During a well-attended Open Factory April 10-12 at its Pianoro headquarters plant outside Bologna Italy, pharmaceutical packaging machinery specialist Marchesini Group (www.marchesini.com) officially unveiled its Industry 4.0 program.
Industry 4.0, of course, is the fourth industrial revolution, a transformation now underway where sensors, machines, and IT systems will be tightly integrated all along the value chain. These connected systems can interact with one another thanks to standardized Internet-based communications protocols. And by interacting with one another, they can analyze data to predict failure, reconfigure themselves, and adapt to changes. Industry 4.0, sometimes called the Internet of Things (IoT), will make it possible to gather and analyze data across machines, resulting in faster, more flexible, and more efficient manufacturing processes to produce higher-quality goods at a reduced cost.
Among several things made abundantly clear at the Marchesini event is that digitization, or the conversion of analog source material into a numerical format, is a critical first step on the road to Industry 4.0. It was even suggested that the very definition of Industry 4.0 might be this: digitization applied to manufacturing.
Why the emphasis on digitization?There are two primary reasons. First, it means that information in a variety of formats can be collected and processed with the same efficiency. This is especially true in Marchesini’s case since the communications protocol the firm has adopted across the board is OPC Unified Architecture (OPC UA).It’s a machine-to-machine communications protocol for industrial automation that’s described as SOA (service-oriented architecture), a style of software design whose basic principles are independent of vendors, product, and technologies. Other distinguishing characteristics of OPC UA include these:
• it’s open and freely available
• it’s not tied to one operating system or programming language
• it’s robust from a security standpoint
A second benefit of digitization is that once processes are digitized, it opens the door to other exciting possibilities such as machine learning, condition monitoring, remote-access monitoring, and, ultimately, the smart factory. In the smart factory, operations are carried out with minimal manual intervention, high reliability, and maximum flexibility. The automated workflows, synchronization of assets, and improved tracking and scheduling in the smart factory lead to increased yield and quality along with reduced cost and waste.
Predictably enough, the pharmaceutical industry is anything but immune to the impact of IoT and Industry 4.0, trends that are transforming pharma manufacturing at a rapid pace. Data shared at the Open Factory indicated that IoT software and services in the pharmaceutical industry are expected to grow from $420 million in 2015 to $2.5 billion by 2020.
“In such an environment,” said Marchesini Business Development Manager Stefano Selvatici at the Open Factory, “we feel it’s our responsibility to contribute to this transformative process by playing a leading role in terms of technology and know-how. That’s why all new machines ordered from us from now on will be Industry 4.0-ready.”
Selvatici went on to explain that Marchesini’s approach to all of this is best understood by thinking of it in three layers arranged in the shape of a pyramid. At the base is the production line itself. “This remains the biggest asset of the plant, no questions asked,” said Selvatici. “What changes going forward is that all of our machines will be equipped with software and sensors and data analytics capabilities to elevate their performance potential and make them intelligent to the point of being semi-autonomous.”
Blister packaging line
The line assembled by Marchesini to demonstrate its Industry 4.0 program during the Open Factory consisted of three machines for primary, secondary, and tertiary packaging of pharmaceutical blister packs. Upstream was the Integra 320 blister packer with Valida infeed system—with five cameras to control shape, thickness, and color of the pills—as well as the HarleNIR system from SEA Vision (www.seavision.it). This is an inspection system that combines a standard vision system solution with Near Infrared Hyperspectral vision technology. Thanks to this integrated imaging technology, HarleNIR can distinguish products based on their active ingredients. So it’s one more QA tool that pharmaceutical manufacturers can use to rule out any opportunity for a wrong product to make its way into a blister pack. Labeling on the line was carried out by the BL-A420 CW, which included a complete solution for tracking, serializing, and labeling of cartons, giving a unique identity to each pharmaceutical product packed. And at the end of the line was a case packer fully equipped to complete the final aggregation of cartons with cases: the MC 820 TT.
Above this foundational layer is what Marchesini describes as SCADA System & Line Management. This is where a huge amount of data related to quality and machine operations is kept track of. The SCADA system provides feedback to operators on a full check-up of the machinery’s mechanical and functional status at any time and from any place—be it on-site or remote. It’s a matter of constantly tracking vital parameters, offering a variety of functions such as pinpointing and correcting feasible problems on the systems, finding inefficiencies linked to the operators, or allowing the different and complex systems and machinery to communicate with each other, detecting the status of the various devices and components at any time.
And at the top of the pyramid is Business Intelligence & Data Analytics, where software technology is exploited to extract the data processed from the work environment so that it can be converted into valuable and actionable information—the very building blocks of Business Intelligence strategies. Thanks to what Marchesini refers to as Artificial Intelligence tools and “deep learning algorithms,” all the data can be analyzed to reach important objectives and to better understand the processes as well as key performance indicators (KPIs). It will also improve the quality of production flow by easily pinpointing what slows down production or by highlighting potentials that have not been fully exploited.
“This top layer of the Industry 4.0 pyramid represents, really, the door to the future,” said Selvatici. “This is where the data captured by the intelligent machines is analyzed by the SEA Vision software to provide full transparency of your manufacturing process, including OEE analysis and performance dashboards.”
Longstanding partnership
Marchesini and SEA Vision, a highly regarded vision system software company from the same region of Italy that Marchesini calls home, have partnered successfully on numerous projects over the years, and in 2018 the Marchesini Group acquired 48% of the firm. What SEA Vision brings to the table is yudoo, the first ready-made software suite designed specifically for pharma, which was born from more than 25 years of experience in system integration and data collection on packaging machines.
A unified environment for Business Intelligence analysis, yudoo includes modules for centralized control systems, KPI reports on historical data, a Data Historian, OEE Tools, real-time shop-floor dashboards, track-and-trace functions, predictive maintenance functionality, and more. Its integrated Artificial Intelligence technology enables the software suite to both centralize operations management on the packaging lines and harmonize the information coming from different sources--including automation devices, machines, IT, and control systems—to transform them from “raw” data to “smart” data.
The fundamentally modular nature of yudoo means that the software incorporates various functions split up into packets that customers can select based on their individual needs. It’s capable of providing complete information on the status, diagnostics, production parameters, and overall performance. It helps customers extract and understand an enormous amount of data that historically is hidden within the production environment. This data can be selected, interpreted, and converted into useful information. So it makes it possible to improve packaging processes by correcting in advance or by finding the causes behind drops in production or by eliminating unscheduled idle times by anticipating routine maintenance operations.
Contextual management of all three levels in this Industry 4.0 pyramid, says Marchesini, will transform packaging lines from being semi-closed systems to being open ecosystems that deliver internal data to the outside world (production data, for example) and that internalize data received from the outside world (production orders, for example). Thanks to the OPC UA protocol and to the interlinked technologies, complete communication is possible not only from within the factory—between the actual machines and such management systems as ERP and MES—but also between the machines and organizations outside the company, such as, for example, those who create and dispatch the unique codes that are the foundation of a serialization system. This favors better connectivity, better management of systems, and interoperability at all levels. It also opens the door to assisting customers remotely thanks to the use of new software programs and tools such as augmented reality visors. Imagine machine builders like Marchesini being able to actually see their equipment from anywhere in the world and providing targeted assistance without having to be physically on site.
Importance of OPC UA
Among thespeakers at the Open Factory was Marchesini Area Manager Jens Trautvetter, who emphasized how important it is that data transmission in Marchesini’s Industry 4.0 Program takes place via OPC-UA protocol.
“It’s by implementing this industrial standard that we link to this new world of 4.0,” said Trautvetter. “It lets us handle all the machine data—alarms, diagnostics, counters, machine status, production information, motor torque, electrical consumption, temperature, flow—in a controlled way and pass it all to upstream systems where smart algorithms are capable of analyzing it and then sending a text or email to the responsible party if some part of a machine needs attention. This condition monitoring capability leads to predictive maintenance, a huge part of the Industry 4.0 conversation. It all gets back to how do I make my factory smarter, how do I improve my processes to become more competitive, how do I plan my service interventions in a way that minimizes or avoids entirely inconvenient downtimes?”
Reactions from pharma engineers
A great many packaging, processing, engineering, and IT professionals representing various pharma companies attended the Marchesini Open Factory. Among them were Jeff Davis, President and CEO of Sheffield Pharmaceuticals, a New London, CT-based maker ofown-label and private-label over-the-counter products; and Tom May, Project Leader at the Sanofi facility in Swiftwater, PA. Here are a few of their reactions to what was presented.
• Davis: This whole connected factory concept, where you have real-time data coming in from your packaging lines that is actually useful and actionable, has been talked about for some time now. But I saw some things this time that were very interesting, especially the extent to which individual pieces of equipment in a line are integrated and in communication with each other. I was also impressed by the ability to centrally control a line through the yudoo software and implement the kind of condition monitoring that opens the door to predictive maintenance. We need our lines up and running. Having a centralized way of managing them and having real-time feedback available quickly and automatically would mean a lot to us.
• May: I like seeing the data being transmitted via OPC UA, because you can run into real problems with Industry 4.0 concepts if the machines can’t talk to each other. This communications standard makes it a lot easier when you’re trying to automate data collection. The same is true for sending input to the machines, like when they demonstrated how the yudoo software can be used to actually input batch information and send it directly to the line. If you’re not transmitting via a standardized communications protocol, this kind of thing is very difficult. So I really like seeing these companies implementing standards that let machines and systems communicate with each other regardless of what part of the world they’re made in.
I was also impressed with how data collected in real time was quickly transformed into dashboards clearly indicating machine performance. This would help us anticipate what type of maintenance is going to be required before the machine fails. I think that’s one of the biggest benefits of Industry 4.0 concepts from a machinery standpoint, being able to use data to make good decisions on keeping machines running efficiently and safely.
Companies in this Article
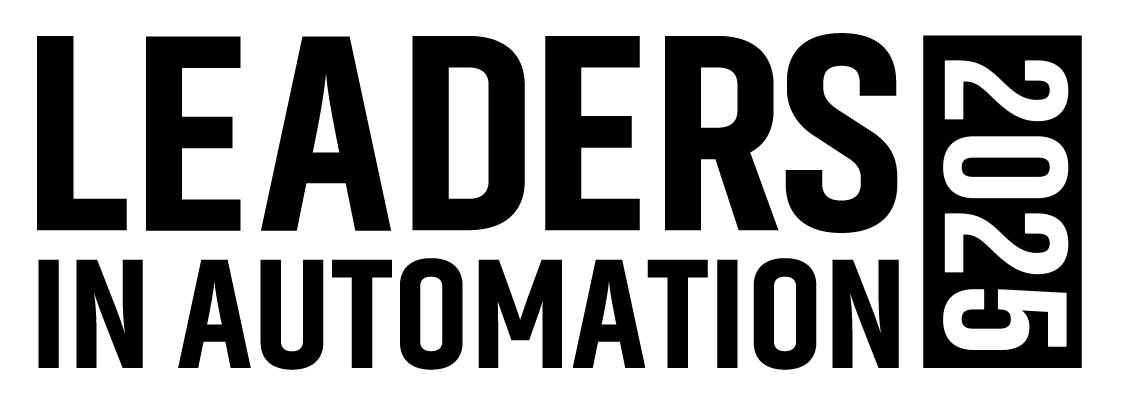
Leaders relevant to this article: