The time: the late-1990s.
The place: a Midwest automotive plant.
Earl, a tug vehicle operator, is pulling a 60-foot long dolly train loaded with panel racks from an outside rack storage area, and is headed toward a rack loading cell. As he approaches an intersection in the plant, Earl notices an unmanned, parts-carrying, automated guided vehicle (AGV) moving perpendicularly in another aisle toward the same intersection.
Earl, hold up!
Instead of stopping, Earl guns his tug truck, hoping he can clear the intersection before the AGV arrives at the crossing.
He doesn’t make it.
The AGV bumps into the side of the dolly train, compressing a hoop-shaped, flexible plastic bumper on the AGV’s front end, which triggers limit switches that bring the AGV safely to a halt. But the AGV bumper, already stressed from several earlier collisions, has been cracked. And as Earl’s dolly train continues through the crossing, one trailer snags the plastic and literally tears the bumper away.
While the AGV itself is OK, its safety bumper is gone, and the vehicle can’t move until a maintenance technician arrives to repair or replace it. Meanwhile, the stalled unit is blocking the aisle, and a production line somewhere in the plant is left waiting for the parts it is carrying.
Different outcome
Fast forward to the present day, at the same automotive plant. Earl is still on the job, and the same scenario occurs.
This time, however, when Earl’s dolly train moves into the intersection, the AGV senses its presence and automatically slows down well ahead of the crossing. The AGV creeps along, though not stopping, until the train clears the intersection, then speeds up again when the way is clear.
Still, just as the AGV arrives at the crossing, another careless worker steps directly in front of the vehicle, this time causing the AGV to stop suddenly, but without any physical contact. No one is hurt, nothing is broken, and once the errant worker passes by, the AGV resumes its motion and is safely on its way.
AGVs get smarter
What makes today’s AGVs smarter about obstacle avoidance than the previous generation? Increasingly, the mechanical bumpers used to ensure safety and negate impact damage on earlier AGVs are being replaced with non-contact, sensor-based collision avoidance systems, such as the Laser Bumper system supplied by Sick Inc., of Minneapolis. These systems rely on optical sensors that scan their surroundings using infrared laser beams, and detect obstacles based on reflected light. They can slow down or stop vehicles as necessary—without making contact—when obstructions enter their protective fields.
FMC Technologies Inc., for one, has been installing Sick Laser Bumpers on most AGVs it manufactures since about 2001, says Mark Longacre, marketing manager for FMC’s Automated Systems Group, in Chalfont, Pa. Prior to that time, there was a question as to whether proximity laser scanning systems such as the Laser Bumper met the American National Standards Institute (ANSI) B56.5 standard governing AGV safety, says Longacre. “Before, the standard specifically called out mechanical bumpers,” he notes. But subsequent revisions now allow for such “electronic bumpers,” Longacre relates.
The Sick Laser Bumpers are significantly more costly than the mechanical, plastic bumpers used earlier, Longacre confirms. Each Laser Bumper can scan an area of 180 or 190 degrees in a single plane, so AGVs typically are equipped with either one or two of the Sick systems, he says—with one looking forward and the second mounted on the rear of the vehicle to avoid back-up accidents. At a cost of $4,000 to $5,000 each for the Laser Bumpers, that can add up to around $10,000 to the price of the AGV. And some complex vehicles use side-mounted and top-mounted scanner units as well, raising the price further, Longacre notes.
AGVs sold by FMC are typically priced the in $60,000 to $150,000 range, and are used in automotive, printing and other industrial applications. FMC claims the largest North American AGV market share, with some 250 units shipped last year, says Longacre, out of a total market of 605 AGVs sold here in 2004.
Quick paybacks
Despite the added cost of the Laser Bumpers, however, Longacre is quick to point out that the laser scanning units provide benefits that enable the technology to quickly pay for itself.
One big advantage is reduced maintenance costs. The older mechanical bumpers were designed to flex upon impact, triggering limit switches that stopped the vehicle. But the bumpers were prone to cracking after several collisions. “Whatever you used—different kinds of plastic, or thin sheet steel—it just seemed that it would get kinked and eventually crack, and people were replacing bumpers,” says Longacre. “That’s not something you want to be doing with your automated equipment.” The Laser Bumpers, by contrast, are “really pretty maintenance free,” Longacre notes.
AGV users such as Robert Wolf agree. “The Sick Laser Bumper system is far less costly to own over a five-year period than the plastic bumper was,” declares Wolf, a Ford Motor Co. specialist in mobile robotics, including AGVs, who is currently material handling manager at Ford’s Romeo, Mich., Engine Plant.
Wolf confirms that frequent cracks were a maintenance headache with the older, mechanical AGV bumpers. Collision potential is higher in plants where AGVs traverse the same areas as manned forklifts and other manned vehicles, he says. And in some mixed-traffic Ford plants where AGVs number 80 or more, incidents of cracked AGV bumpers in the past totaled between 150 and 400 per month, Wolf notes. In these plants, Ford was able to save up to $150,000 per plant per year in maintenance costs by replacing mechanical AGV bumpers with Laser Bumper systems, Wolf estimates.
Other benefits of the scanner-based technology come in improved productivity, by enabling AGVs to move faster and complete tasks more quickly. One reason is that users are able to create two programmable protective zones within the Laser Bumper’s surveyed area—a warning zone and a safety zone.
The safety zone is the smaller of the two zones, and can extend a minimum of five feet radially beyond the vehicle to a maximum of 23 feet, depending on the speed and weight of the vehicle and its load, and the consequent distance needed for stopping. An intrusion by an object or a person into this zone triggers an immediate stop.
The warning zone, by contrast, can extend up to 160 feet radially beyond the vehicle. An intrusion in this zone, such as Earl’s dolly train, can be set to trigger an audible and/or visible warning signal, for example, and may also signal the AGV to reduce speed. “It can go to half speed, or quarter speed, or whatever you want to program it to, and maybe that’s time for the obstruction to get out of the way,” says Wolf. “Then once it’s cleared, it can check again and take the AGV back up to full speed and get going.”
One major advantage of the system is that the size and shape of the protective zones is variable, and they can be changed on the fly, says FMC’s Longacre. This means that the AGV can safely move faster in some areas of a factory or warehouse, which can boost productivity.
“The standard says that we have to be able to stop our vehicle before the frame hits an obstacle, so the size of our scanning area is directly proportional to how fast we can move. The bigger our scanning area, the faster we can move, and the more work we can do,” Longacre explains. “If we’re in a wide open area, we can have that Sick bumper very large. But if we come to a place where we have to snake through a tight area, we can shrink down the bumper size, operate slowly, and then speed it up again when we’re back in the open.”
This contrasts to the older mechanical bumper system, which didn’t allow for such flexibility. “When you had a fixed mechanical bumper, you had one bumper size, and that was it. So you had to pick the trade-off between speed and maneuverability,” Longacre says.
At Sick, in Minneapolis, Mobile Vehicle Market Manager Stacy Kelly notes that sales of the Laser Bumper and other sensor products into the AGV market have “really picked up steam” during the last five to six years. In addition to its Laser Bumper line, Sick sells a variety of other products for use on AGVs, including sensors for load detection, and for fork and mast position and tilt detection, as well as bar code scanners used to avoid load picking errors. Besides FMC, says Kelly, Sick’s primary AGV customers include AGV Products, Charlotte, N.C.; Egemin Automation Inc., Holland, Mich.; and Transbotics, also of Charlotte.
Forklifts next?
Now, according to Kelly, Sick is setting its sights in North America on the market for manned forklift trucks and other manned vehicles. According to figures from the National Institute for Occupational Safety and Health (NIOSH), she points out, nearly 100 workers are killed each year from forklift-related incidents, and an additional 20,000 are seriously injured. As a result, Sick believes the manned vehicle market here may be ripe for more safety-related sensors and other sensor automation products.
Some products today are available that can stop a forklift truck or other manned vehicle upon impact. But such
contact-only systems do nothing to anticipate or prevent collisions before they occur, says Kelly. She believes that non-contact solutions of the kind used on AGVs can help forklift truck owners improve safety, while also reducing damage and downtime.
Sick has already sold some Laser Bumpers into a U.S. government facility that is using them to automatically slow down manned forklifts, as a way to avoid accidents, says Kelly. And Sick is also looking to develop lower-cost collision avoidance sensor products that might be more suitable for the manned vehicle market, she adds.
So far, forklift manufacturers have shown limited interest in Sick’s Laser Bumper system, Kelly indicates. But a couple of manned forklift suppliers are currently testing various other Sick sensors, she says. “I think the time is right for us to go out and talk about this, and try to build a bridge between the AGV world and the manned forklift world,” says Kelly. “It’s not that forklifts should go to the extremes that AGVs do, at a full level of automation, but there are some things that they could learn from what AGVs are doing in this space.”
For more information, search keyword “sensors” at www.automationworld.com.
See sidebar to this article: Getting the Scoop on Vehicle Impacts
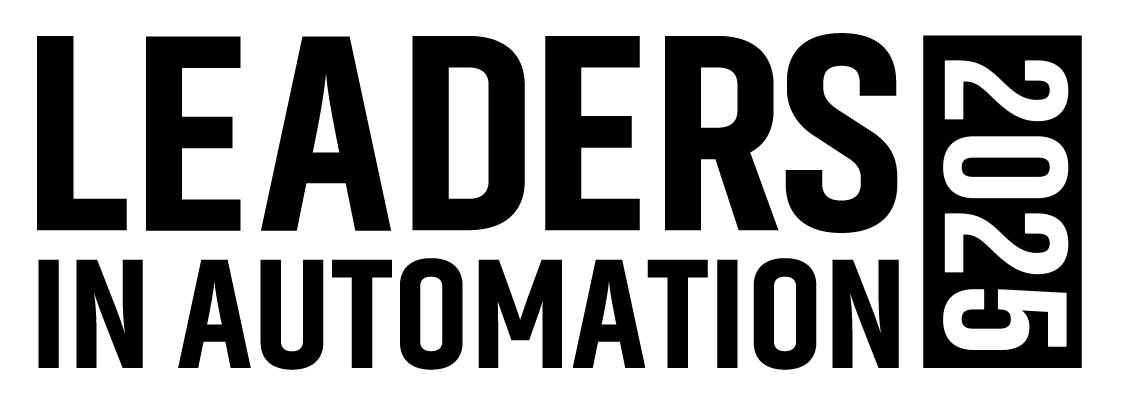
Leaders relevant to this article: