Somewhere in production, one of several thousand sensors records an unusual event, and an e-mail message is automatically sent to your chief executive officer (CEO). Is this an ideal scenario? Not likely. Not for the CEO, anyway, at least not if it happens with every manufacturing blip. The CEO gets enough e-mail without hearing from “Actuator 2594,” or any of its neighbors.Still, if this sensor is part of an array that oversees a cell that is critical to product completion, you might want this bit of data to go to several recipients in the company—and right away. Maybe maintenance could add some oil or change a motor, or operations could shunt production to a neighboring line. Consolidating the continuous flow of production data from operators, machines, sensors and switches into a neatly wrapped package of information that is useful to other enterprise functions is no mean feat. It requires both top-down and bottom-up perspectives. The top-down perspective considers what information is useful for upper management. The bottom-up view depends on a combination of data aggregation, history and presentation (visual dashboards among them) to boil down the broad flood of production data into information that others in the company can understand—and act upon.Of course, if your focus never wanders outside the walls of production, the first question might be, why bother? We do what we do, and we do it at the rate we can achieve—where does the CEO come in? Top management wants to monitor things that are central to your company’s business. It wants you to measure things that matter. And the Manufacturing Enterprise Solutions Association International (MESA) and Cummaquid, Mass.-based analyst firm Industry Directions Inc. recently published the results of a study focused on just that. “Metrics that Matter” looks at some of these interesting questions:What metrics—including key performance indicators or KPIs—matter to top executives?What do a range of companies measure in manufacturing?Which of these measurements, applied intelligently, serve to further company goals?By focusing on metrics that matter, MESA and the study's developers and contributors have made a key distinction between measurement and meaning. You can measure all sorts of things in production, but only a select few make a real difference. And only a select few metrics say anything compelling to upper management."More and more, performance management on the enterprise level centers on core financials," says Julie Fraser, principal, Industry Directions. "The enterprise view calls for ways to track profitability, as well as orders for products, and measures the performance of the company in fulfilling those orders. Manufacturing can gain the ear of top management when production metrics measure the production-side elements that contribute to the performance of the company as a whole."The means and methods of monitoring enterprise activity, "performance management," are in constant flux. At the heart is the marshaling and monitoring of resources to track progress toward specific goals. Taking the broadest possible view of a manufacturing business, these goals include designing and making products that people want, making sufficient numbers of those products to satisfy the need in a timely way and making enough money to stay in business.There is admittedly a lot of static in the performance management signal for a key reason: a lot goes on in production. Because of this, performance management requires an extremely broad system. Those who want to employ performance management must take a systems view that begins with switches and sensors and ends with comprehensive reports. The wider this system view, the more that interdepartmental participation—collaboration—will make sense. Company success is collaborative, whether a given company recognizes or organizes around that fact or not. Design walks on the edge if it doesn't consult with manufacturing about the requirements for profitable manufacturing—in other words, manufacturability. Similarly, manufacturing has to work with design to succeed in making product with full functionality. And it obviously needs input from sales and order fulfillment for planning. Finally, manufacturing can benefit from quality's input on how well it is meeting specifications.And here is where simple guidelines evaporate. "There is, of course, no single answer that applies across all industries, or even across all plants within a company," says Charles (Charlie) H. Gifford, senior solution architect, Lean Performance Management, Global Professional Services Business, at automation vendor GE Fanuc Automation, in Charlottesville, Va. Gifford has contributed in the development of technical standards for manufacturing, including the definition of the Instrumentation, Systems and Automation Society’s ISA-88 and ISA-95 standards."Choosing the exact types of performance measurements for production depends on your perspective," Gifford explains. "If your perspective is limited to the production area, some portion—or maybe all—of what you're measuring may mean something to you, but will probably just puzzle upper management. If you want metrics that matter, you want to work from a higher viewpoint. Ideally, you connect up with the goals from financial metrics, since those are the enterprise goals. You figure out how the goals of the guys in finance translate to operations metrics."In one instance, a business unit-level perspective—developed through a gathering of best practices within the unit—helped the Power Electronics Division of C&D Technologies Inc., in Mansfield, Mass., implement a consistent performance management system. This plant, which makes DC/DC converters, AC-DC power supplies and other products, had been Datel Inc. prior to acquisition by C&D in 2004. Steve Kaplan, global MES administrator for the Division, implemented the Manufacturing Execution System (MES)-based performance management program across several facilities. He held a similar position for Datel in Mansfield prior to the acquisition.As C&D management rationalized its operations post-acquisition and organized the Power Electronics Division, the group reexamined the company's KPIs and its infrastructures for measuring performance. The former MES installation at the former Datel group emerged as the best practices model. Kaplan found himself in the enviable—or unenviable, depending on your point of view—position of overseeing the introduction of MES-based performance management techniques to the rest of the C&D division. "We had been using MES for ten years in a totally paperless system," Kaplan explains. "The Power Electronics Division team saw a need for common measuring methods to meet divisional goals across all three Division manufacturing facilities, here in the United States and in China. A consistent MES implementation was clearly the way to go."Because he could have been perceived as the new kid on the block, an upstart imposing new rules on the old guard, Kaplan approached the task with considerable forethought. "When I walked into the other plants, I carried the decisions and positives we had gone through when my group decided to install MES earlier," he says. "I talked about these, and I drew them out about where they wanted positive change, possible benefits for their specific plant.“There is always going to be resistance to change," Kaplan points out, "but one plus in my favor was that I could offer the others a paperless system. Manual data gathering had been a major drain on resources for them, and now that manual effort would go away. And the groups were positive about why measurement was needed and why it should be consistent."Kaplan worked with each group on exactly what to measure. "The various plants had different ways of determining product pass/fail around customer delivery commit dates," he says. "For example, it was tempting to count a 20-component product with one failing component as 19 passes and one fail. But, if you determine production numbers on that basis, you end up with mighty puzzling mismatches between production output and delivery numbers."In the long run, Kaplan met often with plant personnel at all levels at each facility, listening to their needs and keeping the key goal, consistent KPI data, always in the forefront. "It was much more a matter of guiding them through implementations that made the most sense for them, than one of top-down, rigid enforcement," Kaplan says. "In the end, everybody owned the system and everybody owned the methodology for meeting KPIs."Gifford provides a broad outline for the successful mapping of financial-to-operational metrics, many of which mirror the C&D Divisional experience. The steps include:Determine what the plant makes and how it makes it—something that is not always obvious.Determine the business model—that is, what are the business functions that production provides the company? Given that most manufacturing involves increasingly complex supply elements, where does this business side of manufacturing fit with the supply chain?Determine the stage of the plant's metrics. Is there an existing data flow for statistical process control (SPC)? Is there computer-based, automated data collection in place, or is everyone pushing paper? Are different functions doing different things with, say, Microsoft Excel? Work out a migration path by which data can be turned into meaningful information.Gifford says that companies generally go through three system models before they succeed in fully working through this final step. The first model is often a trial of a finite capacity planning system. "Typically, IT (the Information Technology department) wants to skip over all the data and measures it doesn't understand and put in a finite capacity planner," Gifford says. "This approach is generally built into their enterprise resource planning (ERP) applications, so they tend to be predisposed to it. But a finite system fails to cover an area as dynamic as most manufacturing. Change is the norm, and change management in a finite system becomes a real issue the first time something alters in the product's manufacturing operations."In addition, this first-stage data model soon begins to fray, because, Gifford says, "there has usually been no value-chain mapping, and no consistent mapping of concepts or terminology across functions. You can't assimilate eight different ways to calculate yield. If you try to roll that kind of data into a KPI report, your report is just wrong."To be fair, those who tried early found some issues with early software and tools. Says Colin Masson, research director, Chemical and Process Research, for AMR Research Inc., in Boston, "The first generation tools were not model-based. They tended to be partial toolkits with visualization tools."By they time they reach the second level, companies have rationalized their operations with a consistent model. "Once processes are identified and prioritized, you can tackle the issue of change management," Gifford says.Systems are now robust enough for meaningful measurements. "Systems now offer a real-time, or real-time enough views of operations," Masson says, "and business links are available. It's now possible to see things across the board. If a customer order is at risk, you can see why, whether it's quality, scheduling, constraints in manufacturing, supplier issues, whatever."To see things across the board generally requires the creation of a manufacturing function to oversee the lifecycle of the system. "Most companies have to go through an organizational change to bring this about," Gifford says. "You can't do this from the IT standpoint—if you centralize through IT, you inhibit flexibility for change. Manufacturing MES or manufacturing IT has the production experience to know where to include flexibility. For example, manufacturing IT can find ways to incorporate changes in operations as a new product moves from introduction to volume start-up. Companies benefit when the time between NPI (New Product Introduction) and volume is held to a minimum, and this process is the fastest when you can quickly assimilate change."“The challenges in moving manufacturing data through the enterprise are volume and noise," says Dennis Cocco, founder and chief product strategist, ActivPlant, a London, Ontario, Canada, supplier of enterprise manufacturing intelligence software. "For years, we have been talking about gaining more visibility both within manufacturing and between manufacturing and other areas. The problem is that while you can capture every event, activity, fault or cycle time—and many people do—the real need is to boil the data down into the smallest units of useful information. It's a case of less being more."In developing its particular solution after years of providing tools for data gathering, ActivPlant began to realize its customers were asking for answers that could serve as pointers for action—not more data for data's sake. "What emerged was the need for an easily read map," Cocco says. "For many reasons, people want to know throughput, and, when it's lagging, exactly where things are being impeded and what's causing the lag."ActivPlant boils the process down to what it feels are the three absolutely critical measures for every cell or segment of production: when it's done, when it's blocked and when it's starved. If an operation is not done, or if it is blocked (unable to send product further) or starved (unable to obtain product to work on), the clues add up to a manufacturing constraint. "But most people don't have time or resources to track real constraints because of all the possible variables," he says, "so they chase downtime, which is much easier to trace. The trouble is that downtime may or may not be the heart of a blocked or starved condition. Fortunately, computers can juggle all the variables to identify the true constraints."Performance management offers powerful underpinning to collaborative activity. By providing an objective indication of progress toward goals, it provides a window on the overall effectiveness of any given functional area. The objectivity is important—because there is a minimum of emotion, the data can pinpoint the locations of losses or failures without personality clashes or finger-pointing. With collaborative performance management, less-than-optimum throughput becomes a base point for improvement, which most people enjoy doing, rather than a red mark, which most people avoid.For more information, search keywords “performance management” at www.automationworld.com.
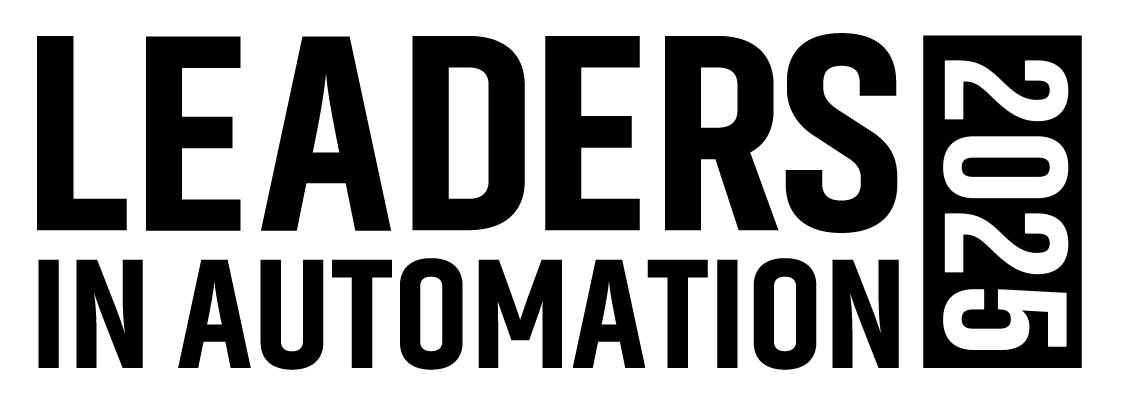
Leaders relevant to this article: