In terms of images, the robot almost defines modern automotive manufacturing. The iconic mechanical arm is the star of countless commercials designed to show that a particular auto company is ahead of the curve in terms of technology. Increasingly, that’s coming to be the case with packaging as well.
OK, I’m exaggerating a bit, but robots have become, if not ubiquitous, then at least relatively common in packaging. “Robotics is probably one of the fastest growing markets within the packaging industry today,” observes Leo Petrokonis, packaging industry business development manager for the global OEM team at Rockwell Automation (www.rockwellautomation.com), Milwaukee. “Robotic applications are increasing in number and expanding across applications, including picking and placing, and case packing.”
Surveys indicate the use of robots will be even more widespread in the future. Part of the reason for this is the ongoing improvement of the robot itself. “Compared to 10 to 15 years ago, robots are faster, more reliable and more affordable,” says Yarek Niedbala, directeur commercial, Kuka Robotics Canada Ltd. (www.kuka-robotics.com), Mississauga, Ontario, Canada.
Few would disagree. In fact, Dick Motley, account manager of North American Distribution for Fanuc Robotics America Inc. (www.fanucrobotics.com), Rochester Hills, Mich., cranks it up a notch by saying that “Today, reliability is almost a given.” It’s a point seemingly borne out by an application at Greenvale AP Ltd., in March, England, United Kingdom.
Keeping up with demand
Greenvale, one of Britain’s leading potato brands, has added robots to the packaging departments at its Cambridgeshire and Berwickshire plants. Each plant uses two Fanuc robots deployed in a packaging cell designed by Abar Automation, a Fanuc strategic partner in Hoofddorp, Netherlands.
Each of the two robots in the Abar DL-16 Loading Cell is tasked with picking 2.5 and 5 kg bags of potatoes and loading them into supermarket display containers at the rate of 60 bags per minute. The robots were originally designed to pick 30 bags per minute but, as Greenvale Operations Manager Rob Phillips explains, “the robots have been upgraded three times to accommodate increased demand.”
The Cambridgeshire plant now produces 2,400 metric tons of packaged potatoes each week, and the Berwickshire plant’s production has also increased. Along with the inherent flexibility that makes reconfiguring the packaging operation relatively simple, Phillips notes that the robotic cells also take up less floorspace than the previous approach. Best of all, though, the robots have been giving stable and reliable performance for the past year, requiring very little maintenance, and racking up an uptime rate of 99.98 percent, he says.
The degree of success that robots are having in packaging is a function of both brawn and brains. Robots are increasingly employed in data-intensive environments and they have been getting more “brainy,” so to speak, in order to operate in those environments. Case in point: Gilde.
The Gilde warehouse and distribution center in Tonsberg, Norway, is a busy place. That’s because Gilde’s extensive line of meat products are highly popular with Norwegian consumers, and approximately 140 employees work at the facility getting freshly processed and packaged meat to customers. For some time now they’ve had help: a Kuka KR 180 PA robot with a PC-based KR C2 control. The robot takes care of the “fast movers”—that is, the products that are ordered most frequently and in the highest quantities, often a seasonally adjusted category.
The process begins with a fork lift truck bringing pallets of crates, each containing large quantities of unmixed products, to the robot’s work area. The warehouse’s central computer informs the KR C2 control which products the robot should pick and in what order. The robot checks for itself whether it has grasped the correct product by holding the crate against a scanner. A new code is then generated and stuck onto the crate to specify the customer for delivery. The robot then places the crate on a conveyor, which transfers it to the next stage.
This unusual degree of flexibility in robotic order picking is mirrored by the flexibility with which the robot handles the crates. The KR 180 PA is able to handle even those crates presented in a non-uniform manner thanks to an ultrasonic sensor system in its gripper.
This monitors distances and allows the robot to be guided at the fastest possible speed to the first pick position. Once it has reached the crate, the gripper initially remains loosely closed until it has found the ideal gripping position. Only then does it tighten its grip. All of this takes more computational power than could be supplied by yesterday’s robot controls, but the KR 180 PA’s PC-based control is up to the task.
It’s worth noting here that Harvard University’s BioRobotics Laboratory (www.biorobotics.harvard.edu) is working on embedded sensing and actuation elements. They are seeking to do this through Shape Deposition Manufacturing (SDM), which alternates material deposition and machining to produce the complex, multilayered structures.
Among the possibilities being explored by the lab is a basic two-fingered gripper equipped with some or all of the following: Hall-effect sensors for joint angle sensing, embedded strain gauges for 3-axis force measurements, optical reflectance sensors for tactile sensing, and piezoelectric polymers for contact detection. The lab claims the parts created so far are extremely robust and able to withstand high impact loads and other forces.
Integration imperative
The PC-based control at Gilde is capable of rapidly handling increased gripper data, but why stop there? As Kuka’s Niedbala observes, consumer Packaged goods (CPG) end users “are looking for a single integrated control solution for packaging machines and robotics to reduce training requirements (eliminate the need to learn a robot OEM’s controller), simplify the control architecture and simplify maintenance.”
The other major robot vendors have also caught the integration bug. Erik Nieves, technology director at Motoman Robotics (www.motoman.com), Dayton, Ohio, explains that his company just released the FS100 controller, which has been designed from the ground up to be an integration platform, not just a robot controller.
“The FS100 allows for machine builders or other system integrators to write custom functions in C or C++ and run those on the main CPU of the controller. This means that a user with a clever algorithm for sortation or task planning or whatever can create a new function and run it on the robot without ever exposing the ‘secret sauce’ to the end users,” Nieves says.
Nieves adds that “any Ethernet-enabled smart device can be connected to the FS100 and run.”
>> Click here to read how one company is working to demystify packaging robotics through integrated robotic and machine control.
Packaging machine manufacturers are also embracing robot-packaging system control integration, says Brian Deal, packaging market segment manager for Schneider Electric (www.schneider-electric.com), Raleigh, N.C.
Deal says many packaging machine builders are investing heavily in integrating robotics into their machines because rather than building a machine around a stand-alone robot with its own black box controller, innovative OEMs are integrating the robot designs into their machines and controlling the entire machine with a single, programmable controller. The result, he maintains, is a higher performing solution that is easier to program, commission and service.
Bill Alexander, the packaging business development manager for Beckhoff Automation LLC (www.beckhoffautomation.com) of Burnsville, Minn., would generally agree, but he and his company replace the programmable controller with a PC-based control. “These PC-based systems have become the natural choice because of their ability to easily implement picking algorithms at the sub-millisecond speeds that are now necessary and demanded by the typical robotic packaging application of today,” he maintains.
Alexander says PC-based control systems can “cost-effectively replace expensive dedicated robot controllers with an off-the-shelf controller and standard software that can actually control the entire machine, including the robotic portion of the application.” When running on an advanced industrial PC with a modern multi-core processor, he maintains, “these robotic functions can be managed in parallel with PLC, motion control, HMI and other functions.”
Power of software
Alexander is quick to point out that it is not simply the processing power alone that accounts for the performance of today’s integrated robotic packaging systems, but also the software those controls run. He cites as example the programming software Beckhoff provides, saying such software has helped fuel the marked decrease in robotic system cost by easing and speeding system implementation. “One of our core technological philosophies,” he stresses, “is to add layers of functionality in software instead of hardware wherever possible.”
>> Click here to watch a video demo on the patent-pending RoboNav, a 6-axis feedback device from QPoint Robotic Solutions. Visit bit.ly/awvids069
Easing and speeding the implementation of robotic packaging systems through software is a subject that is dear to the hearts of all the major automation vendors, Bosch Rexroth among them. Listen to Richard Vaughn, who is mechatronic product engineer at Bosch Rexroth (www.boschrexroth.com), Charlotte, NC, discuss his company’s “IndraMotion for Packaging” suite:
“It allows machine builders to develop their controls faster and more efficiently for their specific application through parameterization, instead of programming. It includes integrated IEC 61131 compliant ready-made robotic Function Blocks and other application-specific technology functions that can help reduce routine work.” Vaughn says the software also helps OEMs configure and program packaging applications that require precise synchronization, camming, registration, electronic gearing, collating, robotic path planning and dynamic belt synchronization. ” Of course, this open architecture programming environment supports the use of OMAC packaging guidelines like PackML.”
Weighing in from an OEM’s perspective, Ted Yeigh, director of sales for Columbia Machine, Vancouver, Wash., concurs: “Common platform controllers are simplifying the integration of robots into systems in general and broadening the number of applications for industrial robots.”
Columbia builds palletizing machines, including robotic palletizers, and their latest offering, the FL2000-R, uses a Rockwell Automation Allen-Bradley ControlLogix programmable automation controller (PAC) to control both the robot arm and the basic machine. This, he says, not only provides increased reliability and pattern forming capability, it also allows plant personnel to more easily understand and maintain the system because they will be working with familiar controls, not a proprietary robot system.
Speaking of today’s robotic palletizing systems in general, and his company’s FL2000-R in particular, he says that “the increase in performance and productivity combined with simpler controls interfacing has brought the ROI/payback to a level that is able to be justified by more end users.”
>> Click here to read what's ahead for vision and robotics.
Companies in this Article
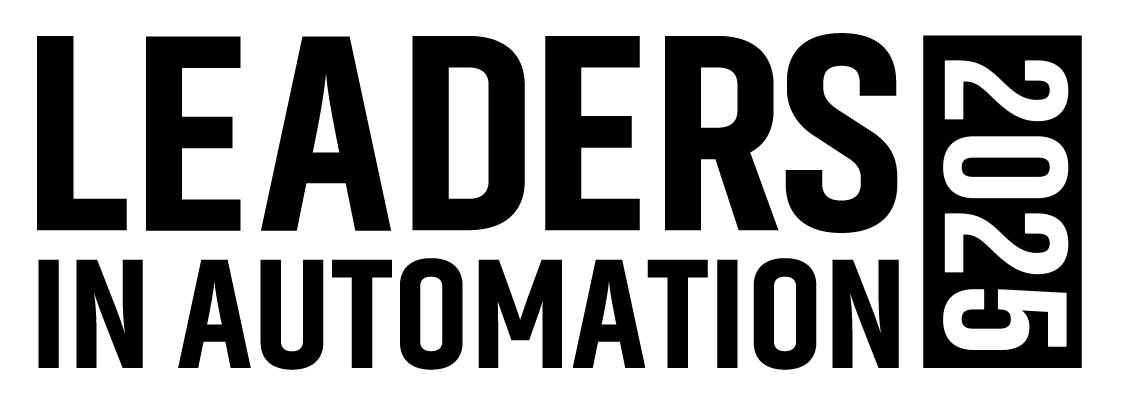
Leaders relevant to this article: