“We have set some really ambitious targets about where we want to take the manufacturing world,” declared Sudipta Bhattacharya, president and chief executive officer of Invensys Operations Management (IOM, www.iom.invensys.com), Plano, Texas, in a keynote address at the company’s OpsManage’09 user conference Nov. 3-5 in Anaheim, Calif.
The OpsManage event replaced the annual conference previously known as WonderWorld, sponsored by Wonderware—one of four units of London-based Invensys plc that were merged last May to form IOM. Other units that make up the new IOM division include Invensys Process Solutions (IPS, which includes Avantis, Foxboro, SimSci-Esscor and Triconex), along with U.K.-based Eurotherm and IMServ.
Will it stick?
Partners exhibiting on the OpsManage Expo floor expressed mixed opinions about the reorganization. “Let’s see how long they stick with this one,” said a representative at one systems integrator booth, in a reference to past uncertainties involving Invensys strategies and organizational structures. But Bhattacharya, who most recently served as president of Wonderware, portrayed the IOM reorganization as one that brings the right focus to the market at the right time.
IPS is “one of the largest and most successful automation companies,” and is strong in safety, control, and advanced optimization applications, he said, while Eurotherm is “very strong in mid-sized controllers.” When combined with Wonderware, which is strong in manufacturing software and infrastructure, and IMServ, which serves the energy monitoring space, the IOM division is well-positioned in both hardware and software to provide solutions for a new set of “macro problems” faced by process and hybrid manufacturers today, Bhattacharya said.
The IOM employee base seems to be on board with the changes. Since the reorganization, an “adversarial” relationship that existed previously between Wonderware and IPS has been replaced by a new spirit of cooperation, one Wonderware manager told Automation World. And as at another IOM conference held in Houston in September, IOM employees who spoke with Automation World at OpsManage were uniformly enthused with their new roles and outlook. Despite the recession, overall attendance at the OpsManage event was about 715, up by around 10 percent over last year’s WonderWorld conference, according to IOM sources.
Fundamental change
In his keynote, Bhattacharya said that the timing of the IOM reorganization was important, because it comes as “the manufacturing market is undergoing some fundamental changes.”
Five years ago, the primary concerns of process manufacturers were productivity and quality, he said. But today, engineers and managers must grapple with an expanded set of issues. These include sustainability and energy concerns; an increased focus on real-time metrics; a need to capture or replace expertise lost through a pending wave of retirements; and control requirements that are no longer limited just to plant automation, but to control of the business as a whole.
No vendor to date has been able to holistically capture and provide a solution for this new set of macro problems, Bhattacharya said. But he expressed confidence that the new IOM business model will enable the company “to morph into the one that can do this.”
Bhattacharya compared the task needed in manufacturing to that undertaken by enterprise resource planning (ERP) suppliers. The ERP market did not exist 30 years ago, he said. It was created when suppliers including SAP, Oracle and Microsoft developed packaged ERP solutions by stitching together a range of applications such as supply-chain planning, materials-resource planning, human relations, accounting and others. “When we stitched the whole process together, we realized that the bottleneck in this real-time world has now started to become manufacturing,” said Bhattacharya, who served as an SAP executive prior to joining Wonderware in 2007.
Enterprise control
So to solve this problem, “our vision is to be able to build what we call an enterprise control system, leveraging the full understanding we have of the automation world, of the control world, leveraging the core understanding we have of the software world and the information management world, and stitching those worlds together,” Bhattacharya explained.
In a subsequent keynote session, Rashesh Mody, IOM vice president, portfolio and strategy, expanded upon Bhattacharya’s comments with a detailed discussion of the company’s product roadmap. It incorporates an open system platform, upon which applications will be built, with yet another layer of industry-specific solutions above that.
Both Bhattacharya and Mody emphasized the importance of the company’s “partner ecosystem,” which enables the company’s 3,000-plus partners to contribute their expertise and innovation in the development of needed industry applications, which can then be incorporated into the IOM platform.
This is an approach that IOM competitors have not done very well, Bhattacharya said. “We want our partners to innovate, and we will work with them. And if it means paying royalty, we are happy to do that,” he noted. “That’s how we choose to be different.” The ideas for IOM’s new energy management solution, as well as a water/wastewater industry solution both came from partners, according to Bhattacharya.
For more on OpsManage’09, check out the podcast interviews and video interviews conducted at the event. Visit the Automation World Podcast Library at www.automationworld.com/podcasts and the Video Library at www.automationworld.com/videos.
IOM unveiled various new products at the OpsManage conference.
EMI entry
The Wonderware Intelligence Software 1.0 solution, introduced at OpsManage, is the company’s initial entry into the enterprise manufacturing intelligence (EMI) space. The solution enables customers to contextualize, aggregate and report both historian and operational data using role-based dashboards, presenting key performance indicators (KPIs) and real-time operational business metrics that are used to monitor, tune and optimize operations and supply chains, IOM said.
Wonderware Intelligence software transforms data and information from multiple sources into business intelligence by aggregating process and production data in real time and adding contextual elements, such as equipment, product, work orders, material and personnel. This information context enables end-users to gain insights into the root causes of problems and understand how production events are related.
The formatted information is saved and optimized for fast reporting and analysis, allowing end-users to create and publish dashboards using the Wonderware Intelligence Analytics Client into a wide variety of Web portals. Users can also configure customized metrics without programming.
The solution acquires data not only from the Wonderware family of products, including MES (manufacturing execution system), InBatch and Historian, but also from external systems such as ERP, laboratory information management systems (LIMS), product data management (PDM) systems or even other execution systems and historians, to provide plant, multi-plant and corporate-wide views of operations and performance. It utilizes best-in-class tools for rapidly creating and publishing dashboards that can be rendered in commonly used Web platforms such as Microsoft SharePoint, mySAP Enterprise Portal and Wonderware Information Server, IOM said.
Utilities optimization
Another new product is the company’s ROMeo 5.2 solution (for Rigorous Online Modeling and equation-based optimization) for industrial utilities optimization. It is built on the company’s SimSci-Esscor optimization software. This solution is aimed at large enterprises, such as refineries, that have several options to produce, buy or sell energy to meet the demands of processing facilities, IOM said.
At most of these operating sites, the cost of power and utilities is often the largest controllable operating expense, after the purchase of raw materials. Rising energy costs and stringent environmental regulations drive an increased focus on energy efficiency. Most companies are responding with demand-side energy management strategies that target process improvements or modifications to reduce energy usage. However, supply-side energy (utilities) management provides additional opportunity to reduce consumption through improved sourcing.
The Invensys solution introduces several new capabilities and functions that simulate steam turbines, gas turbines, heat recovery system generators, boilers, headers and several others plant utility systems. Completely and efficiently modeling demand in a single environment enables user to target significant improvements in supply-side energy management, IOM said.
SCADA advances
Other new entries include the InFusion SCADA 2.0 (supervisory control and data acquisition) software system, with Foxboro SCD2100 and SCD2200 remote terminal units (RTUs) for oil and gas, and water and wastewater applications.
The InFusion SCADA 2.0 package of software components enable SCADA developers to create reusable objects and templates, as well as manage human-machine interface (HMI) display properties, data quality, equipment maintenance tagging and other functions necessary for rapidly building powerful, easy-to-use SCADA applications, IOM said. The system also stores program components in a central repository for remote deployment to Windows-based network devices. End-user engineers can then draw on this repository to build future applications, which enforces standards, preserves applications knowledge and reduces the overall engineering effort. System managers can also propagate changes to multiple computers with a single mouse click, reducing travel and SCADA network troubleshooting costs.
The new SCD2100 and SCD2200 RTUs provide an advanced, integrated operating environment for controlling and monitoring field operations and collecting real-time data for viewing via InFusion 2.0 screens or integration with process control or other enterprise applications. Both of the new RTUs support a wide range of input/output configurations and device integration, including support for the Hart protocol, according to IOM.
Energy management
The Wonderware Corporate Energy Management application is another new product. It is designed to enable manufacturing and industrial automation customers to easily and quickly implement an energy management program and achieve sustainability goals. The application allows users to monitor energy and detect and notify personnel of energy inefficiencies. It connects directly to meters on a network, through industrial controllers and accepts manual entry via the company’s Wonderware InTouch HMI and IntelaTrac mobile solutions.
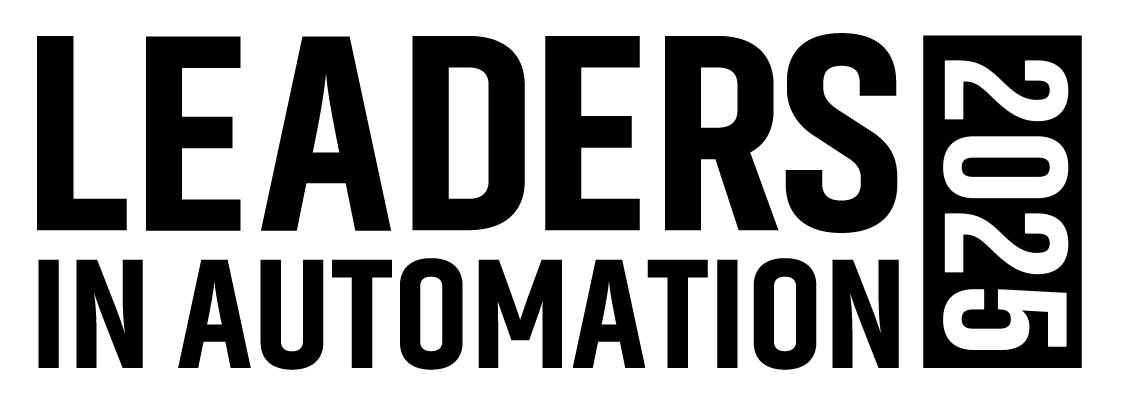
Leaders relevant to this article: