant, a Rexam programmer was able to use GuiXT to create an SAP PM interface that does, in fact, resemble an ATM in its simplicity. The basic menu screen contains just 10, touch-screen, function push-buttons, for example (see screen shot). Thanks to GuiXT scripting, each button in Rexam’s PM interface triggers a series of standard SAP functions that run in the background, but are transparent to the user. In some cases, a single button launches SAP transactions that would have otherwise required the user to navigate 10 to 15 separate screens using a standard SAP interface, Foster says.
The result, according to Foster, is that Rexam training requirements for the SAP PM system were cut from an estimated 40 hours per machine operator—which would have been required using a standard SAP interface—to four hours or less with the simplified GuiXT interface. Multiplied times the 1,500 plant operators who would be using the system, that’s a savings of 54,000 hours. “We more than recovered the cost of the GuiXT license in the training savings alone,” Foster observes.
Moreover, the simplicity of the GuiXT interface has enabled Rexam to largely meet the team’s 30-second goal for users to log on and use the PM system, saving additional time in the plants. The system was phased in for use at all 17 U.S. plants during 2001 and 2002. Each plant has 10 to 12 SAP PM computer terminals on the plant floor that are accessible to operators. “I’d say we’re hitting that 30-second goal about 80 percent of the time, and for the other 20 percent, it’s less than 45 seconds,” Foster notes.
Further, the Rexam team didn’t stop with the GuiXT interface. “The other big thing we did for user-friendliness was to add RF (radio frequency) bar coding in our storerooms,” Foster says.
Once an operator has created and printed out a maintenance work order at one of the terminals, he takes the document to the storeroom to get the parts needed for the job, Foster explains. In the storeroom, the operator uses an RF bar code gun to log in to the SAP system by scanning a bar code ID card that he wears on his belt. For an SAP “goods issue” transaction, a small display on the bar code gun first prompts the user for the work order number, which the operator provides by scanning a bar code printed on the work order document. As the operator gathers parts needed for the job, he then scans the bar codes on the parts bins for each component, and enters the quantity of parts taken. When the operator hits the “enter” button on the gun, the transaction is recorded in the SAP system.
“We used to have a system where the operators would go to the storeroom, grab the parts they needed, and they were supposed to write down what they took on a piece of paper and file it,” says Foster. “With that system, our inventory record accuracy was not as good as it could be. But with the bar code guns, we’re now up to 98 percent accuracy, mostly because it’s so easy to use.”
The improved accuracy is enabling Rexam to more confidently reduce inventories, Foster says. Thanks to integration between the plant maintenance module and Rexam’s SAP Materials Management system, purchase requisitions are automatically generated when part stocks get low, and for time-based preventive maintenance tasks, parts can be automatically scheduled for just-in-time delivery.
Data details
When an operator finishes a maintenance job, he uses one of the plant floor terminals to close out the work order, recording the number of hours worked and some technical details about the job.
The detailed information gathered by the PM system is enabling Rexam to analyze its maintenance activities in ways that were not possible before. Among other things, “we can see which machines are really costing us the most money to maintain, so we can give them a little extra maintenance to get them back in line,” Foster points out.
In general, says Foster, the system is helping Rexam shift to a maintenance approach that is less reactive and more proactive. And it is providing the “best of both worlds,” he says, a system that harnesses the power of a more broadly integrated SAP system that is also easy to use for shop floor personnel. As a result, “we’ve seen our plant efficiencies and our product quality go up, due to better equipment availability, and we’ve seen our repair costs come down.”
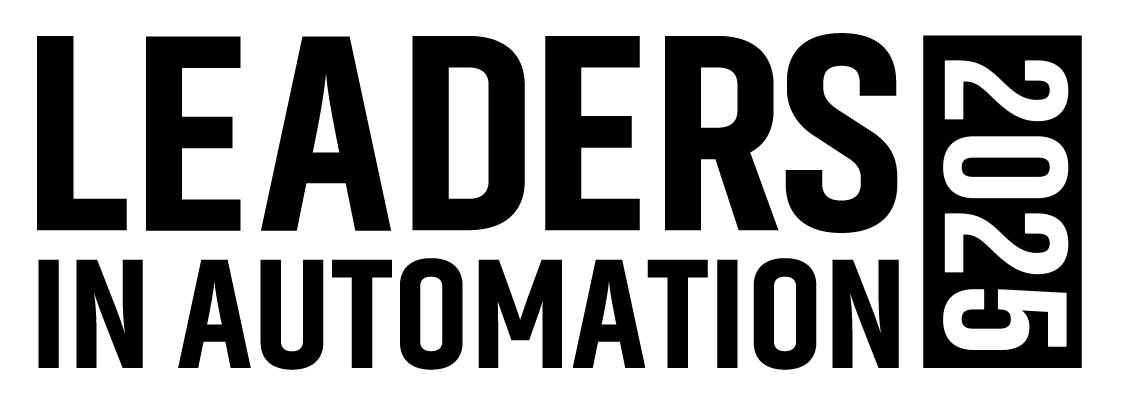
Leaders relevant to this article: